Author
|
Message
|
Frankenstein57
|
|
Group: Forum Members
Last Active: 7 Years Ago
Posts: 131,
Visits: 891
|
I have a 120 volt flux core deal, I borrowed it from my sister. It's ok to weld thin stuff, that's why I borrowed it. It's also handy being portable, for chores out in the yard. But for what you are doing, a 220 stick welder with some 6011's or 6013's, and make it happen.

thanks, Mark
|
|
|
charliemccraney
|
|
Group: Moderators
Last Active: 6 hours ago
Posts: 6.1K,
Visits: 442.2K
|
This 120 does great now that I better know how to use it. I didn't even have issues with the duty cycle for this job.
Lawrenceville, GA
|
|
|
kevink1955
|
|
Group: Forum Members
Last Active: 2 Years Ago
Posts: 236,
Visits: 237.6K
|
Looking good, glad it's working out. As Tim Tailor would say, joining metal with fire way cool (insert grunt noise here)
|
|
|
charliemccraney
|
|
Group: Moderators
Last Active: 6 hours ago
Posts: 6.1K,
Visits: 442.2K
|
Yeah. It went very well. The hardest part was getting it all tacked together and square without any jigs or clamps. When welding was complete, all four corners were sitting flat on the floor. I did some reading about welding strategy to prevent warping and it seems to have paid off. Pulling is definitely the trick, if not in general, at least for these little welders (or for me). It sounds better, looks better, and according to my testing is better than pushing. I was planning to make the top easy to replace but after thinking about it some more, my easy to replace plan really isn't that easy. It will require that I make brackets to weld under the top in order to bolt it down without any bolt heads sticking through. The material I'm using for the top is too thin for any substantially sized countersunk screw, .119". I'd like to mount a vice so these mounting points will need to be able to take that abuse. Then I thought, how often will I need to replace it, probably not very often. So I'm just going to weld it several places along each side and a couple places on the underside, toward the middle. The welded top will also add a little more rigidity to the entire unit. It will be like a shear panel. Future replacement really will not be that difficult if it's ever required. I'll probably outgrow this table before then.
Lawrenceville, GA
|
|
|
57FordPU
|
|
Group: Forum Members
Last Active: 3 Years Ago
Posts: 726,
Visits: 73.6K
|
I like your project Charlie. Also sounds like you have become one with your welder. I know you are almost finished, but I thought I would share a few techniques that have helped me a great deal. I am no welding pro, but I have been forced into either learning or or watching someone else do it, and believe me I am still learning. I read everything I see on welding techniques and this thread is no different. I have a 220v Lincoln with mixed gas, so I haven't experienced as many problems as I would have if I had a 120v setup. I seldom weld anything thicker than .25", but when I do, multiple passes are required. Like Frank said, multiple passes without "V" grinding is futile. The pre heat method is doable with a torch, but instead of making a straight bead, I make multiple half moon shaped welds. For me, this seems to pre heat the metal ahead of the weld better than a single bead does. It also helps me to control the amount of material being laid down and avoids excessive build up. This technique also helps me a great deal with vertical and overhead welding. Needless to say, grinding every surface to be welded and even where the ground attaches makes even novices like me look good. When I am horizontal welding and the parts to be welded are easily accessible, I crank it up and run a single bead. My near site is not so good. The biggest problem staying on the desired location for me is lack of light. I place a flood light over my shoulder and this makes all the difference in the world. It not only helps me start in the best location, but actually helps me stay on track during the weld.
Charlie Burns Laton, Ca (South of Fresno)
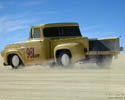
BurnsRacing981@gmail.com
|
|
|
charliemccraney
|
|
Group: Moderators
Last Active: 6 hours ago
Posts: 6.1K,
Visits: 442.2K
|
Prep is key. I learned that in the early days by trying to do it the "easy" way and then having to do it all again. I beveled every butt weld and the outside of every fillet, as if making a piece of angle iron. Some of my best looking welds ever are on this table but there are still quite a few not so great looking ones. It was difficult to find a comfortable position for some of them. Sometimes gussets and angle iron would get in the way of the pulling technique so I had to rotate the gun to get into the corner.
