Author
|
Message
|
2721955meteor
|
|
Group: Forum Members
Last Active: Last Year
Posts: 927,
Visits: 190.0K
|
Teds solution is the best way,as welding cast is very risky especially wher you have spikes of 60 to 80psi.the lesson hear is easy outs,the thred type just make the tapered plug tighter .the square type are my preferenc. some plugs are best left in. welding cracks in water jacket easier and like preveous post sujests small sections and lots of peaning..But ther ar no 2 castings the same re content of nickel etc. i had good results warming the block weld 1or 2 inches peen then leave over night in a warm place.. also when you put the new plug in re teds direction be sure to use a cast plug.
|
|
|
dennis22
|
|
Group: Forum Members
Last Active: Last Month
Posts: 166,
Visits: 59.7K
|
Ah great, thanks everyone for the feedback. Willowbilly3 I have done some cast welding before but it was on thick material so I would be a bit anxious to weld this- good to know but, thanks. Ted, your talking my language here, I was hoping someone would reassure me, but was just unsure having not done any work like this before. Thanks for the reply, much appreciated!
Thanks, Dennis.
56 F100 - 272 Y Block NSW, Australia.
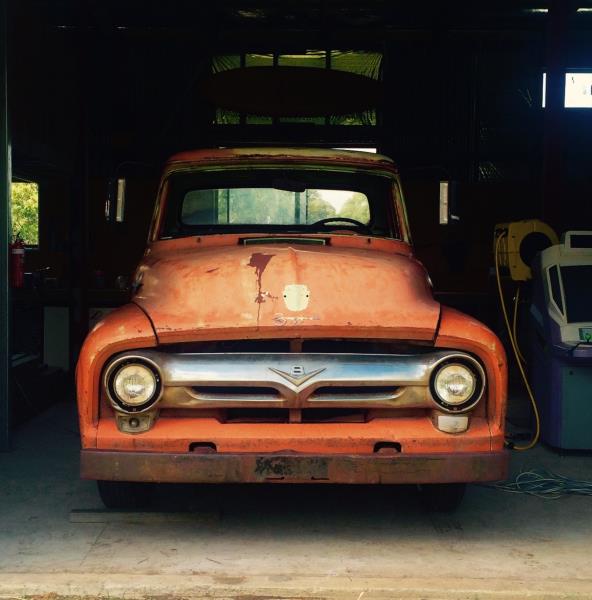
|
|
|
Ted
|
|
Group: Administrators
Last Active: 5 hours ago
Posts: 7.4K,
Visits: 205.0K
|
No Disaster there. You’ll simply need to tap the existing hole a bit deeper with a 3/8”NPT tap and appropriately install the threaded pipe plug deeper into the block. The next intersecting oil hole at that location is roughly 0.850” from the unbroken end of the block while the plug is about 0.500” thick. That gives you about another 0.350” to work with before potentially blocking any intersecting holes. If necessary, you can shorten the leading edge of the pipe plug to give some additional internal clearance. Be sure to put sealer on the threads before installing the plug.
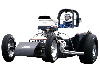 Lorena, Texas (South of Waco)
|
|
|
willowbilly3
|
|
Group: Forum Members
Last Active: 7 Years Ago
Posts: 30,
Visits: 116
|
Very fixable. There are a lot of ways to attack that. My personal preference for welding cast is usually stick weld. I've done a lot of brazing over the years but find it takes so much heat and the chances of warping or damaging other parts is fairly substantial. I would cut the rest of the boss off and weld on a whole new piece. If you haven't done this sort of repair you probably should take it to someone who has. One method that has worked very well for me, especially on exhaust manifolds, is to use the cheap cast iron arc rod, not the high nickel. I don't preheat. After grooving and prep I weld just a very small bit at a time, about a 3 second burst. Then peen the heck out of it with the pointy end of the chipping hammer until you can touch it with bare skin. Then repeat. After the weld is all laid in (especially on a manifold) I grind and smooth the weld. If there is any undercut or area that is below the surface, weld that in until you can smooth it to a nice finish with a flap wheel on the grinder.
|
|
|
stuey
|
|
Group: Forum Members
Last Active: Last Week
Posts: 440,
Visits: 3.8K
|
|
|
|
dennis22
|
|
Group: Forum Members
Last Active: Last Month
Posts: 166,
Visits: 59.7K
|
Maybe about 9mm or roughly 3/8 inch of thread left
Thanks, Dennis.
