Author
|
Message
|
Florida_Phil
|
|
Group: Forum Members
Last Active: 2 Years Ago
Posts: 1.2K,
Visits: 285.6K
|
I have a set of NOS TRW Y Block lifters that I had planned to use in my new engine build. Upon further inspection the lifters have some surface rust and pitting. I don't want to chances, so I ordered a new set of Comp Cam lifters. I also have a set of the bigger tubular push rods. They are the same length as the stock push rods I removed. The push rods have slightly bigger ball ends than the old push rods. Are there different lifters for these push rods or will I be OK?
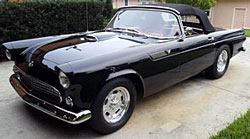
|
|
|
charliemccraney
|
|
Group: Moderators
Last Active: 5 hours ago
Posts: 6.1K,
Visits: 442.5K
|
The older style 1/4" solid pushrods are sort of mushroomed on the lifter end. That makes them look smaller but the rounded end should have the same radius. Check the fit of the new pushrods in the new lifters using grease or a marker or layout dye, something that allows you to observe the contact pattern. Then you know if it is right.
Lawrenceville, GA
|
|
|
PF Arcand
|
|
Group: Forum Members
Last Active: Last Year
Posts: 3.3K,
Visits: 238.8K
|
As Charlie says, check closely the fit of the pushrods. According to an article in Y-block Magazine by John Mummert recently, there are problems with some pushrod to rocker fitup, due to aftermarket parts that are improperly dimensioned for stock part fitup.
Paul
|
|
|
57RancheroJim
|
|
Group: Forum Members
Last Active: Last Year
Posts: 729,
Visits: 112.0K
|
I ran into that issue of the rocker arm end, the cup radius is too small and split instantly. I should have measured first but I didn't.
|
|
|
paul2748
|
|
Group: Forum Members
Last Active: 3 hours ago
Posts: 3.6K,
Visits: 497.6K
|
The rocker arm end is usually the problem end. The cups are too small for the rocker and don't seat on the bottom of the cup. I used the heavier, tubular push rods. I checked the ends of the pushrods to the lifter and found the lifter had plenty of room for the new pushrods.
54 Victoria 312; 48 Ford Conv 302, 56 Bird 312 Forever Ford Midland Park, NJ
|
|
|
Florida_Phil
|
|
Group: Forum Members
Last Active: 2 Years Ago
Posts: 1.2K,
Visits: 285.6K
|
Thanks, I'll check that. I just bought a new Isky cam. When I checked the oil feed grove in the center journal, it was .015" deep. We checked the stock Ford cam we took out of the engine and it's the same depth. We had plenty of oil to the top of this engine before tear down. Mummert says the grove should be .035". We are considering cutting it deeper. Any comments?
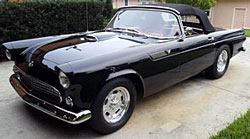
|
|
|
darrell
|
|
Group: Forum Members
Last Active: Last Month
Posts: 455,
Visits: 22.2K
|
the isky cams i seen have a wider groove twice as wide as most other cams.i have been wondering about this myself.
|
|
|
FORD DEARBORN
|
|
Group: Forum Members
Last Active: Last Week
Posts: 775,
Visits: 113.4K
|
I believe Ted adds a grove between the ports on the inside of the cam bearing bore. Not sure if that's where he adds the groove though. When I didn't have a lathe,I enlarged the cam groove myself by laying the cam in a pair of V blocks, cut the head off a partly threaded bolt then screwed it in the cam snout providing a means to rotate the cam with a variable speed drill motor. Enlisting the help from my wife to operate the drill motor, I ground the groove larger with a cutoff wheel in a Dremmel tool. Took a couple minutes for us to get everything coordinated but was able to produced a clean/straight groove. It's been about 5 years ago but the key to this was finding the straightest bolt possible. I know this sounds like a chapter from the Flintstones but it worked good. Hope this may help, JEFF........................
64F100 57FAIRLANE500
|
|
|
Florida_Phil
|
|
Group: Forum Members
Last Active: 2 Years Ago
Posts: 1.2K,
Visits: 285.6K
|
My partner is a retired machinist who has a lathe. The Isky groove is wider than the stock cam. We don't have a problem deepening the grove to .035". I do wonder if we are putting too much oil in the top end?
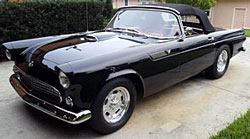
|
|
|
FORD DEARBORN
|
|
Group: Forum Members
Last Active: Last Week
Posts: 775,
Visits: 113.4K
|
I believe if the oil draining into the valley is more than sufficient, then you can't put too much oil through the rocker assembly. Assuming the valve seals, guides and lube system are all functioning as advertised. Tim has an excellent video on his web site showing 100% drain back at high rpm with a cut-away valve cover in place and fully pressurized rocker assemblies. In my case, I have semi pressurized rockers by pinching off about 80% ? of the rocker overflow tubes. I feel I am getting the best of both worlds this way. Just my $.02 JEFF..........................................
64F100 57FAIRLANE500
|
|
|