Author
|
Message
|
B-rad
|
|
Group: Forum Members
Last Active: 2 Weeks Ago
Posts: 333,
Visits: 1.5K
|
Getting opinions on whether it's better to attach the hydramatic tranny to the 317 y block while they're both out of the car, or after engine is in? They're both freshly rebuilt and back home. My engine hoist is a 2 ton so the weight is no problem. But it has 4 holes in the arm that adjusts from 1/2 ton up to 2 tons. A problem I'll have is that the reach of the arm is too short to go far enough into the engine bay. And 1/2 ton setting will probably bend the arm with the full engine and tranny together. I just remember what a pain it was to take all the bolts off of the flywheel, even when it was out of the car. Yes, I took them out together but I had disassembled a lot of the engine before removing it from the car. It is now totally together and weighs a lot more. I don't remember if I had taken the front bumper off before or after removing the engine, so this may be a moot question. There may be adequate room to get the engine in with that removed. I do like the idea of putting them in together, especially being able to put all those bolts in without squirming around under the car. I'm sure many of you have had experience with this problem and I will be very appreciative of any advice, as usual. And like many, if not all of you, my body just doesn't work as well as it used to.
Brad Sierra Vista Arizona 1954 Lincoln Capri
|
|
|
Joe-JDC
|
|
Group: Forum Members
Last Active: 4 hours ago
Posts: 768,
Visits: 22.2K
|
Whenever I need to install both the engine and transmission together, I block the front wheels, raise the rear of the vehicle as far as possible and put jack stands under the rear axles lowering the weight onto the jack stands, and leaving the floor jack under the differential. That allows me access under the middle of the vehicle to have a helper guide the transmission tailhousing into the proper place while I lower/position the engine properly. I have done it alone many times, but a helper makes it much easier. You can use the floor jack to raise the tailhousing up in place before lowering the rear of the vehicle back on the floor. This way, you don't have to raise the engine/transmission quite as high and it is a bit safer IMO. Joe-JDC
JDC
|
|
|
B-rad
|
|
Group: Forum Members
Last Active: 2 Weeks Ago
Posts: 333,
Visits: 1.5K
|
Great advice. Makes sense. I've never put an engine in a car and the tranny attached is just another thing to worry about. Any udea what a complete 317 and hydramatic tranny weigh together?
Brad Sierra Vista Arizona 1954 Lincoln Capri
|
|
|
B-rad
|
|
Group: Forum Members
Last Active: 2 Weeks Ago
Posts: 333,
Visits: 1.5K
|
I got the tranny and engine together with few troubles. But I looked up the torque for the flywheel to tranny and it said 50-55 ft lbs. The bolts aren't too big and I had difficulty torqueing that hi. Can someone please research the torque value for the hydramatic tranny to flywheel? I was really psyched being able to line up and actually install the tranny to engine, having never done that before. It took 3 to 4 hours to do it completely but I had to try and take it apart after finding out that the dowels, or whatever they're called, got lined up in the wrong hole. I had them straight up and down at first but the top one didn't seem to line up right so I turned the torus so the dowel holes were at 3 and 6 o'clock positions, so I could see them line up right. It took a little adjusting of the height of the motor and tranny, but once I got the tranny housing holes and the dowels on the engine housing lined up, and turning the crank bolt in front, lining up the dowel and hole on the flywheel, it slid together nicely. All 30 bolt holes were lined up perfectly. All I need now is the correct torque values for the bolts and I'm golden.
Brad Sierra Vista Arizona 1954 Lincoln Capri
|
|
|
miker
|
|
Group: Forum Members
Last Active: 2 days ago
Posts: 1.8K,
Visits: 194.1K
|
Brad, hard to tell exact weights, but that Hydramatic is at least 435lbs from what I could find. A fully assembled FE (cast iron manifolds) is a little over 700, so your 317 is probably a bit heavier. That’s a lot of weight swinging on the end of a chain, and I have no clue what the safety margin is in your hoist. But I’d be a little leery of putting 1200 lbs on the end of the 1000 lb setting. Especially swinging around in a tight space. And I wouldn’t try it alone.
Anybody down there got a heavy hoist for rent? I know when we had the fleet shop we had a really heavy duty long reach unit for bigger truck engines and vans.
miker 55 bird, 32 cabrio F code Kent, WA Tucson, AZ
|
|
|
Ted
|
|
Group: Administrators
Last Active: Last Week
Posts: 7.4K,
Visits: 205.4K
|
B-rad (6/15/2024) ....But I looked up the torque for the flywheel to tranny and it said 50-55 ft lbs. The bolts aren't too big and I had difficulty torqueing that hi. Can someone please research the torque value for the hydramatic tranny to flywheel? .....What size are the bolts? That will help to determine the amount of torque required to tighten them.
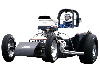 Lorena, Texas (South of Waco)
|
|
|
B-rad
|
|
Group: Forum Members
Last Active: 2 Weeks Ago
Posts: 333,
Visits: 1.5K
|
The bolts are 1/2"
Brad Sierra Vista Arizona 1954 Lincoln Capri
|
|
|
Ted
|
|
Group: Administrators
Last Active: Last Week
Posts: 7.4K,
Visits: 205.4K
|
Is that ½” size that you list for the bolt/shank diameter or the wrench size for the head of the bolt? I’ll take a stab in the dark and guess that you are working with 5/16” diameter bolts in that you have thirty of them. If the bolt diameter is 5/16” and they are 24 tpi, then the standard engineering torque range is 100-140 in/lbs which can vary depending upon the hardness of the bolt. Looking at a 1957 shop manual, the spec is 15-18 ft/lbs for a 5/16-24 bolt.
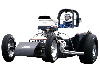 Lorena, Texas (South of Waco)
|
|
|
B-rad
|
|
Group: Forum Members
Last Active: 2 Weeks Ago
Posts: 333,
Visits: 1.5K
|
That's half inch socket.
Brad Sierra Vista Arizona 1954 Lincoln Capri
|
|
|