By 55Victoria - 11 Years Ago
|
Hello. I own a 1955 Victoria with her original 272 Y-Block. The engine is getting tired, so I´m starting to think about a complete rebuild. 272 pistons are impossible to find here in Argentina, but I can easily find 292 pistons, because the F100 was produced with that engine here. The question is: Is it possible / advisable to bore the 272 block to standard 292 pistons? Does anyone tried this? Thanks a lot for your help. Kind regards. Augusto.
|
By aussiebill - 11 Years Ago
|
55Victoria (2/13/2014) Hello. I own a 1955 Victoria with her original 272 Y-Block. The engine is getting tired, so I´m starting to think about a complete rebuild. 272 pistons are impossible to find here in Argentina, but I can easily find 292 pistons, because the F100 was produced with that engine here. The question is: Is it possible / advisable to bore the 272 block to standard 292 pistons? Does anyone tried this? Thanks a lot for your help. Kind regards. Augusto.
Subject to other comments, i can only tell you i,v been donig it for over 40 yrs, boreing 272,s to 292 std bore, dont suggest going o/size on 292. There is allways possibility of cyl wall thickness but never had problem in that time.
|
By Rono - 11 Years Ago
|
Augusto;
Yes it is possible to bore from 272 to 292 specs. I did this with my 56 F-100. As Aussie Bill suggested, I wouldn't go with much more unless you have machine shops there that can sonic test the block for cylinder wall thickness and possible core shift.
Rono
|
By gekko13 - 11 Years Ago
|
Ted, I do not mean to hijack this thread but for the sake of conversation, what is your opinion of the practice of installing 8 sleeves? Thanks.
|
By vntgtrk - 11 Years Ago
|
gekko13 (2/15/2014) Ted, I do not mean to hijack this thread but for the sake of conversation, what is your opinion of the practice of installing 8 sleeves? Thanks.
Valid question. Would the OP be better off doing this and reusing the stock pistons? Provided they're sound of course
|
By aussiebill - 11 Years Ago
|
vntgtrk (2/15/2014)
gekko13 (2/15/2014) Ted, I do not mean to hijack this thread but for the sake of conversation, what is your opinion of the practice of installing 8 sleeves? Thanks. Valid question. Would the OP be better off doing this and reusing the stock pistons? Provided they're sound of course
Unnecessary expense just to use old pistons in my view.
|
By CK and his 55Tbird - 11 Years Ago
|
Gee I hope my 272 is OK I've just had it bored .020" up on 292.
Has anyone tried coating iron blocks like aluminium motor cycle bores are nickel plated? What about ceramic coatings????
|
By vntgtrk - 11 Years Ago
|
aussiebill (2/15/2014)
vntgtrk (2/15/2014)
gekko13 (2/15/2014) Ted, I do not mean to hijack this thread but for the sake of conversation, what is your opinion of the practice of installing 8 sleeves? Thanks. Valid question. Would the OP be better off doing this and reusing the stock pistons? Provided they're sound of course Unnecessary expense just to use old pistons in my view.
I agree. But if they aren't available..........
|
By ian57tbird - 11 Years Ago
|
What is considered as a minimum safe final wall thickness after boring? I'm guessing that would also vary between major and minor thrust sides.
|
By ian57tbird - 11 Years Ago
|
Others will probably know more about this than me.
I recall reading an article on the internet quite some time ago about trying to get max cubes out of Yblock for a dyno shoot out. The engine was sleeved on all eight cylinders and I think they had problems with water getting into the oil. After tearing the engine down it was discovered that the block had twisted through lack of rigidity after being sleeved on all eight.
Would that only be an issue when trying to produce maximum power?
|
By aussiebill - 11 Years Ago
|
ian57tbird (2/17/2014) Others will probably know more about this than me.
I recall reading an article on the internet quite some time ago about trying to get max cubes out of Yblock for a dyno shoot out. The engine was sleeved on all eight cylinders and I think they had problems with water getting into the oil. After tearing the engine down it was discovered that the block had twisted through lack of rigidity after being sleeved on all eight.
