Author
|
Message
|
DANIEL TINDER
|
|
Group: Forum Members
Last Active: 3 hours ago
Posts: 1.7K,
Visits: 150.5K
|
I'm curious what the current general consensus is re: pressurizing the rocker shafts, and drilling/grooving the block valley. I've heard a lot of pros & cons over the years, and wonder what the pro builders do for a street motor? (Verne Schumann is a fanatic about both). Worth the trouble?
6 VOLTS/POS. GRD. NW INDIANA
|
|
|
Ted
|
|
Group: Administrators
Last Active: Last Week
Posts: 7.4K,
Visits: 205.4K
|
Here's my two cents worth. I have drilled the additional oiling holes in the valley only to be surprised how much oil is actually thrown up out of those holes under full throttle. I had a clear cover over the valley while dyno testing which permitted me to observe what was happening in this area under throttle. There’s obviously enough oil to the camshaft without the additional oil holes in the valley but there is some crankcase pressure relief taking place which would allow oil to flow to the back of the block easier and drain to the crankcase via that route. Without the additional holes, the only pressure relief from the crankcase is happening from the two small holes at the front of the block and the distributor hole cavity. Although I haven’t seen it happen, the potential for cracking a block down its middle is intensified in a high horsepower application when drilling the valley with a multitude of small holes. I’m also in favor of grooving the block in the center cam journal so that the three oil holes are interconnected. The cam bearing then just presses in place over this modification. At this point, it’s just a simple matter of putting a restrictor in the rocker arm pedestal to control the amount of oil going to the rockers. On the race engines, I’ve experimented with as small as 0.062” while on street drivers I’ve had this restrictor as large as 0.110”. I still use the oil drain back tubes on the shafts to allow the oil to free flow through the system rather than pinch off or block the tubes and pressurize the shafts.
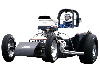 Lorena, Texas (South of Waco)
|
|
|
Unibodyguy
|
|
Group: Forum Members
Last Active: 13 Years Ago
Posts: 240,
Visits: 848
|
This is what I did on one of my motors. When doing a valve adjustment and valve cover replacement. A friend of mine that has/builds all kinds of motors suggested that I take the rocker shaft return line and pinch it down to pressurize the rocker arms. Well what I ended up doing was accually reducing down the return line with a much smaller one so it somewhat pressurized the rocker arms. I had very good oil pressure before, like 30-32 lbs at idle. After that it went up to like 40-42 lbs. I was really surprised what a differencce it made and how much quieter the motor was, but I suppose the adjustment helped a heck of a lot too. Michael
MichaelSandy Valley, NV
|
|
|
DANIEL TINDER
|
|
Group: Forum Members
Last Active: 3 hours ago
Posts: 1.7K,
Visits: 150.5K
|
Ted,
Could you elaborate re: your reasoning for NOT pressurizing the shafts? (In my case, I was always afraid that oil would flood the valves if not directed straight down the pushrod/drain holes).
Michael,
Do you know the ID of the smaller drain tubes you installed?
6 VOLTS/POS. GRD. NW INDIANA
|
|
|
davis
|
|
Group: Forum Members
Last Active: 10 Years Ago
Posts: 188,
Visits: 687
|
i'm new here, are the drain tubes the U tubes that go from the top of the shaft and point down at the ends of the rocker shafts? I know the FE guys would insert holley jets to resttrict oil flow in the heads to prevent oil flooding the valves.
but then FE's do have oil baffles under the shafts.
thanks for the input, i'm trying to figure this out as the thread moves on.
