Author
|
Message
|
speedpro56
|
|
Group: Forum Members
Last Active: Last Year
Posts: 1.3K,
Visits: 9.2K
|
The Best of Luck Ted!
-Gary Burnette-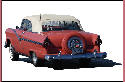
|
|
|
Y block Billy
|
|
Group: Forum Members
Last Active: 7 Years Ago
Posts: 1.6K,
Visits: 5.2K
|
Go Get em Ted!
 55 Vicky & customline 58 Rack Dump, 55 F350 yard truck, 57 F100 59 & 61 P 400's, 58 F100 custom cab, 69 F100, 79 F150, 82 F600 ramp truck, 90 mustang conv 7 up, 94 Mustang, Should I continue?
|
|
|
Ted
|
|
Group: Administrators
Last Active: 2 days ago
Posts: 7.4K,
Visits: 205.3K
|
The Eaton Balancing Y entry fought me most of the week but it’s now turned into a serious performer. Today will be spent taking care of some loose ends such as bracket for the MSD box and coil and some kind of bracket for the throttle utilizing a Morse cable. Once the engine is fired one last time to insure that the changes are as needed, it comes off the dyno, oil drained, and put on an engine cradle for transportation. The team heads out for Lima, Ohio early Monday morning. The engine will be teched in on Wednesday and ran on Thursday. My engine is number 4 on the run order list while Jon Kaase’s entry is #5 and Royce’s is #6. Details on my engine particulars will not be available until after the competition for the obvious reasons.
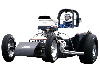 Lorena, Texas (South of Waco)
|
|
|
RB
|
|
Group: Forum Members
Last Active: Yesterday
Posts: 654,
Visits: 16.7K
|
It was very very sad that Danny Miller passed suddenly and too soon.. He had a very quick and inventive mind and boundless enthusiasm.. That Hemi project was quite an effort
|
|
|
Kahuna
|
|
Group: Forum Members
Last Active: 6 Years Ago
Posts: 471,
Visits: 2.4K
|
As I recall, that early Hemi placed 3rd in the competition several years ago. I was very fortunate to be able to watch and assist during the Local Dyno pulls in Chico, CA. I have no idea what HP it made during the EMC, but did get to see it make more than 645 HP on John Beck's dyno. A very impressive engine. Unfortunately, one of the co-builders (Danny Miller) passed away some time later.
|
|
|
Small block
|
|
Group: Forum Members
Last Active: 4 Years Ago
Posts: 90,
Visits: 2.5K
|
The poly engine was the engine that showed the way for the Big block scruby and 351 Cleveland, The poly had some short comings but the canted valve idea was good enough that both Ford and scruby followed with there own design! If you don't have it you will never win a NASCAR race! This class should be interesting Kaase has a way of making power no matter what he builds!
|
|
|
Ted
|
|
Group: Administrators
Last Active: 2 days ago
Posts: 7.4K,
Visits: 205.3K
|
PF Arcand (7/17/2015) That may be true in some cases, however the University of Ohio's dynos ( I don't recall the make or models, but I believe they used three) were starting at 2500 rpm in Engine Masters tests on engines much bigger than a usual Y-block. UNOH uses the DTS dynameters. DTS has sold out to Superflow so the UNOH dynos are now supported by Superflow. It was one of Kaase’s engines that actually ‘smoked’ the water brake on one of the UNOH dyno’s. I’m more in favor of the 3000 rpm start rather than 2500 rpms simply due to some dyno operators not having a soft touch on the controls and operating the dyno controls like a car leaving a dragstrip starting line. If the engine is not tuned for this kind of start, it will cough and spit and in some instances simply die. Assuming the engine gets past that kind of rambunctious start, running the throttle up too fast will make the rpms fall quite a bit below the dyno start rpm and in turn loads both the engine and the dyno extremely hard at that point. If that dyno start rpm is set at 2500, then the potential is there for a high torque engine to drop all the way down to 1800-1900 rpms while the computer is trying to compensate for the sudden load on the water brake. I use the soft touch method at the dyno controls and rarely see more than a 200 rpm drop below the selected start rpm. I rarely make pulls starting at less than 2500 rpms simply due to main bearing and crankshaft loading being severe at low rpms and at full throttle.
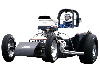 Lorena, Texas (South of Waco)
|
|
|
PF Arcand
|
|
Group: Forum Members
Last Active: Last Year
Posts: 3.3K,
Visits: 238.8K
|
That may be true in some cases, however the University of Ohio's dynos ( I don't recall the make or models, but I believe they used three) were starting at 2500 rpm in Engine Masters tests on engines much bigger than a usual Y-block.
Paul
|
|
|
RB
|
|
Group: Forum Members
Last Active: Yesterday
Posts: 654,
Visits: 16.7K
|
Dyno operators do not like to start dyno pulls at a lower rpm.. The water brake often times can not hold an engine that makes a lot of torque at that low of RPM
|
|
|
PF Arcand
|
|
Group: Forum Members
Last Active: Last Year
Posts: 3.3K,
Visits: 238.8K
|
Interesting point Ted.. It also strikes me as odd that a vintage class would have a somewhat narrow RPM range starting at 3000 RPM. But, then again it's Hot Rod running the show now, not Popular Hot Rodding, who would have undoubtedly started it at 2500 RPM.
Paul
|
|
|