Group: Forum Members
Last Active: Last Month
Posts: 1.2K,
Visits: 137.5K
|
I have a Hobart 110 volt mig that I bought many years back. Never used enough to get good at it. Dug it out and been using it on some sheet metal repair on a '65 Mustang. Still not realy getting the hang of it. In talking to a few friends who have more experience than I do and figured out that mine has a non adjustable gas regulator and theres all have an adjustable regulator. Will and adjustable regulator be worth the cost?
|
Group: Forum Members
Last Active: 2 Years Ago
Posts: 389,
Visits: 31.8K
|
I may be mistaken and I do not know what your welder looks like but most of the time the gauge set is attached to the tank and you set your flow rate into the machine . Are you using gas or are using flux core wire. What is the model number on the machine maybe you should check with Hobart
|
Group: Moderators
Last Active: Yesterday
Posts: 6.1K,
Visits: 442.5K
|
Give more detail on "not getting the hang of it." What's happening?
Lawrenceville, GA
|
Group: Forum Members
Last Active: Last Month
Posts: 1.2K,
Visits: 137.5K
|
Not using flux coated wire. Using gas shield. No gas adjustment on the machine. It would be on the gas valve on the tank. Read the book. Pre set from the factory. No adjustment. Problem with spatter, inconsistant welds. Burns through sometimes. Sometimes insufficient penetration with no change in speed or heat settings. Getting a little better but looking to see if I have an equipment problem. I know I need more parctice.
|
Group: Forum Members
Last Active: Last Year
Posts: 3.3K,
Visits: 238.8K
|
Do you have a book of any kind with the machine? Some things that can be a problem are; Poor fitup, contamination in weld area, heat setting wrong, I've seen a book that indicated that most welds should be pulled, but sometines it's better to push the weld where more heat is needed. Best to try a sample piece sometimes rather than make a mess of the needed weld. Also, 110V machines should be avoided for heavier work that is critical, such as say a heavy truck trailer hitch.. I don't weld any more & a lot of my work was with stick, so others here more into it, may have other suggestions.
Paul
|
Group: Forum Members
Last Active: 2 days ago
Posts: 347,
Visits: 12.2K
|
Is the polarity right?
Vic Correnti
|
Group: Moderators
Last Active: Yesterday
Posts: 6.1K,
Visits: 442.5K
|
I had issues like that when I was learning. I discovered that I didn't have the wire drive wheels tight enough so the wire feed was inconsistent. Made that tighter and I was instantly a better welder.
Lawrenceville, GA
|
Group: Administrators
Last Active: 5 hours ago
Posts: 7.4K,
Visits: 205.6K
|
Rusty wire is at the top of the list for creating problems for MIG welders. This ends up being an issue with welders that are stored in non-heated areas. Never used a ‘fixed regulator’ for the gas and until you mentioned it, didn’t know one was even available. I've also had issues using straight argon as it welds at a cooler temperature. For MIG welding I use a mix of argon and carbon dioxide. I typically have my regulator for wire welding set at about 20 cfm..
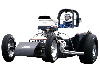 Lorena, Texas (South of Waco)
|
Group: Forum Members
Last Active: Last Year
Posts: 927,
Visits: 190.0K
|
metal being welded must be clean,any rust or paint will cause issues, if welding a repair part be sure the 2nd part is sound. also start with small tacks till you are sure the 2parts are correct. re alignment. I found but welds are for those who are experts.. get a crimper so you are ending to good metal. on a mustang work on arias that are not visible to get practice,they are on the thin side to start. don't do long welds as heat builds burn threw is always there
|
Group: Forum Members
Last Active: Last Month
Posts: 1.2K,
Visits: 137.5K
|
I'm using argon/co2 mix. Got a retulator today and starte at 30cfm and tinkered with it for some time today. Kicked the heat up a noch. Working better. I know to make very short welds on sheet metal. I never thought about the wire having gotten rusty or dirty in storage, It was in an unheated wood storage shed for a lot of years. Will look at that next time I am working on it. I've already had to play with the tension on the drive wheels. I was always prety good with an acdtyliene torch but only fair with a stick welder. As with anything practice makes perfect. I figure by the time I get this Mustang done I should at least be getting decent with it.
|