By charliemccraney - 14 Years Ago
|
I'm building a welding table/workbench and need to weld some 3/16" plate. I'm able to stick it together but I'm not sure if it will be sufficient. I have a 120v, 135A Lincoln. It's suppose to be able to do up to 3/8" with multiple passes and flux core wire. I am using flux core and it is set up correctly for that, at the recommended setting. I can't figure out the multiple pass thing. Obviously, I know what it means, to make more than one pass but that just doesn't seem to work out. I end up with a big fat bead that doesn't seem any better than a single pass, or I move too quickly and it doesn't penetrate well. I can't seem to find the middle ground.
The way I have the table designed, I think the weld on the 3/16 should mostly hold things in place rather than be a structural component.
Some pictures to illustrate, not to scale:
Left, from bottom, up. Right From top, down. Hopefully you can see well enough how it will go together. Casters will be mounted on the bottom. I might add support to that other corner of the caster plate but I want to see how it behaves with some weight as is. I think it will be fine for my use. So ignore that potential flaw for now.
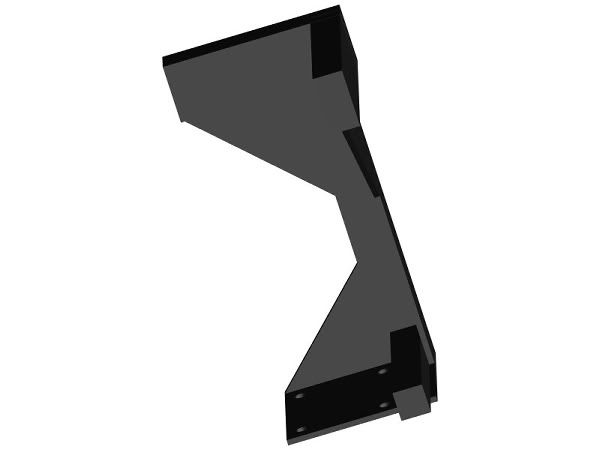
In my practice session, this was my best holding weld, a single pass and beveled edges, 90 degree as if making a piece of angle iron. I guess a filet?
1st half:
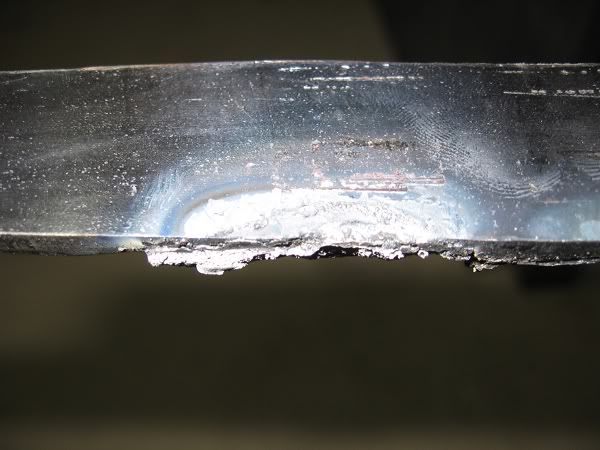
Second half:
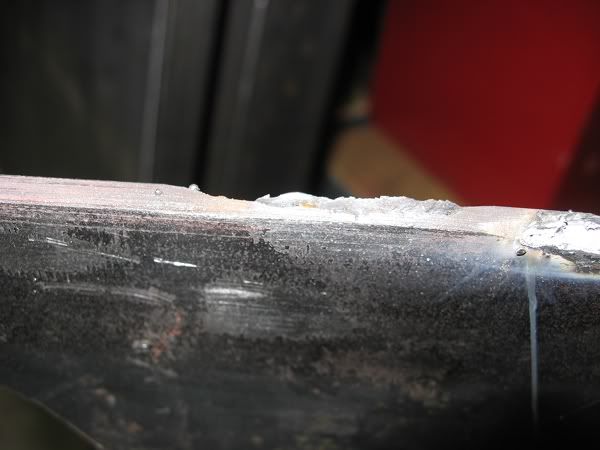
It looks like I spent more time on one piece than the other. That should be easy enough to correct. I clamped it in a vice and used pliers to break it. It broke at the weld, which I guess is better than pulling clean off of the plate, but is it a good thing at all? It actually seemed much stronger if I tried to bend the piece in, as if I was trying to close the angle. The other piece was actually bending in the vice. But it wasn't too difficult to bend it out, as if opening the angle. It will be welded on all sides except perhaps within a half inch of the bolt holes to leave room for flat washers. Do you suppose that quality of weld will suffice? Do I need just a little more practice? Or should tack it together and have someone with more experience and a more capable machine weld the thicker stuff?
