Author
|
Message
|
Ted
|
|
Group: Administrators
Last Active: 5 hours ago
Posts: 7.4K,
Visits: 205.3K
|
Cliff. Thanks for sharing your findings. It does bring a potential problem to the forefront. This is lengthy so try to stay with me on this. I’ll try not to ramble. Don’t take what I say as being okay with the distributor gears riding high. It’s the lesser of two evils when the other side of the coin has the distributor gear too low on the shaft which does create some extreme wear issues. To date, I’ve never seen a distributor gear or block wear issue with the distributor gear riding too high but have seen extreme wear problems when the distributor shaft is in a bind either from the gear being too low or the oil pump drive being too tight. The problem is that the distributor gear placement measurement is not looked at by the majority of people that simply stab the distributor in the hole and take it for granted that all is well. Whether by misinformation or by design, MSD has the Y distributor gears installed high on the shafts and they are simply not riding on the boss in the block. If they had gone with the original Ford Y spec, there would be some instances where the shaft would be in a bind simply due to block manufacturing variances. Now that I’m talking block variances, I do run across Ford blocks where the distributor holes are shallower than stock. The factory obviously compensated for this with the original distributor installation and moved the gear upwards accordingly. Unfortunately when the distributor is replaced with one where the gear is located according to the repair manual specification, the shaft is in a bind and the distributor gear and/or camshaft gear wears out prematurely. In extreme cases, there is some galling going on at that lower distributor block boss. I’ve also seen the block galling on the FE blocks but without having the distributor that was in the block when the galling too place, it’s difficult to determine the exact cause for the wear. My first instance with distributor gear placement was with a rebuilt 351W back in the Seventies that was continually wearing out the distributor gears. The original distributor was long gone and parts store distributors were being used. Once it was figured out that the block distributor cavity was too shallow, it was a simple matter in raising the gear. Since then, I’ve come across the same problem also with the 429/460 engines. One of the fixes simply involved making an aluminum washer to go under the distributor flange to raise the distributor rather than relocate the distributor gear higher. Pulling those gears off the shafts and relocating them can get dicey and especially where they’ve been off the shafts previously and already had new roll pin holes drilled in them. You only get so many tries at this before the shaft is weakened from the additional roll pin holes. So that brings me to a 292 block currently sitting in the shop. The distributor hole on that block measures out at 4.975” rather than the desired 4.995-5.000”. That creates a problem with using a distributor where the distributor gear is installed at the factory dimension. Simply knowing the distributor hole depth in the block does allows me to insure that the distributor gear is at least not too low for that particular block. For a stock application, I do prefer that the gear does rest ‘freely’ on the block boss but the end play in the distributor does force an exactness to the distributor gear location and not a lot of leeway for the shaft being in a bind versus the gear riding high. For an aftermarket distributor using bearings, then riding high for me is not a problem. Thrust bushings in a distributor does create some unwanted loading within the distributor which is better concentrated at the block instead which at least does at least have a constant supply of oil. Because the distributor shaft is end supported in the block, in my mind there’s no additional thrust load being imparted on the gear regardless of if the gear is at spec or riding slightly high. I think the right answer to all this is for the gear to be resting on the blocks’ distributor pad while some distributor end play is still present. It will be interesting to see what the MSD response is.
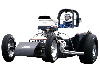 Lorena, Texas (South of Waco)
|
|
|
john2747
|
|
Group: Forum Members
Last Active: 3 Years Ago
Posts: 13,
Visits: 109.5K
|
Ted,I see from your efforts to measure 14 distributors only the three ford distributors and the Hunt distributor would have there gears making contact on the machined pad in the block.If the thrust from the gears is not controlled by the machined pad it would have to be controlled at the top of the shaft, ball bearing or needle bearing? It seems to me the MSD or mallory is not so premium if the gear position variance is .063". I have not seen any serious wear on the bottom of a factory ford distributor gear.There is a small oil gallery from the rear cam bearing that supplies oil to the shaft and gear. Maybe the MSD or mallory are tough enough to handle the thrust at the top bearing, but that would use up some horse power to, the ford's probably are not. On the ford racing site they state that the minimum clearance between the gear and pad [302 distributor] is .005" they don't give a maximum clearance it would depend on the total end play of the shaft.I don't disagree with anyone, just trying to get out the correct information.
