Author
|
Message
|
RB
|
|
Group: Forum Members
Last Active: 4 days ago
Posts: 658,
Visits: 16.7K
|
A little bit more about the problems on Jerry's EMC engine...We discovered the broken rocker arm first.. It looks like a failure due to the shaft being bushed with a bronze bushing and the rocker body broke in a thin spot.. The rockers were R&R'd by Rocker Am Specialists. I have a set from them as well but mine are not bushed. I suppose it is possible the the broken rocker somehow jammed into the adjacent cylinder and caused the lifter failure, but I don't think so.. It was later that the lifter failed. . When we discoverd the rocker failure we installed a different rocker shaft and resumed testing.. Our first thought when we dicovered lifter failure was that we had piston to valve interference. We pulled the head expecting to find bent valves and obvious areas of contact. Not so.. the valves were fine... Upon reflection if it had been a contact or interference issue the pushrod should have been bent, it is the weakest link and is normally what fails before any other parts break. Neither was the cam lobe ruined, aside from some scars where the stem of the lifter left scratches as the engine continued to run. . In my mind it was simply a lifter failure.. for what ever reason..The lifter appears to have broke at the stem foot junction. Maybe an internal flaw in the metal. These lifters are undercut at the stem foot intersection.. My understanding is that this is preferable to a sharp corner in this area and is much easier to manufacture than a lifter with a radiused corner.
Given that these failures seem to be rare I would not necessarily point fingers at any one supplier.. Somes stuff just happens.
|
|
|
Y block Billy
|
|
Group: Forum Members
Last Active: 7 Years Ago
Posts: 1.6K,
Visits: 5.2K
|
Another scenario could be that the broken rocker arm jammed under the adjescent cylinder rocker arm, preventing the valve from opening and forcing too much pressure on the lifter, causing that failure. (a scenario where the weak pushrods would have come in handy if it was the case) Ted, On the undercutting, do you have a picture of how they are undercut? in my world of large machinery, normally when a head shaft failure occurs, its because it was locally made and they did not radius them properly, rather cut square corners on the steps of the shafting. I understand how the radiuses strengthen the joint but not clear how the undercut strengthens them?
 55 Vicky & customline 58 Rack Dump, 55 F350 yard truck, 57 F100 59 & 61 P 400's, 58 F100 custom cab, 69 F100, 79 F150, 82 F600 ramp truck, 90 mustang conv 7 up, 94 Mustang, Should I continue?
|
|
|
Barry L
|
|
Group: Forum Members
Last Active: 2 Years Ago
Posts: 217,
Visits: 6.7K
|
Hi John, The broken rocker was a stock style with bronze bushing and it looked kinda thin after it was bored for the bushing. It broke right on the shaft center-line. This rocker was not next to the faulty lifter, but on the adjacent cylinder. Barry
|
|
|
Hoosier Hurricane
|
|
Group: Moderators
Last Active: 1 hour ago
Posts: 3.7K,
Visits: 322.8K
|
In reading the YBM article on Jerry's engine, it was stated the broken rocker arm was adjacent to the broken lifter. How about this scenario? The exhaust rocker broke, the valve closed, the cylinder fired, and the exhaust valve could not open again. Cylinder pressure would be quite high, acting against a couple square inches of intake valve head. If cylinder pressure was only 500 psi (and I would expect it to be higher than that) at that point, it would be holding the valve closed with 1000 pounds of force. would this break the lifter as it tried to open the valve?
