Author
|
Message
|
Ted
|
|
Group: Administrators
Last Active: 3 hours ago
Posts: 7.4K,
Visits: 205.4K
|
Brent (12/26/2022) ... Is there any concern if I continue by running the engine on the stands at idle and cranking, it has not been placed under load yet? I need to bleed the power steering which requires cranking without starting and I want to fine tune the fuel and ignition systems and adjust the valve lash.Without putting the engine under a load, there is the risk of ‘glazing’ the cylinder walls which will prolong the piston ring break-in. Even once the initial run in is performed, it’s still recommended to fast idle the engine when running it in lieu of just a slow idle if it’s necessary to just be cranking up the engine before hitting the road with it.
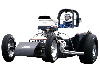 Lorena, Texas (South of Waco)
|
|
|
Brent
|
|
Group: Forum Members
Last Active: 6 Months Ago
Posts: 142,
Visits: 1.5K
|
I have finally completed two 20-minute runs at 2000 rpm, under no load - temp 185 - oil 50 psi. There are no sounds out of the ordinary. After first 20 I dropped the oil and cut open the filter, there was no sign of metal. Headers nearly melted plug wire boots, I have ordered heat shields. There is no smoke coming from the valley or the exhaust. Is there any concern if I continue by running the engine on the stands at idle and cranking, it has not been placed under load yet? I need to bleed the power steering which requires cranking without starting and I want to fine tune the fuel and ignition systems and adjust the valve lash. Many Thanks for all of your help.
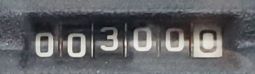 .150 Stroked Y-Block:327.25 ci @ >1hp per ci
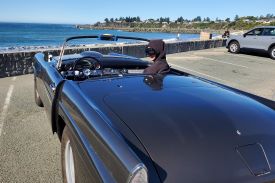
|
|
|
Ted
|
|
Group: Administrators
Last Active: 3 hours ago
Posts: 7.4K,
Visits: 205.4K
|
Definitely run with the valve covers in place. When running the engine at sufficient rpm to break the camshaft in, there will be a lot oil being thrown around. While not necessary in most instances, I do have some valve covers here for the various engines with clear inserts so that the valve train can be monitored during running on the dyno. Very few problems with camshafts breaking in here when due diligence is done with pre-assembly details.
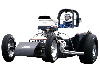 Lorena, Texas (South of Waco)
|
|
|
Brent
|
|
Group: Forum Members
Last Active: 6 Months Ago
Posts: 142,
Visits: 1.5K
|
Do you run without valve covers the first 20 min run in? I have thought about cutting the tops of a couple of valve covers. You mention watching while idling then bring up the rpms, I have read that immediate ignition then hold at 2000 rpm is a path to success. RB: talks about witness marks on the lifters here, the lifter you are holding is damaged right? He also mentions the use of worn out or lifter springs during beak in,
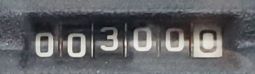 .150 Stroked Y-Block:327.25 ci @ >1hp per ci
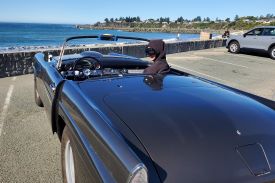
|
|
|
Ted
|
|
Group: Administrators
Last Active: 3 hours ago
Posts: 7.4K,
Visits: 205.4K
|
Brent (12/18/2022) I mixed the ZDDP additive into the oil vigorously, I had the same thought about the blending. Now it is a custom Ferguson break in oil. Gibbs does not list zinc and phosphorous levels in their blends, Valvoline and ZDDP do. I am comfortable with the Brent blend. RE: did not get the initial 20 done. 10 seconds cranking total and 30 running. 