Lawrenceville, GA
|
|
|
MoonShadow
|
|
Group: Forum Members
Last Active: 5 hours ago
Posts: 4.6K,
Visits: 37.9K
|
I'll try the light over the sholder deal. Since I had cataract surgery I can't see the work piece once I strike an arc. Its like I get a double reflection. Chuck
Y's guys rule! Looking for McCullouch VS57 brackets and parts. Also looking for 28 Chrysler series 72 parts. And early Hemi parts.
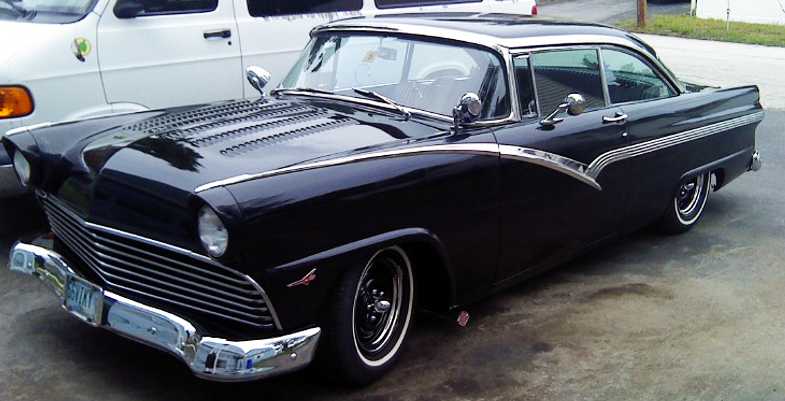 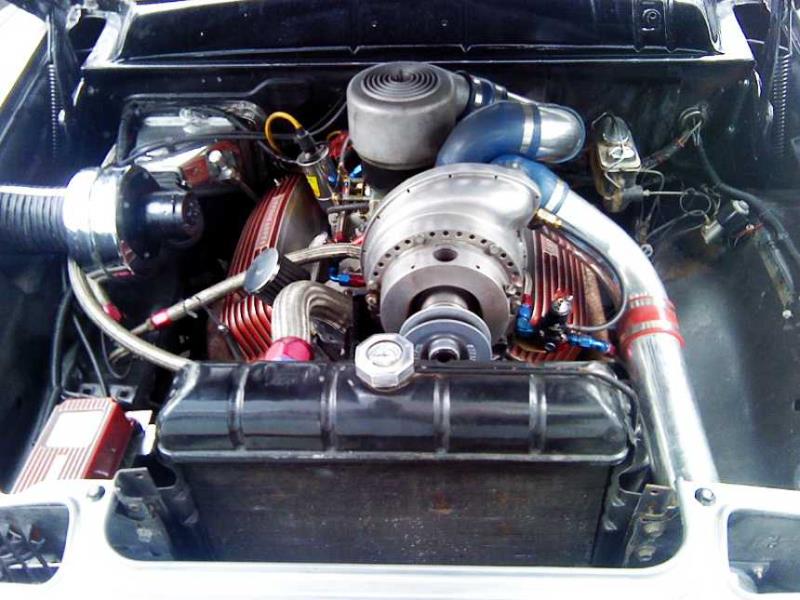 MoonShadow, 292 w/McCulloch, 28 Chrysler Roadster, 354 Hemi) Manchester, New Hampshire
|
|
|
rick55
|
|
Group: Forum Members
Last Active: 5 Years Ago
Posts: 550,
Visits: 4.4K
|
My near site is not so good. The biggest problem staying on the desired location for me is lack of light. I place a flood light over my shoulder and this makes all the difference in the world. It not only helps me start in the best location, but actually helps me stay on track during the weld. I used to have no end of trouble welding with a mig until i realized that the problem wasn't me so much as the mask i was using. Mig welding requires a lighter shade lens than stick welding. I was using my stick welding mask. I now use a variable shade mask and use it on one of the lower settings. It makes sense as it is obvious that the arc from a stick welder is much bigger and brighter than a mig. Here in Oz our single phase welders are 230-250 volt. A stick welder uses about 120 amps and 70 volts to weld 1/8" plate and a mig uses about 30 volts and 100 amps. The comparison in power is roughly 8500 watts to 3000 watts. This is also seen as light. So if you are having trouble seeing the weld try a mask that is compatible with what you are doing. If you use one of the variable light sensitive masks you will not need several masks or swapping lenses between jobs. These variable shade masks do take bit of getting used to but you don't get eye flashburns when you are using one. Regards Regards
Rick - West Australia Do Y Blocks Downunder run upside down? Gravity Sucks!!