|
By PF Arcand - 14 Years Ago
|
Charley: First of all, it seems that many 120 Volt Welder manufacturers tend to exagerate their capabilities. Several passes on 3/8 material is really pushing it. What you are doing is ending up with multiple passes, some of which are likely poorly fused. Those machines are mainly intended for sheet metal ( or auto body) work. However, things that might help; Are you "pulling" the weld or "pushing" it? On regular gas wire feed, pushing seems to help with heavier welds. You could also try pre heating the weld area some, to say 400 degrees. Re the weld ending up mostly on one plate.. hows the eyesite? Do you need glasses? Also, try moving the ground to another location, & weld toward a heavier tack. You could be gettng arc blow. If this is a heavy duty bench, might be an idea to just tack it all up & have somebody with a 200 amp "stick" or heavier welder finish the welding.
|
By charliemccraney - 14 Years Ago
|
I was pushing. I think welding more on one plate has to do with my noviceness. My nearsite is very good.
The table will support no more than a couple hundred pounds about 99% of the time. For the other 1% I'd like it to be able to support about 1000.
I'll try preheating.
I'm sure this is my inexperience, rather than the machine. Even if 3/8 were pushing it, I'm dealing with half that which it had better be able to handle. Otherwise I would not have bought such an expensive model. Though most of my work is with about 12 gauge and thinner which it does very well.
|
By pegleg - 14 Years Ago
|
Charlie. V the edges at about 45 deg. Start at the bottom and continue to push the weld. you should be able to fill it in three passes. One at the bottom, one left and one right. Preheat is not a bad idea if you can (with that welder.) Go find a used Lincoln or Miller Arc welder (220 volt single phase.
|
By Glen Henderson - 14 Years Ago
|
Charlie, I have tried one of the 120v welders and while it worked well on sheet metal, I just could not get it too work on anything thicker. I agree with Frank if you can swing a 220v Miller or Lincoln, you want regret it. Also a gas shielded welder works better than the flux core. I am sure not an expert, but I just never could get good results with the 120v flux core.
|
By GREENBIRD56 - 14 Years Ago
|
(1) A lot of welding pros size up machines by the amp - 135 amps = .135 thickness material. (2) There are a lot of guys who do great work with innershield (flux-cored wire). It's a matter of practice - and sometimes a skilled (and helmeted) helper who can adjust the machine while you are making a pass. (3) My experience is mostly with big structural repairs - but a two good basic rules are "don't weld on anything that isn't the temperature of boiling water" (avoids hydrogen embrittlement) and "grind the faces you intend to weld to a smooth shiny surface" (avoids contaminents).
|
By charliemccraney - 14 Years Ago
|
When making multiple passes, do I need to slow the wire speed so that it does not lay down as large a bead? When I was trying multiple passes, it didn't seem to hold any better and it looked uglier.
The flux core is definitely working better. I tried gas at max settings and it just wouldn't do it. Poor adhesion and the weld sounded terrible. I'm also cleaning the metal even though it's not as critical with flux core. As a result, it seems to be going down much cleaner than my previous flux core jobs.