Would that only be an issue when trying to produce maximum power?
Ian, i think that was the 4" engine ? TED ? In normal sleeve installation and fitted correctly as Ted points out, that would be unlikely. its when reaching for the stars that you push the boundaries.
|
By gekko13 - 11 Years Ago
|
Ted: the reason for my original query was not to suggest re-fitting used pistons. In as much as the alloy cylinder block project seems to be still born, what is possible to achieve with 8 high quality sleeves in a factory 272 or 292 block? Combined with a small diameter, offset ground crankshaft, can a reliable "big inch motor" be built for the street and occasional quarter mile laps?
|
By ian57tbird - 11 Years Ago
|
Exactly what I was thinking, that was the question on my mind as well.
|
By aussiebill - 11 Years Ago
|
ian57tbird (2/17/2014) Others will probably know more about this than me.
I recall reading an article on the internet quite some time ago about trying to get max cubes out of Yblock for a dyno shoot out. The engine was sleeved on all eight cylinders and I think they had problems with water getting into the oil. After tearing the engine down it was discovered that the block had twisted through lack of rigidity after being sleeved on all eight.
Would that only be an issue when trying to produce maximum power?
Ian YES !, i think that was the 4" engine ? TED ? In normal sleeve installation and fitted correctly as Ted points out, that would be unlikely. its when reaching for the stars that you push the boundaries. In normal sleeving situaton there is still original block walls to support sleeevs, but critical thing is when trying to bore block out for largest diameter bore/sleeve size, then the deck isnt attached to the walls strongly, thus big load as you mention causes leaks at sleeve and deck area, this is in the case of more than normal boresizes wanted. I think TED and TIM have tried it, i havent fired mine up yet. My memories fadeing but i know TED is full book on it.
|
By aussiebill - 11 Years Ago
|
TED, thanks for clarifying my suggetions and the guys have clearer understanding. Your word for word answer described the problems of the 4" sleeve/deck problem and furnace brazeing is unaailable here also, hence i,m not holding out for success with my 4" er, fingers x,d. Allways look forward to your clinical and precise explanations, best regards bill.
P.S, is it just me or site, when typing, some of the letters are missig in the words and have to be retyped??
|
By lyonroad - 11 Years Ago
|
[b]. P.S, is it just me or site, when typing, some of the letters are missig in the words and have to be retyped??
Its not you Bill. ts ben going on for some months now.
|
By mctim64 - 11 Years Ago
|
Yes, I did not have good luck with the eight thick walled sleeves and a 4" bore. Ran great for a couple of passes and then went to pumping water. A lesson learned the hard way, and that was with a solid filled block.
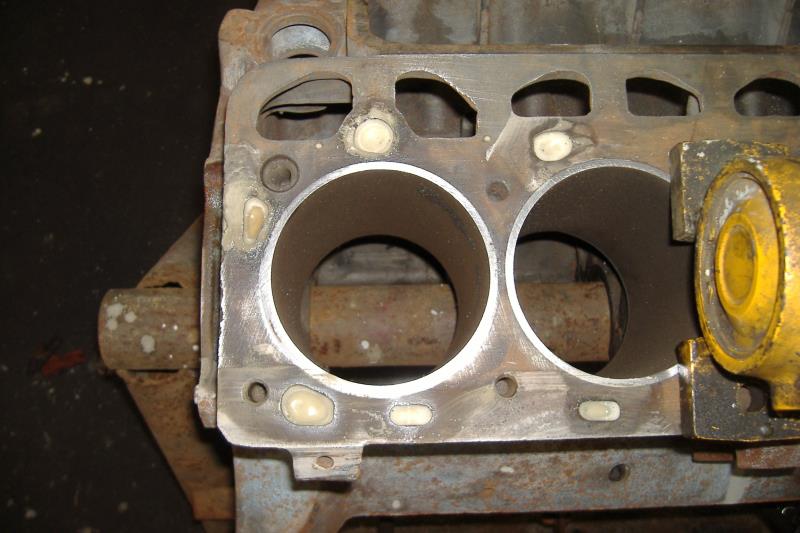
|
By gekko13 - 11 Years Ago
|
Just wondering out loud, could a solid copper (no coolant passages) head gasket have prevented that?
