By pegleg - 11 Years Ago
|
You may have created a monster! Good for you.
|
By pegleg - 11 Years Ago
|
Probably the base Caled "Great Lakes" which is actually in North Chicago or Waukegan, Il. It's the basic training site for most of the Navy. I was there a few short years ago (50! )
|
By pegleg - 11 Years Ago
|
Dan, Hope he makes it. Subs are tough, I kow something about that. Spent 4 years on a diesel boat (s) in the 60's. If he makes through you can be VERY proud of him.
|
By pegleg - 10 Years Ago
|
Dan, Being from Ohio I can tell you the best deals are usually in one of the small towns away from the citizen and work centers.
|
By GREENBIRD56 - 10 Years Ago
|
Good luck finding your own place Daniel - that renting stuff gets old real quick..................... I appreciate your circumstance, been there done that. Smart move to take your time finding the best homestead on your own timetable - always worked best for my family.
|
By kevink1955 - 8 Years Ago
|
Thanks Daniel, that fix for FireFox works.
|
By MoonShadow - 10 Years Ago
|
I bought one of those cheapo florescent lights in a tube. Mounted it to the cabinet so it under the front edge at the top of the face. Adds a new angle light for ridding yourself of shadows. I late added a 100 watt safety enclosed fixture in place of the original light. Nice and bright. My window is exactly 12" X 24" so I just keep a couple on hand. I probably buy two of them a year to replace the damaged ones. Cheaper than the tearoffs. I use a lot of glass bead but for super dirty/rusty parts I switch to black beauty. Chuck
|
By MoonShadow - 10 Years Ago
|
Do you have a part number for the sway bar bushing sets? Chuck
|
By MoonShadow - 10 Years Ago
|
Daniel, Milford, CT is about 3 hours from me in New Hampshire and 5 hour from Bill Myrand in Maine. We will have to meet up someday. Maybe at the nostalgia meet at New England dragway. Chuck
|
By MoonShadow - 10 Years Ago
|
Well at least you be near the shootouts. See you at one of those. Chuck
|
By MoonShadow - 10 Years Ago
|
Since you are renting I guess an ramp access to the basement is out of the question. I'm glad I've made my last move. It would take me weeks to clear out my garage and the metal scrap guy would be dancing. But what would I do with all the "spares" for the Vicky? Doors from Texas are way too good to let go. You never know when I might have a problem driving among-st these Yankee's. The extra engine parts, somebody might need them. AND there is no way I can live without my 3 tool boxes and 8 drawer roll around cart. Traveling in the military I couldn't have a lot of tools or anything else. Since I've been retired I've amassed a ton of tools and still don't have everything I want, not necessarily need. When I die the scrap man is really going to have a field day! Now where was that wrench I needed? It's got to be in one of these drawers. Chuck :-)
|
By MoonShadow - 9 Years Ago
|
I saw a company at the Grand National Roadster Show that reproduces a lot of different old style steering wheels. They did have our wheels but as I recall they were in the $400 plus range. Might have been these guys: http://www.restorationperformance.com/1963-impala-steering-wheel-red/
|
By MoonShadow - 8 Years Ago
|
I'm using internet explorer and cant see the pictures.
|
By MoonShadow - 7 Years Ago
|
Looks and sounds great. Nice work Dan.
|
By glrbird - 11 Years Ago
|
Daniel I have used an air chizel before to rip the bushing from back to front so it wil colapse and just push it out.
|
By pintoplumber - 10 Years Ago
|
Dan, if it happens again that you can't paint, put the paint in the refridgerator. When I painted the 54 f 100, I didn't get enough paint around the rear window opening. I called a friend and he said put it in the fridge. He told me next day add more reducer and spray the touch up area. Then add more reducer and spray again. It blended right in. I was using acrylic enamel.
|
By LordMrFord - 7 Years Ago
|
Looking sweet as what.
|
By Daniel Jessup - 11 Years Ago
|
I have always been impressed by others on this site who let us into their world of all things Y block by posting their work in the form of words, diagrams, and photos. The craftsmanship and attention to detail is simply amazing. For the past several years, all that I have been able to do is work on sub-assemblies - carburetors, transmissions, engines, etc. Now I have delved into the realm where only the talented and dedicated dwell - an all out assault on your vehicle, by yourself, to do the mechanical, the body work, the paint, etc. At one time I had visions of grandeur on this scale when I put a 55 Sunliner project in the garage. The need for the family budget finally overwhelmed the whole idea, and alas - it was sold piece by piece. The sum total of its parts was definitely worth much more than its package value, but the old gal helped many a man complete his own Sunliner project in places around the globe. Well, all the while a 55 Fairlane sat idly by waiting her turn for attention. Some of you may remember that several years ago this car received a rebuilt 292 that really screamed even though an original Fordomatic was weighing her down and robbing her horsepower.
Here is the plan... to put her back on the road again with the following changes and facelifts:
1. Remove the 292 and check her out on the portable engine run stand.
2. Remove the original Fordomatic and lose it in the garage somewhere.
3. Prep and install an original 3 speed/overdrive manual transmission and all associated parts including the column shift.
4. Remove the worn out 55 steering gear and wheel so that I can prep and install a 1956 Steering gear, column, wheel, etc.
5. Remove the entire front end sheet metal to begin the prep for paint. The firewall will come first. Paint with the existing color scheme, SS Urethane red over white. (anyone ever use Summit's paints?)
6. Consider A/C to the mix - the wife is requesting it. 
7. Finish the interior - the dash and sheet metal garnish are all painted and ready to back into the car. The headliner is 90% installed. Need to remove the rear glass first.
That's enough for now. If you are wondering how I removed the hood by myself, first of all you can see the large blanket there on the cowl. I basically put that all the way across until it bunches up against the rear edge of the hood. Then I put the my engine hoist boom up against the front of the hood near the latch. I unscrew all 6 bolts where the hinges attach the hood to the car and then lower the boom up front. Voila! No scratches and the hood is free. I can then pick up the hood from the front, grabbing both sides and then set it aside. (don't worry, I will have help when I reinstall!
Anyhow, this is what I accomplished this afternoon - the 292 has been removed and has been placed on a run stand. I am going to wire it all up, change the fluids, finish the accessory list, and hopefully fire it up tomorrow. You can see the starter hanging out loose in the Fordomatic. I just unbolted it and left it there before I removed the engine... why frustrate yourself?
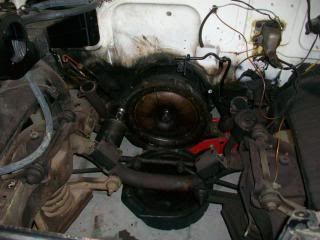
|
By Daniel Jessup - 11 Years Ago
|
thanks for the kind comments fellas... on that hood removal, here is the procedure:
1. Raise the hood.
2. Get a heavy blanket and roll/bunch it up to lay across the cowl. It should "cushion" between the rear of the head and windshield. The thicker the blanket, the better.
3. Move your engine hoist in position in front of the car and raise the boom to meet the height of the hood. I like to place the tip of the boom to the side of the latch (on a 55). Also, you may want to wrap your tip in foam if you are removing a hood and do not want to worry about scratching the underside. Do NOT raise the hood anymore. You are simply trying to meet the hood at its "resting" height.
4. Once the boom tip is in place, remove the bolts. (I like removing from rear to front on either side so you can see if the rear of the hood will tilt up - it gives you an idea if there is any "pressure" on the hood to move. If you are doing this correctly, there should be not pressure.)
5. Go back to the engine hoist and GENTLY lower the boom until it comes down enough to let the hood rest on the valance. (If you are dealing with a hood you are not repairing, etc, then cover your valance with a blanket also, and you may want to slide cardboard between the hood and the hinge arms.)
6. Slide the engine hoist out of the way, and you can pick up the hood from the front (I guess my "wing measurement" for my arms is wide enough I can do this easily) and set it aside. If you cannot do this yourself, you could always use a couple of straps evenly placed under your hood and then use the boom to remove it and take it to a table or a body work stand.
|
By Daniel Jessup - 11 Years Ago
|
Day 2 on the 55 is down, and I did not have much time today because of school supply shopping with the wife and taking her out to eat (tax free weekend in Virginia for school related items). We still have 3 kids in school. The oldest will graduate this year. Anyway, I did get the engine all buttoned up on the engine stand. In addition to installing those headers, the 54 radiator and electric fan, I also changed the oil and spun on a new filter. The run stand has an electric fan that I installed last year (operated by a toggle switch), a tray for the battery, its own gas tank, a gauge panel (I added a tachometer and a light for the ignition), and nice polyurethane wheels that I installed to replace the original casters that were too short to put the engine hoist under (go figure). The polyurethane wheels make this thing GLIDE across the concrete floor. The difference is amazing - those wheels make the load to push seem much, much lighter. The engine fired right up and sounded good, but I detected a miss - after checking all 8 spark plugs it looks like a few need to be replaced. Over the past 4 years, the engine has not been run that long, and when it has the engine never really got hot enough to burn off any deposits. The compression is still excellent. No leaks as of yet - well I take that back. The radiator cap needs to be replaced. The 54 radiator I installed has no overflow tube so the corrosion you see is the coolant leaking from there and then dribbling down the front of the radiator. I will take some time over the next few months to tune the engine and get it to where I like it for reinstallation.
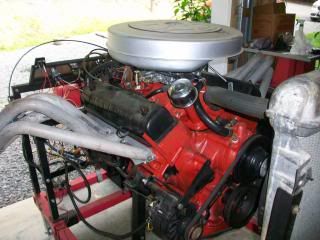
Tonight on the front end of the 55 I began removing sheet metal. I removed the radiator valance, horns, brackets, hardware, etc, and starting organizing the items I removed. I looked again all over the engine bay and have come to the conclusion that I need to get a steam cleaner to do the best job I can. I remember using Steam Jenny's when I was a teenager and I just loved those things. They cut the grease and grime like butter. I called the only place in town that rented them - $300 a day. That's no typo - $300 a day. I called a place about an hour and a half away - $145 a day. Then, when I was out with my wife I got a lead on an acquaintance of mine that has a steam cleaner I could borrow. I have not called to confirm, but the mutual friends we have said it was so. I will find out early next week - won't a steam cleaner be a big help?!? 
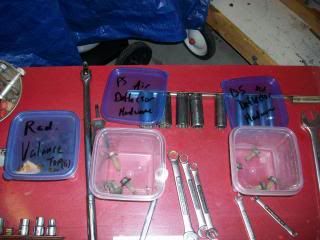
You can see in the second photo what I am doing to store all of the hardware. Instead of throwing everything into a large box, I am using those cheap $ store containers (4 for a buck) and then marking what the hardware goes to, which side, etc. I got in this habit when I rebuilt that 3 speed/overdrive unit this past Spring. I would think this will be a lifesaver (at least something to keep headaches at bay) later on when it is time for reassembly. I did have a snafu tonight - one loud "POP!" when I was at the rear of the shop. I had no idea what it was. I searched to see if something fell, something "sparked" (it almost sounded electrical), or what have you. But wouldn't you know it? When I picked up my air ratchet, I found the end had burst a hole. This air hose was one I got from china freight (harbor freight stores) several years back. It has worked well but I think the rubber is about to give way. I should probably use a whip hose. The hose that burst is attached to a retractable wheel - so I don't relish replacing it anytime soon.
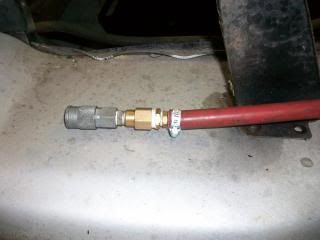
I took some time to repair the hose before I left the shop tonight. How long this hose will last... I am not sure. I have a nice GOODYEAR hose but it is a larger diameter than this one. I definitely do want to use one of those PVC hoses on this unit. During the winter months it would be like unwinding solid cable! 
Tomorrow is the Lord's Day and I will be busy. Maybe I can get back in there tomorrow night after our evening services. On Monday, I am taking the day off to travel down to Felt's Machine Shop in Suffolk, Virginia. They have a crank and a set of heads for me.
|
By Daniel Jessup - 11 Years Ago
|
On Monday I took the day off and went down to Suffolk, Virginia to visit Felt's Machine Shop. The place is a family owned and operated business that has been around for a long time. The owner, Jay Felts, knows Y blocks well. He told me his first car was a 53 Ford in which he took out the Flathead and installed a 312. Over the years, Felts has specialized in Ford engines. Anyhow, the visit down to Suffolk was to pick up a 312 crankshaft that had been ground down to 292 main size (we kept the slinger by turning the rear seal area in a lathe) and to pick up a set of ECZ-B heads they had reconditioned for me.
Behind the shop they had the best looking original 1935 Ford sedan I had ever seen in my life. The odometer read just a little over 11,000 miles and it showed. The story was that about 50 years ago this car was garaged and left to sit because Grandpa had passed away. Grandma did not want anyone driving it. She passed away 20 years ago and the family squabbled over the estate for some time until just recently when items such as this car were liquidated. The only issue with the car was that the Flathead had seized up because of the coolant corroding the interior of the block. Felt's resleeved a few cylinders I was told and they had just put the block back into the car. The condition of the car was amazing - check out that grille too.
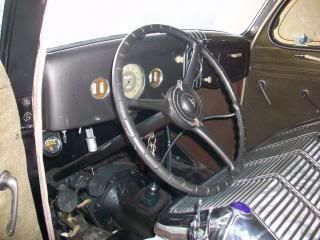
The next stop was to see a friend of mine - Wayne Francis - who lived about an hour away from Felt's. I had rebuilt a Holley 4000 for him a month ago (thanks Ted for those O-rings!) and was going to make a delivery for him and look at what he had going on as far as projects were concerned. This was the 3rd teapot I had rebuilt for him. Wayne has a nice 56 Fairlane Town Sedan, a 56 Victoria project, and another 56 Fairlane Town Sedan project that he bought for $250 after someone had CHOPPED the entire top and left it that way. He is planning to make a roadster out of it since it is so rough. The doors had real problems staying put and the center support between the doors was very wobbly. (Big 6 ft 6 take note here.) Wayne plans to weld quite a bit of sheet metal in it and make it a 2 door, 2 seater, eliminating the rear seat.
It was a full day as the machine shop is about 5 hours away from where I live so most of the time was spent on the road. But it was worth it to see Wayne, to help him out, to get those parts back from Felt's (they know Y blocks pretty well and the prices are unbelievably low - so low that I would be embarrassed to post how little I paid to have a 312 crankshaft cleaned, magnafluxed, the mains turned to 292 STD, and the rod journals cleaned up at .010 - plus keep the rear slinger. I also had those heads cleaned, magnafluxed, surfaced, new seals installed, etc, for very little money. I do recommend Felt's if you live in that part of the woods. A deceased member of the forum was the one who led me to use them a few years back.
I did not get much done, if anything at all, on the 55, but we had a good day foolin' around with Y blocks!
|
By Daniel Jessup - 11 Years Ago
|
I am taking my time with the sheet metal removal and assessment, identifying and storing hardware and doo-dads as we go along. I figured there would be some rust out, but not in this particular area as I always believed this was the car's strong suit. I was surprised by the fender splash shield (I obviously broke off the tab) and inner fender strength and condition - not much rust at all and the parts are very, very solid. All of the bolts have backed out of their nuts and hardware fairly easily, with the exception of the one of the lower bolts near the rocker panel.
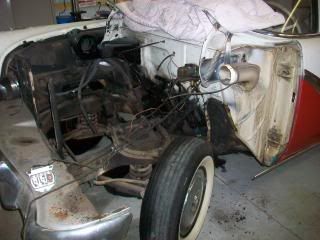
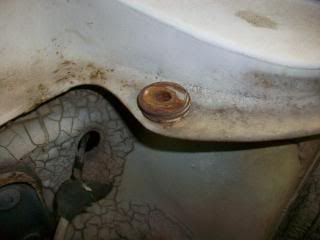 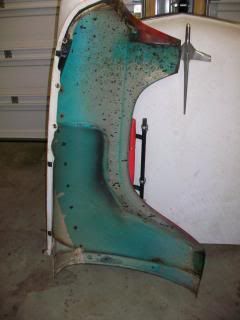
I am pretty sure that the front end sheet metal has never been off the car (but I don't know about that washer stack - read below), so the condition and minimal corrosion surprised me. The fender itself is very solid as you can see - especially around the splash shield area near the rocker panel. There is a bad spot about a foot above that - it will need attention. I think the other side has the same issue. I do not know what that is all about. You can also tell that the front lip inside the headlight housing is a little soft (the lip that attaches to the radiator deflector) - it may need some sheet metal welded in there too. So far the worst I have found is that driver's side air deflector, but the sheet metal to the left and right of the rot is very solid. I have already been banging on it with a hammer to find out how solid it is. I can cut that lip off and weld in some metal for a repair with out having to take out the whole thing, that way the measurements should be a lot easier to make and the fitment of new metal to the piece should go much easier.
If this is all the rot I find, I would be very happy and count myself blessed. However I am expecting more! 
One last item - you see the stack of washers there on the firewall mount for the fender at the rear. What is all of that about? Is that something Ford did? I will have to check the manual - it seemed like a Mickey Mouse setup.
|
By Daniel Jessup - 11 Years Ago
|
Back to the grind here... my parents came up to see my wife and I - and their grandyoungin's - and we had a great time together. I didn't get to work as much on the 55 as I had planned but spending time with mom and dad was well worth it. Besides, ol' Pops carried up a small pickup truck load of parts for me and I was pretty pleased with what I saw. It was from a Craigslist deal down in Pilot Mountain, North Carolina, and dad had agreed to bring up the whole lot for me up here to Frederick County, Virginia.
I did get the entire passenger side front end sheet metal removed. This time I had to simply remove some bolts by twisting them into two pieces but there were only two. The rest came out pretty easily. This passenger side air deflector is in excellent shape compared to the driver's side. Also, the fender lip underneath the headlight bucket is very nice. There are a couple of body work places on this fender, and I am thinking that I will have to completely remove the brace that runs the vertical length at the rear of the fender to get these repairs right, and then reinstall the brace before mounting. I had one hangup that was hard to to deal with at first - the hidden stud that goes through the body (behind the kickpanel under the dash) just spun and spun when I tried to take off the nut. There was no corrosion there so I couldn't figure out what the problem was. The stud just spun with the nut. I had to insert a long screwdriver and keep pressure under the washer as I tried to back out the nut. 5 minutes later we were ready to pull the fender and serious trouble averted. I have no idea how someone would get that fender off if that nut seized up. I don't really think you could get a grinder or cut off wheel in there. Anyone ever face that problem? 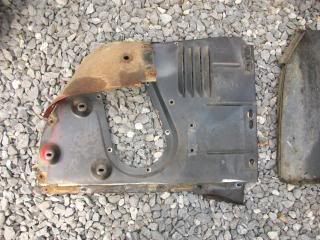
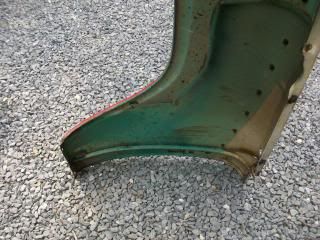 The parts were all degreased and I hit them with a pressure washer for a little while today. The splash pan is also in good condition and will clean up nicely. I will have to put some of these parts up in the rafters in the garage until I can get to things later on. The firewall and the frame is really what I want to attack first and get the car ready to place the transmission and engine back in there. There is definitely some body work to do. I am not going to be able to simply sand and paint, but I was expecting to have to work things over. It will be a learning experience for sure.
I have had some questions about why I left the bumper on the front of the clip while removing everything else. It "should" be easier to remove the bumper after all the other parts are removed. I am expecting some very rough hardware on those bumper brackets and being able to get at them from the TOP with the sheet metal out of the way looks to be a good thing to do.
A couple of questions:
1. What is involved in removing that brace that runs the vertical length of the fender?
2. Hardware - I have plans to degrease and blast the hardware per my ultrasonic cleaner and my glass bead cabinet. However, does anyone have some ideas on coating or finishing the hardware to keep it from rusting? I think the factory simply painted the heads of the bolts, but I am not going original here. If all of the hardware was one color that would not be a problem. This is a driver car for my father-in-law.
3. Thinking along the lines of hardware, has anyone made any updates to what Ford did to put all that sheet metal together back in 55? In other words, I am asking you guys that have disassembled and assembled front end sheet metal on 55/56 Fords with some frequency... was there any change you made to hardware use/location (fender washers, special fasteners, hidden nuts, welded hardware, etc)?
|
By Daniel Jessup - 7 Years Ago
|
Well, it's not a 100 percent done (speedo not hooked up, kickpanels not installed, no side view mirrors installed yet, etc) but I "slapped" things together because I promised my daughter I would take her to graduation in the Fairlane. Because of the timeline, all of the little tweaks such as carb tuning, distributor tuning, etc. were minimal at best. At least it was ready to STOP when needed (brakes bled, adjusted, checked a few times). It went out on several trips yesterday for a total of about 15 miles. Of course, as you guys know, the whole community was giving thumbs up, staring, waving, etc. Great times, and satisfying to get it back on the road. I was especially pleased with the transmission and suspension. Lowering the car with those Aerostar springs was a great idea - I only hit a bump stop once when I pulled into the driveway pretty quickly. On the road, pot holes included, all was fine. After Memorial Day I will post more but for now I thought some of you might like to see this....
