Author
|
Message
|
DryLakesRacer
|
|
Group: Forum Members
Last Active: Last Year
Posts: 1.7K,
Visits: 340.0K
|
Everytime I try to calculate my valve/piston clearance on overlap my head spins. I've eliminated that problem by using test springs and placing the head on with and without a head gasket. Time consuming but it takes me 4 or 5 times to put in a crank shaft before the seal goes in. I do check 15* before and after so I know exactly what the clearance is and I run close with my LSR engines. It seems when running naturally aspirated at a high elevation all the compression you can get is not enough. Even with the cams I run I'm disappointed if my cranking compression in not at least 210. That is one of the many tests I do. Recently I've started running legal oxygenated gasoline and much of my tuneup had to be revised, but so far it has been worth it. Good luck.
56 Vic, B'Ville 200 MPH Club Member, So Cal.
|
|
|
charliemccraney
|
|
Group: Moderators
Last Active: 4 hours ago
Posts: 6.1K,
Visits: 442.4K
|
At .008 out of the hole, you will be pretty close to the minimum clearance to the head, about .035". You will need to know the compressed thickness of the head gasket in order to determine if .008" will work.
Lawrenceville, GA
|
|
|
55 GLASS TOP
|
|
Group: Forum Members
Last Active: 2 Years Ago
Posts: 389,
Visits: 31.8K
|
Man my head is spinning so many numbers wow.
|
|
|
YBLOCKEREDH
|
|
Group: Forum Members
Last Active: 7 Years Ago
Posts: 80,
Visits: 47.9K
|
Thanks again Ted... Gary
|
|
|
Ted
|
|
Group: Administrators
Last Active: Yesterday
Posts: 7.4K,
Visits: 205.4K
|
Gary. If changing the piston from 0.004” in the hole to 0.008” out of the hole, here’s what the difference looks like for both the SCR and DCR. 6.250 | Rod Length | | | | | 3.860 | Bore | | | | | 3.440 | Stroke | | | | | 70.0 | Head cc's | | | | | -5.0 | Piston dish cc's (use a negative value for a dome) | -0.008 | Deck Clearance (in.) | | | | 10.00 | Head gasket cc's | | | | 58.00 | Degrees ABDC where intake is closed. | | 322.04 | Cubic inches | | | | | 9.98 | Static compression ratio | | | | 8.32 | Dynamic compression ratio | | | | | | | | | | Cam Specs | | | | | 0 | ° Cam advance | | | | 260.0 | ° Advertised Intake Duration (0.020") | | 108.00 | ° Lobe Centerline | | | | 58.00 | ° Intake Closing ABDC | | | |
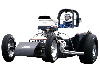 Lorena, Texas (South of Waco)
|
|
|
YBLOCKEREDH
|
|
Group: Forum Members
Last Active: 7 Years Ago
Posts: 80,
Visits: 47.9K
|
Hello Ted, I now have this motor it is .0008 out not .0004 in. Have the heads on with Felpro blue gaskets and have clearance. What can I expect now with the added compression? Gary
|
|
|
Ted
|
|
Group: Administrators
Last Active: Yesterday
Posts: 7.4K,
Visits: 205.4K
|
Pete. The chart is simply a guideline. The timing is whatever is optimal for the engine and not octane based. For the Y engines, the optimal total timing at WOT typically falls in the 36°-40° range depending upon the compression ratio if you take fuel octane out of the equation. Unfortunately it’s not as simple as using a single chart in selecting a compression ratio. As it is, different engines have different efficiency factors and as such, there isn’t a set in stone rule. Selecting a camshaft falls in the same ambiguous category as differences in head design will dictate different rules from one engine design to the next. Knock sensors are definitely nice parts to have but if the engine is having to use them constantly to keep detonation at bay, then the overall combination needs some adjustments. Compression ratio, fuel octane, engine temperature, ignition curve attributes, air/fuel mixture, cylinder head burn characteristics, and intake manifold sizing among other factors all have a part in this. Consider knock sensors a safety cushion in the event something out of the ordinary puts the engine in a position to experience detonation. In general, the ignition timing needs to be optimum for the engine combination. That test is performed with a fuel high enough in octane that detonation will not occur if optimum timing is exceeded but the power loss comes from cylinder expansion pressure occurring too early (or too late) in the cycle. If the ignition timing has to be backed up from optimum because of fuel quality or some other outside factor, then the ignition timing curve or even the engine combination as a whole needs to be re-evaluated. For the Y engines, ideal total timing at WOT wants to be around 36° total timing with high compression and 40° total with low compression. For the GM Vortec heads, 24°-26° total timing is the norm. Cruising ignition timing is another scenario that is tuned separately for.
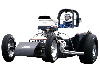 Lorena, Texas (South of Waco)
|
|
|
Pete 55Tbird
|
|
Group: Forum Members
Last Active: 4 Years Ago
Posts: 721,
Visits: 93.2K
|
Ted Thank you for more great information. Can you confirm that you octane vs dynamic compression ratio is based on a fixed amount of mechanical distributor advance timing? If so, what are you using, 38degrees or something else. The reason I ask is my first car was a Model A Ford that had the spark advance/retard on the steering wheel. So that technology is out there as are knock sensors to automatically retard or limit spark advance. Do you think they are worth looking into? For a street driven car not a dragstrip car. Thanks again. Pete
|
|
|
46yblock
|
|
Group: Forum Members
Last Active: 12 Years Ago
Posts: 1.2K,
Visits: 7.8K
|
Thanks again for all the information. I have more to do obviously. I'll go in and get a piston first so I can degree the cam. Then get some readings at the lifter and valve. For todays figures I just put the degree wheel to zero degrees at zero valve lift zero lash, and then reset it to zero with .006 valve lift and zero lash. Read out the duration for both trials, with multiple tests for each trial. Didnt think I could do much more without TDC established.
Mike, located in the Siskiyou mountains, Southern, OR 292 powered 1946 Ford 1/2 ton, '62 Mercury Meteor, '55 Country Squire (parting out), '64 Falcon, '54 Ford 600 tractor.
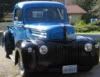
|
|
|
Ted
|
|
Group: Administrators
Last Active: Yesterday
Posts: 7.4K,
Visits: 205.4K
|
Mike. Did you check to insure that the camshaft is degreed in? Be sure to also check the #6 cylinder and to be on the safe side, also check the exhaust lobe centerlines. The chart I’m using is specific for measurements at the camshaft and not at the valve. But because the chart is biased in this regard, I don’t worry about the actual lift at the valve. If I was to actually take into account what’s happening at the valve itself and if using the 0.020” value at the ramp of the camshaft, then valve lift at the valve with 0.020” lash and 1.5:1 rockers will be 0.010” instead of 0.000”. That means the actual intake closing event would be later by whatever number of degrees that 0.010” takes to close up. But to give you something to think about, here’s a set of values from a custom Isky camshaft using various potential lash settings in which to determine the intake valve closing events at the cam lobe. 
As far as quench goes, I don’t consider it a problem until it’s over 0.065”. That means the piston can be as much as 0.020” in the hole with a 0.045” thick head gasket before needing serious consideration. The distance that the top ring is down from the top of the piston should really get more consideration but typically doesn’t. Do the math on the diameter at the top of the piston and how far down the top ring resides and see what kind of volumes start popping up. These volumes can be a serious detriment during the actual fuel expansion process.
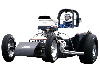 Lorena, Texas (South of Waco)
|
|
|