|
By LordMrFord - 11 Years Ago
|
mctim64 (2/19/2014)
Yes, I did not have good luck with the eight thick walled sleeves and a 4" bore. Ran great for a couple of passes and then went to pumping water. A lesson learned the hard way, and that was with a solid filled block.
Y-Block bored to death.
Some Turbo-Nissan guys use steel plate sinked in top of the block. Supports the cylinders from doing that when they take 600hp from engine what weights about same as one the Y-Block cylinder head.
|
By mctim64 - 11 Years Ago
|
gekko13 (2/19/2014) Just wondering out loud, could a solid copper (no coolant passages) head gasket have prevented that?
Nope! Tried that.
|
By aussiebill - 11 Years Ago
|
mctim64 (2/20/2014)
gekko13 (2/19/2014) Just wondering out loud, could a solid copper (no coolant passages) head gasket have prevented that? Nope! Tried that. 
Tim, although starting 4 " project some 15 yrs ago, ive just been at it on/off, covered up till next time. As i,ve seen ted and your results i hold no happiness in ts future, but will see i i can add it to the pile.
yyy
|
By ian57tbird - 11 Years Ago
|
Is the block deck flexing as it is no longer tied to the lower part of the block?
|
By CK and his 55Tbird - 11 Years Ago
|
A few years back I came across a set of diesel sleeves which were stainless steel and about 040" thick with a rolled lip at the top which is what held it in place.Perhaps with something like this the original bore can be left in place and machined to fit a slimmer steel sleeve.
|
By CK and his 55Tbird - 11 Years Ago
|
Ok, so this is a bit out there and it may be costly.
What if the cylinders where bored out completely including the inner portion of the deck, leaving an outer silhouette of a block deck. Some alterations could be done in the water jacket area. Then a set of larger cylinders attached (precast) to the new inner deck area. This new cylinders would then be pressed into the base of the water jackets and welded, as with the new inner deck area. Maybe web between the banks to for extra rigidity.
Well, what do you think?
|
By Glen Henderson - 11 Years Ago
|
Sounds super expensive even if you could find someone to do it and still most likely want work. The Y block is what it is, just like the Flathead before it. My thoughts are if you really have to have a four plus in bore, find a good FE engine.
|
By CK and his 55Tbird - 11 Years Ago
|
Apparently the Y block crank will bolt straight into a 302 windsor and create a 340.3.3" stroke 4" bore opposed to Y Block -292 B:3.75" and S:3.3" Windsor -302 B:4" and S:3"
|
By aussiebill - 11 Years Ago
|
CK and his 55Tbird (2/25/2014) Apparently the Y block crank will bolt straight into a 302 windsor and create a 340.3.3" stroke 4" bore opposed to Y Block -292 B:3.75" and S:3.3" Windsor -302 B:4" and S:3"
RUBBISH! Also cant see why you want to reinvent the wheel with the sleeve theorys, dreams?, once you bore through the original walls, any reliabilty, longevity is at a minumn. The most expeirenced people here have tried and explained it all i thought !
|
By aussiebill - 11 Years Ago
|
Glen Henderson (2/25/2014) Sounds super expensive even if you could find someone to do it and still most likely want work. The Y block is what it is, just like the Flathead before it. My thoughts are if you really have to have a four plus in bore, find a good FE engine.