Love the Y Block!
https://vimeo.com/271854558
|
By Daniel Jessup - 7 Years Ago
|
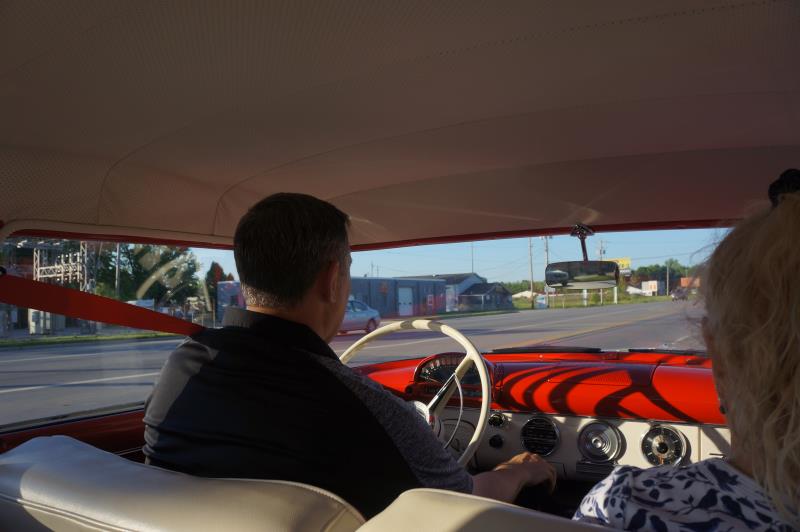 Thanks fellas! Wild times this weekend - the same graduating daughter has here 18th birthday tomorrow, and of course it is also Memorial Day weekend. Gobs of family and friends running around, a crazy schedule to keep up with, etc. I hate to say it but there has been no time to tune at all. Thankfully, right out of the gate things are running so well I can wait until the schedule lets up a bit to make some tweaks. I am grateful for so many family members involved. I am blessed. Here is a photo of my son helping me install the clock.
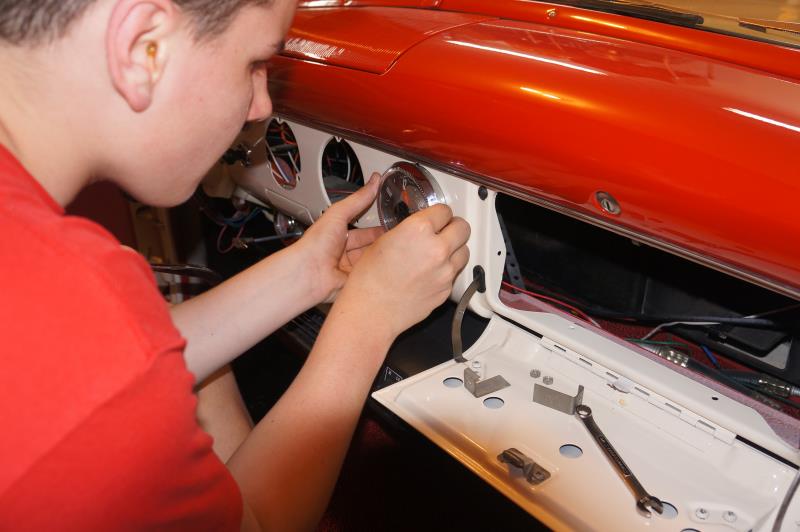 And one last photo of how the car looks at the moment...
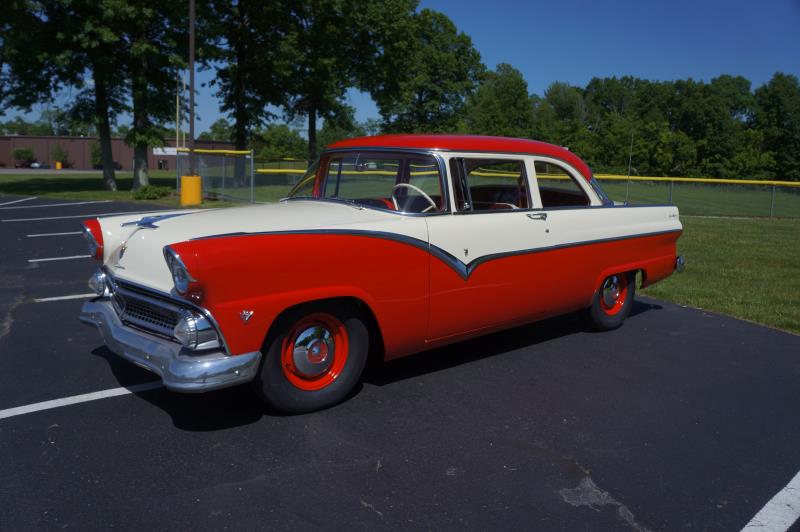
|
By Daniel Jessup - 7 Years Ago
|
Hey guys, check out this video - I thought I would add some captions, stills, and an old Ford commercial voice over.
https://vimeo.com/280181044
|
By Daniel Jessup - 7 Years Ago
|
check it out fellas! two new posts on the blog at hotrodreverend.com https://www.hotrodreverend.com/in-progress
The heater controls are back in and working nicely and the radio upgrade went very well.
|
By Daniel Jessup - 5 Years Ago
|
It has been a looooooong time since I have posted to this thread, but I cannot believe the view count...the most views in this section of the forum. At any rate - all of you that have joined since last summer may be interested to know that I began my own website last year because the videos, photos, and content was taking up so much space across a few forums that I frequent. If you like the mid-50s Fords I suggest you subrcribe here: https://www.hotrodreverend.com/blog-subscribe. The website I built is through Wix.com, a very trusted, secure, online company.
There are well over 100 blog posts with over a 1,000 pictures, videos, and diagrams. Use the information to help you out on your build or just to get a good laugh at my mistakes! There are a number of helpful tags, or keywords, that you can use to sift through information since I put the blog post into particular categories.
For instance, if you click "paint and body" on the header bar, all of these articles pop up. https://www.hotrodreverend.com/blog/categories/paint-and-body
enjoy!
|
By Daniel Jessup - 8 Years Ago
|
continuing with this transmission assembly, the next item up was to remove the small stud - it is a press fit - and then remove the large metal spring clip that keeps the pawl assembly in the adapter. Of course the actual pawl must be remove as well. Once you remove the U shaped clip from the end of the shaft, the sun gear assembly just slides right off....
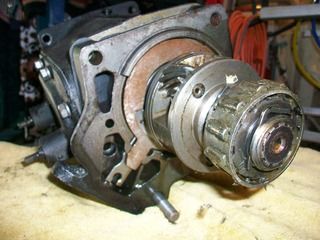
Next up is to drive out the shaft that the countershaft gears ride on. You drive it out from the front of the case here:
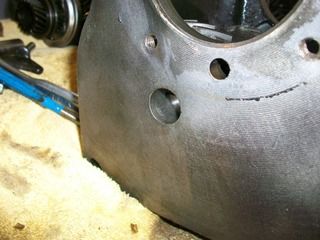
note the hole at the lower left - it is 3/4".
After the countershaft drops to the bottom of the case (and your needle bearings - keep track of those!), the rest of the gears can be removed by simply unbolting the adapters and sliding the particular assembly out. The snout will have a number of rollers inside of it - keep track of those too!
Everything but the reverse idler gear was removed.
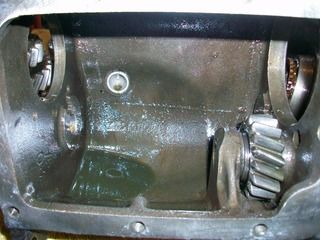
We will take some time out here and just note that for this refresh I used better gasket material than what came in the kits. It was not too difficult to cut my own and the bolt holes were punched with an old socket.
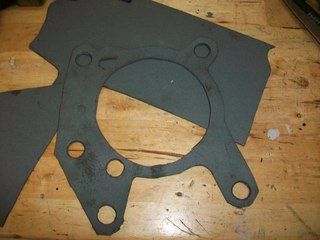
Ok, so back to the gears. The first thing I needed to do was secure a 3/4" dummy shaft of wood to use for the countershaft assembly. This was installed in the sleeve, the sleeve and dummy shaft were placed in the countershaft assembly, and both sides received the 22 needle bearings. Do not forget to put your small washers on either end!
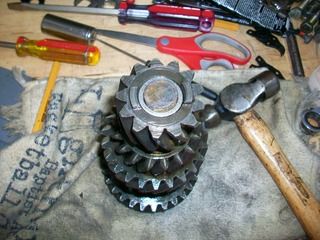
Next up was to prep the snout by putting all of the rollers back in. A "little" grease helps with this because you don't want anything falling out while you are sliding it back onto the main shaft.
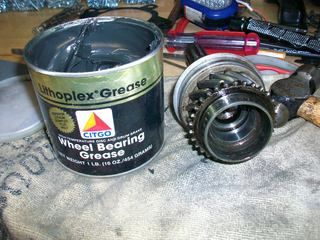
Then I checked to make sure it would slide on like normal...
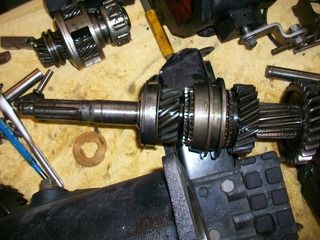
Now back to the main case. The countershaft was placed inside first, with the one large washer at the front and two large washers at the rear. For now we just let them slide into position and sit there. Later on when we raise the countershaft to meet the main shaft we will make sure the washers are lined up to pilot holes.
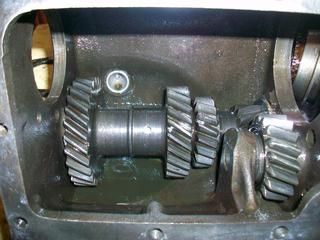
After that we fit the main shaft and adapter assembly to the main case, making sure the gasket was sealing nicely. Then the snout and its adapter (with a good gasket and sealer) were slid into position and bolted down.
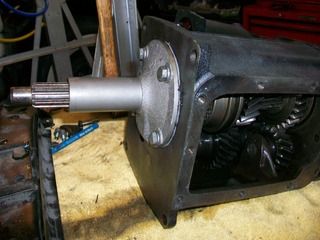
Next up we will show you why we need that dummy shaft sitting in the countershaft assembly...
|
By Daniel Jessup - 8 Years Ago
|
Next up is to raise the countershaft assembly into position, checking your dummy shaft reference to the pilot holes on either end at front and rear, and checking your washer locations. It is tight for sure but still doable. Once you are in position, you can begin tapping the metal shaft entering the main case at the rear like so.
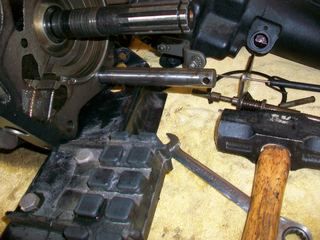
As the shaft goes into the case it will push the dummy shaft out:
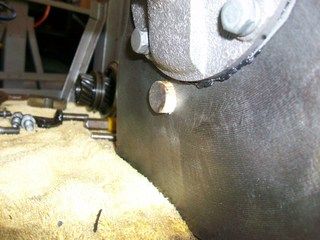
Along the way as you get ready to flush up the shaft with the case, you will want to pay attention to the rear of the shaft and the small hole seen here:
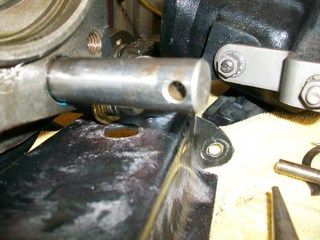
This will need to align with the pilot hole in the main case that traverses the case perpendicular to the countershaft (remember the photo from before where this pin was not flush with main case, causing a leak?). If this small hole is not lined up properly you will never get the pin to go through.
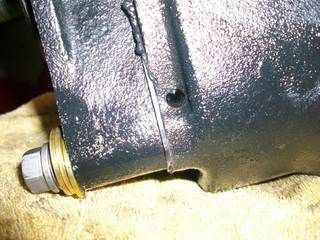
As you can see above that pilot hole for the pin traverses the length of the case from side to side so that when you full seat the axle for the countershaft you can make sure it is oriented correctly.
Fully seated and ready to go!
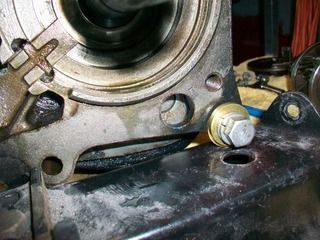
From the rear you can tell that I had to use some washers to help keep enough pressure on the adapter so that the gasket and sealer would keep things tight. Obviously this was removed when the tail housing was installed. You can tell from this picture though that the axle shaft can be seen/accessed here at the rear of the case even with the OD adapter installed.
We are almost done - I have not alluded to the main case cover that seals up the gears and orients your shifter forks but this should be pretty standard I would imagine. Just make sure that pin is driven flush, or below, the main case pilot hole.
From here I decided to put the transmission on end so that we could place the tail shaft and tail housing on without much issue. The old Black & Decker Workmate came into play here. Once the transmission was in position we went in reverse order of disassembly and installed the pawl and its mechanism and the large clip. From there we put the sun gear assembly back on with the lockout slide/stud in position too. Don't forget the U clip that keeps the assembly on the main shaft! Also, I elected to use a copious amount of bearing grease to keep all of the rollers in position. Some fellas use rubber bands to keep them in position.
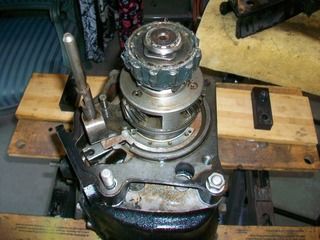
I double checked all of the work leading up to the installation of the tail shaft and housing and prepared a gasket. From there it was simply a question of how to get that large clip to expand enough for the housing to slide over the tail shaft.
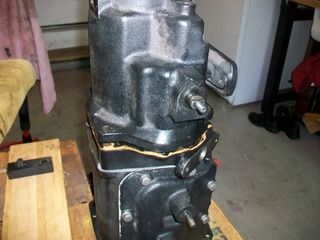
I probably should have taken a few more photos but I would imagine that good manuals show the same idea. The best thing to do is to take the tail shaft out of the housing, install on the sun gear full seated, and then take your tailhousing and slide that on the whole works. You will need to work with the large clip that is basically a keeper for the tail shaft itself. The clip can be accessed by removing a small rectangular plate on top of the housing. Spread the clip and the housing will go the rest of the way. The clip basically surrounds that main bearing on the tail shaft and is kept in a small groove on the bearing's circumference. Once that was sealed up, I reinstalled the lockout lever on the exterior of the tailhousing. While I did not refer to it, the small shaft here needs to meet up with the cutout that is on that lockout lever slide on the inside of the transmission. This is key. there is also a spring in the tailshaft that you need to make sure is oriented correctly because it is used to help with this slide. Once the lockout lever shaft was seated back into the housing, I tapped the small pin back in and attached the lever correctly.
Here she is, ready to be re-installed. And this time hopefully without leaks!
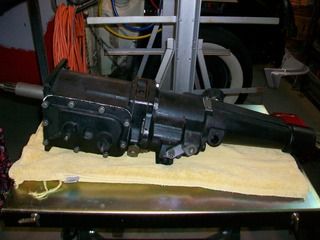
I did blast the brackets for the Hurst Mystery Shifter and painted them too.
|
By Daniel Jessup - 8 Years Ago
|
Holy Cow! What a fun time my 14 year old son and I had last night - the best example of which was when mama came into the garage and said, "What is going on in here?"
My son replied, "Ummm, Dad just almost killed himself when that bellhousing came close to falling on his head..."
Really, you can't make this stuff up! Here's the story:
With the transmission all buttoned up and ready to go, it was time to reattach the bellhousing and get the whole works in position to be reinstalled. First I removed the housing from where it sat bolted to the engine block.
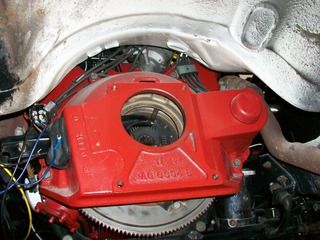
Once it was removed I briefly inspected it, making sure the fork looked good and the clutch release bearing was in place.
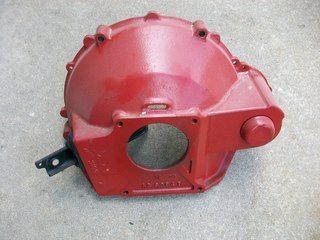
While inspecting the housing and considering the plan to hoist back up into position with the transmission, I thought of a good idea - make a couple of pins, or studs, that will help locate the bellhousing to the block when we are reinstalling everything back into the car. Here is a photo of the original 2.5" bolt (7/16, 14 threads per inch) lined up with a 3" bolt that I found in my stash. The four bolts that mate the transmission to the bell, and the four bolts that mate the bell to the engine block all have a 5/8" hex head.
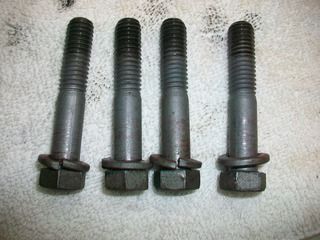 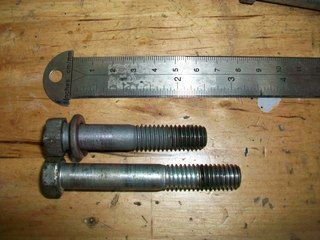
I cut the heads off of two of these bolts and then made a slot for a screwdriver.
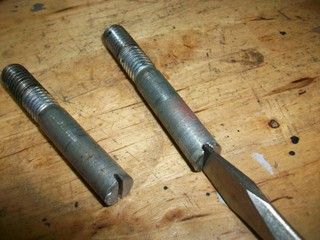
So far so good. Next was to bolt the bell to the trans while both units were resting on the workbench.
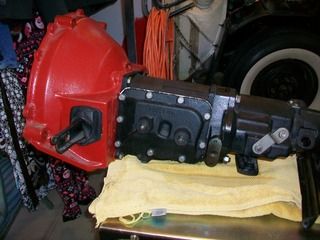
One note we will give here, I did take another look at everything before putting it down on the floor and noticed that the overdrive lockout lever was flipped the wrong way. The 90 degree was supposed to face in, not out, so we took care of that pretty quickly.
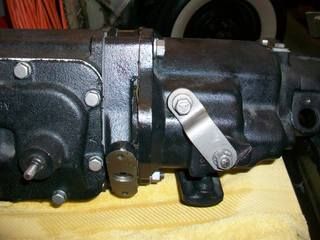
Down to the floor gently went the whole works, and the transmission was placed on sheet of thick cardboard to help it slide into position.
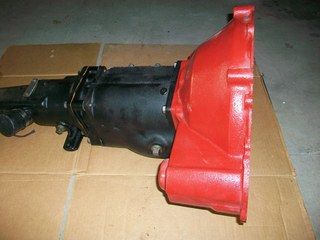
There is a crossmember towards the rear that must be cleared first, so essentially the tailhousing must be lifted up first and slid backwards in order for the bell to clear the clutch/flywheel.
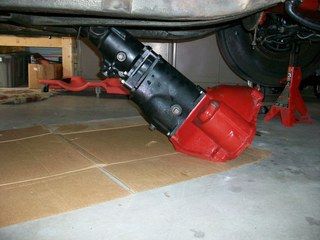
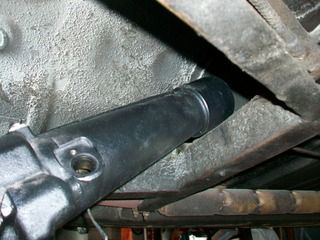
This is where it got really sticky. Tried as we might, there was no way for the bell to clear the clutch pressure plate assembly as it was jacked into position. The more I think about it now, it may just be that the replacement clutch, though working normally, is much taller (in essence thicker) than the original 55/56 parts. (Remember two things here - I had no original assembly to compare because this was a switch from an automatic to a standard, and secondly I had installed the engine and transmission as a combination when they first went in together.)
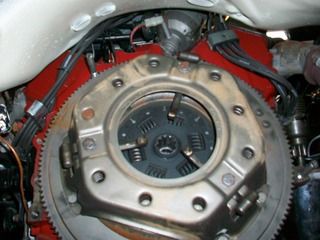
I must have spent an hour with my son just trying to figure out how to clear, make more room, etc. There was no way it was going to work. My body went through several configurations as I went into Gumby mode. Often tied up like a pretzel, placing my arms and legs for leverage/power, smearing grease all over my body, on the creeper/off the creeper, charlie horses in my left leg, my son trying to operate the jack, and me wrestling with a stubborn assembly of cast iron. It was indeed a show - we could have sold tickets! So, we did the hard thing... the assembly was pulled back out, the bellhousing was unbolted from the transmission and we made plans to lift the two into position and then bolt the two together before sliding the final assembly forward. I am not so sure that is the way it is supposed to work but here is how we did it and where the bellhousing almost took my head off:
1. The transmission was jacked up into position, slid back as far as it would go against the permanent cross member. 2. The bellhousing was lifted up into position and held there using the pins I had made earlier - since they were so long, the bell had room to slide back and forth as needed. 3. The real issue is that at first I did not use the pins, just the shallow studs on the block itself that are used to orient the bell to the block. Big mistake. As I was trying to move a spark plug wire out of the way the bell came down pretty heavily while I was on the creeper and underneath of the whole works. I saw it in time so no injury and everything is ok but good grief it was getting ridiculous at this point. I would have paid good money to have a full size car lift Saturday night! 4. The transmission was inched forward and the bell moved backwards until the holes lined up. One by one the bolts were reinstalled, clearances checked, and back onto the block. The locator pins made it a breeze really. My big issue was getting the bell to clear.
