Author
|
Message
|
gekko13
|
|
Group: Forum Members
Last Active: 8 Years Ago
Posts: 128,
Visits: 2.6K
|
Ted: the reason for my original query was not to suggest re-fitting used pistons. In as much as the alloy cylinder block project seems to be still born, what is possible to achieve with 8 high quality sleeves in a factory 272 or 292 block? Combined with a small diameter, offset ground crankshaft, can a reliable "big inch motor" be built for the street and occasional quarter mile laps?
|
|
|
aussiebill
|
|
Group: Forum Members
Last Active: 5 Years Ago
Posts: 1.8K,
Visits: 11.4K
|
ian57tbird (2/17/2014) Others will probably know more about this than me.
I recall reading an article on the internet quite some time ago about trying to get max cubes out of Yblock for a dyno shoot out. The engine was sleeved on all eight cylinders and I think they had problems with water getting into the oil. After tearing the engine down it was discovered that the block had twisted through lack of rigidity after being sleeved on all eight.
Would that only be an issue when trying to produce maximum power?Ian, i think that was the 4" engine ? TED ? In normal sleeve installation and fitted correctly as Ted points out, that would be unlikely. its when reaching for the stars that you push the boundaries.
AussieBill YYYY Forever Y Block YYYY Down Under, Australia
|
|
|
ian57tbird
|
|
Group: Forum Members
Last Active: Last Week
Posts: 498,
Visits: 21.5K
|
Others will probably know more about this than me.
I recall reading an article on the internet quite some time ago about trying to get max cubes out of Yblock for a dyno shoot out. The engine was sleeved on all eight cylinders and I think they had problems with water getting into the oil. After tearing the engine down it was discovered that the block had twisted through lack of rigidity after being sleeved on all eight.
Would that only be an issue when trying to produce maximum power?
|
|
|
Ted
|
|
Group: Administrators
Last Active: Last Week
Posts: 7.4K,
Visits: 205.4K
|
ian57tbird (2/16/2014) What is considered as a minimum safe final wall thickness after boring? I'm guessing that would also vary between major and minor thrust sides.The accepted minimum cylinder wall thickness is 0.100”. Boosted or high horsepower applications will typically require more than this.
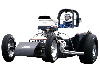 Lorena, Texas (South of Waco)
|
|
|
Ted
|
|
Group: Administrators
Last Active: Last Week
Posts: 7.4K,
Visits: 205.4K
|
gekko13 (2/15/2014) Ted, I do not mean to hijack this thread but for the sake of conversation, what is your opinion of the practice of installing 8 sleeves? Thanks. Sleeves properly installed should pose no problem but as mentioned, the cost is prohibitive when attempting to do all eight cylinders. Not all machine shops are capable of properly installing sleeves so be cautious when getting that operation performed. Using used pistons is fine as long as they are in ‘like new’ condition but unless they are low mileage, that will likely not be the case. The money that is spent to sleeve eight cylinders in a block to use a set of old pistons is much better spent on a set of custom pistons that are sized to fit the next oversize of bore or ring sizing availability. And with custom pistons comes the ability to use a more modern piston ring design which helps with both the power and efficiency of the engine.
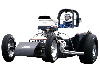 Lorena, Texas (South of Waco)
|
|
|
Ted
|
|
Group: Administrators
Last Active: Last Week
Posts: 7.4K,
Visits: 205.4K
|
CK and his 55Tbird (2/15/2014) ...Has anyone tried coating iron blocks like aluminium motor cycle bores are nickel plated? What about ceramic coatings???? I’ve refrained from using ceramic coatings on the street engines simply due to the hours or cycle times in which the coatings are good for. If those coatings start to peel or lose their adhesion properties after an extended period of time, then that debris will damage the cylinder walls and rings.
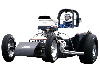 Lorena, Texas (South of Waco)
|
|
|
ian57tbird
|
|
Group: Forum Members
Last Active: Last Week
Posts: 498,
Visits: 21.5K
|
What is considered as a minimum safe final wall thickness after boring? I'm guessing that would also vary between major and minor thrust sides.
|
|
|
vntgtrk
|
|
Group: Forum Members
Last Active: 11 Years Ago
Posts: 75,
Visits: 144
|
aussiebill (2/15/2014)
vntgtrk (2/15/2014)
gekko13 (2/15/2014) Ted, I do not mean to hijack this thread but for the sake of conversation, what is your opinion of the practice of installing 8 sleeves? Thanks. Valid question. Would the OP be better off doing this and reusing the stock pistons? Provided they're sound of course Unnecessary expense just to use old pistons in my view. I agree. But if they aren't available..........
|
|
|
CK and his 55Tbird
|
|
Group: Forum Members
Last Active: 11 Years Ago
Posts: 104,
Visits: 273
|
Gee I hope my 272 is OK I've just had it bored .020" up on 292.
Has anyone tried coating iron blocks like aluminium motor cycle bores are nickel plated? What about ceramic coatings????
|
|
|
aussiebill
|
|
Group: Forum Members
Last Active: 5 Years Ago
Posts: 1.8K,
Visits: 11.4K
|
vntgtrk (2/15/2014)
gekko13 (2/15/2014) Ted, I do not mean to hijack this thread but for the sake of conversation, what is your opinion of the practice of installing 8 sleeves? Thanks. Valid question. Would the OP be better off doing this and reusing the stock pistons? Provided they're sound of course Unnecessary expense just to use old pistons in my view.
AussieBill YYYY Forever Y Block YYYY Down Under, Australia
|
|
|