By KULTULZ - 2 Years Ago
|
- ASKING FOR A FRIEND -
[QUOTE=metro1;2268638]
I removed the heads from another engine and had them reworked at the machine shop. I was installing them today and ran into something I had not experienced before. On the drivers side head the top holes in the head do not exactly line up with the threaded holes in the block. The bolts drag against the front of the holes in the head. I tried it back on the old engine and the same thing. It must be bored wrong. The bolts will go in but the drag will make torqueing it incorrect. I am using ARP bolts which have a smaller shaft diameter except for the top 5/16 so they only scrape there. At this point I could shave a few thousands off of the top part of the bolts but I really don't want to do that. I guess I could open up the front top of the holes in the head. Has anyone ever ran into this?
THREAD SOURCE - https://www.fordbarn.com/forum/newreply.php?do=newreply&p=2268638[/quote]
|
By DryLakesRacer - 2 Years Ago
|
If the head sits on the dowels correctly I would slightly enlarge the holes and use hardened arp type washers on the fasteners. I’ll bet .005” would probably do it. Since they are cast iron a die grinder with an extended shank tool would do the same thing. My father owned a machine shop and was a wind tunnel model maker but I saw him fix a friends head with a similar problem. He clamped a head to the Bridgeport mill table, put a cutting tool that looked like a reamer and cut the side of the hole that hit a bolt. Also it’s possible to put studs on the top row a slide the head over them or if there are Allen ends on them put them in with all the other fasteners in but not tight. There are many ways to fix this without distorting the torque.
|
By Ted - 2 Years Ago
|
I run into this when angle milling the heads. At a 2° angle change, the head bolt holes in the heads are no longer perpendicular to the threaded holes in the block and are off significantly at the top of the heads. At a two-degree head deck angle change, the head bolts will not come close to starting into the block. For these, I have to machine the head bolt holes with an end mill at the appropriate angle so it elongates the head bolt hole at the top of the head while not changing the hole dimension at the bottom of the head. And then the head bolt holes at the top of the head (both the long and the short) must be refaced so that they are square with the holes. From the description you give for the friend’s cylinder head, it was resurfaced without care to ensure that the deck surface was square to the grinding or cutting tool when the head was resurfaced. If that is indeed the case, then the angle between the head surface and the intake mating surface will be different. If one cylinder head bolts down fine, then use that angle as a comparison to the deck to intake angle on the head that’s having a head bolt issue. Another telltale would be if the head bolt hole at the bottom of the head is not square with the deck surface of the head. A machined bar that fits the head bolt hole at the bottom of the head would help to determine that either with some layout dye or a square or a dial indicator. Several options there.
|
By KULTULZ - 2 Years Ago
|
- THANK YOU GENTLEMEN! - Didn't need to hear about the intake not sitting down correctly ...  How difficult to 'square' the cyl head ($$$) (if it is the cyl head) ?
|
By Ted - 2 Years Ago
|
KULTULZ (11/10/2023) Didn't need to hear about the intake not sitting down correctly ...  How difficult to 'square' the cyl head ($$$) (if it is the cyl head) ? First is to validate that the intake to deck angle is indeed different. Once that’s confirmed, the head just needs to be milled again and this time removing the amount of inappropriate deck angle that was put there. One option would be to adjust the deck angle off of the intake manifold flange while another option would set the milling machine off the head bolt holes so that the mill is at a 90° angle to the head bolt holes. Keep in mind that the combustion chamber cc’s are getting reduced and that might be an issue depending upon how much is being milled versus what the other head has been milled. I would suggest cc’ing both heads before any more milling to see exactly what is there. Generally, a 0.0065” cut reduces the chamber volume 1cc. Here’s the link for the exact numbers for milling the various Y heads a specific amount for a 1cc reduction. Cylinder Head Milling for a 1cc Reduction – Eaton Balancing
|
By Hoosier Hurricane - 2 Years Ago
|
Kultulz said that the bolts drag on the front side of the holes. That would indicate that the head is milled crooked end to end. A quick and dirty way to check this would be to measurer the pads on the lower side of the head and compare them end to end. He could also CC the chambers and see if they vary from one end to the other.
|
By KULTULZ - 2 Years Ago
|
I wanna thank you guys again.
If this happened to me I would have had a heart attack ...
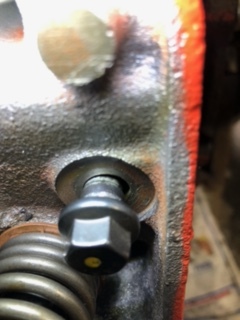
|
By Ted - 2 Years Ago
|
Hoosier Hurricane (11/11/2023) Kultulz said that the bolts drag on the front side of the holes. That would indicate that the head is milled crooked end to end. A quick and dirty way to check this would be to measurer the pads on the lower side of the head and compare them end to end. He could also CC the chambers and see if they vary from one end to the other. John. Thanks for pointing out that the bolts are dragging on the front side of the holes. I totally missed that in reading the original post. The intake to deck angle is likely okay in that case but still could present an intake gasket sealing problem from front to rear on that particular head. Cc’ing the combustion chambers would confirm that the head was simply milled more in an end-to-end fashion rather than more in a intake to exhaust side fashion. Using the math on the difference in the combustion chamber sizes would give a good indication on how much the end of the head with the larger combustion chambers would need to be milled to get the end with the larger chamber even with the end of the head with the smaller chamber. Still a simple fix in remilling the head again and this time getting the deck square with the head bolt holes.
|
By Ted - 2 Years Ago
|
Kultulz. It would be good to know what the head casting number is. Knowing that and the combustion chamber sizes would be helpful in determining how much the head would need to be remilled to correct the difference in combustion chamber sizing.
|
By KULTULZ - 2 Years Ago
|
10-4.