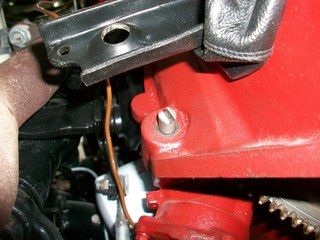
Once we were lined up, I pulled the two access grommets inside the car just below the firewall and installed the two bolts up top:
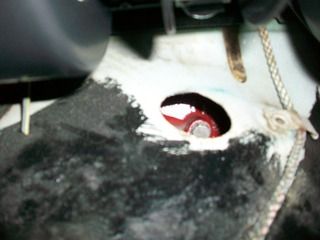
Now to get everything else where it needs to be. How I can turn a 1 hour project into 3 hours I have no idea, but I am becoming an expert!
|
By Daniel Jessup - 8 Years Ago
|
For those of you that cannot view these photos in your browse, I did find a fix for Mozilla and Google Chrome browsers. Please read this post from the HAMB...
"I found these links posted over at T.R.A.K last week by Bernard Kron. The Mozilla link worked for me. Post by Bernard Kron on Aug 27, 2017 at 4:41pm An add-on (plug-in) has been developed, originally for Chrome and now ported over to Mozilla Firefox, that re-establishes the links to all Photobucket images that have been blocked with the Photobucket "Logo of Death" (see below. So far it's available only for Firefox & Google Chrome browsers. I will update this post if it emerges for Microsoft Internet Explorer, Edge or other popular browsers. For Google Chrome users open Chrome and navigate here: github.com/kzahel/photobucket-embed-fix ; or here: chrome.google.com/webstore/detail/photobucket-embed-fix/naolkcpnnlofnnghnmfegnfnflicjjgj?hl=en For Mozilla Firefox users open Firefox (v. 48 and above) and go here: addons.mozilla.org/en-US/firefox/addon/photobucket-embedded-fix/?src=ss end quote"
|
By Daniel Jessup - 7 Years Ago
|
Fellas, It has been a long time since I have posted anything to this thread... I did want to let you know that I began my own website, www.hotrodreverend.com. Much of that was due to the issues with photobucket and not being able to have third party hosting for the media I had saved and posted on three different websites. Making my own gave me liberty and license to design what I wanted. With over 26,000 views on this forum alone, I would imagine that some of you would like to continue to follow the action on the 55 Fairlane.
Simply go to this address to view the blog: https://www.hotrodreverend.com/in-progress
and if you want to subscribe to get automatic updates to your e-mail address you can go here: https://www.hotrodreverend.com/blog-subscribe
Your personal information will be kept secure - this is a website built through Wix.com
thanks!
|
By Daniel Jessup - 7 Years Ago
|
Here are some video links if you are interested.
https://vimeo.com/263944152
https://vimeo.com/263944328
https://vimeo.com/263953373
there is a bunch more over at hotrodreverend.com
|
By Daniel Jessup - 8 Years Ago
|
I leave for Canada tomorrow, Ajax Ontario to be exact, but I did want to make one more post before "leaving the country" in the morning.
Last week I picked up this free Rack Cart - it has metal shop casters, is quite sturdy, and will be used to hold the doors once I remove them from the body. Obviously I plan to modify this unit a tick because I will need to figure out exactly how I want to mount the doors for access and stability but it looks like it should not be too difficult to figure out. Any ideas?
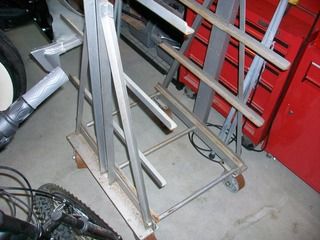
And then there was last night when I finally wired up the AC 100% (except for the compressor of course, but the wiring is there just disconnected) and turned on the evaporator unit to see what kind of volume of air I would get out of the thing. If it holds up it looks like it will turn out a good amount of air. Let me see if I can post a video.
Of course the last thing I would need would be refrigerant, R134a. I stopped by Autozone and it was $13 a can. Went to Home Depot to see what they had for courtesy light idea under the dash and wouldn't you know it but the refrigerant was on sale for $10 a can. Beyond that, the utility lights pictured rang up at $.01. That's no typo - look at the photo too, $.01 !!!
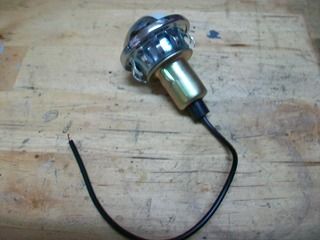
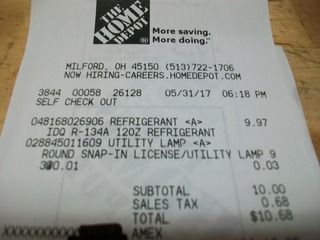
Sometimes it falls into place, other times... it don't lol. Hopefully I can fill the AC system when I return from Canada.
|
By Daniel Jessup - 8 Years Ago
|
Well what a day we had! :confused:
It all started at the post office. After being in Canada for about a week or more, we had our mail held and delivered... well we thought it was all delivered. I had to go to the post office and pick up three packages. One was a father's day present for my dad, the other was a new key/cylinder set for the 55 trunk and doors, and the other was a box of 6 cans of R134a (yep - I returned the Home Depot special - these 6 cans were much cheaper and the same brand
http://www.ebay.com/itm/282046970166?_trksid=p2057872.m2749.l2649&ssPageName=STRK%3AMEBIDX%3AIT
The guy behind the counter at the post office was having a rough day - according to the website reviews and complaints registered this fella is always having a bad day. After my request to receive the mail he slapped down a few pieces of junk mail (which we had already received paper mail so I have no idea what this was about) and the package with the key/cylinders set. He finally decides it best to go get his supervisor. 15 minutes later my other two boxes miraculously show up. Fun times.
So... we get home and it's time to fill this AC system with oil and refrigerant and... "Oil? did we get oil?" I muse to myself. Uh... and out to the parts store. So... we got the oil, we got the refrigerant, we got the can tap and we are READY.
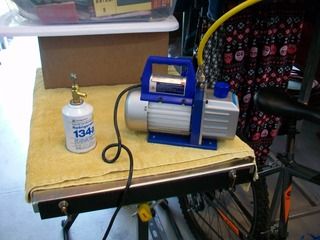
First up was to hook up the vacuum and let that run for at least 45 minutes (I actually ran it for almost an hour while getting some other things done today like some body work on the hood.) I was surprised how quiet the pump is - it never got that loud. The gauges looked good again and we were holding a good vacuum on the line without the pump (like before when we did a test run). Here is a brief video as well:
https://vimeo.com/221109056
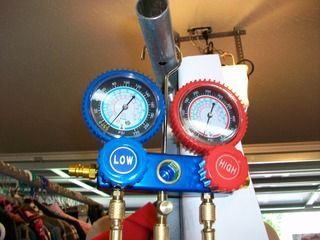
Ok so the compressor was turned about 20 revolutions to move the oil through the reed valve, and we got out a can and hooked it up. It only took about 10 seconds for me to hear a "hissssssssss........" :eek: What in tarnation? This thing was holding a good vacuum!
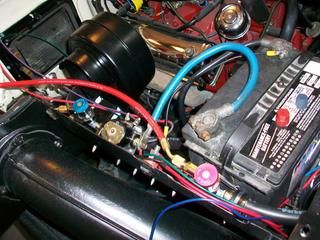
Close the valve quick and find that leak! When I found the leak I had to remove that section of line from the car and take it to the bench to re-crimp. When I got that done I reinstalled the line and fired it back up to load the refrigerant through the manifold. Hey! We got it going now - the clutch is engaging, the air is cooling, and we are on our way to...
What's that hissing sound? Yep - another leak. On the high side of course. By this time I am on my second can of R134a and I don't want to remove a section of line because of what I will lose. What can we do?
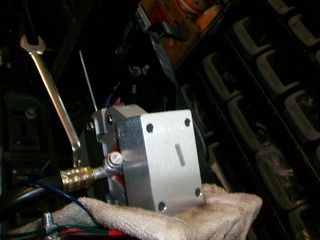
Take the crimper to the line and finagle a way to get it recrimped while still installed. Don't ask me how, but it worked and we were on our way! 
I loaded up that can and started watching my gauges as we were starting to get close. We were not quite there after can number 2 and so we tapped in to can number three. Good deal - the AC is humming along, we aren't leaking anything, no squeals or what have you and the gauges are good. Successful job I'd say, let's shut this thing down. Now to get a drink! (come back a few minutes later....)
Are you kidding me?
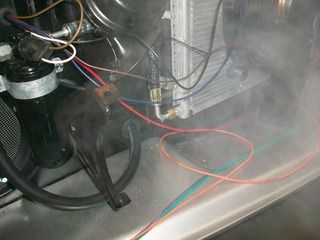
If you want to see video, click this link:
https://vimeo.com/221109039
If you are with the EPA, I have no idea where this car and garage are located. 
Obviously the high pressure (about 200 psi on the Hi side) overcame the crimp job I did on that particular fitting. So... off she came and we did a recrimp on another section of line. I cannot understand why if a vacuum held like it was supposed to why there was all this issue with leaks. Of course the vacuum goes one way and the hi pressure goes the other but this was getting ridiculous!
All is well that ends well. I feel like I wasted a lot of time correcting my own errors but there you go - Ford Follies in action. I did get the heater core lines run and another coat of primer on the hood so all was not in vain I guess. And, we do have cold air in the car!
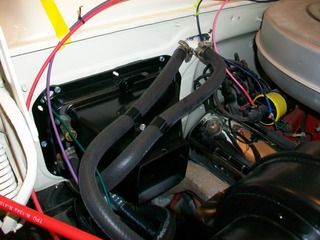
|
By Daniel Jessup - 8 Years Ago
|
Got a few things done yesterday - the best of which was a brake light switch install and test.
https://vimeo.com/221671549
Here are some details on the bracket... I used 16 gauge sheet metal reinforced a little with some welding. The switch is a generic plunger I picked up on epay.
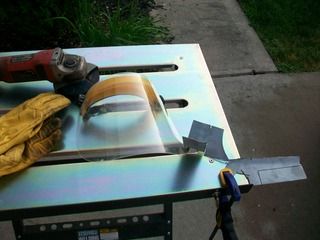
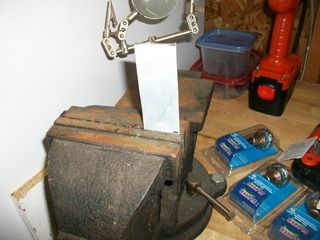
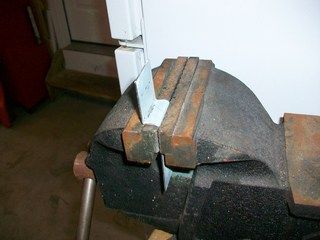
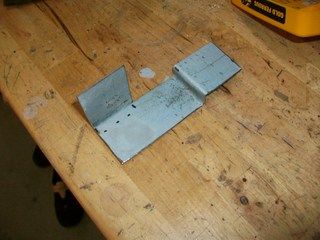
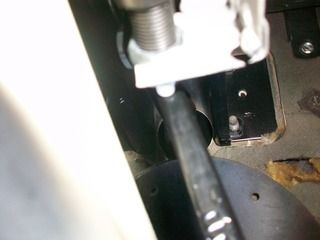
It took just a bit to fabricate, my welder was turned up too high so I blew through the first tack pretty quickly but it dialed in nicely and I added a small triangle to the return that holds the switch.
|
By Daniel Jessup - 8 Years Ago
|
I finally got around to installing the firewall cover plates that surround the steering column. This was a little more involved than I thought it would be what with the clutch rod and the seal.
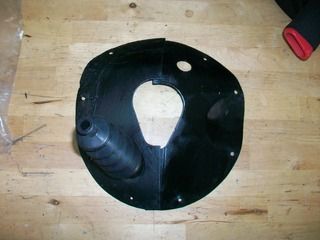
First up was to align the rubber seal to the holes on the firewall.
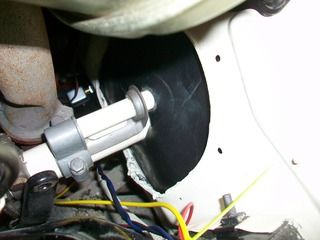
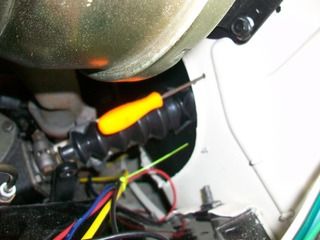
You can see I pulled the speedometer cable through just to be sure of alignment. I also used a dental pick to align the holes on the firewall to the holes in the rubber seal. Two slits were cut for the clutch rod seal to go through and we began installing the driver's side plate first. There are 9 total screws, and the two at the very top are installed from the engine bay through the firewall while the seven other screws are installed from the interior through to the engine compartment.
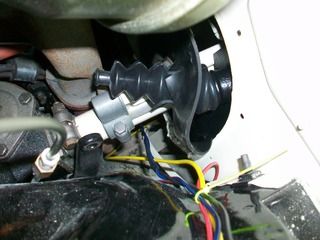
The clutch rod seal was pretty pesky. It was difficult to install on the sheet metal plate so I decided to leave it on while pushing through the seal and screwing the plate to the firewall. It obviously pulled the alignment through so I had to readjust that. After it was all aligned, I installed the screws loosely so that the plate and rubber seal could slide a little bit until both sides were installed.

this photo here shows where the light coming through the firewall helped to line up the holes in the rubber seal.
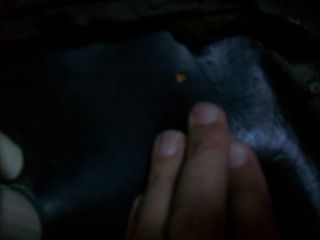
That clutch rod seal was very tight. I could not get the clutch rod through the seal without it popping off of the sheet metal plate. So... it was over to the bench to pry and tug and work the end through. After that we reinstalled the clutch rod and things were made ready to go.
|
By Daniel Jessup - 8 Years Ago
|
Disaster struck again...
While getting things together for the OD cable I happened to notice serious oil leaks at the transmission. The small seal for the solenoid was actually torn and would not hold its seal, and the the OD adapter on the case was leaking at two separate places, and the cover plate for the shifter forks was also barely seeping. :mad:
More on this later but for now let's look at the OD cable. (yep, you can tell from the photos that I pulled the shifter and brackets that attach to the transmission) These photos show me trying to make sure the lever works appropriately with the cable pull and that there is little to no play with the movement.
Overdrive engaged: well, kind of - it won't actually engage unless you are above 28 mph, but at any rate this position means that it is ready to engage.
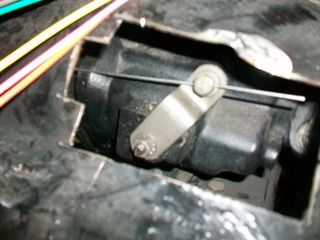
Overdrive lockout: it will not engage for anything, and for all practical purposes you only have a standard transmission with regular gearing.
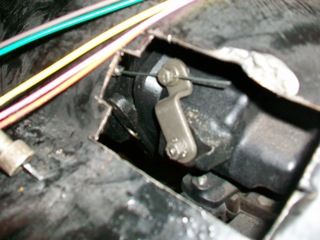
Of course at this point for me, this is all sheer conjecture because I have never driven the car while having the OD hooked up and ready to go. The standard transmission did shift just fine and worked well the summer I installed it in 2015 and moved the car around quite a bit in a very large parking lot.
Before we start looking at this transmission (again) let's take a look at this:
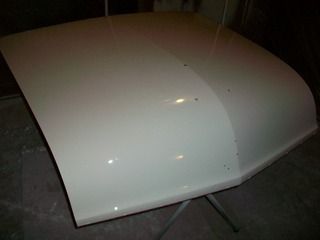
YES! Color on the hood! Can't wait to shoot some clear coat.
Ok, now on to the transmission :confused:. First I had to drain it. I filtered the old oil since it was basically unused, and I stored it in a clean jug marked appropriately:
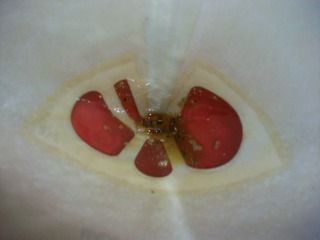
Then I got my jack, unscrewed a "few" fasteners and bolts (don't you like the one bolt/nut combo at the crossmember where the bracket for the E-brake attaches to the frame??? Aaaaaarrgghhhh!), and dropped her down gently to the floor:
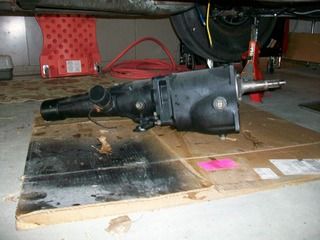
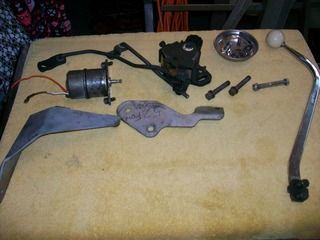
Once it was on the bench it was time to pull that pesky seal and install a new one:
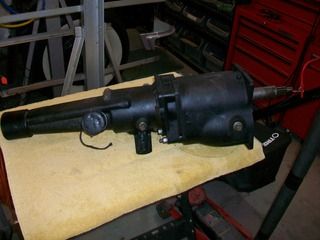
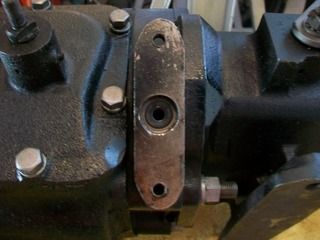
I will have to say that after wrestling with all of the hardware to remove the transmission, messing with the oil, etc, I was not looking forward to knowing that it was indeed tear down time - AGAIN. I guess this is the way you learn and in the future make sure you concentrate and do right the first time. But, the shifter brackets did need to come out because they had to be painted, the cable routing was done (pics on that later) so it was time to pull some stuff back, I wanted to trim some of that sheet metal around the shifter to ensure a good fit, blah, blah, blah. All of that still did not help my attitude. :eek:
Ok, game on! There is a job to do, so let's get to it.
|
By Daniel Jessup - 8 Years Ago
|
After I removed the cover plate that hides the shifter forks, I saw this:
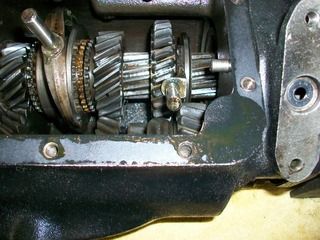
The oil was already puddling down near the lower corner and was ready to give way. At first I wondered why that was the only area showing oil on the gasket. Once I removed the gasket though I noticed that the pin that secures the countershaft in place WAS NOT DRIVEN FLUSH with the case. Therefore the cover could never fully meet the surface of the case itself and a good seal just would not happen. MISTAKE TWO in this process! The picture below shows the pin driven below flush so as not to cause further issues.
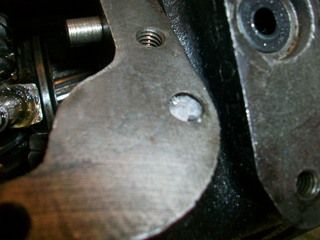
We turn our attention next to the rear of the transmission and the OD adapter case. This is held to the transmission in four places and they all have 5/8" heads - eazy breezy. However, before you fully disengage keep in mind two things.
1. There is a pin that must be removed - if you don't do this you will never get the case to separate completely. The pin is this small:
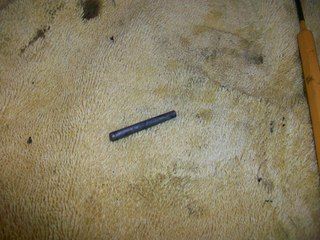
and it is placed here, driven in from the top of the casing. The picture from the bottom:
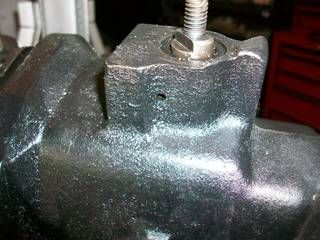
and from the top:
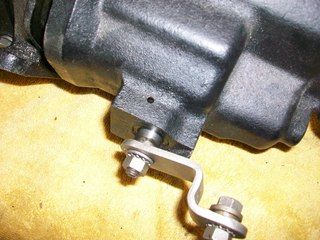
The pictures above show the boss for the lever/shaft that operates your engagement of the Sun Gear (well, provided the pawl from your solenoid engages also, but we will talk about that more later). At any rate, once the pin is removed, you need to pull the shaft out as far as it will go. (Don't worry, it won't completely fall out - it is actually inserted from inside the case.) Ok, so that is number one.