And you know, this is the first time I've ever examined a weld I've made. So I can't even say with certainty that my work on thinner material is worth anything, other than to say that none of my previous work has fallen apart yet - even my absolutely terrible welds from the early days. That cross member I made for my transmission is still stuck to the frame of the truck and if I remember right, the frame is a 3/16" channel. I made that weld with gas, on the setting for 12 gauge because that is what the crossmember bracket was made with. Based on my experimentation in the past days, I would not have expected that to last, but 3 years and several thousand miles later it's still holding. It still may break, but on a table which is fully welded (or brazed ) that I don't think will experience the same sort of stresses, it may work.
A 220 volt unit might be optional in a year or so, but right now 120 is all it will be. Space and cash are coming into play.
|
By ALL AMERICAN RACER - 14 Years Ago
|
charlie
see if you can send ME
a private message w/your e mail address OR
empty your inbox OR turn on 'get messages from other members'
what kind of welder is it?
and what kind of rod are you using?
|
By charliemccraney - 14 Years Ago
|
I have a friend who I forgot is a pretty good welder. I went to his house last Sunday and brought my welder. The only thing we changed is to pull rather than push. He said you pull with stick and since flux core is similar, he figured it should be the same. So I made a few welds in scrap 3/16. We beat on them, tried bending them with a vice and a crescent wrench and they were holding. Today I made sure I can duplicate the results at home, and I can. So it still may not be the perfect weld, but I think it's going to do great for my intended use - and it'll get better with practice. The base metal bent before the weld began to bend which is far better than my attempts a couple weeks ago.
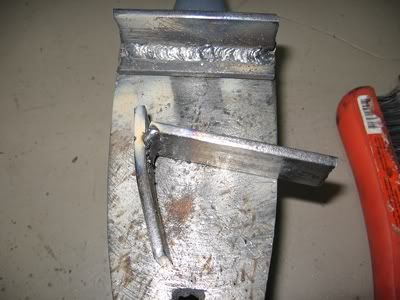
Now I need to install a properly rated circuit breaker so I can finish the job.
|
By kevink1955 - 14 Years Ago
|
If you have trouble duplicating the good welds you got at your friends house look into how the outlet you are using is wired. I found a dedicated 20 amp circuit 10 feet from my 100 amp garage subpanel works better with my welder than the outlet on the side of my house. I think the problem with the house outlet is that it is almost 100 feet from the house main panel and even thogh it is a 20 amp circuit with nothing else turned on the voltage drop in 100 feet at full load is more than the welder can handle. My 130 amp welder peaks at 25 amps when at the highest setting, it does not blow a 20 amp breaker because the breakers are designed to handle minor overloads for a short time (thermal trip) but designed to instant trip (magnetic trip) on a dead short. That 100 foot of #12 wire does cause a large voltage drop on my house outlet and almost none on the garage outlet.
|
By Frankenstein57 - 14 Years Ago
|
I have a 120 volt flux core deal, I borrowed it from my sister. It's ok to weld thin stuff, that's why I borrowed it. It's also handy being portable, for chores out in the yard. But for what you are doing, a 220 stick welder with some 6011's or 6013's, and make it happen.
|
By charliemccraney - 14 Years Ago
|
This 120 does great now that I better know how to use it. I didn't even have issues with the duty cycle for this job.
|
By kevink1955 - 14 Years Ago
|
Looking good, glad it's working out. As Tim Tailor would say, joining metal with fire way cool (insert grunt noise here)
|
By charliemccraney - 14 Years Ago
|
Yeah. It went very well. The hardest part was getting it all tacked together and square without any jigs or clamps. When welding was complete, all four corners were sitting flat on the floor. I did some reading about welding strategy to prevent warping and it seems to have paid off. Pulling is definitely the trick, if not in general, at least for these little welders (or for me). It sounds better, looks better, and according to my testing is better than pushing.
