Author
|
Message
|
bergmanj
|
|
Group: Forum Members
Last Active: Last Year
Posts: 257,
Visits: 3.9K
|
Folks, [Yes, it's really a 312, ECZ crank, main caps, and rods out of a '57 Mercury wagon a very long time ago now.] "Search" isn't working for me again, so...: 1. What is ideal quench range between piston top and head quench area? 2. I'm looking for new composite and original equip't steel head gasket crush (I know that I saw it here recently - just can't search it!) 3. With typical replacement pistons being "down in the hole", I thought that using EBU-dimension rods (0.072" longer C to C at 6.324"), rather than the original ECZ rods (at 6.252" C to C), quench might be brought back up into the appropriate range when using composite head gaskets.
Critique, comments, please.
Thanks, JLB
55 Ford Crown Victoria Steel Top
|
|
|
steinauge
|
|
Group: Forum Members
Last Active: 10 Years Ago
Posts: 143,
Visits: 1.4K
|
Both my 312 and 292 engines had pistons .022-.025" down in the hole.I had both blocks decked .025". The replacement pistons I used measured the same from the pin centerline to the top of the pistons as the OEM pistons.The 292 and 312 both got Egge machine pistons.Deck clearance is now zero to +.002. I decked the 113 heads on the 292 .020" and used a .035" crush thickness gasket.All seems to work fine.I believe the .072" longer rod is going to require you to machine more off the piston head than would be wise.It is also going to get the top ring closer to the deck surface and that will likely require more end gap. I wouldn't think that a piston to head clearance under about .035-.040" would work out well for general driving.
|
|
|
NoShortcuts
|
|
Group: Forum Members
Last Active: 2 Years Ago
Posts: 1.4K,
Visits: 179.6K
|
FoMoCo original piston in-the-hole manufactured dimension coupled with the use of composite head gaskets and the replacement pistons I've checked (Silv-O-Lite, Sealed Power have a greater piston pin height than original) will add up to significantly greater quench dimension than original engine manufacture. My recollection of previous quench topic discussions with input from Ted Eaton and John Mummert was that approaching a total quench dimension of .060 is too much on a y-block and can result in detonation issues. I THINK that there was recommendation of trying to come in with a total quench figure of .035 to .045 accomplished by decking the block. Ted Eaton authored a comprehensive article on the compressed thickness of various manufacturer's y-block cylinder head gaskets. Click the link below to reference it. http://www.eatonbalancing.com/blog/2012/06/30/head-gasket-volume-calculation/Hope this helps.
NoShortcuts a.k.a. Charlie Brown near Syracuse, New York
|
|
|
bergmanj
|
|
Group: Forum Members
Last Active: Last Year
Posts: 257,
Visits: 3.9K
|
Folks, Thanks for the interest and feedback! I found the article by Ted Eaton in regards to Head Gasket Volume Calculation, and studied it carefully (thanks for the link!): Very good information about specific gasketing: Kudos to Ted and Michael Henaults. Also, thanks for the concern about piston head thickness; I've read about that elsewhere too, so, am paying attention there too. Ted E., I've followed your “stuff” here for years, and very much respect your “real-world” opinions: Could you also please comment on my thoughts about using the longer EBU rods; and, ideal range for quench thickness. I'd sure appreciate it, if you would / could. I believe, though, that I found an error in the caculation formula stating that Area (A) is calculated as (Circumference © [as approximated by sealing ring distance] divided by pi (3.1416)) squared, i.e., Diameter (D) squared. To my best knowledge, Area is calculated as pi times (radius (r)) squared (not (D) squared); i.e., A = pi x r squared, which gives actual answers one-fourth as shown in the table. The answer for the example stated should be 2.259 cc, instead of the 9.64 cc as published; and, all the following answers in the table should be divided by four for the correct calculated volumes. Also, because none of these sealing ring openings are perfectly round, the actual volumes will always be somewhat less than shown as calculated; though, fairly close (close enough to be decent, useable “for-comparison” estimates). Regards, JLB
55 Ford Crown Victoria Steel Top
|
|
|
NoShortcuts
|
|
Group: Forum Members
Last Active: 2 Years Ago
Posts: 1.4K,
Visits: 179.6K
|
Steinauge's mention of electing to mill his 113 heads .020 has no bearing on your engine's quench dimension. I suspect that he had the heads milled to compensate for the increased effective volume of the cylinder head combustion chamber and quench area above the piston caused by the thickness of the particular composite head gaskets he chose to use. The effective increase in combustion chamber volume and quench area volume only relates to the static compression ratio of your engine. A factor to consider? Yes... What's likely more important is the dynamic compression ratio of the engine you plan to assemble. The timing event of your camshaft (specifically, when the intake valve closes) will tremendously affect the dynamic compression ratio of your engine and what grade of gasoline you'll need to prevent detonation.