2. Once you remove the rear casing there are a number of small rollers that will drop out and you will hear them plunking all over the place. Don't lose them! You need each one and they are a specific size, etc. Look at these two photos below. One shows the small rollers on the circumference of the shaft, sitting in their bosses. The other shows how a few of the rollers have already dropped into the tailhousing.
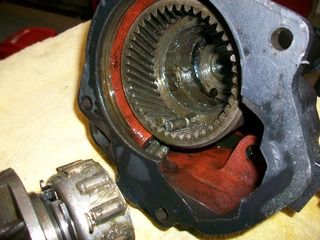
There is a large clip that keeps the rear shaft in place in the tailhousing, but we will talk more about that later - for now, just know that the clip is secure - it ain't coming out. Later on for final reassembly you will find that it is a real pest.
|
By Daniel Jessup - 8 Years Ago
|
Thought I would post some pictures of what I did to route the lines and how I situated the bulkhead fitting where the lines pass through the firewall. At this point I am not finished with the plumbing since I want to get my heater sheet metal installed first and I am not 100% sure how I want to route in the engine bay itself, I am HAPPY that I bought a number of various fittings ahead of time. This is definitely a custom install and different bends/sizes are needed all over the place - especially with that bulkhead fitting. 
First up, the receiver/drier line... used one 180 and one 90 to put this together. This install was pretty straight forward. The size 6 line goes behind the horn on the passenger side.
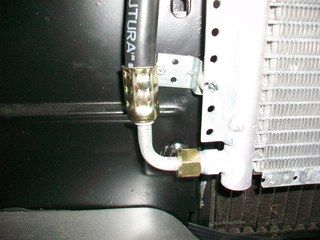
Next up was to determine where the bulkhead fitting was going to go. I decided the best place would be on the same plane with the evaporator and the fortunate thing for me was that this placed the pass through point directly below the heater duct that attaches to the firewall. If you are thinking, "Great, he is burying the fitting where he cannot reach it later on..." Just remember that the sheet metal plenum at the firewall is easily removed with the two levers on the heater core boss and the clamp that attaches the square duct.
I placed the fitting plate on the engine side of the firewall and made a mark, then used a punch to give me a locating point. Next up was a step drill to give me the first hole (size 6 fitting).
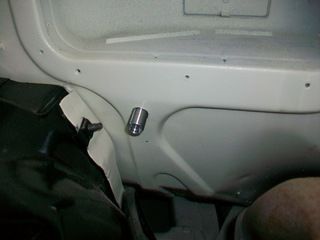
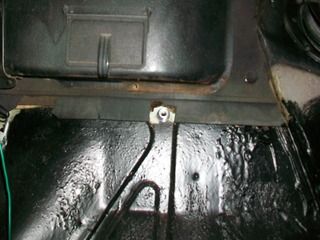
Then I attached the plate/fitting to give me a reference point for the larger hole on the bottom - this one needed a 1 1/4" hole saw. :eek:
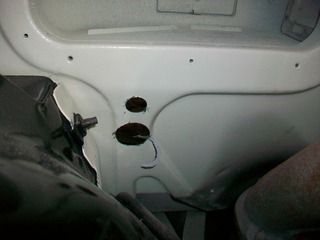
after a little clean up...
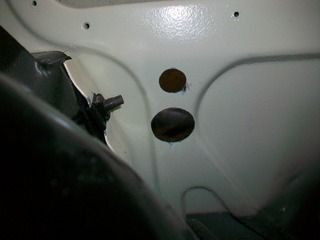
Once I checked the fitment of the bulkhead fitting I used some 3M weatherstrip sealant on the back of the plate so we wouldn't get any leaks later on.
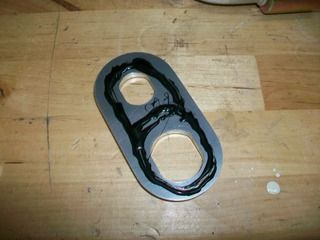
and we attached the two fittings, plate, and the nut and voila!
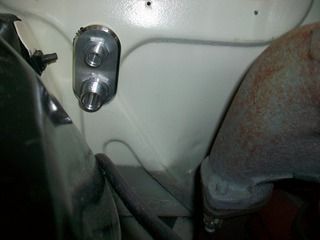
Back to the inside of the car now. I played around with various fittings - 90 degree, 45 degree, and 180 degree - to find out which orientation would work best.
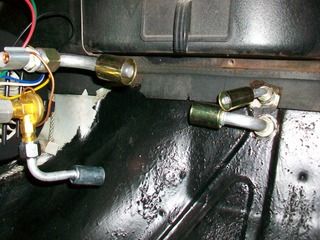
If you are paying attention you can see that the lines will criss cross as they pass through the firewall. This is "by design" - this time I actually thought about this ahead of time since I knew where we were headed with the size 6 line and the size 10 line moving up front. I also had to orient the fitting in "portrait" and not "landscape" on the firewall so this configuration worked best. It really was not a big deal. However, if you look at the photo above you will see that the size 10 fittings are just not lining up. I did have work them a little with some judicious, altered, bends so that they would line up to each other.
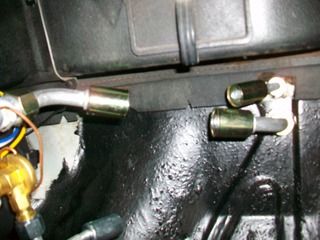
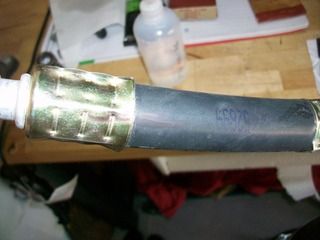
Since I was not dealing with any 180's on this evaporator hook up, the first fitting was crimped to the hose after a general measurement was taken. Then that fitting and the hose was installed. I then took the other fitting that the hose was connecting to and installed that with the hose in the final fitting "uncrimped". This made the jockeying around very easy and I just marked the fitting to the hose, pulled everything out, crimped, and reinstalled. I am not sure if that is the way it is supposed to be done but it worked for me and I am happy with the way it all went together. I am also very PLEASED I bought this Mastercool crimper. I could not imagine the multiple trips to a shop to have the ends crimped without being able to tell what I was doing. Some guys may be good enough to handle that but I am not. 
Next up was the size 6 hose for the evaporator and by this time it was getting to be standard operating procedure.
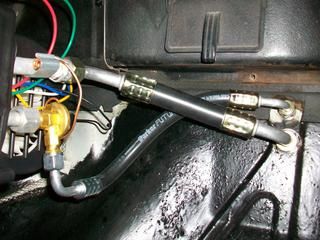
Next up is to install these parts...
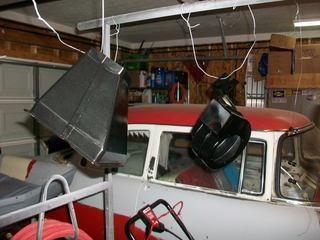
and then get the lines from the bulkhead to the compressor, condenser, and receiver/drier up front. If I can get as much installed as possible it should be easier to figure out where the ports need to go. With a rear exit compressor and the Vintage Air bracket that puts the compressor almost out of reach, I am planning to bring both the Hi and Lo ports over between the starter solenoid and the heater box somewhere.
|
By Daniel Jessup - 8 Years Ago
|
Between projects such as powerwashing the deck, repairing a water hose, hanging a window for the wife, painting hardware for the wife, and other Saturday busyness I did have a chance to get a few things done 
I installed the heater core and box since my new gaskets arrived yesterday. Even though they are Made in the USA, they leave much to be desired and are not the same thickness as the FoMoCo versions.
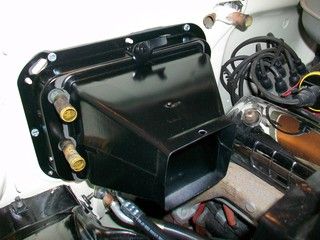
Take these three photos for instance. Notice the gap in each one as it gets a little tighter each time I adjust the levers on the Heater Core boss.
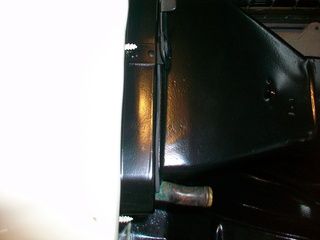
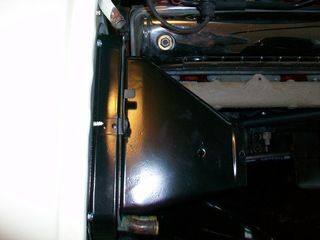
We are sealed up but I don't think these are going to last near as long as Ford's original equipment.
I decided to work on the Heater parts because the AC lines I am running are weaving in and around the units and I wanted to get an idea of where to put the Hi and Lo ports for access. I settled on the Lo port (which is a size 10 hose in this setup) to be just forward of where the squirrel cage boss sits. This should be accessible pretty easily and it is tucked out of the way.
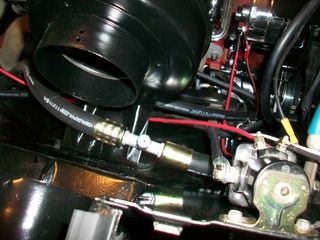
When the special AC grommets I ordered arrive, I will take some photos of how I plan to orient and install the final line from the compressor to the condenser (will also show the ports at the rear of the compressor - it is tight in there!)
|
By Daniel Jessup - 8 Years Ago
|
Some other things that got accomplished were wiring up the ignition switch so the Ford would fire and run... (nice to get that going)
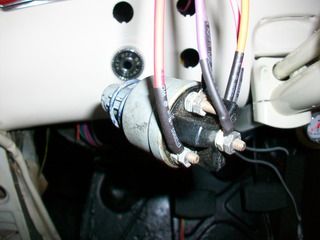
And 3 coats of clear on both of the fenders - the gloss is really looking good on these. It is almost time to purchase the clips I need for the stainless and to buff the stainless (remember how those clips just disintegrated when I pulled the stainless off the fenders last year? :confused
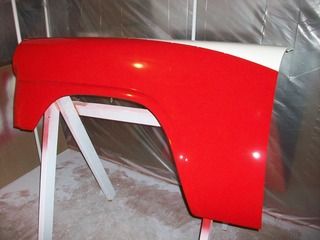
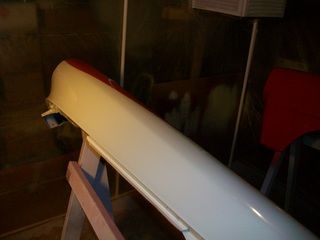
And another satisfying project to get finished was gluing down the trunk seal. I purchased what looked to almost 10 feet of the stuff shown here:
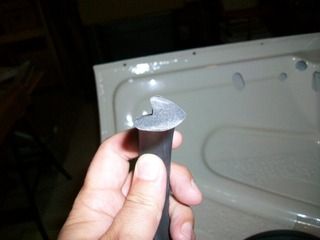
I checked and rechecked on how it should be oriented to the lip of the trunk (I would imagine this is pretty important) and I looked up some good information on the Steele Rubber website. They have pretty good instructions about installation tips and suggestions. I also picked up a tube of this handy 3M weatherstrip sealant:
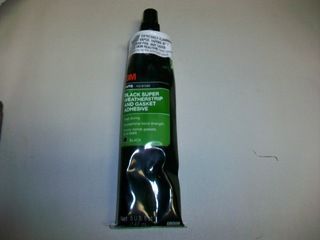
Ok, so first was take the roll out of the bag. Tried as I could, I was never able to the ends to "unroll" - they kept springing back to a "C" position like this.
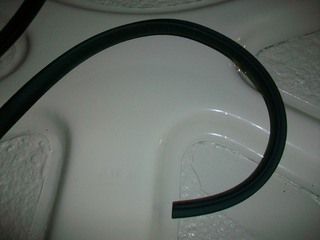
Since I had so much to begin with, I just snipped off the offending end of the seal and began with a fresh, straight end. The plan - place the seal on the lip of the trunk correctly, beginning at the point where the lock mechanism is installed. Then tape the seal to the trunk lip as it should be installed, going all the way back around to meet the beginning at the trunk lock section. The remaining length was snipped off and we grabbed the 3M sealant.
You can see the way the seal was oriented to the lip of the trunk:
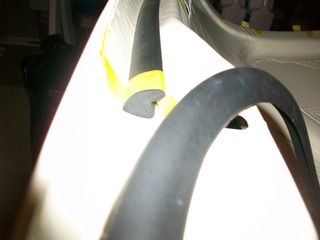
The tape kept the seal in position until I was ready to work on each section at a time.
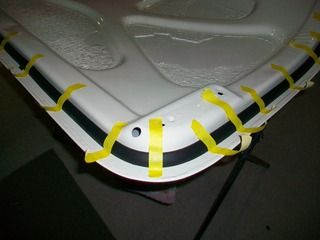
At times I needed a bit more tape...
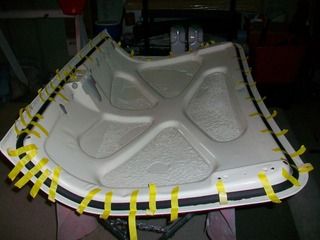
But it was worth it. The seal looks very nice around the edges and the ends met up well.
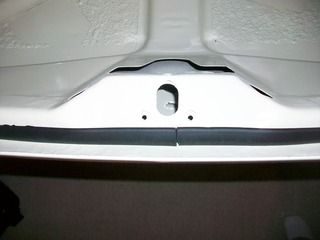
It is going to be down to almost freezing here tomorrow morning. With a day at church and cold weather besides, I am not sure how much more I am going to get done tomorrow night but you never know. There is always some project that needs to be completed on this old Ford!
|
By Daniel Jessup - 8 Years Ago
|
We are picking up my oldest daughter from her second year of college today so I thought I would post this morning to show a little progress. After checking my gauges this morning I am pretty happy with the AC install and that Mastercool Crimper Tool (more on that later).
First up was to locate the overdrive cable grommet I had purchased and to punch through the firewall where it is supposed to be located. No big deal here - pretty easy setup.
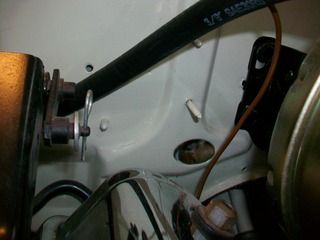
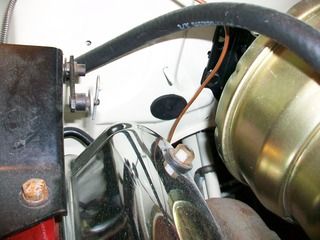
After the install you could hear me say... "Dag Blast It! Where did I place that cable and bracket?" (Update... I found the cable, well, one of the two I own, and the one I located does not have the bracket. Somewhere around here is the cable AND bracket together. Easter Egg hunt coming soon!)
Now for some drilling up front - you can see from the following holes made that wiring and plumbing for the AC has to go to the front (AC condenser fan, receiver/drier, number 8 hi pressure line for condenser). We got out the drill and appropriate size grommets. The large grommet is especially made for AC hoses and will fit sizes 6-10 through sheet metal.
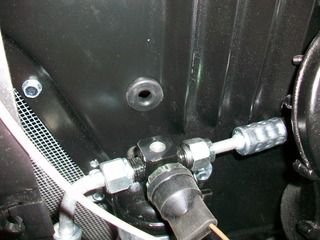
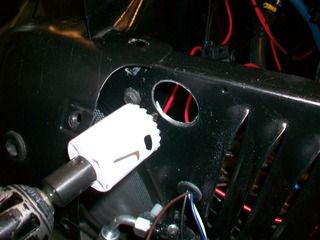
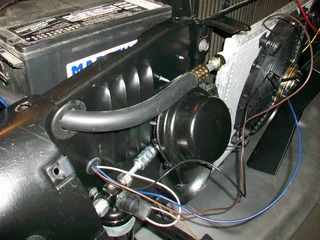
That number 8 hose was connected to the top of the condenser, put through the air deflector, and snaked around the side of the battery. Surprisingly there was plenty of room for this and with the idea of using looped brackets to hold the ported fitting in place I really think this will work.
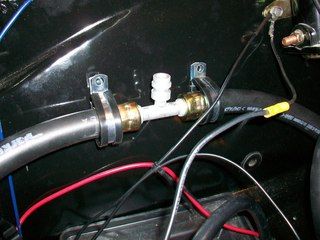
The spacing up front is extra close as you can see:
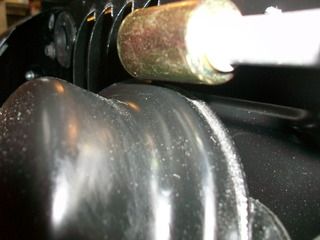
Several weeks ago I tried to get the condenser in a position where we could exit out with a 180 degree fitting and it looks like we hit the jackpot there with no interference. I am happy about that of course.
The final fitting being crimped!
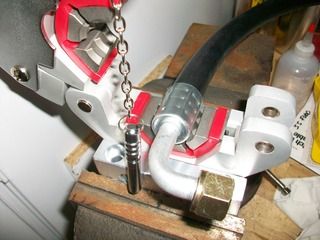
This little tool has been well worth the investment. Again, I cannot imagine having to go back and forth with a shop on trying to get all of this crimped. In a full custom job like this one where you measure 3 or 4 times, take it out, examine it, check the routing of lines so that you have no other interference, sit there and look at it with a tall glass of iced tea, (well you get the idea!) having the crimper on hand made it extremely satisfying. The ports to the rear of the compressor look like this:
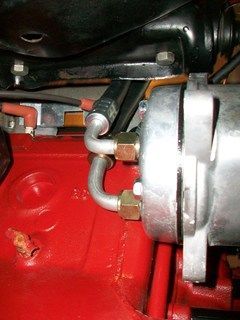
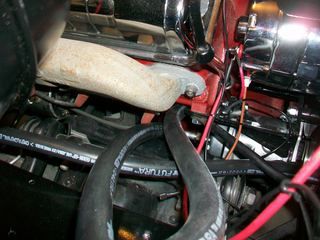
Would you believe I actually considered the 90 degree fittings exiting at the bottom instead of facing up as installed? I was a little off in thinking that would have worked but I guess it was because I had that side of the car jacked up and the lower A arm was completely extended giving so much room. I came to myself for some reason - glad I did. I cannot imagine what it would have been like to crimp it all up, drop the car and see my AC lines riding on the control arm. :eek: You can tell from the photos how tight it all is. The number 10 hose fitting is almost at the very top of the compressor and comes as close as possible to the block but there is just enough room to turn the nut.
Now for the big reveal - time to put a vacuum on this thing and see how we did on these lines! Everything was pretty straight forward. I have never dealt with AC before in my life and I am a complete novice but here we go.
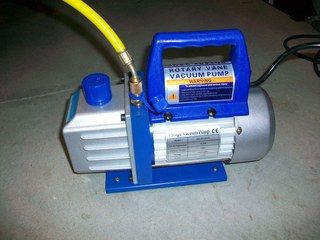
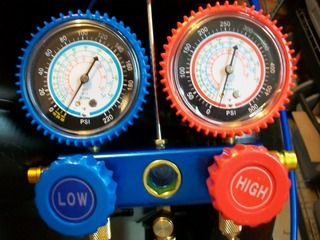
We hooked up the lines correctly, filled the new vacuum pump with oil, turned on the pump, and opened the valves and the lines at the ports. The vacuum held steady and while I did not want to do a full evacuation (30-45 minutes, but that will come later when I am ready to install refrigerant) I did want to check to see if my lines were sealed up well. After all, we have a novice here with a vise mounted crimping tool, with 16 places where we had to make a crimp to the hoses. The pump was run for about 5 minutes and then the valves were closed at the gauges to seal off the pressure from the pump but show the pressure from the AC lines in the car. I checked on the gauge about 30 minutes later - no needle movement! This morning I checked on it again. We had moved a whole 1 psi but since the temperature had dropped dramatically in the garage from last night to this morning I was not alarmed at all. I believe we are sealed up and ready to go.
|
By Daniel Jessup - 8 Years Ago
|
On with the Ford Follies! 
I was reminded again tonight how much I miss "room" in the garage and work space area. I jacked up the rear then jacked up the front all on jackstands and then found that I was off by about 1" to be able to close the garage door :mad:. So...down we came and back up again. Take a look at this photo:
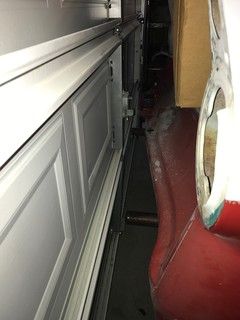
And more Ford Follies to grin at - as in the case of the mystery squeal. While testing my new alternator to make sure the excitor wire was acting correctly, checking our charge at idle, etc, I heard a ruckus coming from the front and it sounded like a pulley. Knowing the alternator was new, the AC compressor was new, and I had just installed the belts I thought, "Oh great, now what Jessup?"
Wouldn't you know it but 3 of the 4 water pump pulley bolts had backed out?!?!?
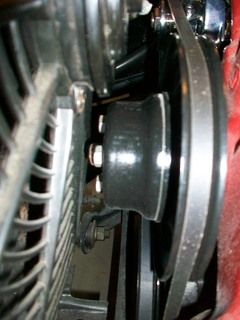
So we shut everything down, tightened up those bolts, and away we went.