|
|
|
MoonShadow
|
|
Group: Forum Members
Last Active: 5 hours ago
Posts: 4.6K,
Visits: 37.9K
|
I didn't mention but I am using a auto dim mask. Tried every setting but still couldn't see the work. Chuck
Y's guys rule! Looking for McCullouch VS57 brackets and parts. Also looking for 28 Chrysler series 72 parts. And early Hemi parts.
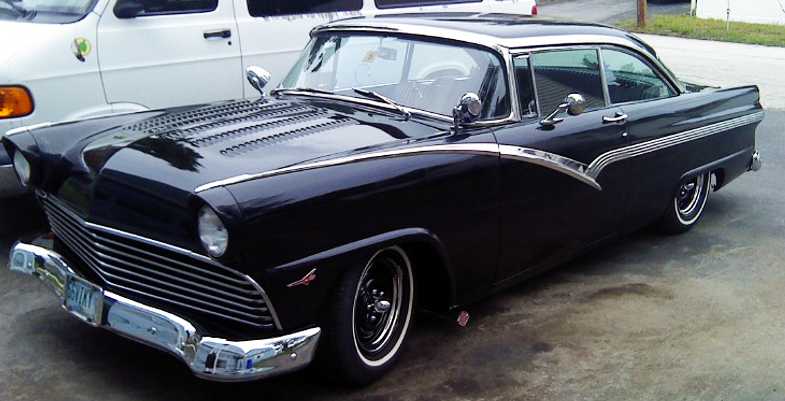 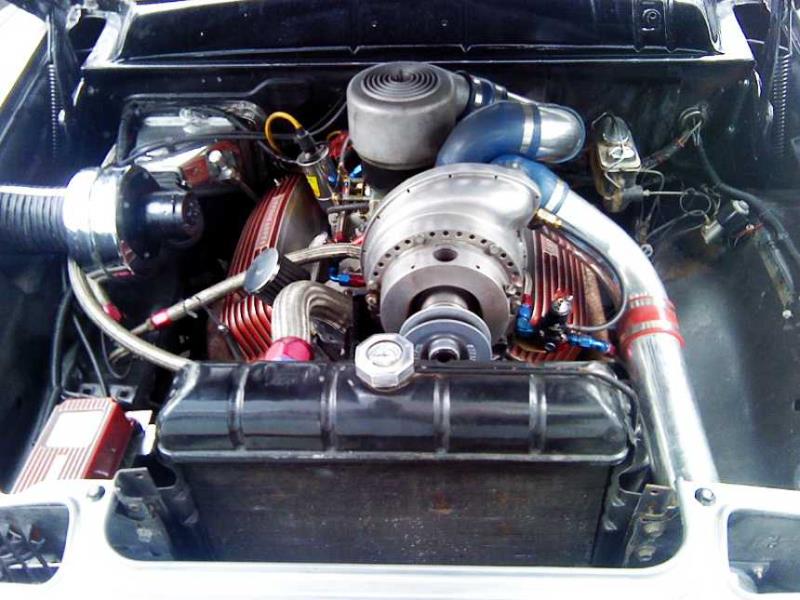 MoonShadow, 292 w/McCulloch, 28 Chrysler Roadster, 354 Hemi) Manchester, New Hampshire
|
|
|
pegleg
|
|
Group: Forum Members
Last Active: 3 Years Ago
Posts: 3.0K,
Visits: 8.7K
|
That reminded me of something else l've discovered. I found I could see the weld better with my safety glasses on the my "street" ones. I discovered that the street glasses, wich are the type that darken in the sun, also get very dark with the rays from the welder. So dark it's like having the lens too dark. That might help you Charlie. I also got a step lighter hood lens for the MIG, and that really helps your weld when you can see what you're doing!
Frank/RebopBristol, In ( by Elkhart)  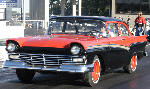
|
|
|