I was planning to make the top easy to replace but after thinking about it some more, my easy to replace plan really isn't that easy. It will require that I make brackets to weld under the top in order to bolt it down without any bolt heads sticking through. The material I'm using for the top is too thin for any substantially sized countersunk screw, .119". I'd like to mount a vice so these mounting points will need to be able to take that abuse. Then I thought, how often will I need to replace it, probably not very often. So I'm just going to weld it several places along each side and a couple places on the underside, toward the middle. The welded top will also add a little more rigidity to the entire unit. It will be like a shear panel. Future replacement really will not be that difficult if it's ever required. I'll probably outgrow this table before then.
|
By 57FordPU - 14 Years Ago
|
I like your project Charlie. Also sounds like you have become one with your welder. I know you are almost finished, but I thought I would share a few techniques that have helped me a great deal. I am no welding pro, but I have been forced into either learning or or watching someone else do it, and believe me I am still learning. I read everything I see on welding techniques and this thread is no different. I have a 220v Lincoln with mixed gas, so I haven't experienced as many problems as I would have if I had a 120v setup. I seldom weld anything thicker than .25", but when I do, multiple passes are required. Like Frank said, multiple passes without "V" grinding is futile. The pre heat method is doable with a torch, but instead of making a straight bead, I make multiple half moon shaped welds. For me, this seems to pre heat the metal ahead of the weld better than a single bead does. It also helps me to control the amount of material being laid down and avoids excessive build up. This technique also helps me a great deal with vertical and overhead welding. Needless to say, grinding every surface to be welded and even where the ground attaches makes even novices like me look good. When I am horizontal welding and the parts to be welded are easily accessible, I crank it up and run a single bead. My near site is not so good. The biggest problem staying on the desired location for me is lack of light. I place a flood light over my shoulder and this makes all the difference in the world. It not only helps me start in the best location, but actually helps me stay on track during the weld.
|
By charliemccraney - 14 Years Ago
|
Prep is key. I learned that in the early days by trying to do it the "easy" way and then having to do it all again. I beveled every butt weld and the outside of every fillet, as if making a piece of angle iron. Some of my best looking welds ever are on this table but there are still quite a few not so great looking ones. It was difficult to find a comfortable position for some of them. Sometimes gussets and angle iron would get in the way of the pulling technique so I had to rotate the gun to get into the corner.
|
By MoonShadow - 14 Years Ago
|
I'll try the light over the sholder deal. Since I had cataract surgery I can't see the work piece once I strike an arc. Its like I get a double reflection. Chuck
|
By rick55 - 14 Years Ago
|
My near site is not so good. The biggest problem staying on the desired location for me is lack of light. I place a flood light over my shoulder and this makes all the difference in the world. It not only helps me start in the best location, but actually helps me stay on track during the weld.
I used to have no end of trouble welding with a mig until i realized that the problem wasn't me so much as the mask i was using.
Mig welding requires a lighter shade lens than stick welding. I was using my stick welding mask. I now use a variable shade mask and use it on one of the lower settings. It makes sense as it is obvious that the arc from a stick welder is much bigger and brighter than a mig.
Here in Oz our single phase welders are 230-250 volt. A stick welder uses about 120 amps and 70 volts to weld 1/8" plate and a mig uses about 30 volts and 100 amps. The comparison in power is roughly 8500 watts to 3000 watts. This is also seen as light.
So if you are having trouble seeing the weld try a mask that is compatible with what you are doing. If you use one of the variable light sensitive masks you will not need several masks or swapping lenses between jobs. These variable shade masks do take bit of getting used to but you don't get eye flashburns when you are using one.
Regards
Regards
|
By MoonShadow - 14 Years Ago
|
I didn't mention but I am using a auto dim mask. Tried every setting but still couldn't see the work. Chuck
|
By pegleg - 14 Years Ago
|
That reminded me of something else l've discovered. I found I could see the weld better with my safety glasses on the my "street" ones. I discovered that the street glasses, wich are the type that darken in the sun, also get very dark with the rays from the welder. So dark it's like having the lens too dark. That might help you Charlie. I also got a step lighter hood lens for the MIG, and that really helps your weld when you can see what you're doing!
|
By rick55 - 14 Years Ago
|
If you are using an auto dim mask make sure what filter rating it has. Most I have seen which aren't adjustable are 11 and the setting for a mig should be 9 or 10. Can't remember what unit of measure is, but googling variable welding helmet will tell you what you should have.
