Group: Forum Members
Last Active: 2 Years Ago
Posts: 476,
Visits: 22.0K
|
They likely will stop making them,. I can't see them making new shafts where they were reusing the original shafts before. It probably wouldn't be cost effective. I think we Y-blockers may sowed the seeds of this situation by sending in Loadamatic units as cores when we bought the rebuilt '57+ units. Sooner or later they were going to run out of the later cores to rebuild. I don't know if the Loadamatic units use the same shaft as the later ones but maybe they could use those.
|
Group: Forum Members
Last Active: Last Year
Posts: 729,
Visits: 112.0K
|
I hope it is a sign of them taking responsibility, it would help their credibility as a supplier. If they just stop making due to a lack of proper shafts it could hurt people in the future needing them
|
Group: Moderators
Last Active: 3 hours ago
Posts: 6.1K,
Visits: 442.4K
|
That could be a good sign.
Lawrenceville, GA
|
Group: Forum Members
Last Active: 2 hours ago
Posts: 3.7K,
Visits: 32.6K
|
I thought I was done adding my 2 Cents worth to this Topic but I just did a search for the Cardone 30-2808 which was the original cause for this Topic. They don't appear to be available from anyone who usually sells them. Is it possible that Cardone is now admitting there is a Problem with the Frankenstein Distributors they tried to produce using the wrong Shafts? Everywhere I checked online they are "not available". About Time they stopped selling them if that is the Reason they are not available.
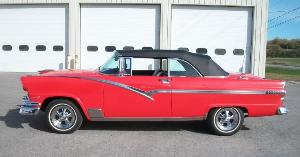
|
Group: Forum Members
Last Active: Last Year
Posts: 729,
Visits: 112.0K
|
Tedster (8/22/2018)
57RancheroJim (8/22/2018)
...if I add the machined surface then it comes into spec. and that was with the shaft pushed up with the collar against the body. Huh. Well there you have it. Thanks Jim! I owe ya beer. Ted, forget what I said, I confused myself again. The measurement from flange to gear was 4.965 + .030 to the machined surface on the bottom of the gear = 4.995 with the shaft PULLED DOWN.. Sorry
|
Group: Forum Members
Last Active: 3 Years Ago
Posts: 513,
Visits: 153.3K
|
57RancheroJim (8/22/2018)
...if I add the machined surface then it comes into spec. and that was with the shaft pushed up with the collar against the body. Huh. Well there you have it. Thanks Jim! I owe ya beer.
|
Group: Forum Members
Last Active: Last Year
Posts: 729,
Visits: 112.0K
|
OK, I was only able to measure the gear surface, if I add the machined surface then it comes into spec. and that was with the shaft pushed up with the collar against the body. It must be correct as that engine ran for countless miles since 59 and everything is still tight.. I just saved it for a back up or some future use..
|
Group: Forum Members
Last Active: 3 Years Ago
Posts: 513,
Visits: 153.3K
|
The bushing doesn't look NOS or supplied in a FoMoCo box or anything like that. It's just like the pic, bronze/copper color. With an oil hole, so I doubt it's oilite.
It did fit fine on an old shaft. After installation into the housing though, no way. I thought maybe if it was just a little on the tight side I could spin the old shaft with some oil and a drill and knock off the high spots, but it's going to take more than that.
The problem is usually the shaft and bushing are best replaced together. The wear is mostly on the bush but if one is trashed the other is getting there.
The measurement should be taken from the flat machined surface at the bottom of the gear is my understanding. If you want to get fancy, from what I'm reading the way to do it is to measure the dimension from the actual thrust surface in the block to the mounting boss on the block. Then, with all that fancy-pants arithmetic and jiggery-pokery that I should have paid more attention to in school instead of Kathy, the proper clearances can be determined so the gear and shaft ends up exactly halfway in the endplay range. The camshaft gear drives the distributor gear down, utilizing the pad in the block as a thrust surface. That's why the measurement should be taken there, or based upon that point anyway. If you can measure the dimension of the individual gear, then subsequent measurements would be easier using the top of the gear. I have three distributor gears on hand and the machined pad dimensions varies quite a bit, and the holes are placed randomly basically. That's at least one reason why they can't be swapped around.
|
Group: Forum Members
Last Active: Last Year
Posts: 729,
Visits: 112.0K
|
Tedster (8/21/2018)
57RancheroJim (8/21/2018)
This just gets more confusing. I pulled out an old one and it's very hard to get a really accurate measurement with the tools I have but the best I could do was 4.940 with the shaft pushed up and 4.965 pulled down. So those numbers aren't even close to what they call for in the manual,???? Don't know what to say at this point.. OK, thanks very much for that info. So it's roughly (at least) 0.026" too high? Same amount roughly as the endplay. Did they install it wrong?? I better go lay down for a while. LOL I have a digital vernier caliper on the way. Highest quality - $6.99 delivered to my door. Maybe a machinist can explain this to me (hafta talk to me like I'm 5) but the plan is on installing the gear within the 4.991" to 4.996" range with the shaft pulled out. What does the gear wear pattern look like on that one? On the cardone it was clearly engaging only about the bottom 1/3! The shaft itself looks to be the right length oddly enough. The rotor end of the shaft is a bit longer though. Makes ya wonder who signed off on that operation. Sorry for the late reply but my mouse went dead and I had to wait until this morning to go get batteries LOL. To add to the confusion is the measurement taken to the bottom of the gear where the teeth are or to the bottom of the stepped area that meets the block surface?? That adds about another .030.. The distributor I'm measuring is a completely original 59 model. The wear pattern is as close to center as I can tell. Is the new bushing steel or bronze? A 57 shaft would have 26 degrees of advance. Are you rebuilding the Cardone or another one?
|
Group: Forum Members
Last Active: 2 days ago
Posts: 774,
Visits: 113.4K
|
Sounds to me like you have it all down very well. Tightening the screw on the "special tool" would push the shaft down against the bushing/bowl. You are also correct in that there is a typo in the '64 book. It should be as you state, .022, not .002. This procedure establishes the correct positioning of the collar only. Then, feeler gauge removed and the shaft pushed against the screw, the shaft now moved upward .022, the collar is to be placed against the bottom of the housing and pined there which will therefore establish the .022 end play. There were different cam slots. The one that was in my '57 tach strib was 14 or 15* and I replaced it with the cam from my stock '64 strib which was something less, like around 12 or 13* I'm not at home and this is from my old memory. With out a distributor machine, a degree wheel placed on the cam would probably be the only way to check movement. As to the shaft and bushing fit, your mention of .0012 - should work. I personally have never had to "burnish" a bushing as I always was able to reuse the old, but good shaft. In your case, some tweaking of the bushing will be necessary. During the course of this thread, I did indeed check the fit of a new shaft and a NOS bushing which fit properly. That is, moved freely with no detectable slop. If I was home, I would measure these parts. Hopes this helps, JEFF............
64F100 57FAIRLANE500
|