I did wire up a makeshift warning light for the alternator so we could test it. Just a simple wire from the alternator excitor side of things at the terminal on the alternator case to the wire that goes back to the ignition switch. We turned the key and...
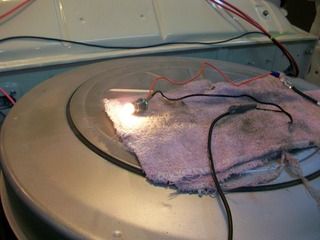
After firing up the engine and idling the light immediately went off and we took a multimeter to check voltage at the rear of the alternator and at the posts of the battery.
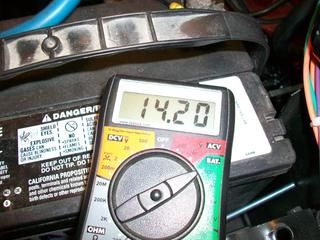
Plenty of Juice!
Now on to the Cooling Fan Relay Test. I did take some video of this one but cannot get it to upload to Photobucket quite yet. Once I do i will post again. At any rate we warmed up the engine and ran up to 190 or so on the gauge (as I recall the switch on the intake manifold is set for 195) and the fan kicked on!
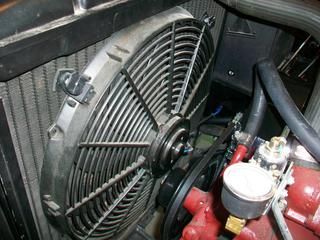
She cycled off just fine after cooling down a bit and recycled back on like it should. Pretty happy with that. I guess the relays are wired correctly at least. Speaking of relays, I also put the electric fuel pump (to fill fuel bowl or just to have as a back up) on a relay with a toggle switch to boot.
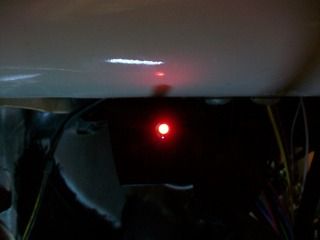
It has a red LED on the end of the switch to let you know it has power to the pump. Works like a charm. For now anyway.
Here are some shots of where some of the Relays sit and where we hot wire some of the leads off of the HOT side of the Starter Relay. (some more AC plumbing pics included too)
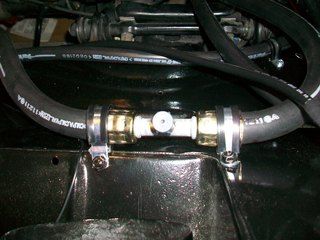
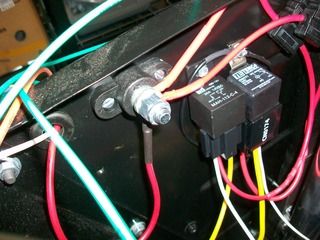
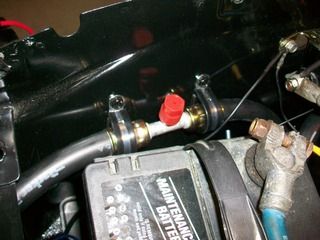
We will keep chugging along - got to get some more body work done. I did get the OD wired up on the transmission, an aftermarket relay, and the kickdown switch as well. More of that to come at a later date when we make a test run.
|
By Daniel Jessup - 8 Years Ago
|
here is a link <iframe src="https://player.vimeo.com/video/218726702" width="640" height="480" frameborder="0" webkitallowfullscreen mozallowfullscreen allowfullscreen></iframe>
|
By Daniel Jessup - 8 Years Ago
|
Lord Gaga (4/18/2017)
"Why I get involved in little projects like this, I don't know. Maybe it is the satisfaction of fabricating something small that will be entirely functional and serve a purpose, maybe it's the OCD part of me that just can't let things rest, who knows? :confused:" It's called Anal Retentive Disorder. ( Describes a person who pays such attention to detail that it becomes an obsession and may be an annoyance to others, potentially to the detriment of the anal-retentive person.) Good luck with that! Okay, Okay, laugh out loud!!! You are not the only person who has ever said that to me.
|
By Daniel Jessup - 8 Years Ago
|
Got a little more done today - we will take some time to talk about a product I really like so far: TAMCO HC 2100 Clear Coat.
Times have changed since the early 90s when I worked at a shop out in Manassas Park, Virginia. The helpful advice on this site, and others, has been invaluable. From some of you retired body men to the guys that make only an occasional post, I remain very thankful for all of the help!
My pieces don't look like professional panels but that's ok - I am satisfied with my build and getting oo's and ah's from the fellas that take a look at the work when they come by the house - they can tell I have put some quality time and effort into it. The car is going to be a daily driver and not a show car, but when I get ready to build a 60s Mustang for the wife on our 25th anniversary i will be light years ahead of the game.
A while back I was introduced to clear coat. One of the old men at our church is a retired body man, having worked in the industry for over 40 years and built over 10 cars of his own. He recommended I go that route. On another site I learned about a Euro clear labeled HC 2100. Now remember when I say all of this I am a novice - if you look up the definition of the word there is a picture of me standing there grinning ear to ear with a paint gun in my hand lol. There are probably other clears that are better than this product at $130 a gallon. Today I shot three coats of this clear on the exterior of the trunk lid. While the pictures at this point cannot do it justice, when the Tamco HC 2100 clear says it is "self-leveling" it ain't kidding.
Take this first example...
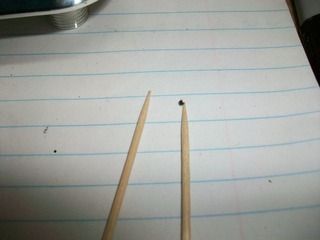
Yes, that is a bug, and yes, that is picture of the two toothpicks I used as a set of tweezers to pull said bug from my freshly clearcoated trunk!
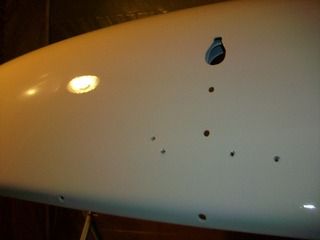
It is difficult to see in the second photo but when that bug was removed the clear coat "leveled" out. 5 minutes later and I could not tell where the bug had been. Add to that my small mistake of having a one inch run during my 3rd coat (yes, I waited 30 minutes for the previous coat to flash, just got too close on my pass). I don't know if anyone would believe it unless I had a video but THAT RUN LEVELED OUT TOO. 
Needless to say I am very happy with this clear - it almost seems like it was made for guys like me that are not that experienced, do not have a professional paint booth, and need a little "magic" from their products to get the job done. Just want to say again I am very grateful for the advice from you fellas out there who contribute your autobody knowledge. As we know, much of the work that goes into restoration includes body and paint!
|
By Daniel Jessup - 8 Years Ago
|
ian57tbird (4/26/2017)
That sounds amazing! Things have changed so much over the years. I need to learn more about the chemistry behind the paints.
These Urethanes are great stuff! If I can just keep the dust and crap out of it...I will certainly post pictures of the cut and buff on the trunk. Hopefully I can get on that soon.
|
By Daniel Jessup - 8 Years Ago
|
Look what came in today!
 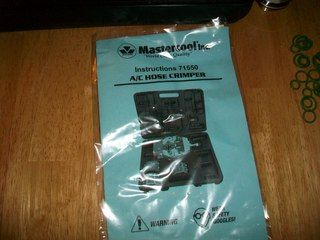
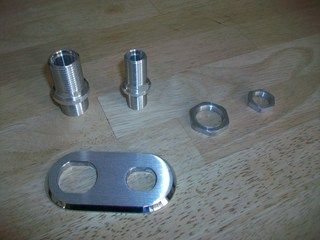
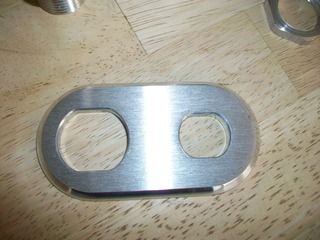
The AC kit I ordered some time ago has plenty of fittings/etc for a standard install, but this install is not going to be "standard". 
I wanted a clean pass through the firewall, hence the bulkhead fitting. Also, since I am using a Vintage Air bracket that puts the compressor extremely low. I am going to use inline service ports for the HI and LO sides. I also ordered a small plethora (is that even a phrase?) :eek: of various fittings and sizes so that I won't be locked in to the fittings from the original kit (with the bulkhead I needed fittings anyway). I like where the condenser, drier, compressor, and evaporator are all sitting. It will now be a matter of plumbing all of this up while using the original heater parts and controls.
I did plunk down some change for the Mastercool crimper. I did some research and read reviews - they all seemed to be pretty good on this unit. I will certainly let you know what we discover. When I found out how much places wanted to crimp hoses I just decided it would be good to get my own crimper. I have to make quite a few for this AC install, and of course Mama keeps talking about a late 60s Mustang she wants to have done for her 25th wedding anniversary. That car will have to have an AC unit as well. And.....that car will have to wait as well - gotta get this one done first. Anyone have a lead on a late 60's Mustang? :confused:
I will be out of town again this weekend but hopefully I can get to some of this stuff. I did make myself a little diagram so that I can follow along as to how I am installing this system. Once I get the fittings chosen and the lengths of hose all dialed in I will add that to the diagram as well.
|
By Daniel Jessup - 8 Years Ago
|
And some outdoor shots on this trunk... I got home tonight and decided to get it out, go over it with 2000 and then run the buffer real quick - still want to do one more pass but my wife came by at the end and just dropped her jaw and stood and looked at the trunk and then looked at me. :clap:
I just nodded lol!
Take a look - hopefully I can continue this trend through the build.
before cut and buff:
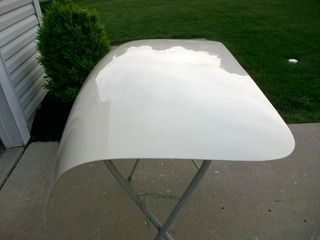
and then after:
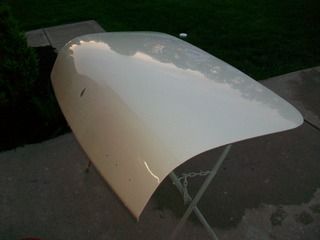
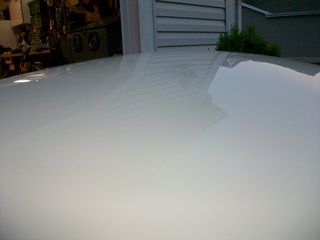
Flat out - it's awesome stuff. Take away the amateur portion of this work and the products used would really stand out.
Now where did my wife get off to? :wink:
|
By Daniel Jessup - 8 Years Ago
|
If you have been following this thread that seems to be 15 miles long , you know that I decided to plunk down some coin and purchase a crimping tool that would help me get the AC lines and fittings together. I figured it was a good idea since the wife wants me to start putting together a Mustang for her in a few years.
The tool is from a company called "Mastercool" and seems to be very well made. It is designed to be placed in a vise as you crimp your lines.
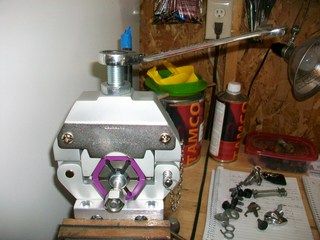
The main unit is heavy, and the tool comes with 4 different sizes of crimping inserts, 6, 8, 10, and 12. (did not need the 12 for this installation) The tool I purhased also came with a nice plastic, blo-molded case to keep the entire unit and inserts together.
Basically the idea here is that you set your fitting in the crimper, insert your hose to the end of the fitting (each one has a sight hole so that you can be sure you have inserted far enough) and then use a wrench or ratchet to cinch the ends together - the inserts crimp the fitting and hose together.

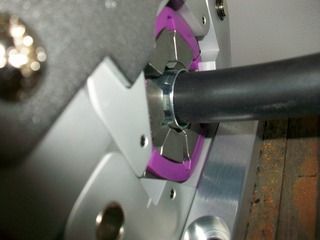
I made sure the fitting and hose were centered in the bore before I hand tightened the press, and then after doublechecking I used a 3/4" wrench to bring it all together. There is a mark located on the boss so that you know how far to go...
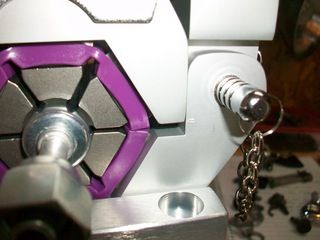
The tool works as advertised and the crimps look to be even and of course that hose is very tight in the fittings!
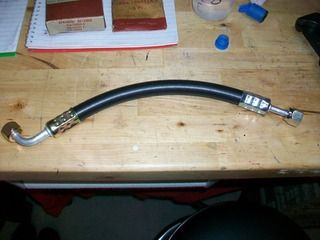
For some hoses you make you will end up with fittings that need to be oriented to a particular "clock" or angle. Of course, if one end is a straight 180 degree fitting then there is no issue. I marked my fittings and hoses by using a sharpie and making sure the fitting and hose were oriented correctly before I cinched them down.
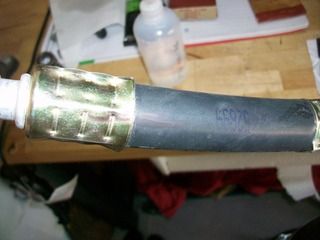
Of course, keep a little mineral oil on hand for those O-rings, and make sure you don't cut them as they go on the fittings/get connected to fittings in the car.
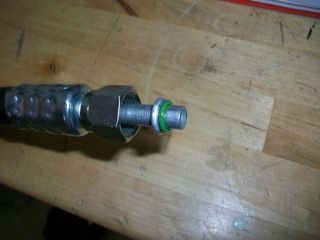
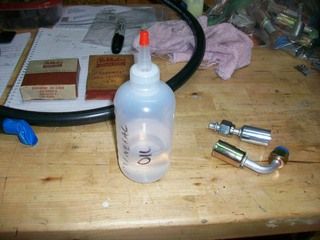
I am pretty happy with the AC kit I purchased - although the price point seemed to make it a "budget kit" the hoses shipped with the kit are obviously name brand "Parker" - a well recognized name in the industry.
|
By Daniel Jessup - 8 Years Ago
|
Thanks Charlie, I was not aware of that. I think I am going to be ok and I do like where the plug will be positioned.
|
By Daniel Jessup - 8 Years Ago
|
On with the Ford Follies! 
Last night it was time to get the wiring harness going. If the weather is nice I try to get body work and paint completed. If it's raining then on with the things we can get done in the garage.
What we have here is a RebelWire brand aftermarket harness.
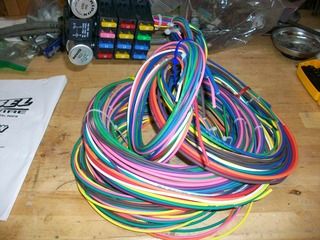
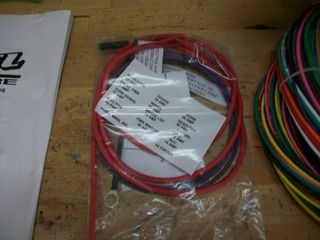
I chose RebelWire after looking at reviews, reading other forums, and checking out what they had available. I did not want to go with an original harness - too expensive and there would not be fuse panel, not enough circuits for what we are adding here, etc. RebelWire is made in the USA from what I am told, and from what I have read the customers who write on forums like this one appreciate the customer service with RebelWire in case there are any problems. Each wire is laid out with its intended use/circuit labeled every 6" along the insulation. The kit comes with the main loom and panel, is zip tied (color coordinated in that regard) per bundled use, a separate bag for the alternator and other accessories, and of course instructions. There are no terminals with the kit.
Ok so first up was to choose a location for that fuse panel. You can see in the photo below where I chose to place the panel. It seemed reasonable enough and will not be too hard to read/replace fuses when needed. The only hitch was that ALL wires exited to the right of the loom - headed straight for the main pedal bracket! (more on that later).
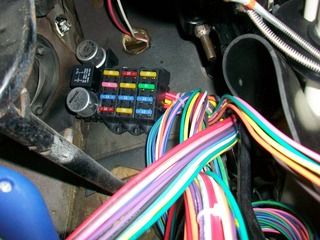
What a mess of wires coming out of that small panel!
Time to take a break and get a Ford Follies story. Take a look at this photo and guess what happened...
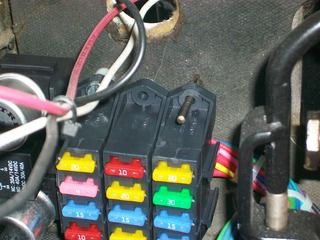
Yep, dufus me - while drilling the third hole to mount the panel to the firewall my drill bit came loose from the keyless chuck in my cordless drill! :mad: Nice. I will have to say that while I like the location of the fuse panel it was a joke with all of the contortions and octopus-like positions I had to be in to secure everything under there. A real show. Me and the 55 playing a round of "Twister" :eek: Thankfully this is not a reality TV show but I would bet people would pay money to see the unplanned goofs and what have you!
Take a look at the following photo to see how I solved the issue of the wires exiting to the right...
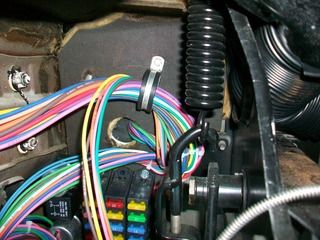
With that small piece of hardware, the wires were brought up and back to the left - especially those wires going to the ignition and headlight switches. Trust me, there was plenty of wire in there to reach to the steering wheel if needed, and the loom that ran to the steering wheel could reach the front seat easily.
So what was it like at the firewall in the engine bay? Could we use the original rubber grommet and keep things pretty clean looking?
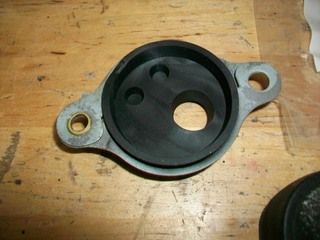
I had my doubts - there were a lot of wires coming out of there!
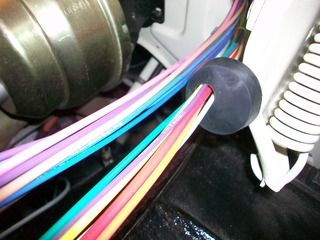
So, I started with one run of the loom and that fit pretty well. I looked at the other and noticed that there were splices to run through where the end of the run had two wires but that same line had one wire at the firewall. This.just.might.work.
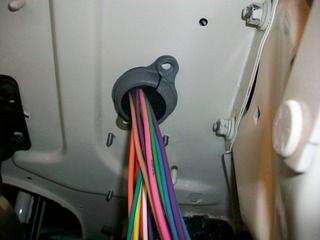
And so it did! Nice and tight too so that it held pretty easily at the firewall.
But now look at this mess!
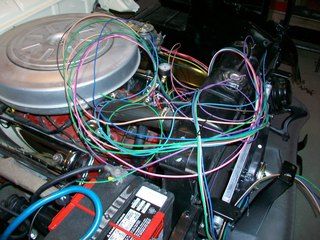
Although it looks bad I really don't think there is going to be too much problem here. The instructions read pretty well and the lines are all marked every 6".
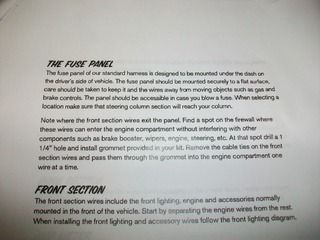
This afternoon was very nice outside so I finished removing all of the paint (and a little rust) from the hood outside, and I cleaned up the shop for some friends coming over later on this week. (Needed to put new gloves in the blast cabinet and a new lens as well)
More Ford Follies coming soon...
|
By Daniel Jessup - 8 Years Ago
|
As promised, the saga continues:
With the good weather yesterday I spent some time outside removing all of the paint (and a little rust) from the hood. I have been waiting on the trunk lid for it's next coat of primer/surfacer just so I can get the guns out and paint at the same time since prep and cleanup takes a little bit to do. I did some sandblasting where needed, used some paint stripper, and then a plastic wheel that is made for removing paint.
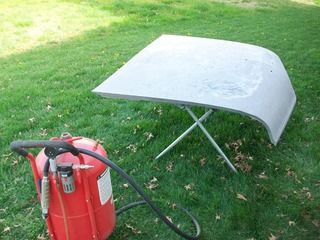
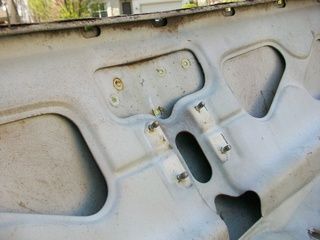
There were some small holes up under the lip, but there was not enough a problem to warrant breaking out a patch panel or what have you. The hood does has a few small dings here and there that I will have to smooth out. Some of the work I have already done with hammer and dolly - I didn't see much now but I am sure that once a guide coat goes down things will "pop up"! 
Towards evening I decided to stay in the garage. I don't know about you fellas, but the garage is like a place of peace and satisfaction to me. Nice to get in there, turn some wrenches, get a few things done, organize parts and plans, etc. My attention turned to the blast cabinet again...it was already time to replace the lens. I guess I use that thing quite regularly to blast small parts and what have you. Hardware is especially easy to save and very quick to turn around.