That is not to dismiss what was stated previously about maximum quench dimension. Regardless of how appropriate your dynamic compression ratio is for your intended grade of fuel, if the quench dimension for your engine assembly is approaching .060 on a y-block, you will likely experience detonation.
Decking a block is the most effective way to increase static compression ratio. It will accomplish more than milling the heads to reduce the combustion chamber volume because it reduces the quench volume, too.
With a 50+ year old engine block that was machined using the technology of that day, coupled with the heating cycles the block has been through since... I would encourage you to seriously consider having the block squared and decked. I can think of no advantage to using 292 engine EBU connecting rods instead of 312 ECZ connecting rods. You seem to be focused on attempting to compensate for the pistons being in the hole due to day-one machining.
IF you rummage through the Forum archives, Ted Eaton and John Mummert, to name but two of our members, have recounted numerous examples of how incorrect the original machining of y-block FoMoCo engine block decks have been found to be. I THINK I read somewhere that the pan rails were the basis for the FoMoCo machining of the block decks back in the day. IF you have block deck work done in an auto machine shop today, the reference plane will be the crankshaft main bearing saddles. The dimension and the uniformity of dimension from the center of the mains to the deck is the resolution to your excessive in-the-hole measurement.
IF I were 'efforting' to use longer connecting rods in a 312 engine build, I would order custom pistons with the piston pin moved to compensate for the increased length. Technically the longer rods should affect the engine's generated torque curve and at what rpm it peaks.
NoShortcuts a.k.a. Charlie Brown near Syracuse, New York
|
|
|
bergmanj
|
|
Group: Forum Members
Last Active: Last Year
Posts: 257,
Visits: 3.9K
|
Charlie,
Thanks for the reply. My background is in manufacturing and electronics technical and engineering work (mostly Fed. Gov't and Military); retired now. But, I've lived long enough to understand that practical considerations often are more important than theoretical -- which is why I'm asking for feedback here from you y-block "experts". (A little "groveling" never hurts anyone [smiley].)
I've built a few of these engines (239, 272, 292, and 312) over the years; and, have striven to be more "perfect" with each one as built ( ya, I know: Probably "obsessive / compulsive" - lots of us engineering / technical types go with that issue. It's much easier to deal with "things" than with people!).
Yes, I simply want to understand the nuances of replacement pistons being "down-in-the-hole" further than originals, plus the effect of modern thicker head gaskets on compression (call it a bug up my a$$, if you will). I do understand that decking the block can correct for that, and that head milling won't. But, between the replacement pistons and thicker head gaskets, I am simply exploring what effects using the longer EBU rods would have (too little quench, not enough piston top clearance, less piston wear / skirt scuffing, torque and horsepower curve differences, etc., perhaps).
Can you, or someone else explain more in detail the effects of cam timing, duration, lift, etc., too. This is an area in which I have absolutely NO expertise.
Regards, JLB
55 Ford Crown Victoria Steel Top
|
|
|
Ted
|
|
Group: Administrators
Last Active: 2 days ago
Posts: 7.4K,
Visits: 205.0K
|
bergmanj (9/19/2015)
.........Ted E., I've followed your “stuff” here for years, and very much respect your “real-world” opinions: Could you also please comment on my thoughts about using the longer EBU rods; and, ideal range for quench thickness. I'd sure appreciate it, if you would / could.
I believe, though, that I found an error in the caculation formula stating that Area (A) is calculated as (Circumference © [as approximated by sealing ring distance] divided by pi (3.1416)) squared, i.e., Diameter (D) squared.To my best knowledge, Area is calculated as pi times (radius (r)) squared (not (D) squared); i.e., A = pi x r squared, which gives actual answers one-fourth as shown in the table. The answer for the example stated should be 2.259 cc, instead of the 9.64 cc as published; and, all the following answers in the table should be divided by four for the correct calculated volumes.