Glen, words of wisdom to the deaf !
|
By Pete 55Tbird - 11 Years Ago
|
As far as a 292 Yblock crank being used in a 289/302 I think it has been done. I bought a 66 Shelby 350 in the late 1970`s that had been a drag strip car. The engine was replaced by a plain 302 but in the trunk there was a set of professionally ported hipo heads and a steel Yblock 292 crank. That was extensively re worked, stroked ( offset ground) I never tried it myself but I gave it to a guy who road raced his GT350R and I lost track of him so I never knew if he used it or not. Pete
|
By ian57tbird - 11 Years Ago
|
My brother mentioned a while back that he recalled reading in a car mag many years ago the mod to install a Y crank in a Windsor when I mentioned about bore spacing being the same.
|
By CK and his 55Tbird - 11 Years Ago
|
Of course no one would want to work away from the Y block anyway, that would be ridiculous.
And I did mention with the opening sentence "Ok, so this is a bit out there and may be a bit costly"
Words are only words to the wise.
|
By Glen Henderson - 11 Years Ago
|
I have been told that Fords Indy engines of the early 60's used a crank that was based on the 292 steel crank. If I remember right rules limited the engines to 255 ci. I have no idea how much machine work went into the block or crank to make this combo work, but I will assure you that it was not plug and play.
|
By pegleg - 11 Years Ago
|
As regards the 292 crank in the Windsor. This was pretty common when the 260/289's first came out, in drag racing circles. There were no aftermarket cranks available for the SBF's let alone Steel cranks. When you wanted to run a Ford in an Altered, Gasser or Rail and needed more displacement to race 327 Scrubs it was a useful trick. Problem was the early 289 heads didn't flow enough for a good 289. Really didn't work on a 330 or 40 incher.
|
By RodL - 11 Years Ago
|
Hi all, I've just come across this thread. I was given an unused of Silvolite pistons 292 +60 to put in my 272. Am I going to get into trouble with this combination? RodL
|
By Glen Henderson - 11 Years Ago
|
292 +60 = 312 +10 or 3.810, I would not do it without sonic checking the block as has been stated before. You may get lucky and have a block that will go that big, but the only safe way is to have it checked.
|
By John Mummert - 11 Years Ago
|
I have bored a number of 272 blocks to std 292 and a few to 292 +.020" and 2 to 292 +.060". I have only seen 1 that had a problem at 292 +.020". In looking at it closer we found that the water jackets were serious corroded from running tap water. We recently bored a 256 block to 292 +.020". Sonic testing showed that was a safe bore.While sonic testing 272 blocks I found cylinders as thick as .395" and never found anything under .200". The old Dearborn blocks were very thick, in fact a 272 DIF block weighs more than a 292 Cleveland block and I'm guessing that much of the weight is in the cylinders. Having said that, I would sonic test any 272 I was boring past std 292.
|
By RodL - 11 Years Ago
|
Thanks John & Glenn, I will get my block tested. John, this may result in a minor adjustment to my current order. RodL Be in touch by PM or phone soon.
|
By CK and his 55Tbird - 11 Years Ago
|
Many years ago I had a repair to a cast iron head which had cracked. Mini coopers were common for this between cylinders.The means of repairing this was by an Arc weld, I was told they used a specific rod to meld the cast material.
|
By aussiebill - 11 Years Ago
|
CK and his 55Tbird (3/4/2014) Many years ago I had a repair to a cast iron head which had cracked. Mini coopers were common for this between cylinders.The means of repairing this was by an Arc weld, I was told they used a specific rod to meld the cast material.
If we are still Referring to furnace brazeing the sleeves to make block rigid again, then arc welding would not be practicle as access and control is very limited, thats why flowing brazeing material is way it was done. Yes there are a few arc wedling rods for cast iron, i,ve had good success on exhaust manifolds with stainless steel rods, preparation is the key to this welding.
|
By CK and his 55Tbird - 11 Years Ago
|
Yet i'm not suggesting around the cylinders, the actual deck.