Would you believe I have owned this thing for 10 years and have never replaced the gloves? Check out these photos though:
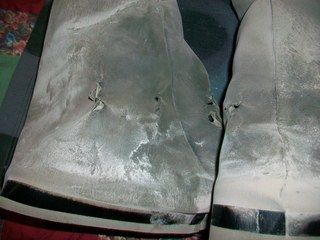
I had bought new gloves at the Carlisle, PA, swap meet a couple years ago actually (man, has it been that long since I have been out there? ) So, I quickly remembered where I had put them and replaced them without much fanfare. The SkatBlast cabinet I have is made pretty well and the accessories I got with the cabinet itself have held up well. Of course I use quite a bit, and I have gone through a lot of media and several of the replacement lens. Nothing beats tearing off the old foggy lens, removing all of the old goo from the plexiglass, giving it all a good cleaning, and then installing a new lens!
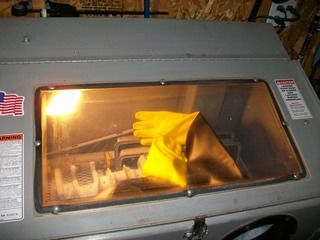
After the move from a 40x24 shop I have a new appreciation for many of us that do not have much room. I am in a 19x18 garage that holds everything - tools, the car, parts, refrigerator, kids stuff, lawn equipment, etc. That may be larger than what some of you guys on the forum may have, I don't know. But man, trying to navigate the garage with body parts, stands, tools, other parts, benches, cabinets, and the like - just trying to keep a car door open can be chore!
If any of you have space-saving tips or photos that show what you've got, let me know by all means.
|
By Daniel Jessup - 8 Years Ago
|
Didn't get too much done today, tomorrow is Easter and I spent most of the day running around with the wife and kids - including the "Crepe Cafe", antique stores, TJ Maxx, etc. How we missed Walmart I don't know! 
Looking forward to church tomorrow with all the kiddos and the wife. We are supposed to have some staff members over for Easter dinner - one of them quipped, "Will we get to see the car?" So I did a little cleanup today too.
The hood was primed, and what will probably be the final two coats of primer surfacer were shot onto the trunk. It gets better with each session. I had to hang the hood in an interesting way on my panel cart so that I could paint both sides in one session.
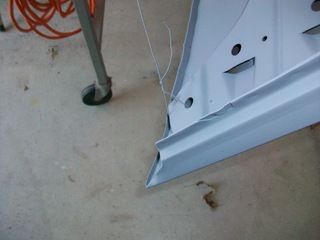
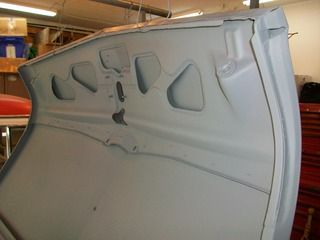
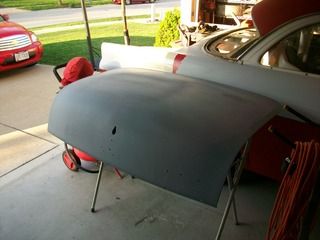
When I checked the mail today, what was this in the mailbox? 
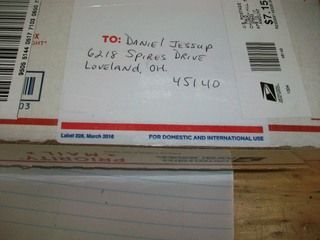
Now what can this be?
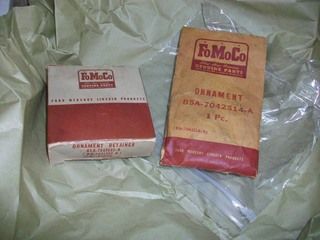
Oh yes, an NOS find! A beautiful hood crown bezel with plastic insert... very nice - check it out.
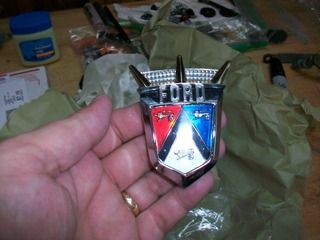
After looking at those pictures it seems like the color is off, but I assure you it is not. I guess the flash on the camera changes the color hue at different angles.
At any rate, have a Happy Easter tomorrow!
|
By Daniel Jessup - 8 Years Ago
|
Why I get involved in little projects like this, I don't know. Maybe it is the satisfaction of fabricating something small that will be entirely functional and serve a purpose, maybe it's the OCD part of me that just can't let things rest, who knows? :confused:
Take tonight's overkill for instance. Not wanting to have the heater hoses touch the alternator as they run back from both the intake manifold and the water pump caused me to come up with a simple way to make a bracket from pieces of scrap I had lying around. 1/8" flat stock and some 18 gauge sheet scrap and way we go! 
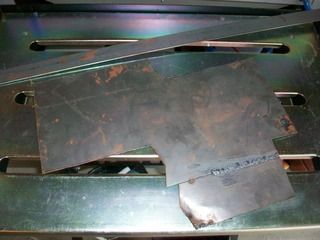
First up was to trim the flat stock:
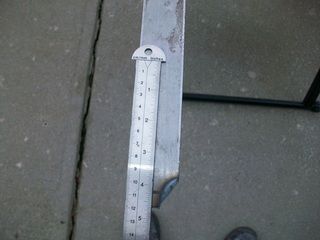
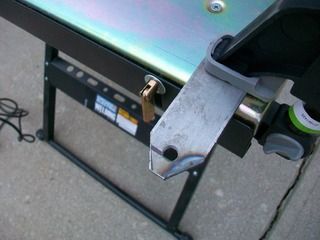
I drilled a 15/32" hole with the press, planning to make a slot that the bolt that tightens the alternator could use to keep the bracket in place. I also found a stainless bowl about the circumference of the alternator to give me the arc I wanted.
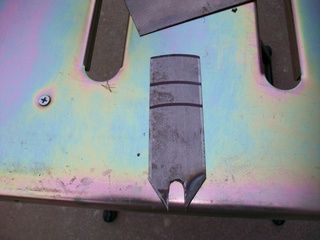
(you can tell I measured this a few times to see what angle/distance on the arc I liked best off the alternator - crazy how much changing the attachment point of the upright to the sheet metal changed the angle of attack for the heater hose bracket I was fabbing up.)
Next was to get a good rectangular shape out of that sheet metal piece that would essentially be rail for the hoses to ride on. About 6.5 by 4 or so...
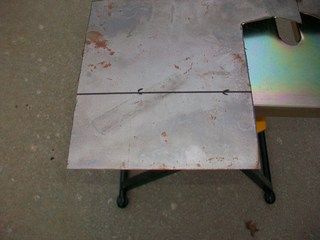
Then we judiciously fitted the sheet metal to the arc at the top of the upright (1/8" flat stock).

and got them both cleaned up and ready for welding by using a magnet to give us a 90 degree angle.
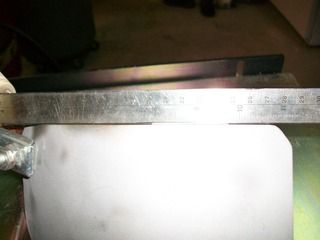
(the straight edge was used to check our distance on either side of the bracket, we didn't want to weld anything up without the two pieces being as square as we could get them.)
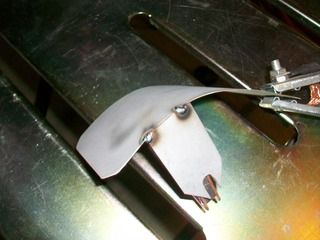
A couple of tacks and then on the backside.
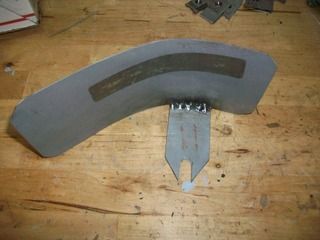
We checked our welds and we had good penetration. I decided not to go too crazy since this was sheet metal and very easy to blow through.
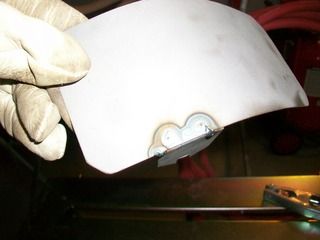
cleaned up the welds...
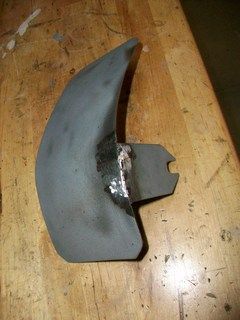
and then into the blast cabinet...
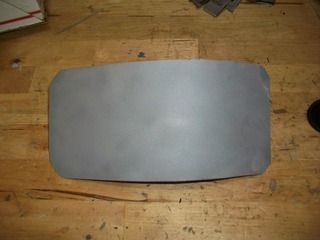
What welds? lol Not quite perfect but good enough for what we are doing here.
And here is the fitment before painting the bracket -
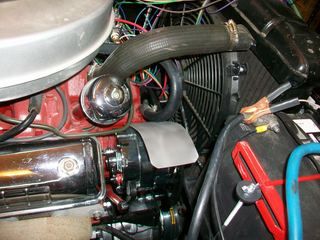
If you know the way that the stock heater hoses run, they take this exact path as they head to the inner fender on the passenger side just aft of the battery. There is a special FoMoCo bracket that keeps the hoses resting on the fender - I can only assume that this is to keep them from flopping around.
I have more photos of the trunk and the hood but it is pretty boring stuff, just block sanding, more block sanding, and a little more block sanding! Although, the trunk is about ready for color!
|
By Daniel Jessup - 8 Years Ago
|
charliemccraney (4/18/2017)
NIce work. I would find a way to attach that shield using at least 2 mounting points. The hoses will lay on it in a way that the vibration and very slight force applied could loosen the bolt. Not a bad idea. Let me see what can happen here beyond a lock washer!
|
By Daniel Jessup - 8 Years Ago
|
I have used clecos too but only in welding panels together and such...never thought about alignment, but maybe that would work. Post some pics of your progress too when you can fellas. I am not a thief but I like "borrowing" good ideas!
|
By Daniel Jessup - 8 Years Ago
|
I was hoping to have more time to get things done but life calls and the work beckons - greater things to take care of at this time of year. Recently though I did have the chance to get a couple of things done (albeit late or night or early in the morning) .
First up would be the trunk lock mechanism and chrome. It all needs to be replaced but I thought I would like see if I could not remove the keyed cylinder. The key has to be inserted and turned just so - that small pin at the back in the middle of the threads can then be pushed down and the cylinder slid out of its boss.
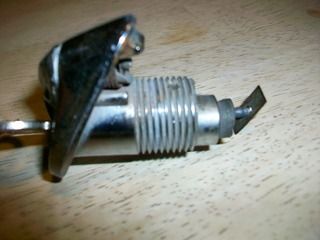
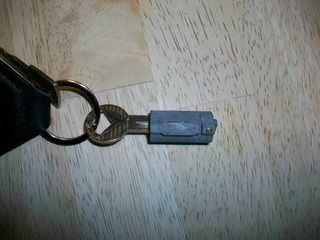
Since I was able to do that I thought I would fit the old lock cylinder into a reproduction trunk lock assembly, yeh right, it wouldn't go. Looks like the interior of the repro lock assembly is chrome too where as the original sleeve was not chromed at all.
I also removed the bezels for the windshield wiper pivots. They will have to be replaced as well - and those cheap paper gaskets too...
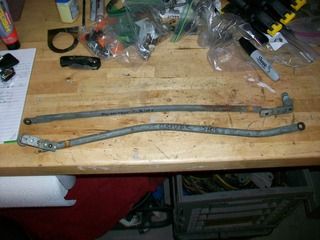
Of course, I mark everything I remove.
|
By Daniel Jessup - 8 Years Ago
|
Ever have one of those moments when what you thought you were going to do had to be changed because you really screwed up the measurements? :confused:
the best laid plans of mice and men... anyway, on with our story here. So to introduce the idea of AC, which this car never had in its lifetime... a little background. The females say the car must have AC, so ok time to get to work looking at different kits, manufacturers, pricing, reviews, etc. Vintage Air and Classic Auto Air at the top of the list of course (see previous posts about the Vintage Air brackets for AC Compressor and Alternator for the Y Block).
My thought - "Wouldn't it be great to put the round, chrome, louvered vents in the dash?" In my mind video of Jay Leno's 56 Buick came to mind when I recall watching a show years ago that told the story of how louvers were put into that dash. Knowing I have like 5 extra 55 Ford dashes that are in great shape, why not take the chance to customize one? We also wanted to keep the original controls for the heat with the matching ductwork in the engine compartment. All of these things narrowed our options, so it looked like the custom route it was. A company named "Coldmaster" down in Florida, had good reviews from Bus Companies (basically people who run greenhouses on wheels) and people posting on 4x4 websites. And... what's this? they sell a kit to put louvers in your dash!
So, I measured, measured again, looked at the specs, and I says to myself, "This will work just fine." So I ordered a custom kit that would give me an evaporator core under the dash with four exits for ductwork and louvers! 
Here's the box:
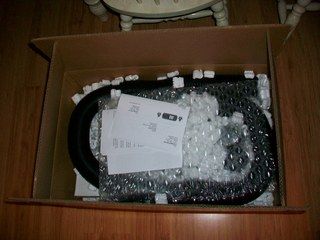
And here's my son getting in on the act as we laid out all of the parts on mama's kitchen table. :eek: Very good looking setup indeed. The kit came with full contents as listed, bagged, labeled, wrapped, protected, and secured.
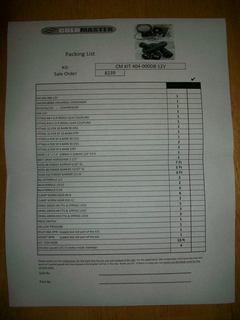
After the inventory was checked off, it was time to get to the install. First up, let's get that evaporator core in there so we can run the ductwork. By the way, this is the front face of the core...
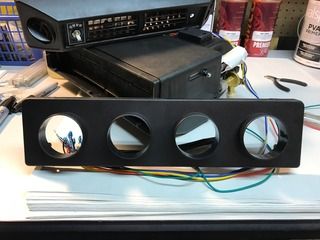
If you are looking at the photo and checking things out you can tell what's about to happen because there is regular vent face in the photo about to be installed! Yep - once I got that unit up under the dash the front plate where the ducting would begin was sticking out way too much. Seems I had not measured when the heater plenum was against the firewall...:mad:
Once that was discovered a new face plate was ordered and quickly installed.
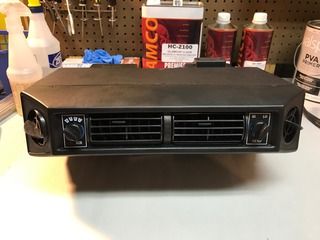
The way the evaporator core is put together gives you three attachment points to hang the unit under the dash.
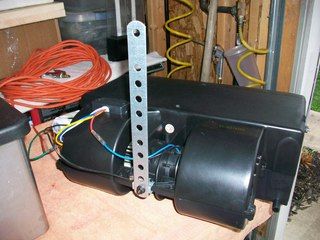
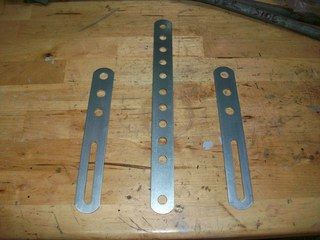
The installation went reasonably well but my main concern was that shifter. As you follow along in the photos you can see it is pretty close up in second gear but there is plenty of room to spare. I did have to use my own bracket for the rear of the unit - what was supplied was way too short, but the other two were just fine.
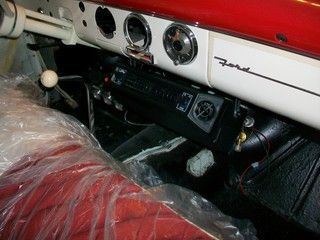

And one more final picture as it sits...
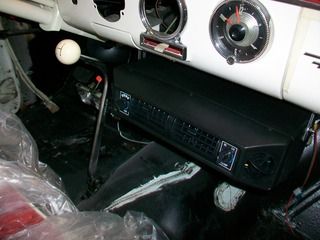
While it certainly ain't the ductwork action we were planning to do, the unit fit pretty well even though offset and it the air handlers look pretty good. More on this install coming up...
|
By Daniel Jessup - 8 Years Ago
|
Now that the evaporator core is hung, we will move on to the excitement in the engine bay. Vintage Air and their compressor/alternator bracketry that was expensive enough to be gold plated is up next. Very nice kit, bullet proof metal plate that will stop bullets and IED's ... I painted them with high heat engine paint and away we went.
First a couple of photos of the formerly used setup on the alternator -
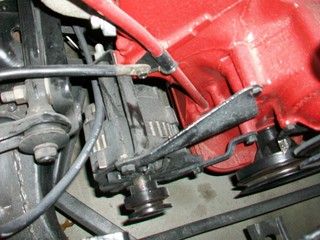
The plan is to add one crankshaft pulley before installing the bracketry though, so thankfully when I laid out the brackets and instructions I had an extra crankshaft dampener to help me mock things up.
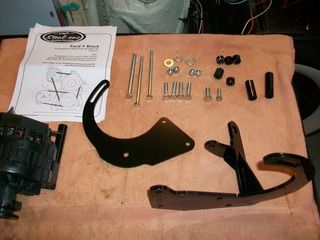
There was going to be interference if I was to use the old crank washer. Check this out:
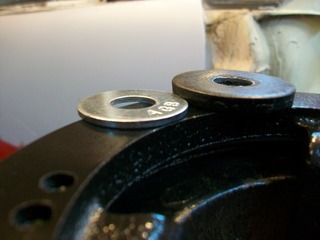
That shiny washer was just the ticket.
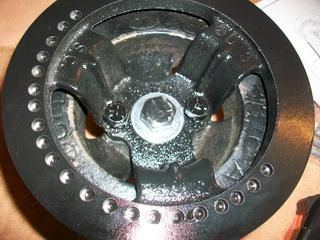
I was glad I had an extra crank dampener to use on the bench! Ok, so we got the pulley installed, and things are looking good so far.
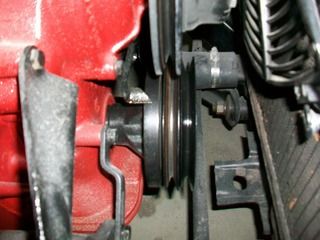
According to the Vintage Air instructions, this will be the pulley that drives the compressor, so let's hope the alignment is ok with the bracketry and with the Sanden compressor from the kit I purchased.
From here we will just say that the kit from Vintage Air includes quite a few spacers such as what is shown in these pictures:
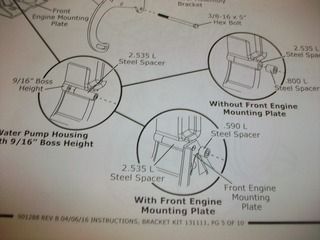
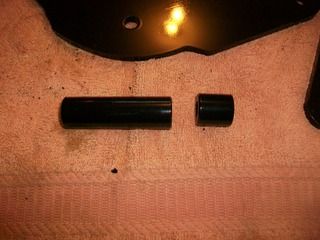
With the variance in Y block timing covers, several different spacers are included in the Vintage Air kit so you can get things lined up. After you remove the original generator bracketry or other custom bracketry, you are really just going to use the hole under the passenger head, the two holes on the timing cover that seal one of the coolant passages, and then one hole on the lower side of the timing cover. The hole in question is towards the middle and upper portion of this photo:
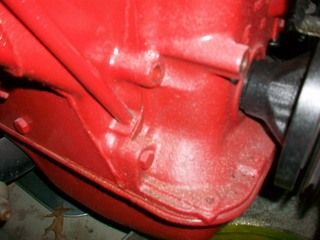
The original hole used for the tightening arm for the generator mount is not used.
The first bracket to install is the one that bolts to the timing cover AND the original boss on the head. The instructions pictured above indicate the spacers needed according to your timing cover variance.
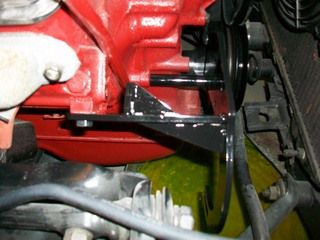
After that I installed the flat plate that mounts a 10SI or 12SI alternator.
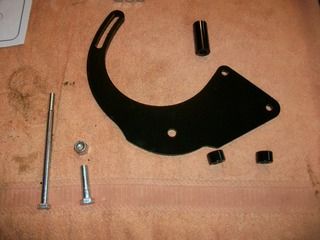
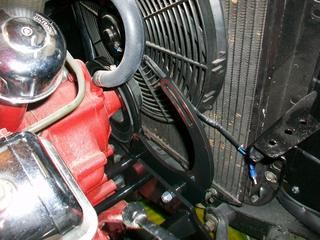
Of course, don't forget the spacers. And of course you will want to use thread sealant on that one hole for the timing cover that is open to the coolant passage.