Also, because none of these sealing ring openings are perfectly round, the actual volumes will always be somewhat less than shown as calculated; though, fairly close (close enough to be decent, useable “for-comparison” estimates). I revisted the formulas used in the head gasket volume calculation and I’ll stand by them. By using the head gasket fire ring length measurements in the head gaskets, not having a perfectly round hole in the head gasket in which to measure is not a show stopper. What you have to love about basic math is how the same result can be derived from different approaches. I’m using diameter squared X 0.7854 for the basic area formula rather than pi r squared; same result with either formula but using diameter simply reduces the amount of number crunching that must be performed on my end. The 0.7854 value is derived by dividing pi by 4 while the 12.87 value used in my head gasket volume calculation comes from multiplying together 0.7854 and 16.387. The 16.387 value is simply 2.54 cubed with the 2.54 number being the number of centimeters per linear inch. I’m using pi in the head gasket calculation to simply convert the circumference measurement of the gasket fire sealing ring back to a diameter dimension that is then used as part of the head gasket volume calculation. Back to rod lengths. While a longer rod will have less angularity with the crank throw at 90°, it does exhibit a longer residence time at TDC which is good where detonation may be border line or the exhaust is not very efficient. The 2010 EMC Y engine used a 6.750” long rod due to the engine fuel that was supplied having an 86 MON octane value. The longer rod will also exhibit less thrusting on the piston skirts which simply makes for reduced piston skirt wear but also less friction at that point. On the flip side of this, the piston take away speed from TDC with a shorter rod happens more quickly which tends to make for better torque production by lieu of a quicker movement of the intake charge. The 0.070” difference in lengths between the ECZ/C1TE rods versus the EBU/C2AE rods is not much and for the most part is not measurable at the seat of the pants. I have experimented with shortening the rods 0.450” while also increasing the camshaft lobe centerline 4° which has resulted in a 45 horsepower increase with all other attributes remaining the same. In that particular instance, the exhaust was so good it was over scavenging which was allowing for a loss of intake charge out the exhaust; a shorter dwell time at TDC (by lieu of a 0.450" shorter rod) along with a reduced camshaft overlap cycle (increased lobe centerline) fixed that problem without having to put a less efficient exhaust system on the engine. The total package must be taken into account when working out an engine combination. As a general rule, the minimum value for piston top to the cylinder head should be no less than 0.035”. I’ve been right there and have left the imprint of the oversize that was stamped in the piston on the head surface when working with a performance application. Varying the piston alloy and/or the connecting rod construction can make this number somewhat variable and especially where aluminum connecting rods are being used. On the other end of the scale, 0.065” should be considered the maximum value between the piston top and the head surface but as the compression ratio lowers, this value can be increased.
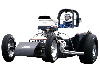 Lorena, Texas (South of Waco)
|
|
|
bergmanj
|
|
Group: Forum Members
Last Active: Last Year
Posts: 257,
Visits: 3.9K
|
Ted, Please excuse the delay: Dead-slow dial-up isn't really conducive to quick replies
55 Ford Crown Victoria Steel Top
|
|
|
bergmanj
|
|
Group: Forum Members
Last Active: Last Year
Posts: 257,
Visits: 3.9K
|
Ted, Open mouth, stick foot in! (Me, that is!) Please excuse the delay: Dead-slow dial-up is just "the pits". Thanks very much for the detailed explanation; math looks good; I made a bad conversion a$$uption. Still looking for more info on cam timing effects. Regards, JLB
55 Ford Crown Victoria Steel Top
|
|
|
Ted
|
|
Group: Administrators
Last Active: 2 days ago
Posts: 7.4K,
Visits: 205.0K
|
bergmanj (9/23/2015)
....... Still looking for more info on cam timing effects. Regards, JLBI recently did a series of articles for the Y-Block Magazine going into detail on how to degree in a camshaft. Within the first part of that article, there are some definition explanations covering the various aspects of camshaft design which is what you are probably looking for. If you don’t get the YBM, then you likely missed that series of articles (it was a three parter). In the near future I will post those articles on my website at which point I’ll put the link here.
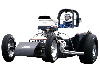 Lorena, Texas (South of Waco)
|
|
|