Group: Forum Members
Last Active: Last Year
Posts: 912,
Visits: 7.4K
|
One of the things we changed about the aluminum head was to move the rocker stand bolt closest to the intake manifold farther from the existing lower row.That left room to move the rocker shaft father from the valve making rocker ratios above 1.60:1 possible. This new rocker is longer from the roller to the shaft so it can't be used on factory heads.We just got our first set of samples of the new rockers Modern 1.70:1 rocker ratio similar to all Ford V8 engines (except SBF) since 1958 With so many of the popular cam grinds being low lift designs this will put nearly all of them in the .450-.500" lift range. Price has still to be determined.
http://ford-y-block.com 20 miles east of San Diego, 20 miles north of Mexico 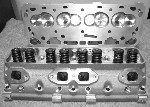
|
Group: Forum Members
Last Active: Last Year
Posts: 912,
Visits: 7.4K
|
One thing that should be added to the good info given is that the rocker arm is a tool. One might argue that the spring pressure would increase on a given lobe. But!! One must be looking at Pounds per square inch. A low ratio rocker forces you to go in all the wrong directions with the lobe. Because the bearing journals are a given dimension the lobe height cannot exceed this height. Resulting in reducing basecircle size for each thousandth of lift desired. Seeing that the lobe you are trying to grind on the core is a fixed shape every thousandth you reduce the basecircle the nose radius decreases right along with it. To understand how much stress is really on the nose of a lobe you calculate how much square area is contacting the lifter, figure out what percent of a square inch it is then divide your total spring pressure x rocker ratio by that. As an example 340 open lbs. x 1.54/ by .1" = 5236 lbs/in.. Now if you choose a lobe that has the same valve events with your new ratio the the lift can drop by 10% meaning the basecircle can increase by 20% 340 open lbs. x 1.7/ by .12"= 4816.66 lbs/in..  The other thing that should be looked at is where the load is applied to the lifter. Running more lift on a lobe of a given duration increases the lobes velocity there by placing the load farther out from the centerline of the lifter increasing the shear stresses on the stem and lifter bore. A higher ratio rocker increase valve lift without imposing this additional stress. Please remember that these are for example figures. The simple point trying to be established is that fastest way to decrease lifter pressure is to increase the area of the wear face and keep it closer to the center of the lifter. This new rocker arm set up is a tool. Allowing for greater selection of lobes to be used for street or racing use.. We believe this motor needs more options on the table. Putting things into perspective Winston Cup or whatever its called today is still forced to run flat tappets and wear/ slash cam life is something they have been dealing with.. Bigger cam bearings allowing for bigger basecircles, high rocker ratios, high grade oils, etc. etc. are all part of their solutions. As was mentioned before Ford Engineers shot up over 1.7 ratio by 1958 and rarely looked back.. FE, MEL, 385 Series(429-460), Cleveland, M Series, 3.8-4.2 V6, Boss 302 all used 1.7 or higher ratio from the factory.
http://ford-y-block.com 20 miles east of San Diego, 20 miles north of Mexico 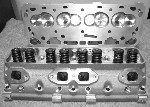
|