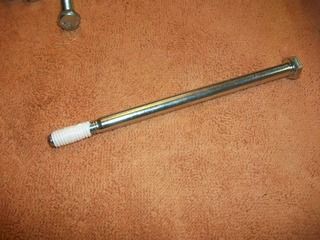
more coming up...the picture count is getting high
|
By Daniel Jessup - 8 Years Ago
|
Since I do not have the correct alternator, I could only install the compressor today. Vintage Air has a good reminder here about the oil cap and making sure your compressor is oriented correctly.
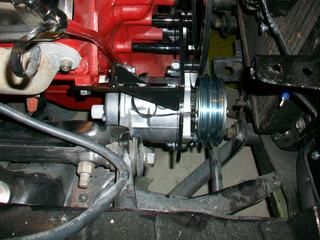
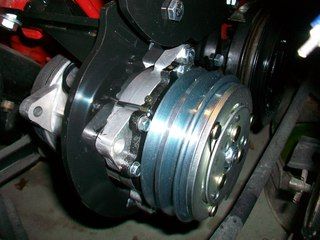
The compressor installation was pretty quick. Keep in mind that with the location of the compressor and the way these brackets are made, you are going to have to use a rear exit compressor as shown. (it's going to be tight enough as it is.)
Next up was the condenser. Hey, check this out, it doesn't fit lol!
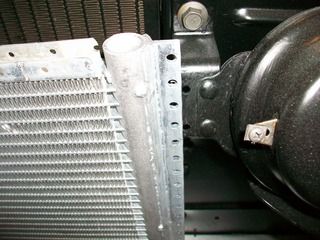
Yep, the overall size of the condenser is great - lots of square area to cool the refrigerant down. But the horn brackets get in the way of mounting it near the radiator. So, we broke out the Dremel tool.
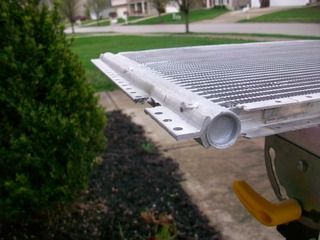
After notching the frame of the condenser, I fabricated/salvaged a couple of mounts that worked great but we still had a problem - we needed room to make sure we could tighten the fittings to the condenser. A couple of spacers helped with that issue. Using a few self-tapping hex head screws the condenser was put into place.
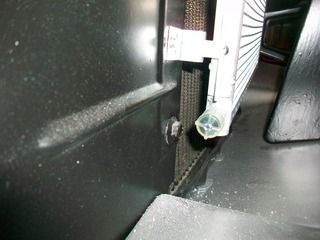
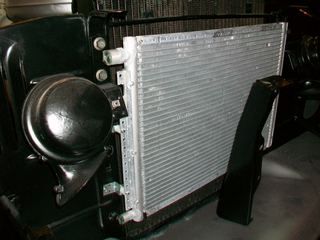
You can tell that installed the upright support that fits between the gravel pan and the hood latch panel. I thought that important to do since the electric fan was coming next.
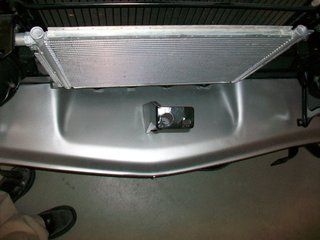
plenty of room...
So the fan went on next
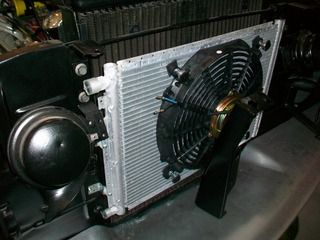
The receiver-dryer came next and it proved to be a little difficult to find a place where it would be 1. not exposed to excessive heat, 2. installed upright, 3. good port access to the condenser/evaporator core, 4. not in the way of anything else. I really think that what I came up with is about the only place it would have gone. However, if I put it inside the engine bay maybe there would have been more options? At any rate, here are some photos:
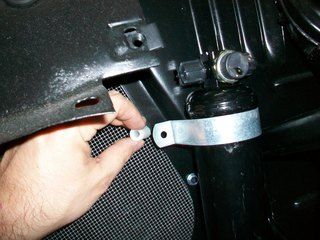
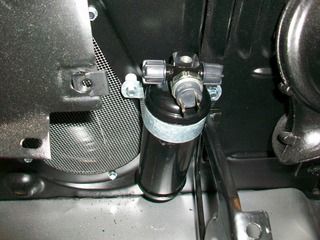
As you can see, another spacer was needed. But, everything is now installed and the AC lines and wiring are all that needs to be put into place before we charge it up! :p
|
By Daniel Jessup - 8 Years Ago
|
Well, well, well... another story to tell about the new alternator and AC compressor mount that involves a lot of receipts, conversations at a parts counter, and chasing a scrap of part-numbered scrap of paper through a parking lot! :confused: Buckle up, time for the Ford Follies...
Where do we start? Let's start with the front porch - after being out of town for a few days working with scores of people at a church hundreds of miles away I was looking forward to getting back into the garage to unwind and "rest" as it were. Thankfully, the new alternator had arrived, along with some other goodies, so in the afternoon we were all set to get a few things done.
If you are working through a restoration for a car that will be as about as original as possible, usually things fit - FoMoCo saw to that years ago. For those types of cars and trucks it is just a matter of finding the right parts, or even period pieces, getting a hold of a good shop manual or Ford parts book with diagrams and away you go. If you are doing a restomod that will be a daily driver, then well, good luck. :o You guys that are experts know full well you have to plan, measure, research, plan some more, use some of your own sketches, think things through, etc.
Ok, after thinking, "Yeh - it's a Vintage Air bracket, it cost quite a bit of money, they are bound to think through how this all fits together..." I went ahead and pulled the 10SI alternator out of the box. It looked pretty good since I went the chromed route and 120 amps no less. A 10SI or a 12SI is what the bracket calls for... so down we go.
"Wait, what's this?"
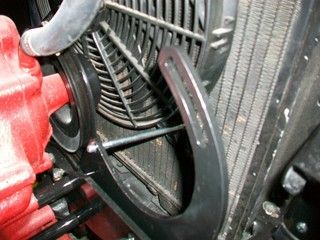
Yep - that long bolt cannot go into that hole in the bracket because it cannot clear the electric fan/radiator (that Vintage Air recommends... ). Ok so now what? Time to loosen up the bracket and slide that bolt ever so gingerly into the hole, twist the alternator just so, get that rinky dink 1/2" spacer into position and... and... wait a sec... there! she's in!
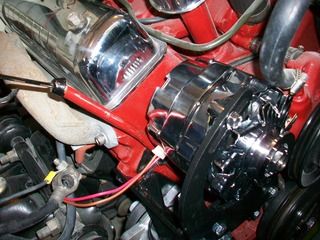
Looks good. Never knew there would be so much drama over getting an alternator into position. I purchased one that had the 2 wire socket at the 3 o'clock position, thinking that we would be ok on that side and thankfully it fits like it should - the position of that main battery hook up is close though!
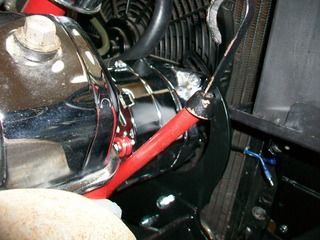
If you know Y blocks, by now you can probably tell that the dipstick tube is backwards. In other words, the main bend is oriented towards the passenger side when it should be towards the driver's side. I am glad I did this. I really don't know how the alternator could have fit into position if the dipstick tube was in the stock position. Maybe a 12SI is smaller?
Back to our story.....
Now it was time to get some belts! Vintage Air had some suggested measurements in there instructions, but they did not seem to match what I was coming up with on the Y block. The instructions did say something about variances with pulleys and all of that so I decided it was time to take things into my own hands.
I took some wire, placed it around the pulleys, twisted it together, and then cut it so I could measure it on the bench, adding a little bit of length to make up any difference in pulley groove depth.
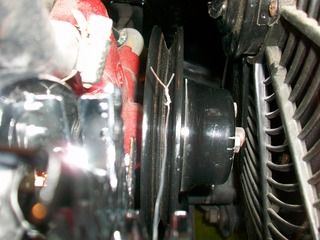
What happens next is an exercise in futility. I ended up going through these pictured belts lol...
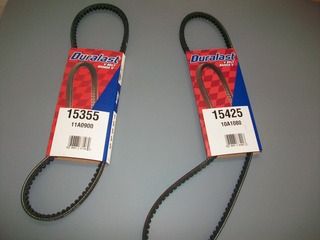
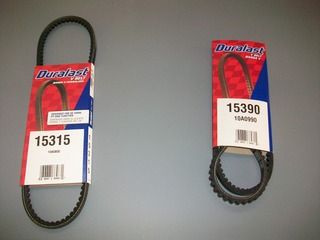
Let's just say I am glad that Autozone is literally 1.5 miles away from my house! What a fun time all of that was. You should have heard the wife when she found out I was going for the third time...:eek: "Are you kidding me? You gotta go back again? That don't sound like you at all, you usually nail this stuff..." Oh my, if she only knew! 
One of the best parts was on my second trip the piece of paper with measurements and part numbers went flying out of my grip and across the entire parking lot. I waddled around trying to step on it, chasing it down. That was completely hysterical. I probably looked like I was chasing a $100 bill!
Ok so, third time's a charm - these grooves look to be lined up really good, and the belts fit very nicely with good tension.
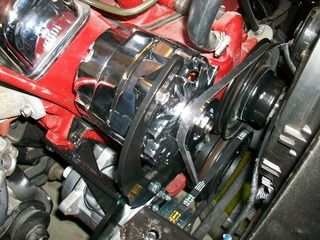
After assessing this alternator install a little bit however, I realized that the heater hose from the water pump is going to rest right smack dab on top of that alternator as it swings back to the heater core. Nope, can't have that.
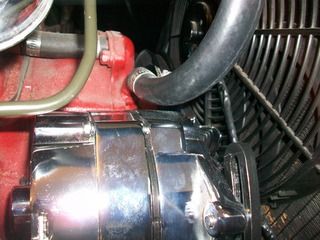
What I plan to do is make a sheet metal bracket that will come off of the alternator, placing both the hose from the water pump and the hose from the intake manifold above the alternator a bit more as they travel back to this spot on the passenger side fender -
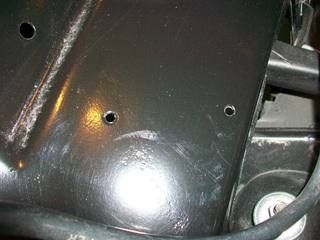
And, after reinstalling the aftermarket battery tray what have we hear?
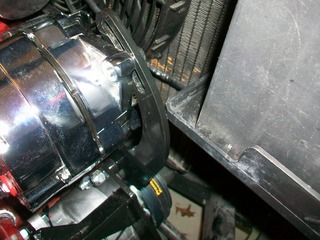
Looks like this tray barely rests against the Vintage Air bracket. It is a plastic tray, not a big deal, but I do wonder if I should not notch it or find something else. I would imagine that over time with any engine movement it will wear into the tray.
If you want more Ford Follies, stay tuned. I happened to start looking at the RebelWire wiring harness tonight. Oh boy, we are in for some fun!
|
By Daniel Jessup - 9 Years Ago
|
Merry Christmas! Everybody in the family "wound down" tonight after eating a second time and playing a few games together, having a Gingerbread House contest, etc so I said, "off to the garage" to install a Christmas present.
Almost 20 years ago my wife bought me an entry level, though very nice, Craftsman tool box combo for Christmas. For years I had been looking for a way to add a riser, or at least something in the middle and finally this year my wife pulled the trigger on this middle chest with drawers. Sears was running that Black Friday, free shipping, deep discount special back in November so I decided to take a shot to see if a newer model would work/fit on what I had kept all these years. Here are some photos of the install...
First I removed the top chest unit with the two bolts that hold it to the lower cabinet and then I removed the one large drawer in the lower cabinet. The new middle chest was put into position to check the hole alignment and position so its lower drawer was also removed. The size and dimensions were perfect - roughly 12 inches deep by 26 inches wide. The holes were way off and so I just marked new locations and drilled away.
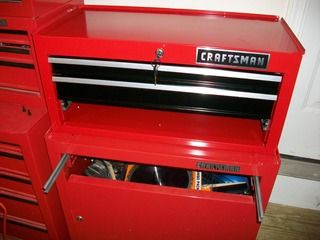
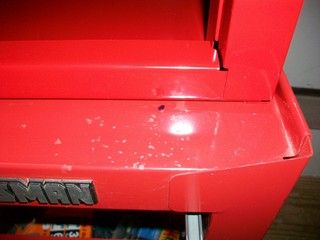
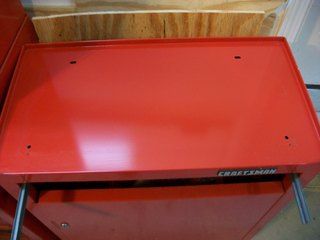
The original slotted holes were in the rear of the cabinet, but the new holes had to placed at the front. Easy breezy and to top it off I used nuts with serrated faces so that one wrench was all that was required to tighten it down.
I thought this was pretty telling...
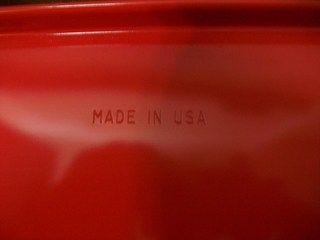
I don't know where the new unit was made but of course the old tool chest/cabinet combo was purchased years ago. A good number of people are saying that the Craftsman tool boxes are now being made overseas...
Next came the mount of the old chest on top of the new middle chest to check the alignment for holes... way off lol.
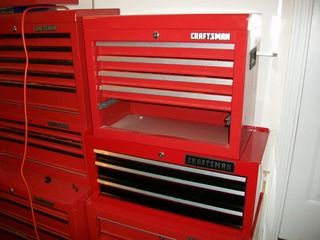
New holes had to be drilled after measuring. This process was a little more tricky because the original chest had nut inserts so there was not much room for error. Also, lining this up would be problematic because of the location at the back of the chest and I really did not want to remove so many items from the wall to get it out to roll. So... we measured twice, drilled once, and then got out a portable LED to see exactly where the holes were lining up.
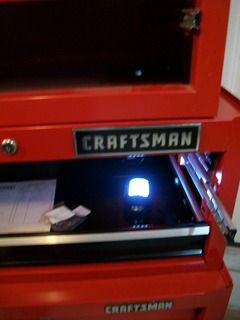
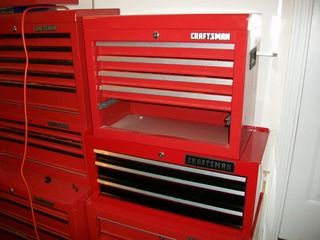
Thankfully that worked well and with very little fanfare the new unit has been installed. Obviously the drawer colors are black, but so be it. At the ultra low cost of the new chest who cares?
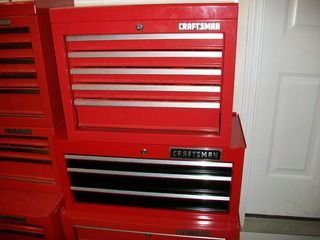
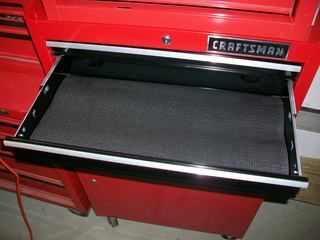
Took a few minutes to trim some tool mat and then it was time to reorganize my stuffed drawers and put the new space to good use. The unit on the left houses most of my mechanic tools, the one on the right holds most of my woodworking tools.
Anyone else get that deal from Sears for Christmas? I was thankful that a "retro-fit" went pretty well with what I have.
|
By Daniel Jessup - 9 Years Ago
|
Check out this clear coat! pretty happy with first time results - these have not been sanded or buffed yet. I do have some small places to take care of but they won't show up on camera.
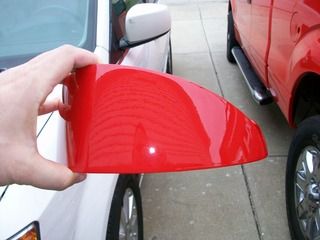
It is Tamco brand clear coat, HC 2100 euro. Very easy to shoot and lays out very nicely.
The weird thing is that my mom and dad are in town and his 2014 Ford Truck has what looks to be a very close, or even spot on, color match to what I am spraying lol. I am using an Eastwood SSU called Pinup Red for color in this two tone job. Crazy. I guess I never realized it, but the Ford truck has more orange peel than my paint job on these headlight hoods. I hear people talk about factory orange peel but never considered it. Crazier.
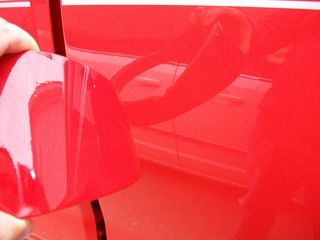
|
By Daniel Jessup - 9 Years Ago
|
Round 2 with the Devilbiss FLG670 tonight in the "paint booth" o shoot the white on both of the fenders. Things went pretty well. The Wimbledon White paint looks good - can't wait to peel back the tape and see the Red/White tutone combination on those fenders. I fiddled with the gun a bit more and dialed back the psi from the 23 I shot last time (lost of overspray but good coverage, etc) to just about 15 psi at the air inlet. PLENTY of pressure and volume to lay it out nicely and much less overspray this time in the booth. On the first coat on one of the fenders I thought I saw a small spot where the surface was contaminated, but on the second and third coat it disappeared. Not sure what that was. I went over the surfaces pretty good with Eastwood's Pre like I always methodically do... an hour later there were no signs of problems when I took the photos.
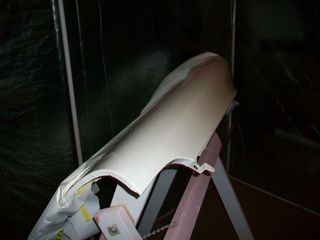
 the most rewarding part of all this is kind of reflected in this photo (sorry, my camera lighting was pretty dim but you can see the shine of course).
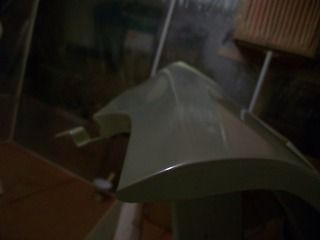 This is the same fender that had the ugly antenna hole that someone had cobbled up. A number of posts back I had to weld in some metal in that area and make sure it was all "seamless" in that particular area. Glad it turned out nice... no sign of the original damage!
The FLG 670 is a gun I am getting use to and enjoy spraying with it, but boy it takes a little bit to clean it up well after a spraying session.
|
By Daniel Jessup - 8 Years Ago
|
Bobwanna (12/31/2016)
Daniel, Thanks for keeping up on this project and sharing with us the products and tools used especially stuff from HF. I have learned much about painting here since I am more of wrencher on cars - Bob
No problem Bob, I keep posting here because I am a fellow Y blocker and like you I enjoy turning wrenches on these old motors quite a bit. The foray into quality restoration work such as body, paint, etc is still pretty much new to me as I walk through this process. Glad to hear someone is being helped. The same thread here has a much larger following over on the Fordbarn.com's forum. Not too many reply or comment here --- this is mostly an engine site.
|
By Daniel Jessup - 8 Years Ago
|
Boys I am back at it after having a long stint of illness and travel related to what I do for a living... " unselectable="on" style="max-width: 90%; border: none; cursor: text; vertical-align: text-bottom; margin: 0px 1px; width: 18px; height: 18px; background: url("styles/default/xenforo/xenforo-smilies-sprite.png" -40px 0px no-repeat;"> At any rate here are some photos of progress. First up would be the AC/Alternator Bracket setup from Vintage Air. The plates used are near bullet proof and the hardware looks pretty complete. I have since painted the brackets and hardware with Black Engine Paint. More on that install later - the AC kit just arrived and I am looking at mock-up, routing, etc.
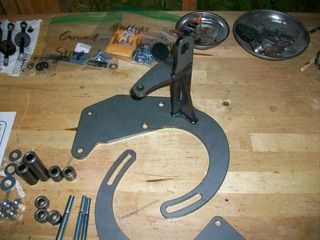
 I am thinking of replacing the firewall pad - should I go with original, ABS plastic, or something else you guys are happy with? A radiator catch can came in while I was down so I got that installed this weekend. Pretty easy to do. The kit came with pop rivets to attach the brackets to sheet metal up front, but I decided drill 1/4" holes in the radiator support and attach the brackets with bolts - the holes were tapped 1/4 - 20. Kind of think that will be much better than pop rivets and of course removable as well.
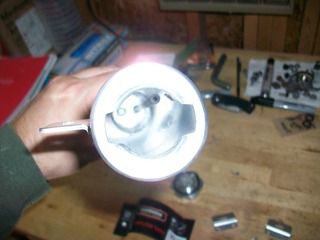 

 The catch can is made of aluminum, has a decent cap on it, and obviously it has the tubes inside - one for intake/one for exit. Looks nice in the engine compartment. Keeping the brackets on the radiator support will also allow room for relays if I need them on the sheet metal panel to the left in the photo. I also removed the rear bumper brackets so I could access the body at the rear for sanding. Since they were off and handy I went ahead and blasted the brackets and coated them with Rustoleum.
|
By Daniel Jessup - 8 Years Ago
|
And... I also decided it was time to remove the trunk so we could get that painted since the fenders turned out so well. I did make adjustments to ensure that the gaps were right on. After that I decided to drill a 1/4" hole in the middle of the plate that bolts to the trunk.
