john2747 (6/26/2018)
Charlie: I doubt very much if you have ever checked a rocker arm for ratio,but yet you chose to criticize people who have made the effort to do that.I have been to Ted Eaton's web site many times,and it is very apparent that you are using his effort's to criticize other peoples effort's,very handy.I totally respect Ted's work to give us information about y-blocks when I get a y-block mag in the mail Ted's article is usually the first one I read.Any engine builder that can put John Kasse in 2'nd place has to be very knowledgeable.But no one gets it right100% of the time.Ted's rig for checking rocker arm ratio does not maintain the angles and pivot points of an assembled y-block engine.The jig I use maintains all the angles and pivot points of a fully assembled y-block engine About 10 years ago I was going to send an article to Bruce for his mag.I didn't do that,now I will send the info to Ted and hope to hear his thoughts about checking rocker ratio's.
This discussion has prompted me to clean the dust off my jig and put it to work again.For this ratio test I will use a ECG 6564-A2 1956 rocker arm and a long EAN adj.screw.This time using.300" push rod travel and the adj. high enough so that no threads are visible under the body of the rocker arm, the valve moves .476" divided by .300"= 1.586 to 1 ratio.The rocker screw is then turned down 10 full turns.Moving the push rod .300" the valve moves .485" -- .009" more than the first test .485" divided by .300" = 1.616 to 1 ratio.Charlie your theory about rocker arm ratio is useless if it can't be proven with legitimate tests
john2747charliemccraney (6/26/2018)
There was no criticism and it's not my theory. If you just google rocker ratio and look at the explanations and pictures, you will see that the ratio is the distance from valve tip to pivot center divided by the distance from pivot center to pushrod contact point. The ratio does in fact decrease as the adjuster screw is turned in..
Your setup performs the check with valve and rocker dimensions setup as they would be on an actual engine which does give a better picture of how it all interacts. I bet when it is actually on an engine, it changes yet again because of the pushrod and lifter angles. What your test does not take into account is rocker geometry. Simply adjusting the screw may not be an accurate way to perform this check since geometry will not be correct for both and that is going to affect the lift result. It would be interesting to know how the effective ratio works out with actual Y block dimensions and when geometry is correct. That would make for a good article.My name is being brought up so I'm going to be a part of this conversation. Rather than keep this in Cliff’s thread, I’ll start a new thread for this. John. I look forward to what your information provides. Always interested in a different approach. What initially brought about the rocker arm ratio test device or apparatus was actually checking rocker ratios and net lifts on finished engines. I was using net lifts at the valves to adjust the rocker arm geometry and found that pushrod lengths were also a player. While that methodology proved to be accurate, it proved to be time consuming and cumbersome when checking the actual rocker arm ratio. That’s where the idea of making a fixture that would actually check the rocker ratio by itself without having to deal with all the articulation points involved originally came from. All those various articulation points actually added noise to the data as there is only one spot on each side of the rocker movement where the pushrod and valve stems are actually perpendicular to the rocker arms’ axis plane. And too many times, those two perpendicular points did not happen at the same time adding more noise to the data. Hope that made sense. The test apparatus using two dial indicators did indeed validate the same results as was being found when doing the same tests on an engine but removed a bunch of extraneous noise that was confusing the results.
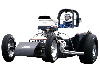
Lorena, Texas (South of Waco)