Here in Oz we get bundled with Asia Pacific so our stuff tends to use this regions grading system.
Regards
|
By PF Arcand - 14 Years Ago
|
About seeing the weld area better. Many over 50 yrs of age need glasses for reading or close work. An item that worked for me, & also spared likely damage to good glasses, was a magnifier lense. They come in 1.25 to about 2.5 or more magnification. This was used with a standard Welding mask... On the issue of pushing or pulling the weld, I was referring to std gas cover Mig welding, which may have confused the issue some, as Charlie is using Flux core.
|
By Hoosier Hurricane - 14 Years Ago
|
In addition to Paul's observation, I have found that since I'm WAY past 50, my eyes don't adjust to light changes as quickly as they used to. I start out in the light, lower the hood, am in the dark, strike an arc, light again but can't see where I'm welding, finally see the target, lose the arc, in the dark again, etc. Frustrating. Thought an auto darkening hood would help, but it's no better.
|
By glrbird - 14 Years Ago
|
Glad you cleared that up about the auto-dark helmet, Now what do we do, my granddaughter can't weld yet.
|
By Ol'ford nut - 14 Years Ago
|
I have found that a gold tinted lens works better when mig welding. Another trick for us that are over 50 is to mark the area you want to weld with your soap stone. That shows up much better.
|
By MoonShadow - 14 Years Ago
|
All good advice, I'll try them all. Its a real pain not being able to stick two pieces of metal togather! Especially for a car nut. Chuck
|
By aussiebill - 14 Years Ago
|
Hoosier Hurricane (12/1/2011) In addition to Paul's observation, I have found that since I'm WAY past 50, my eyes don't adjust to light changes as quickly as they used to. I start out in the light, lower the hood, am in the dark, strike an arc, light again but can't see where I'm welding, finally see the target, lose the arc, in the dark again, etc. Frustrating. Thought an auto darkening hood would help, but it's no better.Me too, i loose the line i,m supposed to be welding and i have magnifer lens in helmet, guess the yrs start to tell.
|
By PF Arcand - 14 Years Ago
|
Pushing the arc in Mig welding may help with keeping on the joint, because you are not blocking the travel path with your hand & gun. Also, if I recall correctly, my instructor indicated that it also directs the heat forward which can help with heavier materials. All of these methods requires some practice of course... And for information, he also indicated that while Mig is the prefered method for most welding these days, it was invented & perfected for production reasons (over stick electrode) not necessarily because it gives better welds...
|
By charliemccraney - 14 Years Ago
|
Here it is. On to the next project.
|
By Y block Billy - 14 Years Ago
|
Practice makes perfet Charlie! so get off the computer and back to welding! When I started welding as a teenager, a pipe welder informed me to try to keep the molten puddle in a nice round circle while moving on. I found it very helpful information and ended up doing my share of welding over the years, from structural to steam pipe in power plants etc, although never certified the contrators and plants knew if i welded it it would look ok and pass. I still do some welding for shops around here, just last week an equipment dealer had me weld a thumb on an new excavator because they didn't want to do it themselves and have it look bad. On the lense thing, I always used #9 for mig and 10 or 11 for stick, now I do need the magnifying lenses or I am welding off the line like the others as we age. Oh! Table looks great, put some material on there and back to practicing!
|
By charliemccraney - 14 Years Ago
|
That's enough practice for now. I'm a better welder than I was a month ago so that is good. Now I need to get those engines apart and inventoried so I can get them on the shelves and free up some floor space.
|
By pegleg - 14 Years Ago
|
Looks good Charlie. a couple of years from now you'll forget you ever didn't know how to weld!
|