john2747
|
|
|
Cliff
|
|
Group: Forum Members
Last Active: 6 hours ago
Posts: 872,
Visits: 13.4K
|
Hi guys, my measurements were taken with the shaft pushed up tight against the housing (per MSD), the rough measurements shown in the photos were to get the best photo not the best measurement, the problem is the wear on the top ball bearing in the distributor, this bearing is made to run in a neutral setting (no load top or bottom), the cam gear puts a high load on that bearing if it is not supported by the block, and when the gear gets to high I see poor wear patterns (I don't know how high it can go before problems), I have seen metal shavings inside of the distributor caused by this, I currently know of a 460 Ford that just took out the cam gear because of this, My Opinion is the gear should rest on the machined surface of the block in the center of the shaft end play, however that's only me not any one else that I know of.
Cliff
PS haven't heard from MSD today
|
|
|
Hoosier Hurricane
|
|
Group: Moderators
Last Active: 4 hours ago
Posts: 3.7K,
Visits: 322.5K
|
Ted, here's my 2 cents worth. The helix on the cam and distributor gear will tend to drive the distributor gear down. If the gear does not contact the machined surface of the block, then the thrust will have to be absorbed by either the top of the upper distributor bushing (or the case itself) or the oil pump drive rod. I have seen distributor cases worn at the top of the bushing, but never realized why.
John - "The Hoosier Hurricane"
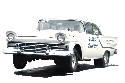
|
|
|
Ted
|
|
Group: Administrators
Last Active: 5 hours ago
Posts: 7.4K,
Visits: 205.3K
|
Ditto on using a straight edge on the bottom of the gear when measuring distributor gear placement. The distributor gears being higher on the shaft than called for in the specification manual likely hasn’t come up before simply due to it not being a problem. I’ll weigh into this as I typically check that the distributors and the oil pump drives are not in a bind when being installed. The distributor bind occurs when the fully compressed distributor shaft measurement exceeds the depth measurement for the distributor in the block. The oil pump drive is in a bind when the shaft is either too long or the receiving holes are too short. What this conversation brings up is the opposite in that the distributor gears are not resting on the machined boss in the block and are instead free floating above that boss. Joe Craine and I looked at this in detail yesterday while working on his engine and came to the conclusion that for optimizing the performance, the gear does not necessarily need to be riding on the machined boss in the block. There may actually be some horsepower to be had in not letting the gear drive itself into the block. Friction is the enemy here and any place where metal to metal contact can be eliminated, then there’s always the potential for some additional power gain. The question for me is how far up can the distributor gear be above the camshaft centerline before it actually becomes a problem? I do find some variances in the various block distributor hole depths so distributor measurements are necessary to prevent the possibility of the distributor being in a binding situation when installed. That creates undue wear on the cam/distributor gears and in some cases, the oil pump rotors. The winning 2016 EMC engine had the MSD distributor sitting approximately 0.073” above the distributor pad when the shaft was fully extended down. The gear wear pattern is good and there was no wear other than the black oxide on the gear being rubbed off where it was running against the camshaft gear. The plan is to have this years’ EMC entry with the distributor gear not touching the boss in the block and the plan is to run the same distributor this year as was used on the 2016 entry. Joe and I did go through some of the Y distributors sitting here in the shop and it was interesting on some of the measurements. Here are some of the distributor measurements with the shafts fully extended downward with feeler gauges being used to take up all the end play. 5.013” with 0.038” end play - 1957 Ford ball bearing advance distributor. 4.993” with 0.024” end play – 1962 Ford pivot advance distributor 4.995” with 0.020” end play – early Ford cast iron slotted distributor for HD truck engine 5.001” with 0.016” end play – Hunt electronic “Magneto look alike” distributor 4.990” with 0.028” end play – Mallory late model style 4.968” with 0.022” end play – Mallory point distributor new in the box 4.965” with 0.013” end play – Mallory model ZC 4.946” with 0.020” end play – Mallory model YCM 4.985” with 0.049” end play – Mallory model ZCM 4.968” with 0.068” end play – Mallory model ZC340B with tach drive 4.975” with 0.026” end play – Mallory model YD 4.935” with 0.025” end play – MSD 8383 recently installed in a 298” Y 4.940” with 0.025” end play – MSD 83831 4.927” with 0.026” end play – MSD 83831 used in the 2016 EMC entry 4.941” with 0.030” end play – MSD 83831 to be used in a fuel injected Y In summary, any distributor with less than a 4.990-5.000” shaft measurement when the shaft is fully extended downwards is potentially going to have the gear free floating or not touching the machined boss in the block. Any distributor with more than 4.990” with all the end play taken up is going to be in a bind situation creating some gear wear issues. It will be interesting to see what MSD does have to say about this. Any additional thoughts on the subject always welcome.
