the combustion chambers will be progressively larger in cc’s from one end towards the other. In these cases the calculations are performed so that the heads are angle milled end to end so that one end is milled heavier than the other which in turn allows the combustion chamber cc’s to be more equalized over the length of the head.
And, many times, but not always, the problem is in the factory machining. If the casting is not in the fixture correctly. One end, or one side, can be sitting on chips, and will be too high in the fixture. The mold assembly can be wrong, etc. When you make and cast several thousand per shift, you'll find all kinds of variables.
Daniel, remember the casting is made in sand. Normal tolerances for that process are +/- .030". Which actually means one casting can be .060" different from the next one, and still within tolerance. Aftermarket production rates are usually much lower, more costly and the inspection processes are much more closely watched.
Many of the engines produced by the factory run for one or two hundred thousand miles with those errors, and are scrapped without anyone ever checking or knowing how far from optimal they are. If you attempt to control tolerances in a process more closely than the process is actually capable of producing, often all you do is scrap parts that are useable. All this adds considerably to the cost of production, without gaining much. Y-Blocks were not concieved as race car motors, most were 2 bbl truck engines, or taxi cab motors, where cheap was very important. The difference between a 7 1/2 to one or a 7 3/4 to one compression ratio wasn't noticeable.
Frank/Rebop
Bristol, In ( by Elkhart) 
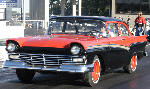