This ain't no L-Kamino!
|
|
|
Hoosier Hurricane
|
|
Group: Moderators
Last Active: 2 hours ago
Posts: 3.7K,
Visits: 322.7K
|
Opinions are wanted here, so here's mine. I feel the overflow tubes are there to make sure the rocker shafts are always full of oil, but not under pressure. This supplies drip oiling to the rockers. It seems to be adequate on all my Ys, even my Crane cammed 6500 rpm supercharged engine with stock 1.54 rockers. I feel that if the tubes are blocked, then all the oil to the rocker area would have to try to drain away via the two small drain holes in the ends of the heads. They don't have enough capacity, therefore the oil level can rise in the rocker cover area until it can drain through the pushrod holes. At that point, the oil level is above the tops of the valve guides. I also use the grooved block plus the restrictors as Ted explained above. Without the restrictors I flooded the rocker area even with the overflow tubes in place. John in Selma, IN
John - "The Hoosier Hurricane"
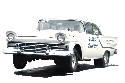
|
|
|
John F
|
|
Group: Forum Members
Last Active: 7 Years Ago
Posts: 128,
Visits: 2.6K
|
This may be a dumb question but, what are you using to restrict the oil flow into the rocker shafts?
John F  Ballwin, MO 
|
|
|
Unibodyguy
|
|
Group: Forum Members
Last Active: 13 Years Ago
Posts: 240,
Visits: 848
|
Daniel, what I basically did was join two brake lines togther with one being smaller. I did this by taking the tube down to a Car Quest store and matching things up. Pretty straight forward. Michael
MichaelSandy Valley, NV
|
|
|
Ted
|
|
Group: Administrators
Last Active: Last Week
Posts: 7.4K,
Visits: 205.4K
|
DANIEL TINDER (2/28/2008) Ted, Could you elaborate re: your reasoning for NOT pressurizing the shafts? (In my case, I was always afraid that oil would flood the valves if not directed straight down the pushrod/drain holes).By not blocking the oil outlet tubes, air is purged from the shafts thereby insuring that the shaft stays full of oil. If these tubes are blocked, then the potential is there for air to be trapped within the shafts. A constant flow of oil through the shafts by the use of the overflow tubes will purge the air and help to carry off some of the heat rather than the oil potentially stagnating and then sludging up. On a solid lifter engine such as the Y, the rockers get to relax between valve actions which promotes additional leakage at the bottom of the rocker but on a hydraulic cammed engine such as the FE, that period of relaxation doesn’t occur and this is where pressure oiling would have some additional benefit. But as John also brought up, allowing the excess oil to bleed off at the overflow tubes also insures that the oil level in the heads does not exceed the ability of the drain holes to carry it away.John F (2/28/2008) This may be a dumb question but, what are you using to restrict the oil flow into the rocker shafts? To restrict the oil to the rockers themselves, I thread the ‘second from the right’ pedestal at its bottom with a 5/16 X 18 tap and install a set screw that is drilled with the appropriately sized hole. This could be done in the head as an alternate choice. An Fe is already sized at 0.125” in the head gasket but the Y is pretty liberal in its oiling up to the rockers if the restriction at the camshaft is freed up. Not counting the restriction in the oiling at the camshaft, the Y has a 5/16” hole in the block with a corresponding 5/16” hole in the head gasket. The oil passageway in the cylinder head downsizes to a ¼”and this size is maintained up to the rocker arm shaft. If the oil is freed up at the camshaft, then that’s a lot of oil flow to contend with.Another rocker shaft modification would be to grind some angled slots across the lower oiling holes to promote more oil across the inside wear area of the rocker arm. There’s a picture of this modification elsewhere in the forums. Davis (2/28/2008) but then FE's do have oil baffles under the shafts.. The oil shields or baffles under the rockers are another story. This would appear to be another item on the Y that was dropped as a cost cutting measure early on but I do prefer to run them when given the option. If running a positive seal on the valve guide, then the baffles are likely not worth much but if running the stock unbrella type of seal, then these shields do reduce the amount of oil getting to the guide.
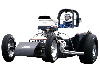 Lorena, Texas (South of Waco)
|
|
|
Ted
|
|
Group: Administrators
Last Active: Last Week
Posts: 7.4K,
Visits: 205.4K
|
Here’s the picture of the rocker shaft oiling modification posted elsewhere on the site. And the link to the original thread. http://forums.y-blocksforever.com/Topic6985.aspx
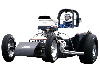 Lorena, Texas (South of Waco)
|
|
|