|
By CK and his 55Tbird - 11 Years Ago
|
Apparently the trick is to heat the cast to 2-300*C during and after welding. Hence furnace brazing.Another option could be to remove the cylinders and recess the base for a new cylinder to be housed, and at the base sealed by some form of gasket/sealer. And having the deck removed then a new deck could be used with a recess to house the cylinders again like the lower cylinder. The deck plate and cyl. could then be held together by studs through to the crank portion of the block/ head bolts. 3bond or some sort of sealer could be used at all the new joining areas. Aluminium cylinders could be used or steel etc. Imagine 4.4" bores/3.3" stroke - 401CID I read that Mummert was considering making a block to match his heads! I also read that the Crank shaft is rated to about 400HP I wonder how Ted's 500+HP engine treated the Crank?
|
By aussiebill - 11 Years Ago
|
CK and his 55Tbird (3/8/2014) Apparently the trick is to heat the cast to 2-300*C during and after welding. Hence furnace brazing.Another option could be to remove the cylinders and recess the base for a new cylinder to be housed, and at the base sealed by some form of gasket/sealer. And having the deck removed then a new deck could be used with a recess to house the cylinders again like the lower cylinder. The deck plate and cyl. could then be held together by studs through to the crank portion of the block/ head bolts. 3bond or some sort of sealer could be used at all the new joining areas. Aluminium cylinders could be used or steel etc. Imagine 4.4" bores/3.3" stroke - 401CID I read that Mummert was considering making a block to match his heads! I also read that the Crank shaft is rated to about 400HP I wonder how Ted's 500+HP engine treated the Crank?
CK, unfortunatey all of that theory s not actually practicle on y blocks after youve bored block to fit 4" sleeves, other thanf/brazing the deck. There is no room or material to do it Ted, Tim and i have tried it with no success so far!. Gart Croan is trying for new cast block with big bore, not john. Teds cranks are by Moldex usually, All of the above are beyond the financial reach of most of us.
|
By PF Arcand - 11 Years Ago
|
Since this discussion has gotten into 4 " bores & custom order cranks, I've heard of welding cranks.. What about welding a 292" steel truck crank & then offset machining it? Is that feasable & possibly cost effective as compared to a full custom order crank?
|
By NoShortcuts - 11 Years Ago
|
Ted (3/15/2014)
PF Arcand (3/14/2014) Since this discussion has gotten into 4 " bores & custom order cranks, I've heard of welding cranks.. What about welding a 292" steel truck crank & then offset machining it? Is that feasable & possibly cost effective as compared to a full custom order crank? Welded cranks had a high failure rate with the life expectancy also being on the short side. Porosity, flaking off of weld, bearing wear issues, and breaking crankshafts are just some of the problems related to the welding up of crankshaft journals to increase the stroke. The advent of aftermarket cranks in both the forged and cast versions for the more popular engines has made the welding up of crankshafts for stroke increases a very unpopular option.
Good information. Thanks, Ted. My list of 'things to do' (bucket list) just got reduced! 
Anybody need a steel crank?
|
By PF Arcand - 11 Years Ago
|
Ted: Thanks for your reply & I certainly don't doubt it's accuracy. I thought it worth asking, particularly when you stated a priceof $3200 for a custom crank! Unfortunately, our favorite engine isn't one of the popular engines that the aftermarket makes reasonably priced cranks for..
|
By charliemccraney - 11 Years Ago
|
I wonder if you could us some high grade all thread rod for head studs that go all the way through and tie the upper and lower portion of the water jacket together. Or maybe dowels in the upper an lower portion of the sleeve. Maybe the head bolt bosses would have enough meat up top. Not sure about the bottom.
Both will have challenges but may be possible.
|
By charliemccraney - 11 Years Ago
|
CK and his 55Tbird (3/8/2014) I also read that the Crank shaft is rated to about 400HP I wonder how Ted's 500+HP engine treated the Crank? It is a custom crank that can handle it.
