Author
|
Message
|
DiLL
|
|
Group: Forum Members
Last Active: 3 Years Ago
Posts: 29,
Visits: 17.6K
|
Is there a significance to the castings on the 272 block? I’m currently looking at one coded as “ECG 8” I’ve seen another coded as “ECG 14” what does the number represent?
DiLL
|
|
|
Ted
|
|
Group: Administrators
Last Active: 6 hours ago
Posts: 7.4K,
Visits: 205.5K
|
Without seeing a picture of the placement of the additional letters or numbers, I suspect you may be looking at the mold number for that particular block. When casting those blocks, there were several cast at a time and the mold numbers would help to track back to the mold any casting issues that might show up further down the line.
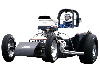 Lorena, Texas (South of Waco)
|
|
|
DiLL
|
|
Group: Forum Members
Last Active: 3 Years Ago
Posts: 29,
Visits: 17.6K
|
Ah gotcha! So, I was reading through an older post that you had commented on (can’t seem to find the post now) about a 272 with a 4” bore. I was just curious as to which casting/mold that may have been and if these blocks are worth attempting to find.
DiLL
|
|
|
Ted
|
|
Group: Administrators
Last Active: 6 hours ago
Posts: 7.4K,
Visits: 205.5K
|
All the thick wall blocks I’ve come across were ECG castings. There have been no external markings on those blocks that differentiate those blocks from standard production blocks. Those thick walled blocks were found by sonic testing the cylinder wall thicknesses but in hind sight, measuring the smaller than normal air gaps between the cylinders at the freeze plugs would have yielded clues towards the blocks being thick walled. The first thick walled block I found did make me question the sonic tester readings but after verifying the tester results by performing an additional calibration check using a piece of cylinder wall material, the readings were reaffirmed when retesting the block after boring. While I do record the block casting numbers and date codes when sonic testing, I do not keep up with the mold numbers as those only represent the outer shell of the castings. To date, I’ve never come across another block with a duplicate date code where both blocks were cast on the same day. There’s also a shift or time code on the blocks so that adds some more complexity to finding blocks within the same date and time frame. It’s the inner cores that would dictate exactly how thick the cylinders are and those are placed within the molds prior to pouring. Gut feel says that all the molds during a given run would be cast the same so it would be easier to track further down the line. If it’s an R&D or special projects run, then doing all the blocks the same during a given run would simplify things. Excess blocks or those not needed, would be simply subjected to regular machining. To date, the 272 thick walled blocks I’ve come across were cast in 1954.
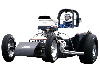 Lorena, Texas (South of Waco)
|
|
|
DiLL
|
|
Group: Forum Members
Last Active: 3 Years Ago
Posts: 29,
Visits: 17.6K
|
Thanks for the info! I plan on tearing it down this weekend. I’ll try and get some pictures and measurements off of it.
DiLL
|
|
|
darrell
|
|
Group: Forum Members
Last Active: Last Month
Posts: 455,
Visits: 22.2K
|
ted what did these blocks measure between cylinders.how thin were they at 4 inches
|
|
|
Ted
|
|
Group: Administrators
Last Active: 6 hours ago
Posts: 7.4K,
Visits: 205.5K
|
darrell (3/26/2019)
ted what did these blocks measure between cylinders.how thin were they at 4 inches If a 1/8” drill bit shank barely fits or doesn’t go in between the cylinders at the core plugs at the outside of the block, then you have the makings for a big bore block. It’s been awhile now but memory wants to say that the cylinder wall thicknesses were in the 0.075”-0.085” range on the thin sections at 4” bore. That's too thin for a performance application but it's still working for the low compression 272 Y that was bored out to 4".
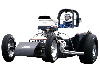 Lorena, Texas (South of Waco)
|
|
|
darrell
|
|
Group: Forum Members
Last Active: Last Month
Posts: 455,
Visits: 22.2K
|
ive never seen anything like that.best i seen was about .230.i checked a couple of 57 blocks and they started out good at one end but opened up at the other.with the 272 blocks i wonder what happened with later blocks.did things become worn.
|
|
|
pegleg
|
|
Group: Forum Members
Last Active: 3 Years Ago
Posts: 3.0K,
Visits: 8.7K
|
The cores have prints where they are located, as the tooling wears out and is corrected the location may change in the mold. Also as the cores are assembled during production the can move slightly. You're dealing with heavy cores made of sand surrounded by 2500 degree liquid iron. Lots of things can and will go wrong. Those cores were set by people who can get sloppy toward the end of the shift. Cores get bumped, dropped, put together wrong, bla, bla. I spent the best part of 40 years doing this, don't thing I ever saw a perfect sand .casting
Frank/RebopBristol, In ( by Elkhart)  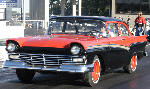
|
|
|