I'm building a welding table/workbench and need to weld some 3/16" plate. I'm able to stick it together but I'm not sure if it will be sufficient. I have a 120v, 135A Lincoln. It's suppose to be able to do up to 3/8" with multiple passes and flux core wire. I am using flux core and it is set up correctly for that, at the recommended setting. I can't figure out the multiple pass thing. Obviously, I know what it means, to make more than one pass but that just doesn't seem to work out. I end up with a big fat bead that doesn't seem any better than a single pass, or I move too quickly and it doesn't penetrate well. I can't seem to find the middle ground.
The way I have the table designed, I think the weld on the 3/16 should mostly hold things in place rather than be a structural component.
Some pictures to illustrate, not to scale:
Left, from bottom, up. Right From top, down. Hopefully you can see well enough how it will go together. Casters will be mounted on the bottom. I might add support to that other corner of the caster plate but I want to see how it behaves with some weight as is. I think it will be fine for my use. So ignore that potential flaw for now.
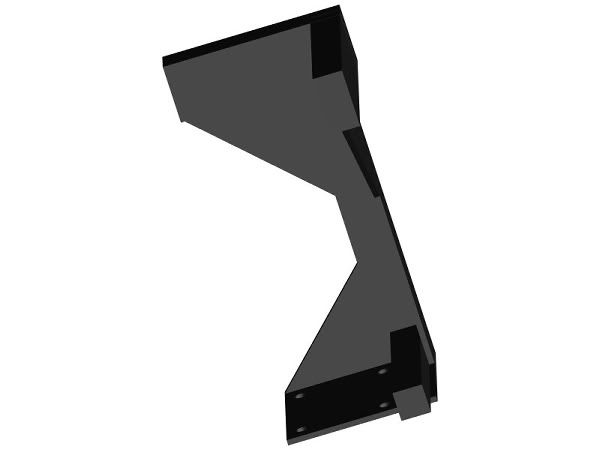
In my practice session, this was my best holding weld, a single pass and beveled edges, 90 degree as if making a piece of angle iron. I guess a filet?
1st half:
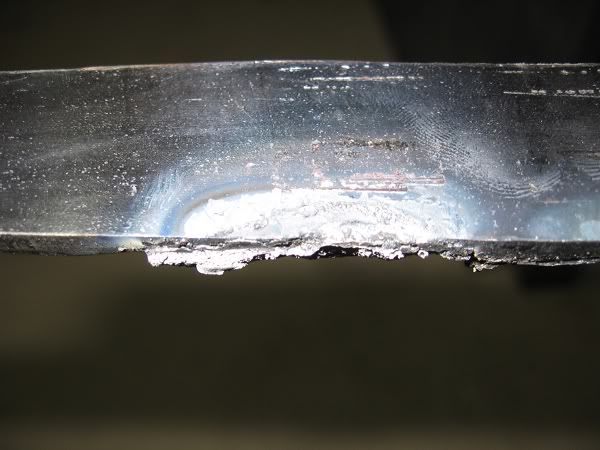
Second half:
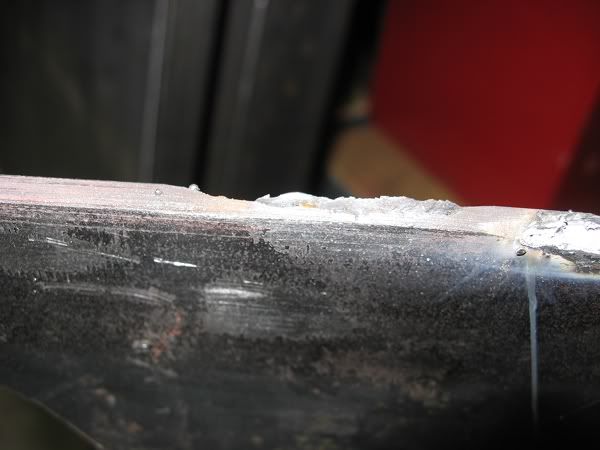
It looks like I spent more time on one piece than the other. That should be easy enough to correct. I clamped it in a vice and used pliers to break it. It broke at the weld, which I guess is better than pulling clean off of the plate, but is it a good thing at all? It actually seemed much stronger if I tried to bend the piece in, as if I was trying to close the angle. The other piece was actually bending in the vice. But it wasn't too difficult to bend it out, as if opening the angle. It will be welded on all sides except perhaps within a half inch of the bolt holes to leave room for flat washers. Do you suppose that quality of weld will suffice? Do I need just a little more practice? Or should tack it together and have someone with more experience and a more capable machine weld the thicker stuff?
Lawrenceville, GA