|
By Ted - 11 Years Ago
|
As Bill and Rono bring up, going past a standard 292 bore gets the 272 block really on the thin side. Sonic testing the block will at least show where the core shift is located which can help the machinist in moving the boring bar to help equalize the cylinder wall thicknesses. Here are some past threads on the subject. http://forums.y-blocksforever.com/FindPost18677.aspx http://forums.y-blocksforever.com/FindPost41511.aspx http://forums.y-blocksforever.com/FindPost41541.aspx http://forums.y-blocksforever.com/FindPost39639.aspx
|
By Ted - 11 Years Ago
|
In looking for the original post that had the sonic sheet for a 272 that had been bored to a standard 292 size, I find that it must have been on the old site as it’s no longer available. With that in mind, here's another sonic sheet for an over-bored 272. The bore thicknesses highlighted in red do make this block questionable for use. Had the block been sonic checked first and then offset bored to compensate for core shift, then the block could have still been more suitable for use.
|
By Ted - 11 Years Ago
|
CK and his 55Tbird (2/15/2014) ...Has anyone tried coating iron blocks like aluminium motor cycle bores are nickel plated? What about ceramic coatings???? I’ve refrained from using ceramic coatings on the street engines simply due to the hours or cycle times in which the coatings are good for. If those coatings start to peel or lose their adhesion properties after an extended period of time, then that debris will damage the cylinder walls and rings.
|
By Ted - 11 Years Ago
|
gekko13 (2/15/2014) Ted, I do not mean to hijack this thread but for the sake of conversation, what is your opinion of the practice of installing 8 sleeves? Thanks. Sleeves properly installed should pose no problem but as mentioned, the cost is prohibitive when attempting to do all eight cylinders. Not all machine shops are capable of properly installing sleeves so be cautious when getting that operation performed. Using used pistons is fine as long as they are in ‘like new’ condition but unless they are low mileage, that will likely not be the case. The money that is spent to sleeve eight cylinders in a block to use a set of old pistons is much better spent on a set of custom pistons that are sized to fit the next oversize of bore or ring sizing availability. And with custom pistons comes the ability to use a more modern piston ring design which helps with both the power and efficiency of the engine.
|
By Ted - 11 Years Ago
|
ian57tbird (2/16/2014) What is considered as a minimum safe final wall thickness after boring? I'm guessing that would also vary between major and minor thrust sides.The accepted minimum cylinder wall thickness is 0.100”. Boosted or high horsepower applications will typically require more than this.
|
By Ted - 11 Years Ago
|
As Bill brings up, simply boring the block for big bore sleeves destroys the built in support between the decks and the main webbing. To simply sleeve the block for the sake of sleeving gains you nothing in cylinder wall wear or block integrity. In the grand scheme of things, any installed sleeve in an iron block actually weakens the block integrity to some degree as the original cylinder wall thickness is compromised. . Sleeves for the Ford Y-Block engines are reserved simply for those cylinders that need repairing due to some kind of damage. If the original cylinder wall is severely damaged to the point where the ring wearing surface is exposed to coolant (cracks, holes, etc), then even a sleeve may not be an adequate repair due to the head gasket design on the Y engines. Most engines have a round sealing ring on the head gasket that can catch the top of a sleeve for sealing purposes but the unique design of the Y combustion chamber requires the use of a head gasket that does not fully seat on the edge of the bore. If there’s a chance for coolant seepage between the sleeve and the original cylinder wall, it typically happens because the head gasket is sealing on the deck and not the edge of the bore. . It was my 4” bore engine that was sleeved in such a manner that the original cylinder walls were removed to accommodate the thick wall sleeve installation. While the engine made a tremendous amount of power, the block did take a twist early on which allowed coolant seepage between the decks and the installed sleeves. Furnace brazing the block may have helped with this but that operation is not available in my part of the country. . On a lesser horsepower engine, this problem would have still occurred but simply would have taken longer for it to take place. An example I have is a 347” Y here that was fully sleeved and it did manage to run for awhile before coolant seepage came to the forefront. In examining the water jackets on that engine, some of the sleeves did break through the original cylinder walls which reduces the block strength and also gives the coolant a path to the top of the deck when conditions are right. That engine will be put together again as a smaller bore engine without sleeves.
|
By Ted - 11 Years Ago
|
ian57tbird (2/21/2014) Is the block deck flexing as it is no longer tied to the lower part of the block?