56 F100 - 272 Y Block NSW, Australia.
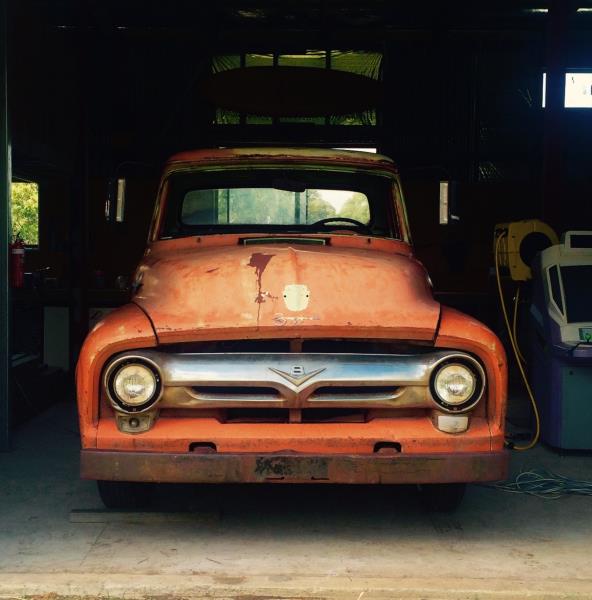
|
|
|
dennis22
|
|
Group: Forum Members
Last Active: Last Month
Posts: 166,
Visits: 59.7K
|
Thanks, Dennis.
56 F100 - 272 Y Block NSW, Australia.
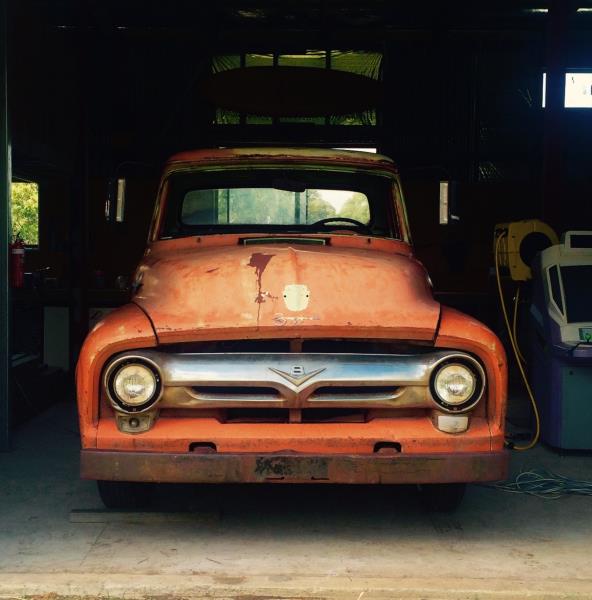
|
|
|
dennis22
|
|
Group: Forum Members
Last Active: Last Month
Posts: 166,
Visits: 59.7K
|
Thanks, Dennis.
56 F100 - 272 Y Block NSW, Australia.
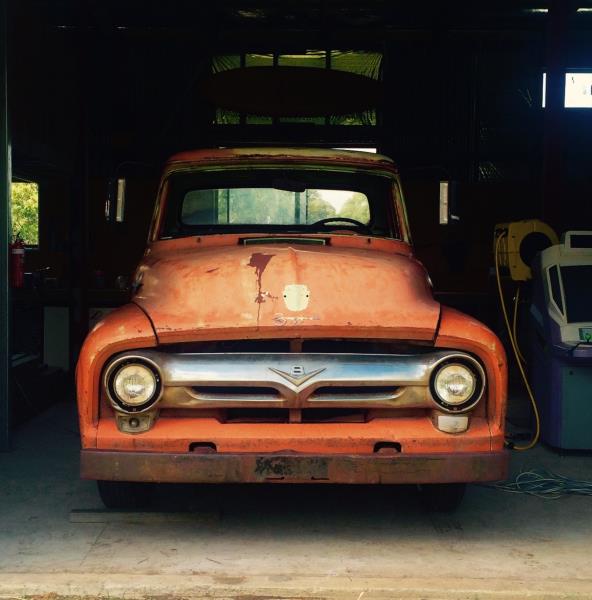
|
|
|
dennis22
|
|
Group: Forum Members
Last Active: Last Month
Posts: 166,
Visits: 59.7K
|
Hi guys, just removing the oil gallery plugs,they were all frozen in there so I used an easy out. Worked well getting all of them out, except this is what happened to the last one. Pretty devastated, is it a complete disaster or is it salvageable? There looks like there might be enough thread left.
Thanks, Dennis.
56 F100 - 272 Y Block NSW, Australia.
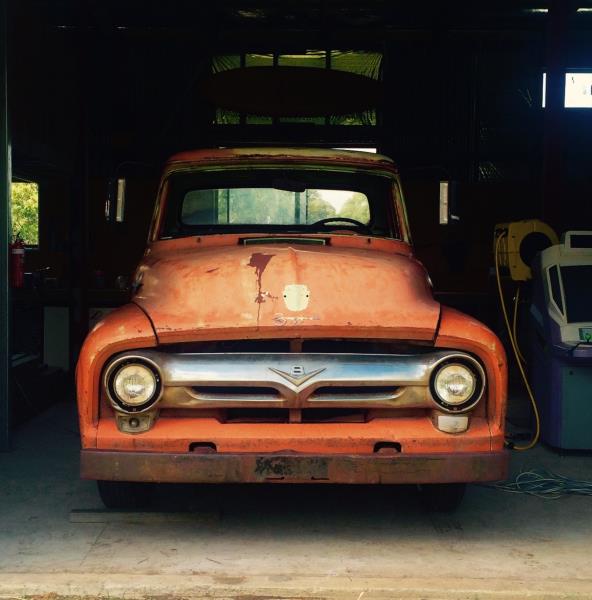
|
|
|