Let me see if I can get it. It belongs to a poster over@ FORDBARN.
|
By KULTULZ - 2 Years Ago
|
HE POSTED -
The numbers I see are ECL6090 with an "A" over top of the 0 . Other number 4BA.
|
By KULTULZ - 2 Years Ago
|
While I have all the expert FYB people gathered, there is one more thing I would like to ask concerning the FYB CYL HEAD -
The pads @ the bottom of the head, they are used to determine deck thickness before and after machining, correct?
On the EXH SIDE there are four pads. Are all four used to determine squareness?
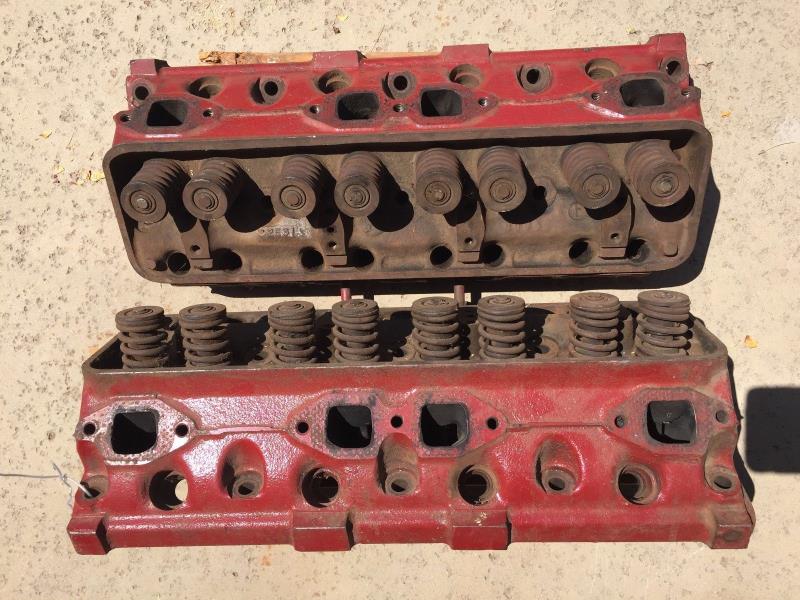
There are also two pads (?) on the INT SIDE (@ bottom runners). Are these used also?
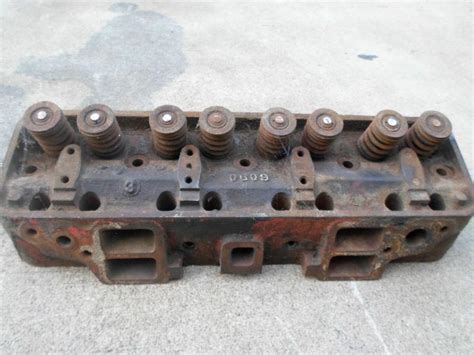
Again, THANX! for the info ...
|
By 55blacktie - 2 Years Ago
|
Good question. The experts (Mummert & Eaton) told me to measure the center pads, near the spark-plug holes. If the heads have not been milled, the pads should be 1.010". Compare the heights of the center pads to the heights of the end pads, in case the heads were milled more on one side/end. As Ted said, measuring the combustion chamber volumes also helps.
Although Ted did say that it's possible for one side (front-to-back) of a head can be milled more than the other, I've not been told (or read) anything about measuring the pads on the intake side. Maybe misalignment of the intake manifold confirms the same thing.
|
By Ted - 2 Years Ago
|
KULTULZ (11/11/2023) HE POSTED- The numbers I see are ECL6090 with an "A" over top of the 0 . Other number 4BA. The ECL-A heads require a 0.0063” cut for each combustion chamber reduction of 1cc. If the heads get progressively larger (or smaller depending upon your perspective) from one end to the other, then that 0.0063” number can be used to mill the heads accordingly to equalize the combustion chamber volumes.
KULTULZ (11/12/2023) While I have all the expert FYB people gathered, there is one more thing I would like to ask concerning the FYB CYL HEAD - The pads @ the bottom of the head, they are used to determine deck thickness before and after machining, correct? On the EXH SIDE there are four pads. Are all four used to determine squareness? There are also two pads (?) on the INT SIDE (@ bottom runners). Are these used also? Again, THANX! for the info ... The intake bosses have no measurement value related to the thickness of the Y cylinder head. As a general rule, the four bosses on the exhaust side of the head for head thickness/milling purposes are all the same size but it’s the two center ones that are the ones specified by Ford when checking the heads. When milling the heads, it’s not unusual for the end exhaust side bosses to differ from the two center ones depending upon the warpage of the heads. As Jeff brings up, it is possible to mill the heads a different amount end to end by design to equalize the combustion chambers. I get away with as much as 0.020” difference from end to end and not have any issues with the intake manifold sealing as it should. The actual Ford spec for the thickness of the two inner bosses under the exhaust ports for the Ford Y is 1.000 ±0.001”. There are some exceptions to that and TSB #973 lists one of those exceptions. Here’s TSB 973 but it’s in a bound book and does not copy well at the binding.
|
By 55blacktie - 2 Years Ago
|
Ted, does the same +/- 0.001 also apply to ECZ-G heads?
|
By KULTULZ - 2 Years Ago
|
Thank You for sharing that info Ted ...
|
By Ted - 2 Years Ago
|
55blacktie (11/12/2023) Ted, does the same +/- 0.001 also apply to ECZ-G heads? Yes.
|
By 55blacktie - 2 Years Ago
|
Thanks, Ted.
|
By 2721955meteor - 2 Years Ago
|
the head bolts showed are nothing like the originator replacement grad8 cap screws. the bolt showed incorporates a flat washer and bolt 1 part why not machine a small a mount just below theboltwherthehead of bolt touches the head casting
|