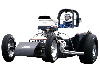 Lorena, Texas (South of Waco)
|
|
|
john2747
|
|
Group: Forum Members
Last Active: 3 Years Ago
Posts: 13,
Visits: 109.5K
|
Cliff ; Your numbers and the description of how the measurement is taken is not correct.1957 FORD SHOP MANUAL,on page 2-22 top left corner you will see a tach drive distributor that is in a fixture upside down,the distributor housing is locked in the fixture,there is a screw in the bottom of the fixture.This screw is tightened against the main shaft forcing it to the bottom of the housing.After all end play is removed the measurement from bottom of flange to the bottom of the pad on the gear is 4.991"to 4.996".You cannot take this measurement with a caliper with out having a straight edge clamped to the bottom of the gear pad. All y-block distributors have to be measured this way. Giving out the wrong information is worse than none at all. All this came up about 1 month ago.
john2747
|
|
|
charliemccraney
|
|
Group: Moderators
Last Active: 8 hours ago
Posts: 6.1K,
Visits: 442.2K
|
The spec in my '61 shop manual says 4.991" - 4.996" with .022" - .030" end play. It's interesting that this has not come up before, given how long the MSD distributor has been available.. I wonder why the Mallory is similar. Makes me think the aftermarket is getting an incorrect spec from a common source.
Lawrenceville, GA
|
|
|
Cliff
|
|
Group: Forum Members
Last Active: 6 hours ago
Posts: 872,
Visits: 13.4K
|
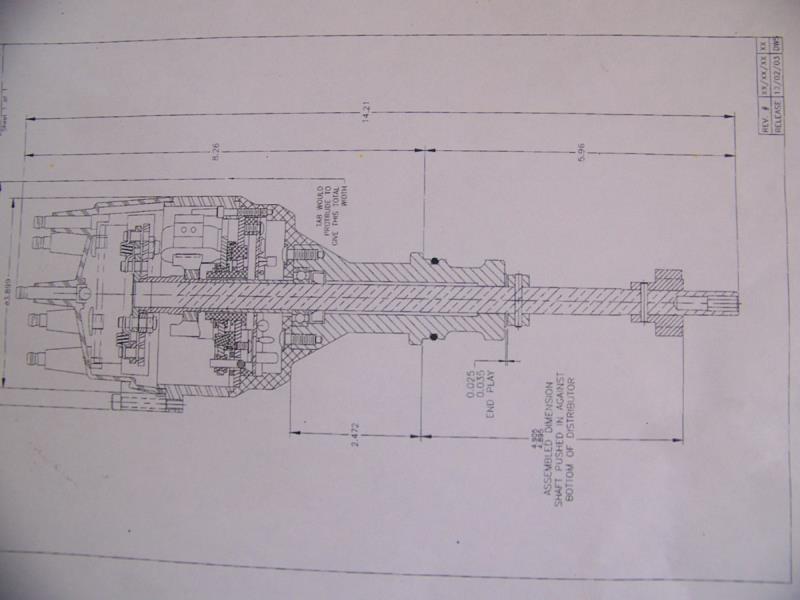 Here is a copy of my E Mail to MSD Hi Bass, those measurements are incorrect, that is the source of our problems, your measurement from the flange to the bottom of the gear should read 5.0 (+or-) your numbers of 4.905 - 4.895 is the problem, your numbers will not let the gear rest on the machined surface of the block, this causes cam gear problems, I am able to repair this, however I am bringing this to your attention so that you guys will look into and correct this problem Thanks Cliff Murray
|
|
|
Dave C
|
|
Group: Forum Members
Last Active: 5 Years Ago
Posts: 101,
Visits: 31.2K
|
I couldn't hurt to let MSD know there is an issue, and it wouldn't take anything for them to fix the problem.
Dave
|
|
|
Cliff
|
|
Group: Forum Members
Last Active: 6 hours ago
Posts: 872,
Visits: 13.4K
|
I think your right, Geoff Mummert says the same thing, however I think for the good of the whole I am talking to MSD about this, I have sent them pictures, it maybe all of our distributors are built wrong.
|
|
|