Author
|
Message
|
Grizzly
|
|
Group: Forum Members
Last Active: 10 Years Ago
Posts: 281,
Visits: 1.9K
|
I'm a newcomer to the forum but have been watching the progress with the alloy heads for a while. My two cents worth on the Rocker hold down bolts is that if you went to a larger diameter hole, the hole could incorporate a thread insert and still use 5/16 bolts. This would allow the use of standard covers and bolts and increase the strenght of the assebly. I don't do enough engineering work to be able to quote hole and tap sizes or inserts. Nor do I know what John has in his machine for tools and bits. Warren Adams
Grizzly (Aussie Mainline)
|
|
|
charliemccraney
|
|
Group: Moderators
Last Active: 7 hours ago
Posts: 6.1K,
Visits: 442.4K
|
Are FE or Chrysler rocker arms close enough to work with the revised shaft position?
Lawrenceville, GA
|
|
|
John Mummert
|
|
Group: Forum Members
Last Active: Last Year
Posts: 912,
Visits: 7.4K
|
Bill, by spreading the rocker bolts from 1.200" apart to 1.450" apart it opens up a lot of options for future ideas. For now, I just want to make the heads available for use with stock shafts and existing rocker arms. There will have to be a number of sets of heads in use before it is worth while for one of the rocker manufacturers to make something special for them. With the OE design you can only increase rocker ratio by moving the pushrod ball closer to the shaft. With the bolts 1.45" apart you can move the shaft up to .100" farther from the valve and make that side of rocker longer, increasing the ratio. By moving the pushrod ball .040" closer to the rocker and making the valve side .100" longer the ratio becomes 1.73:1
http://ford-y-block.com 20 miles east of San Diego, 20 miles north of Mexico 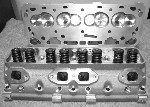
|
|
|
yehaabill
|
|
Group: Forum Members
Last Active: 10 Years Ago
Posts: 426,
Visits: 1.4K
|
Y-guys While ya'll are thinking about the "rocker" area what about making an optional "stand" to use a larger(dia) shaft so that a roller rocker from a different engine family might work. With the problems, with other rockers, this could remedy both problems. I'm far from an engineer, and I realize the geometry etc. would have to be worked out......... Bill
Bill Pelham,Al
|
|
|
bird55
|
|
Group: Forum Members
Last Active: 2 Years Ago
Posts: 1.1K,
Visits: 58.8K
|
wow, I remember when the discussion used to be someone should make aluminum heads for the y…yea right, like THAT was ever gonna happen. NOW listen to you guys!
A L A N F R A K E S ~ Tulsa, OK
|
|
|
Ted
|
|
Group: Administrators
Last Active: Last Week
Posts: 7.4K,
Visits: 205.4K
|
The way John explained it to me was the stock rocker shafts and rocker arms would still work with the aluminum heads but must be used with the rocker arm pedestal supports that are furnished with the heads. The valve cover studs themselves would still be in the original locations.
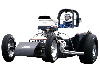 Lorena, Texas (South of Waco)
|
|
|
speedpro56
|
|
Group: Forum Members
Last Active: Last Year
Posts: 1.3K,
Visits: 9.2K
|
John, I believe the outside studs will stay in the same position as the originals but the inside ones may have to be repositioned a small amount, hopefully not enough that only slight modifications to our original rockers can be worked out and still be used.
-Gary Burnette-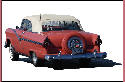
|
|
|
Hoosier Hurricane
|
|
Group: Moderators
Last Active: 3 hours ago
Posts: 3.7K,
Visits: 322.7K
|
Ooops! John just mentioned relocating the rocker shafts. That causes a problem with the mounting studs, may require slotted holes in the rocker covers, OR special cast aluminum, pretty finned covers to fit the new heads. John????
John - "The Hoosier Hurricane"
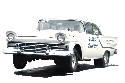
|
|
|
aussiebill
|
|
Group: Forum Members
Last Active: 5 Years Ago
Posts: 1.8K,
Visits: 11.4K
|
Hoosier Hurricane (3/21/2010)
John: Are the 5/16 rocker stand bolts getting close to failure with the spring pressures and inertia loads, prompting the possible need for 3/8 bolts? The rocker cover attachments should be no problem, just run a 3/8 drill through the grommet and use 3/8 nuts. John, that seems simple remedy to proposed problem, i think we are all trying to help as heads get closer to completion, i was thinking of stepped 3/8 down to 5/16 rod but its more machining etc, i like your idea. I,ll bet johns thinking its close but yet so far! regards bill.
AussieBill YYYY Forever Y Block YYYY Down Under, Australia
|
|
|
John Mummert
|
|
Group: Forum Members
Last Active: Last Year
Posts: 912,
Visits: 7.4K
|
John, since we need to make new rocker stands and we're drilling/tapping the holes in the head we can make this change easily, more or less. I don't think that the 5/16" bolts are stressed at current levels but with higher lifts, more RPM ect it could become an issue. I found that some rocker grommets have a 3/8" hole already, some don't. Either way it is the simplest fix for the problem. The bolt change is not written in stone at this point. Part of the reason for considering the change is that our machine only holds 16 tools. Now that sounds like enough until you actually start machining a head. Since the rocker bolts are the only 5/16" tapped hole it would save a tool position and increase the strength. The drill also makes the oil passage to the rockers so it has to be there.
http://ford-y-block.com 20 miles east of San Diego, 20 miles north of Mexico 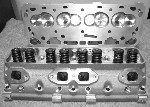
|
|
|