Author
|
Message
|
Campsite
|
|
Group: Forum Members
Last Active: 9 Years Ago
Posts: 35,
Visits: 632
|
Ted; Thank You for the reply. I will keep all this info, and this winter engine will come out, and go thru very slowly. The flywheel was resurfaced,and the Damper was done before the balance. I know about the plug wiring.So at this point the bird is going to be driven, till winter. A couple of lessens learned. Thank You Bob
Bob
|
|
|
Ted
|
|
Group: Administrators
Last Active: 2 days ago
Posts: 7.4K,
Visits: 205.6K
|
Campsite (7/18/2015)
Here is my problem, There is a vibration in the lower end. This is what I have tried, With engine in car, disconnected Trans, slide it back some, dropped Clutch plate, and pressure plate, reinstalled starter, reinstalled Trans. Then started engine, and ran it. The vibration starts at about three thou, and at 4500 rpm it is getting bad. This engine was balanced, line honed, and it was total rebuild. When balanced it was done with all the parts needed. Vibration Damper was rebuilt. The reason 7 cylinder was sleeved, was there was a very bad spot, with rust just below the ring travel at TDC. Some time in 25 years storage The antifreeze and water mix, leaked thru, into 7 cylinder. I have tried every thing that I can think of to find the Vibration. This is why I have come up with the sleeve not installed right. At this point I will try any idea out there. While the balance job is suspect, here are some other things to consider. First insure that the spark plug wires are hooked up correctly. While this may seem obvious, I’ve seen some engines with as many as four cylinders out of sequence that actually idled just fine but simply didn’t have throttle up power and there was a noticeable vibration at rpm. Even the GM engines with the 4-7 cylinder swap run pretty decently even when the spark plug wires are not swapped to match the changed up camshaft. Again these have a noticeable vibration when running at 3000 rpms. Next run a compression check on all eight cylinders. All readings should be within 10% of each other from the lowest to the highest. If there’s a wide spread in the readings, then look at the valve lash next. Performing a leak down test can also help to isolate problems with cylinders that are reading to the low side. Have you unhooked the belts from the accessories to insure that the vibration is not coming from one of the accessories? Water pump, fan pulley, fan, generator/alternator, air conditioning compressor, power steering pump, etc. Back to that balance job. Was the flywheel balanced as part of the rotating assembly? Has the flywheel been resurfaced since the rotating assembly was balanced? I’ve seen some major balance issues with rebuilt dampers so make sure it was balanced as part of your rotating assembly after it was rebuilt. Beyond all that, do you have a balance spec sheet showing what the bobweight value was for that 312? If you can post that bobweight value, it can be compared it to some of the other 312’s and determine if it’s in the ballpark. Extremely heavy or light bobweight values could be the result of a simple math mistake by the person performing the engine balancing.
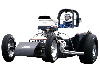 Lorena, Texas (South of Waco)
|
|
|
2721955meteor
|
|
Group: Forum Members
Last Active: Last Year
Posts: 927,
Visits: 190.0K
|
if the sleve was off canter you would have isues with the con rod being way off centre at the wrist pin,or wrist pin would pop out a keeper.,if the rod moves back and forthwith no effort the bor has to be alighned.even if ther was water showing a thick sleeve is as good as new.also to bore of center would have to be a carpenter doing the work.posible the balance jub is the isue,what a shame.let us know what you find
|
|
|
Campsite
|
|
Group: Forum Members
Last Active: 9 Years Ago
Posts: 35,
Visits: 632
|
Here is my problem, There is a vibration in the lower end. This is what I have tried, With engine in car, disconnected Trans, slide it back some, dropped Clutch plate, and pressure plate, reinstalled starter, reinstalled Trans. Then started engine, and ran it. The vibration starts at about three thou, and at 4500 rpm it is getting bad. This engine was balanced,line honed, and it was total rebuild. When balanced it was done with all the parts needed. Vibration Damper was rebuilt. The reason 7 cylinder was sleeved, was there was a very bad spot, with rust just below the ring travel at TDC. Some time in 25 years storage The antifreeze and water mix, leaked thru, into 7 cylinder.I have tried every thing that I can think of to find the Vibration. This is why I have come up with the sleeve not installed right.At this point I will try any idea out there.
Bob
|
|
|
Rono
|
|
Group: Forum Members
Last Active: Last Year
Posts: 1.3K,
Visits: 80.0K
|
Another thing to think about when re-boring is core shift. If you can find a shop that can sonic test the block before any additional work is done, that could save the block. You don't want to get to close to or into a water jacket and with the sonic test you can determine just how much material you have all around the cylinder bore. Maybe this is why #7 cylinder was bored off center in the first place.
Ron Lane, Meridian, ID
|
|
|
charliemccraney
|
|
Group: Moderators
Last Active: 22 minutes ago
Posts: 6.1K,
Visits: 442.5K
|
Is it off center enough that it is actually a problem? Cylinders can usually be resleeved and they can likely bore a fresh liner back to a better center. Ultimately, you need to get it apart and check with local machine shops about that one.
Lawrenceville, GA
|
|
|
Campsite
|
|
Group: Forum Members
Last Active: 9 Years Ago
Posts: 35,
Visits: 632
|
Good Morning; I also have a small problem with a 57 312 block. I had to have a sleeve installed in number 7 cylinder. The guy when he did the sleeve, bored the cylinder off center, and installed the sleeve, Lord only knows how he did it. The bore is .040 over. I did not find it out until I had build the engine, and had run it. Now I am wondering if that block can be saved. by re boring it. And installing a new sleeve.
Bob
|
|
|
Ted
|
|
Group: Administrators
Last Active: 2 days ago
Posts: 7.4K,
Visits: 205.6K
|
If the threads in that single main bolt hole is all that’s wrong with that block, then it’s worth fixing. As has been mentioned, check the webbing and the block for cracks before investing too much time and/or expense into the block.
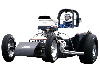 Lorena, Texas (South of Waco)
|
|
|
PF Arcand
|
|
Group: Forum Members
Last Active: Last Year
Posts: 3.3K,
Visits: 238.8K
|
Good 312 blocks are getting harder to come by.. If the lower threads held previously, it might be possible to helicoil the upper stripped area. I believe I read that some blocks can also be drilled slightly deeper & further threaded. Maybe one of the engine gurus here can elaborate on that. Of course it would also be wise to confirm that the block isn't also cracked before attempting repairs.. Hope it can be saved.
Paul
|
|
|
slumlord444
|
|
Group: Forum Members
Last Active: 7 days ago
Posts: 1.2K,
Visits: 137.6K
|
I have an original '57 standard bore 312 block that I managed to strip out the threads in one of the mains by using the short bole 49 years ago. Cobbled up a longer bolt in the stripped hole and ran it for while with no problems. I am cleaning out one of my storage garages and need to know if this can safely be repaired or should I scrap it? I have a couple of spare 292 blocks that could be converted to 312's but I hate to trash something that I may need or someone else may need.
|
|
|