That would be an affirmative“Yes”. Ford 292/312 blocks using big bore sleeves tend to crack the decks between the cylinders as well as have water seepage between the sleeve and the deck into the combustion chamber where the head gasket is not residing on the edge of the cylinder itself.
CK and his 55Tbird (2/22/2014) A few years back I came across a set of diesel sleeves which were stainless steel and about 040" thick with a rolled lip at the top which is what held it in place.Perhaps with something like this the original bore can be left in place and machined to fit a slimmer steel sleeve.
Not many 292 blocks will bore out to the 4+” bore required for big bore sleeves without breaking through at least a part of the cylinder walls. Core shift within the block has a lot to do with how severe that cylinder wall offset will be and the subsequent complete boring away of part or all of the cylinder walls. If the cylinder head had a combustion chamber that was fully within the bore confines, then a head gasket with a perfectly round sealing ring could catch the top of the sleeve and minimize the water leakage issue regardless of what was going on between the sleeve and what was remaining of the existing cylinder wall. Granted that this would not be a total fix but this would go a long way towards addressing the water seepage issue with big bore sleeves. . Cylinder wall integrity has much to do with making the big horsepower numbers. Minimal cylinder wall thickness simply promotes cylinder wall flex which in turn costs some serious horsepower as well as setting the cylinder wall up for an early failure. It’s for this reason that cylinder walls are intentionally left at smaller bores so that the cylinder walls can be thicker in boosted applications. A case in point is when building the engine for Randy Gummelt’s rear engine dragster, the bore size was intentionally left at 3.800” bore rather than the 3.860" bore used on a serious normally aspirated Y engine build.
|
By Ted - 11 Years Ago
|
CK and his 55Tbird (2/25/2014) Ok, so this is a bit out there and it may be costly.
What if the cylinders were bored out completely including the inner portion of the deck, leaving an outer silhouette of a block deck. Some alterations could be done in the water jacket area. Then a set of larger cylinders attached (precast) to the new inner deck area. This new cylinders would then be pressed into the base of the water jackets and welded, as with the new inner deck area. Maybe web between the banks to for extra rigidity.
Well, what do you think?
That’s where furnace brazing comes into play. Unfortunately that’s not available in my area. I did try soldering both ends of the sleeve from the water jacket sides and putting a layer of resin at both the upper and lower portions of the bores within the water jackets but that also failed. For what I'm doing, a 375 incher is as big as it gets and still be a reliable combination.
|
By Ted - 11 Years Ago
|
CK and his 55Tbird (3/8/2014) ......I also read that the Crank shaft is rated to about 400HP I wonder how Ted's 500+HP engine treated the Crank? When planning for a 500+ HP Ford Y engine, then a billet steel crankshaft becomes part of that build. For the Y engines, I use Moldex Crankshaft Co. for the billet cranks which are in the $3200 neighborhood. An added feature on the custom cranks is the option of changing rod and/or main journal sizing, snout dimensions, flywheel flanges, etc. with the cost remaining the same. I've done these cranks with both a scrub flyheel flange so a Powerglide tranny would fit up easier and with a Ford FE flywheel flange so an FE bell-housing, flywheel, and starter could be more easily fitted up. For many builds, a $550-$650 cast crank stroker crankshaft would suffice if they were available for the Y.
|
By Ted - 11 Years Ago
|
PF Arcand (3/14/2014) Since this discussion has gotten into 4 " bores & custom order cranks, I've heard of welding cranks.. What about welding a 292" steel truck crank & then offset machining it? Is that feasable & possibly cost effective as compared to a full custom order crank? Welded cranks had a high failure rate with the life expectancy also being on the short side. Porosity, flaking off of weld, bearing wear issues, and breaking crankshafts are just some of the problems related to the welding up of crankshaft journals to increase the stroke. The advent of aftermarket cranks in both the forged and cast versions for the more popular engines has made the welding up of crankshafts for stroke increases a very unpopular option.
|