Author
|
Message
|
Ted
|
|
Group: Administrators
Last Active: Yesterday
Posts: 7.4K,
Visits: 205.6K
|
pegleg (11/15/2010) Ted,........I don't understand the 45 degree thing unless it spreads the torque curve out. Frank. The beveled cut on the end of the collector makes for a larger exit area for the exhaust without actually enlarging the diameter size of the collector. This allows for an easier transition in the differential pressure between what’s in the collector and what’s outside the collector. Reduced back pressure within the collector is the net result of the angled cut on the end of the collector. This also has an effect on the db or noise level at the collector outlet. The analogy to this is a water pipe that stands vertical with its exit or drain at the bottom. With a straight cut, the reduced (and constant) surface area at the exit permits the water to actually stand within the pipe without draining. This is atmospheric pressure actually holding the liquid in place. With an angled cut, the difference in pressure is varied at the pipes exit from one end of the cut to the other allowing the water to freely drain without atmospheric pressure being able to hold it in place. I trust that makes sense.
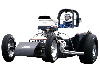 Lorena, Texas (South of Waco)
|
|
|
Ted
|
|
Group: Administrators
Last Active: Yesterday
Posts: 7.4K,
Visits: 205.6K
|
charliemccraney (12/1/2010) Ted, can you test a truck exhaust system which is set up for duals, you know where the crossover pipe is removed and blocked off on the passenger side, and the pipe bends down and under on the driver side?Charlie. There are plans to run the single exhaust system with the overhead pipe but no plans to take that particular system and test as a dual exhaust conversion. There’s just not enough material here to fab up an extra pipe to test that particular scenario. The ’57 car manifolds are laid out for a dual exhaust test which should be sufficient in quantifying the basic differences between a single and dual exhaust sytem. The Rams Horns and Fenton manifolds will also be tested in a dual exhaust configuration. After that, it will be a myriad of headers with various exhaust combinations being tested. At this point, I’m waiting on header flanges that can be welded to the various pipe extensions before proceeding any further.
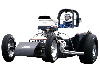 Lorena, Texas (South of Waco)
|
|
|
charliemccraney
|
|
Group: Moderators
Last Active: Yesterday
Posts: 6.1K,
Visits: 442.5K
|
Ted, can you test a truck exhaust system which is set up for duals, you know where the crossover pipe is removed and blocked off on the passenger side, and the pipe bends down and under on the driver side?
Lawrenceville, GA
|
|
|
PF Arcand
|
|
Group: Forum Members
Last Active: Last Year
Posts: 3.3K,
Visits: 238.8K
|
Just a side note, re copper & aluminum. In some environments, such as in a salt air environment, copper & aluminum can react with each other. So best to keep an eye out as to what might happen with copper gaskets against aluminum heads...
Paul
|
|
|
PF Arcand
|
|
Group: Forum Members
Last Active: Last Year
Posts: 3.3K,
Visits: 238.8K
|
Yes, copper can be annealed by heating it to a good cherry red & letting it cool slowly. I've worked with plumbers that did this successfully to 2" or bigger pipe that had to be bent.
Paul
|
|
|
marvh
|
|
Group: Forum Members
Last Active: Last Year
Posts: 513,
Visits: 16.7K
|
Hoosier Hurricane (11/16/2010) In aircraft school, I was taught to anneal copper by taking an acetylene torch with pure acetylene, play it over the surface until it is black with carbon, turn on the oxygen and heat the copper until the carbon burns off.That is exactly the way I was taught to weld aluminum with an oxy-acetylene torch before we had tigs. Blacken the metal then heat and start welding just as the carbon clears off. Go to far and it becomes a glob on the floor. marv
|
|
|
Hoosier Hurricane
|
|
Group: Moderators
Last Active: 5 hours ago
Posts: 3.7K,
Visits: 322.8K
|
In aircraft school, I was taught to anneal copper by taking an acetylene torch with pure acetylene, play it over the surface until it is black with carbon, turn on the oxygen and heat the copper until the carbon burns off.
John - "The Hoosier Hurricane"
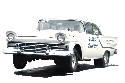
|
|
|
marvh
|
|
Group: Forum Members
Last Active: Last Year
Posts: 513,
Visits: 16.7K
|
Ted (11/16/2010)
marvh (11/15/2010) .....copper yblock exhaust manifold gaskets .......I have not decided if they should be annealed or not. My experiences working on diesel engines using copper gaskets say to anneal. Opinions?Copper exhaust gaskets definitely need to be soft to help them seal. The copper header gaskets I use for the Y’s on the dyno are not annealed and do leak as a result of being essentially too hard. They are not deforming as needed to match the header flange. As a general rule, I have problems with copper header gaskets sealing on all engines when being used dry or without additional sealer (hi temp RTV) on them. On the dyno, I can live with some minor header leaks but on a driver, these would be unacceptable. Thanks Ted: That is what I will do... anneal them before installation. That way they will be soft and fit any imperfection on the mating surfaces. If I remember correctly it takes 700-900 deg F to get copper cherry red to anneal. Installing then driving would probably get the metals this hot just may take several re-tightenings. Annealing would do the job in one pass. marv
|
|
|
Ted
|
|
Group: Administrators
Last Active: Yesterday
Posts: 7.4K,
Visits: 205.6K
|
marvh (11/15/2010) .....copper yblock exhaust manifold gaskets .......I have not decided if they should be annealed or not. My experiences working on diesel engines using copper gaskets say to anneal. Opinions?Copper exhaust gaskets definitely need to be soft to help them seal. The copper header gaskets I use for the Y’s on the dyno are not annealed and do leak as a result of being essentially too hard. They are not deforming as needed to match the header flange. As a general rule, I have problems with copper header gaskets sealing on all engines when being used dry or without additional sealer (hi temp RTV) on them. On the dyno, I can live with some minor header leaks but on a driver, these would be unacceptable.
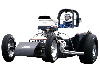 Lorena, Texas (South of Waco)
|
|
|
pegleg
|
|
Group: Forum Members
Last Active: 3 Years Ago
Posts: 3.0K,
Visits: 8.7K
|
Ted, I have seen formulae for the primary lengths, but never the "Collecter" lengths. We used hear that you cut the collecters at the "Blue" lines on the pipes, I always used ET's to determine where to stop. In many cases the added low or mid range torque got the car through quicker than just top end HP. I spent about three months getting a 67 Pontiac Sprint (OHC-6) right. Car would go 12's with 230 ci and break store windows two miles off. The big deal then was the square Box collecter, never could make that work. John's tubing diameters are too small for the HP he makes, BUT, it's an automatic and fairly heavy. So maybe the mid range torque actually helps out of the hole. He's TWO SECONDS quicker than my car, with a 6-8 mph advantage. Something works! I don't understand the 45 degree thing unless it spreads the torque curve out. Marv: I'd think the copper would be annealed by one or two passes. Exhaust gas Temps will exceed the melting point of aluminum, or 1100 degrees. More than enough to anneal copper.
Frank/Rebop Bristol, In ( by Elkhart)  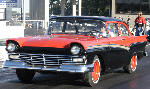
|
|
|