John - "The Hoosier Hurricane"
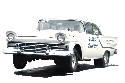
|
|
|
Ted
|
|
Group: Administrators
Last Active: 2 hours ago
Posts: 7.4K,
Visits: 205.6K
|
PF Arcand (1/6/2011) Ted: A thought based on your observation about the undercut on the lifters you use. If a lifter without sufficient undercut jambed in the block, could that also break a rocker arm? Maybe the lifters Schumann sourced, are oversize under the head?...The lifter would have to be jammed extremely hard to create an issue at a rocker arm. Valve spring pressure by itself is expected to be more than adequate to free up a stuck lifter. The lifter foots have an 1/8” or more clearance between the top of the lobes and being in a position to be jammed at the bottom of the block so for a lifter to get jammed on an engine that has already had the valves set, something else is going to be out of kilter. But improperly set valves (way too much clearance) could increase the propensity for jammed lifters. Assuming the radius at the base of the lifter stem is not excessively high, it’s improbable that a jammed lifter is the root of the problem for a broken rocker arm. Having only used the undercut lifters in recent times though, I haven't had an opportunity to examine the radius on the other lifters that are available. On the flip side of all this, I have checked blocks where core shift did have lifters on one side of the block having less clearance in regards to jamming than what the clearance was on the other side of the block. I’ve ended up having to check some of these oddball clearances only because of using camshafts in the Y engines with a 1.150” base circle which has the lifter coming out of the bottom of the bore just enough that if core shift is evident, one lifter bank can be a problem in that the lifters are coming too far out at the bottom of the lifter bore. But back to the undercut. Undercutting is another way to allow for an increase of pressure at a joint before experiencing a failure just as including a generous amount of radius at the same joint does the same. The undercut simply has the advantage of allowing the lifter to go all the way up without allowing the lifter to stick in the lifter bore whereas a radius at the lower end of the lifter stem will allow the lifter to wedge itself at the bottom of the lifter bore if pushed up too high.
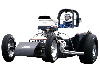 Lorena, Texas (South of Waco)
|
|
|
PF Arcand
|
|
Group: Forum Members
Last Active: Last Year
Posts: 3.3K,
Visits: 238.8K
|
Ted: A thought based on your observation about the undercut on the lifters you use. If a lifter without sufficient undercut jambed in the block, could that also break a rocker arm? Maybe the lifters Schumann sourced, are oversize under the head?...
Paul
|
|
|
PF Arcand
|
|
Group: Forum Members
Last Active: Last Year
Posts: 3.3K,
Visits: 238.8K
|
If I read the article correctly in the latest issue, #101 of YBM, J.C.'s engine also suffered a Rocker Arm failure, at about the same time the lifter failed. However, apparently it was not on the same valve! The article doesn't say if the rockers were stock or aftermarket? Seems like there is something strange going on there...
Paul
|
|
|
speedpro56
|
|
Group: Forum Members
Last Active: Last Year
Posts: 1.3K,
Visits: 9.2K
|
I always bank on the old original USA stuff .My vote is Wohlert, just good insurence.
-Gary Burnette-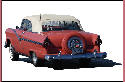
|
|
|
aussiebill
|
|
Group: Forum Members
Last Active: 5 Years Ago
Posts: 1.8K,
Visits: 11.4K
|
Oldmics (1/4/2011)
Has anybody spoken to Vern about the failure. I gotta admit that I"m a little concerned. Got a fresh engine here waiting for Mummerts heads that have Vern"s "white box" lifters inside. Now I am considering changing those out for some old N.I.B. Wohlert Johnson tappets that I was saving. Wadduya think folks.Safe with Verns products?Or change them out to be safe? Oldmics Mike, saving the good lifters for what? use the good ones while you pursue the others, thats my thoughts. regards bill.
AussieBill YYYY Forever Y Block YYYY Down Under, Australia
|
|
|
Oldmics
|
|
Group: Forum Members
Last Active: 5 Years Ago
Posts: 710,
Visits: 78.1K
|
Has anybody spoken to Vern about the failure. I gotta admit that I"m a little concerned. Got a fresh engine here waiting for Mummerts heads that have Vern"s "white box" lifters inside. Now I am considering changing those out for some old N.I.B. Wohlert Johnson tappets that I was saving. Wadduya think folks.Safe with Verns products?Or change them out to be safe? Oldmics
|
|
|