1/2 cup leaked from valve covers going on and off. Any thoughts about adding a bit of something to the 1/2 cup? Or any other advice.... Here’s my two cents on the subject and additional comments always welcome. The following comes from Fifty plus years of engine assembly experience but I haven’t seen it all yet. Watching the pushrods while the engine is running is just one way to determine that the lifters are rotating. Prior to starting an engine, I check for lifter rotation during the cam degree in process before any pressure is applied to the lifters. When rotating the engine while degreeing in the camshaft, the lifters can be observed for that rotation. If you have adequate lifter to bore clearance, lifter rotation will be there assuming an adequate rake angle on the cam lobe and correct radius on the lifter face. I find that lifter to bore clearances are the number one reason for camshaft failures. Some of that is attributed to a wider range of lifter diameter tolerances while other failures are simply a failure to ensure that the lifter bores are clean and not rusty. It pays to do a micrometer check of the lifters and the lifter bores prior to starting the engine assembly. Lifter/bore clearance is easy enough to correct before assembling the engine if a problem there is found. Not all camshafts are ground the same. Inadequate rake angle on the lobes will inhibit lifter rotation and cause an immediate camshaft lobe failure. There are brands of camshafts out there that are sloppy in that regard, and I’ll not use them at all. If there are eight guys working at a cam grinding shop but only one is not doing due diligence in maintaining the stone on the cam grinder, he’s giving his company a bad name in reference to the number of camshafts that fail. I’ll not post the names of those companies, but I’ll be happy to discuss those on the phone. While it’s cumbersome to do so, it pays to check the lobe taper on all the lobes before installing the camshaft. The first 5-20 seconds of running are the most critical for cam lobe / liter break in. The brand of oil and the zinc content are only minor considerations during that time frame; the zine/phosphorus (ZDDP) content comes into play during the long haul or many thousands of miles later. Keep in mind that there are different forms of zinc for the various engine oils, and they are designed for different applications. The zinc used in the oil for diesel engines is different than the zinc used in gasoline engine oil besides the overall additive packages being different in each of those oils. I do have a low opinion of some of the break in oils out there and that comes from conversations with my Nascar associates that deal with flat tappet camshafts with extreme amounts of valve spring pressures. While some of the break in oils do advertise an adequate amount of ZDDP, the base stock of the oil is not of the highest quality and creates other problems. The shear property of the oil is important as there must be enough shear in the oil to promote lifter rotation. As a general rule, you want an oil with at least 30 in its weight classification to ensure enough shear in the oil for promoting lifter rotation. I’ve posted this link before but I’ll post it again. It’s the list of contributing factors for cam / lifter failures in no particular order. Camshaft and Lifter Failure Causes – Eaton Balancing
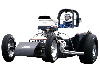 Lorena, Texas (South of Waco)
|
|
|
KULTULZ
|
|
Group: Forum Members
Last Active: Yesterday
Posts: 1.7K,
Visits: 306.2K
|
The easiest (IMO) way is to mark the top of the push-rods with white marker and while idling watch for movement/rotation. Increase idle speed and continue watching. If one (or more) is not rotating you will need to go into to find out why. Now this should have been done at run-in. If one is not turning, you need to shut it down and find out why. 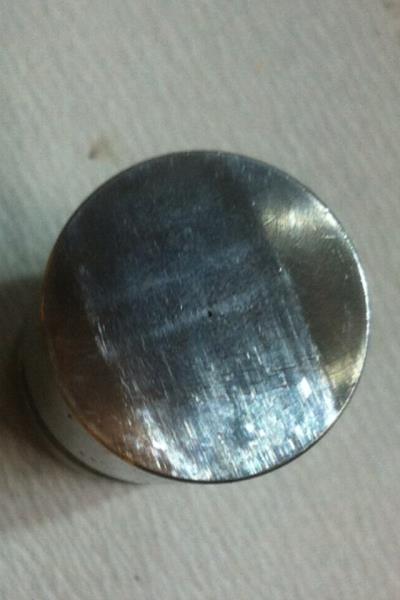 Please tell me after proper run-in you dropped the break-in oil. It is going to be full of trash.
____________________________
|
|
|
Brent
|
|
Group: Forum Members
Last Active: 6 Months Ago
Posts: 142,
Visits: 1.5K
|
|
|
|
KULTULZ
|
|
Group: Forum Members
Last Active: Yesterday
Posts: 1.7K,
Visits: 306.2K
|
You are quite welcome. As long as the cam/lifters wore in correctly, you are OK. Too late for break-in oil.
____________________________
|
|
|
Brent
|
|
Group: Forum Members
Last Active: 6 Months Ago
Posts: 142,
Visits: 1.5K
|
|
|
|
KULTULZ
|
|
Group: Forum Members
Last Active: Yesterday
Posts: 1.7K,
Visits: 306.2K
|
... sigh ...
____________________________
|
|
|