Author
|
Message
|
PF Arcand
|
|
Group: Forum Members
Last Active: Last Year
Posts: 3.3K,
Visits: 238.8K
|
Ted: Thanks for your reply & I certainly don't doubt it's accuracy. I thought it worth asking, particularly when you stated a priceof $3200 for a custom crank! Unfortunately, our favorite engine isn't one of the popular engines that the aftermarket makes reasonably priced cranks for..
Paul
|
|
|
NoShortcuts
|
|
Group: Forum Members
Last Active: 2 Years Ago
Posts: 1.4K,
Visits: 179.6K
|
Ted (3/15/2014)
PF Arcand (3/14/2014) Since this discussion has gotten into 4 " bores & custom order cranks, I've heard of welding cranks.. What about welding a 292" steel truck crank & then offset machining it? Is that feasable & possibly cost effective as compared to a full custom order crank? Welded cranks had a high failure rate with the life expectancy also being on the short side. Porosity, flaking off of weld, bearing wear issues, and breaking crankshafts are just some of the problems related to the welding up of crankshaft journals to increase the stroke. The advent of aftermarket cranks in both the forged and cast versions for the more popular engines has made the welding up of crankshafts for stroke increases a very unpopular option. Good information. Thanks, Ted. My list of 'things to do' (bucket list) just got reduced! 
Anybody need a steel crank?
NoShortcuts a.k.a. Charlie Brown near Syracuse, New York
|
|
|
Ted
|
|
Group: Administrators
Last Active: 6 hours ago
Posts: 7.4K,
Visits: 205.3K
|
PF Arcand (3/14/2014) Since this discussion has gotten into 4 " bores & custom order cranks, I've heard of welding cranks.. What about welding a 292" steel truck crank & then offset machining it? Is that feasable & possibly cost effective as compared to a full custom order crank? Welded cranks had a high failure rate with the life expectancy also being on the short side. Porosity, flaking off of weld, bearing wear issues, and breaking crankshafts are just some of the problems related to the welding up of crankshaft journals to increase the stroke. The advent of aftermarket cranks in both the forged and cast versions for the more popular engines has made the welding up of crankshafts for stroke increases a very unpopular option.
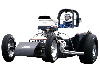 Lorena, Texas (South of Waco)
|
|
|
PF Arcand
|
|
Group: Forum Members
Last Active: Last Year
Posts: 3.3K,
Visits: 238.8K
|
Since this discussion has gotten into 4 " bores & custom order cranks, I've heard of welding cranks.. What about welding a 292" steel truck crank & then offset machining it? Is that feasable & possibly cost effective as compared to a full custom order crank?
Paul
|
|
|
Ted
|
|
Group: Administrators
Last Active: 6 hours ago
Posts: 7.4K,
Visits: 205.3K
|
CK and his 55Tbird (3/8/2014) ......I also read that the Crank shaft is rated to about 400HP I wonder how Ted's 500+HP engine treated the Crank? When planning for a 500+ HP Ford Y engine, then a billet steel crankshaft becomes part of that build. For the Y engines, I use Moldex Crankshaft Co. for the billet cranks which are in the $3200 neighborhood. An added feature on the custom cranks is the option of changing rod and/or main journal sizing, snout dimensions, flywheel flanges, etc. with the cost remaining the same. I've done these cranks with both a scrub flyheel flange so a Powerglide tranny would fit up easier and with a Ford FE flywheel flange so an FE bell-housing, flywheel, and starter could be more easily fitted up. For many builds, a $550-$650 cast crank stroker crankshaft would suffice if they were available for the Y.
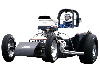 Lorena, Texas (South of Waco)
|
|
|
aussiebill
|
|
Group: Forum Members
Last Active: 5 Years Ago
Posts: 1.8K,
Visits: 11.4K
|
CK and his 55Tbird (3/8/2014) Apparently the trick is to heat the cast to 2-300*C during and after welding. Hence furnace brazing.Another option could be to remove the cylinders and recess the base for a new cylinder to be housed, and at the base sealed by some form of gasket/sealer. And having the deck removed then a new deck could be used with a recess to house the cylinders again like the lower cylinder. The deck plate and cyl. could then be held together by studs through to the crank portion of the block/ head bolts. 3bond or some sort of sealer could be used at all the new joining areas. Aluminium cylinders could be used or steel etc. Imagine 4.4" bores/3.3" stroke - 401CID I read that Mummert was considering making a block to match his heads! I also read that the Crank shaft is rated to about 400HP I wonder how Ted's 500+HP engine treated the Crank?
CK, unfortunatey all of that theory s not actually practicle on y blocks after youve bored block to fit 4" sleeves, other thanf/brazing the deck. There is no room or material to do it Ted, Tim and i have tried it with no success so far!. Gart Croan is trying for new cast block with big bore, not john. Teds cranks are by Moldex usually, All of the above are beyond the financial reach of most of us.
AussieBill YYYY Forever Y Block YYYY Down Under, Australia
|
|
|
charliemccraney
|
|
Group: Moderators
Last Active: 9 hours ago
Posts: 6.1K,
Visits: 442.3K
|
CK and his 55Tbird (3/8/2014) I also read that the Crank shaft is rated to about 400HP I wonder how Ted's 500+HP engine treated the Crank?It is a custom crank that can handle it.
Lawrenceville, GA
|
|
|
CK and his 55Tbird
|
|
Group: Forum Members
Last Active: 11 Years Ago
Posts: 104,
Visits: 273
|
Apparently the trick is to heat the cast to 2-300*C during and after welding. Hence furnace brazing.Another option could be to remove the cylinders and recess the base for a new cylinder to be housed, and at the base sealed by some form of gasket/sealer. And having the deck removed then a new deck could be used with a recess to house the cylinders again like the lower cylinder. The deck plate and cyl. could then be held together by studs through to the crank portion of the block/ head bolts. 3bond or some sort of sealer could be used at all the new joining areas. Aluminium cylinders could be used or steel etc. Imagine 4.4" bores/3.3" stroke - 401CID I read that Mummert was considering making a block to match his heads! I also read that the Crank shaft is rated to about 400HP I wonder how Ted's 500+HP engine treated the Crank?
|
|
|
CK and his 55Tbird
|
|
Group: Forum Members
Last Active: 11 Years Ago
Posts: 104,
Visits: 273
|
Yet i'm not suggesting around the cylinders, the actual deck.
|
|
|
aussiebill
|
|
Group: Forum Members
Last Active: 5 Years Ago
Posts: 1.8K,
Visits: 11.4K
|
CK and his 55Tbird (3/4/2014) Many years ago I had a repair to a cast iron head which had cracked. Mini coopers were common for this between cylinders.The means of repairing this was by an Arc weld, I was told they used a specific rod to meld the cast material. If we are still Referring to furnace brazeing the sleeves to make block rigid again, then arc welding would not be practicle as access and control is very limited, thats why flowing brazeing material is way it was done. Yes there are a few arc wedling rods for cast iron, i,ve had good success on exhaust manifolds with stainless steel rods, preparation is the key to this welding.
AussieBill YYYY Forever Y Block YYYY Down Under, Australia
|
|
|