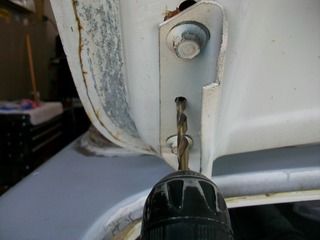
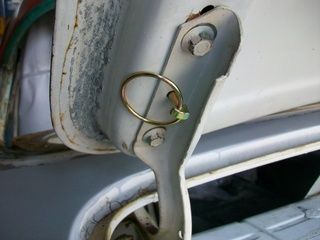 I used those 1/4" pin clips (easily purchased at most hardware stores). Since the circlips are somewhat spring loaded, the pin will stay in its boss. As you would surmise, this was my idea to make re-installation much easier to keep my gaps. It may not be 100% spot on when I go back to install it after paint, but it will be very, very close. At any rate I don't think I will have an issue with an paint scratches. The trunk was turned upside down so the lip could be cleaned really well and primed. I did tape off the holes so that no sand and could get in the cavities.
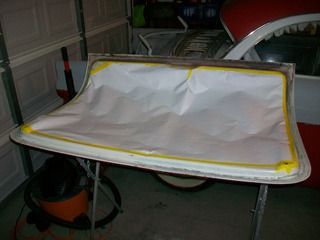 The lower lip has some corrosion, but not enough to warrant a trunk skin. 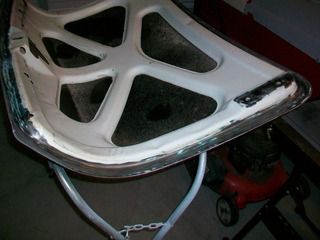
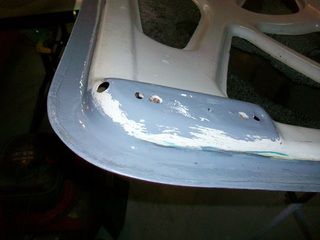
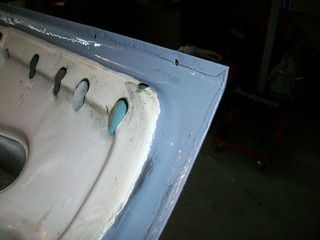 Hopefully I can get the trunk sanded and primed a little more next week. Moving right along now...
|
By Daniel Jessup - 9 Years Ago
|
Oh man what a night! :mad:
My plan was to spend a few minutes removing the rear glass. I had stripped up to the edges of the stainless trim as not to scuff them up so to get the rest of the metal there and underneath of the seal (windshield and the doors/quarter windows will come next) the glass and SS trim needed to be removed. Right. A few minutes. Jessup don't kid yourself. 
On with the "show"
First off, I say to myself, "Jessup, you better get out the manual and read up just to check it out, there may be a hidden clip or screw or retainer that you can't see."
Now mind you, I have installed and removed the windshield 4-5 times and was very familiar with that and felt pretty confident about the rear glass. I read up on the pages in the manual.
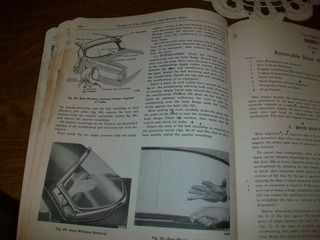
Good, got it, ready to go. Now out to the garage to remove the rear glass.
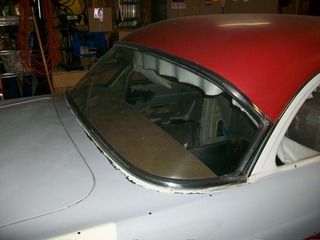
The seal was still on the soft side, but you could also see places where it had split or come apart and just needed to be replaced.
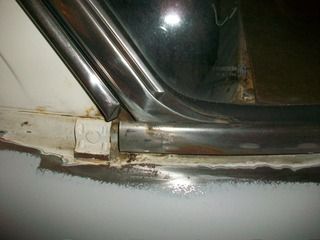
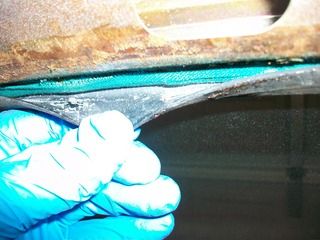
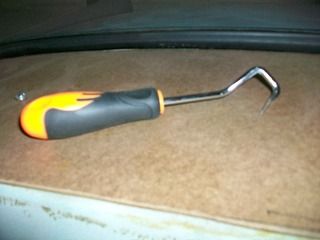
I used the tool above to pry the edge of the seal along the length of the sheet metal edges and tried to push the glass out like the manual says to do. I spent over an hour trying to nudge, push, tug, shove, cajole, tap, move, slide, pry, coax, cut, pull this 62 year old installation of rear glass from FoMoCo. I decided to cut the seal on the inside of the car.
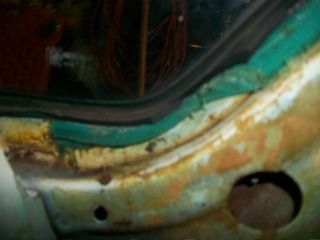
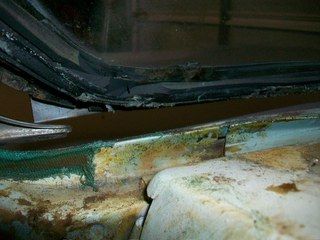
and it finally started to budge.
How, I have no idea. For some reason it seemed that the passenger side was glued in heavily.
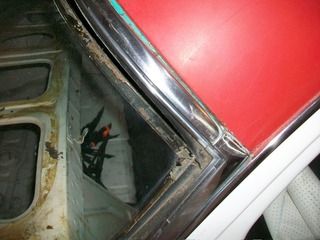
Let me just say that through all of this frustration I was glad of one thing... I did not gorilla the thing out. If I had done so, I would have surely cracked the glass. Look what was hiding under the side trim on the passenger side.
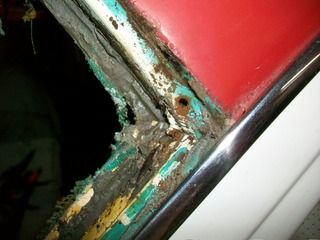
Thank you Ford, no help there lol.
I thought there would be one on the driver's side but there wasn't.
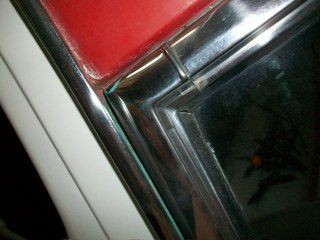
It all came out fine but I am concerned about how to that screw back in there and then put that side trim over the screw after everything is fitted. How will that work?
|
By Daniel Jessup - 9 Years Ago
|
ian57tbird (10/19/2016)
You still need to take care even with those discs as they still create some heat and it doesn't take much to get warping.
Thanks for the reminder... I work it pretty good and never stay in one place too long. I would hate to have to deal with oil canning.
|
By Daniel Jessup - 9 Years Ago
|
Been so long since my last post, almost forgot where this thread was at! The last month has been very busy but hopefully it is showing signs of letting up a bit as we head into the new year soon. I did get around to start putting up a paint booth - pvc and plastic with filtering/ventilation - and have finished prepping the fenders. I am pretty happy with their look and feel after all the blocking and fine prepping. The scissor stands I have been using for the fenders are lightweight and versatile, just not a good fit for actually spraying. I was able to hit the fenders with primer alright but it took some finagling.
So... it was time to consider what to hang the fenders now that we need to spray the SSU. Enter the versatile 2x4!
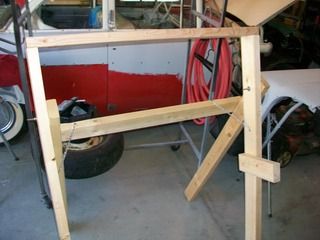
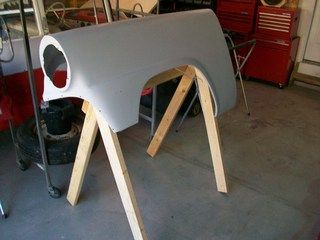
I built them on a scissor principle, but much higher. The top sits about 55" off the floor level. These were built so I could have access to both sides, tall enough to be able to shoot the bottom of the fender comfortably, and with a dog leg attached so that the bottom portion of the fender will "stick out" a bit for easier access. They are 40" wide and are obviously built for 55/56 fenders. The good thing is they fold up just about as flat as 4" give or take.
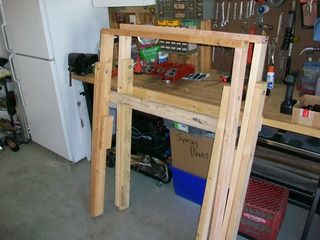
For those of you concerned about the dust... YES, I did wipe down the wood and prime the stands once they were all bolted together and functional.
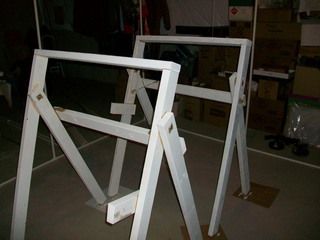
What have you guys used in the past? I have seen some good stands manufactured by different companies, but I really didn't want to spend the dough because I don't do this full time and I am not sure how many cars i will ever do in my lifetime. Any more DIY on fenders, hood, trunk lid, doors??? your pics would give us good ideas if you have some available.
|
By Daniel Jessup - 9 Years Ago
|
I went with a PVC frame up and 5 mil plastic for a make shift paint booth. A box fan to bring air in and a box fan to exhaust the air. The "air replacement" and fume containment was excellent... until the exhaust fan filter clogged up - then it was a blow out as the overspray found its way out every nook and cranny under the plastic.
The paint is an Eastwood SSU color called Pinup Red. The gun I used was a Devilbiss FLG670, with a twin stage 5 HP compressor that has plenty of flow with those High Flow fittings. CFM was not a problem. As a matter of fact, the overspray seemed to be quite a bit much when compared to my cheapie HVLP guns I have. The flow, atomization, and ultimately the finish of what I sprayed was excellent. I am very happy with it, but I am confused at all of the overspray. My Devilbiss gauge showed 23 psi at the gun, and I had the nice cigar shape spray test pattern from the gun. The tip is a 1.5, and the material knob on the gun was wide open. The paint was mixed according to the manufacturer's recommendations. Any ideas or is it just something I need to live with and just replace filters more often?
|
By Daniel Jessup - 9 Years Ago
|
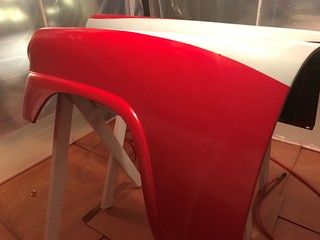
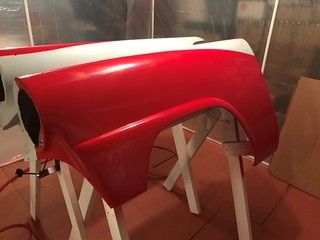
Don't want you all to think I've been lazy!
|
By Daniel Jessup - 9 Years Ago
|
Sprayed the final parts that needed to be red in color - the body + doors still need red of course.
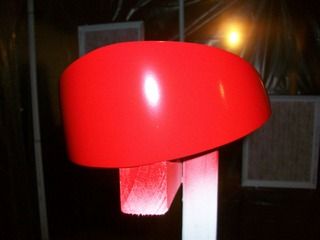
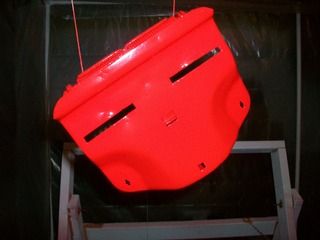
The "paint booth" really worked well but it did not see that much in overspray. I used a HF detail gun -
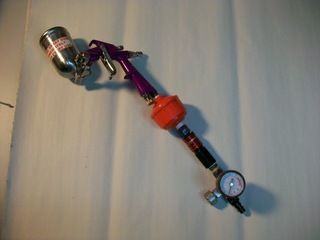
It has a .6 tip, and the SSU was mixed 3:1 with a splash of reducer. I turned the PSI down to 22 or so and the paint atomized nicely and flowed well out of the gun. The gun did not leak at all or have any issues - the pieces are a little difficult to clean but they came out nice with Urethane Reducer used as a solvent to remove the residue. I think I will end up painting the door jams and the hood channel with this gun.
One more shot of the fender in better light....
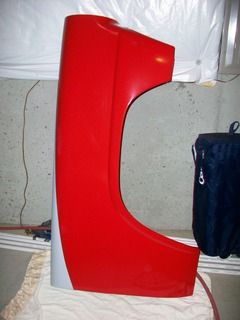
And I had some clear coat delivered just today. The plan is to take on the panels and parts with 800 grit paper before clear coating with a 1.3 tip. Any suggestions on clear coat let me know. 
|
By Daniel Jessup - 9 Years Ago
|
Late night work...
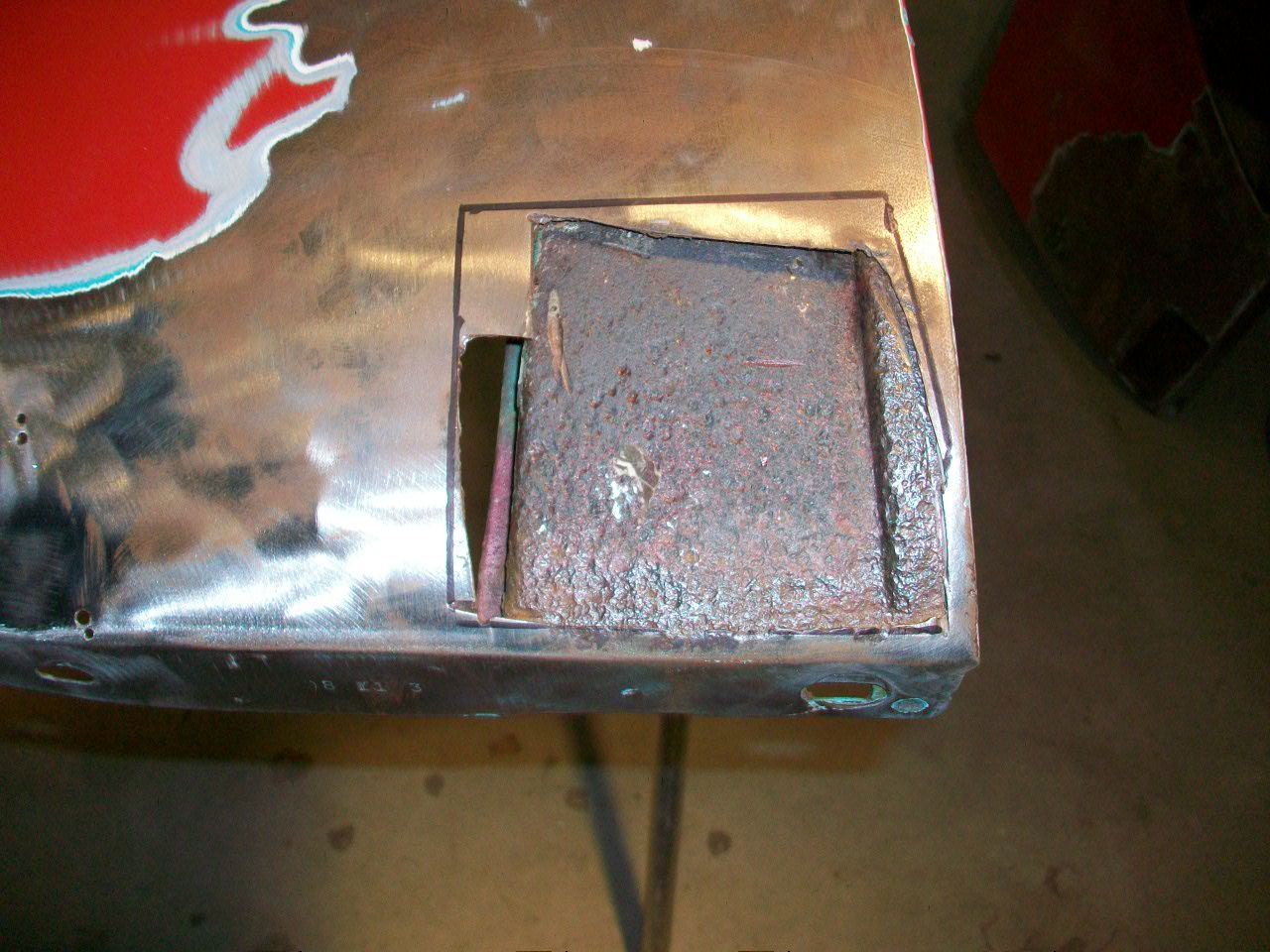
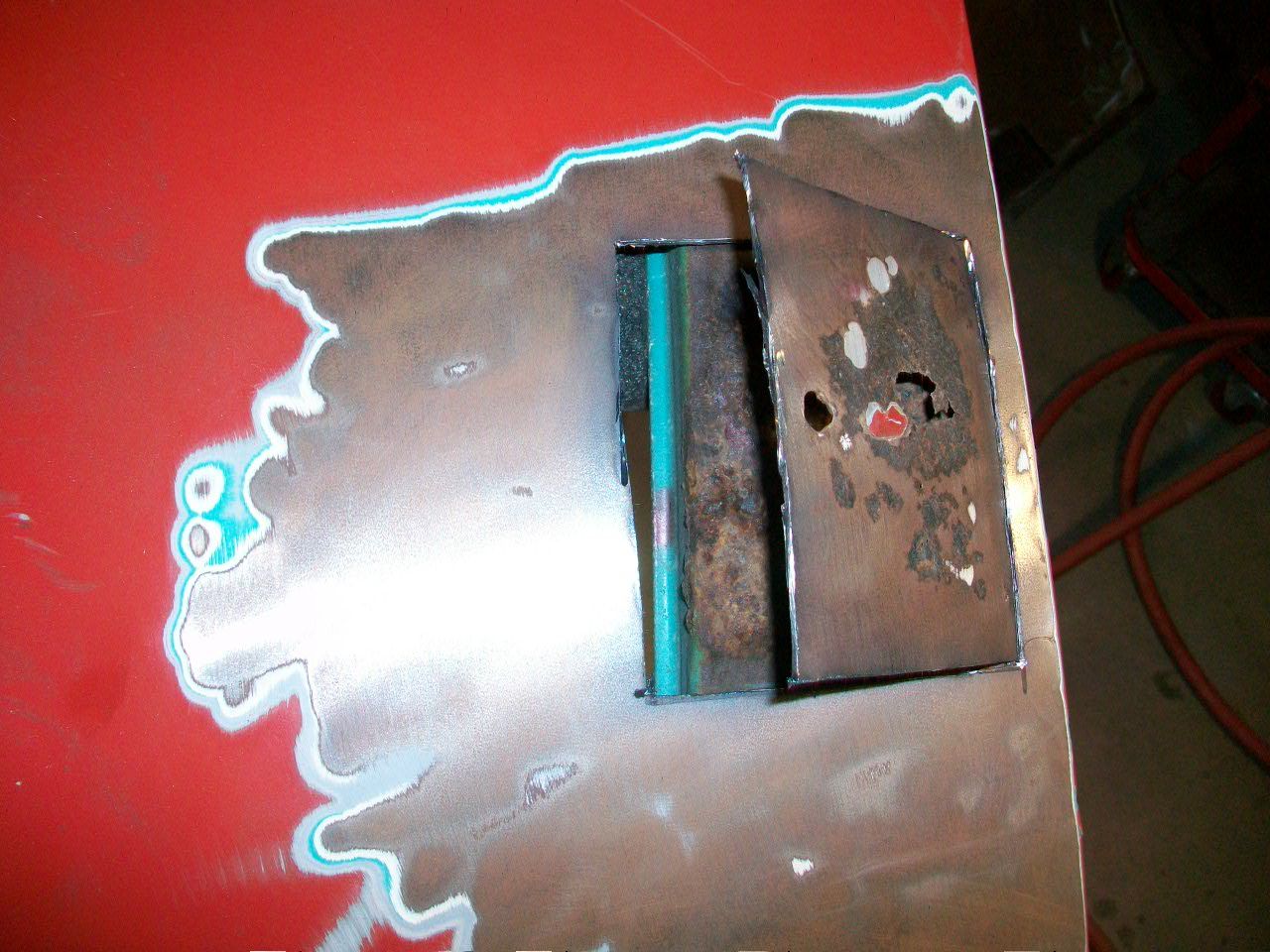
I decided to patch it up as you can see. No one makes a patch panel tall enough to reach up to that place almost in the middle of the height where the rot needs to be cut out. So I figured if I have to make a patch, what's one more? 
I basically tried to square things up as much as possible to make my patches easier to cut and fit. For the smaller hole I made above the original "bondo basket" I found, it was pretty easy to take the rectangle piece I cut out and use that as a template to cut a new piece. The lower hole was a little more difficult as it was not completely square and there was not a good way to get thin cardboard behind it to trace it out. I had to use poster board above it, cut, fit, cut, fit, repeat and there we go.
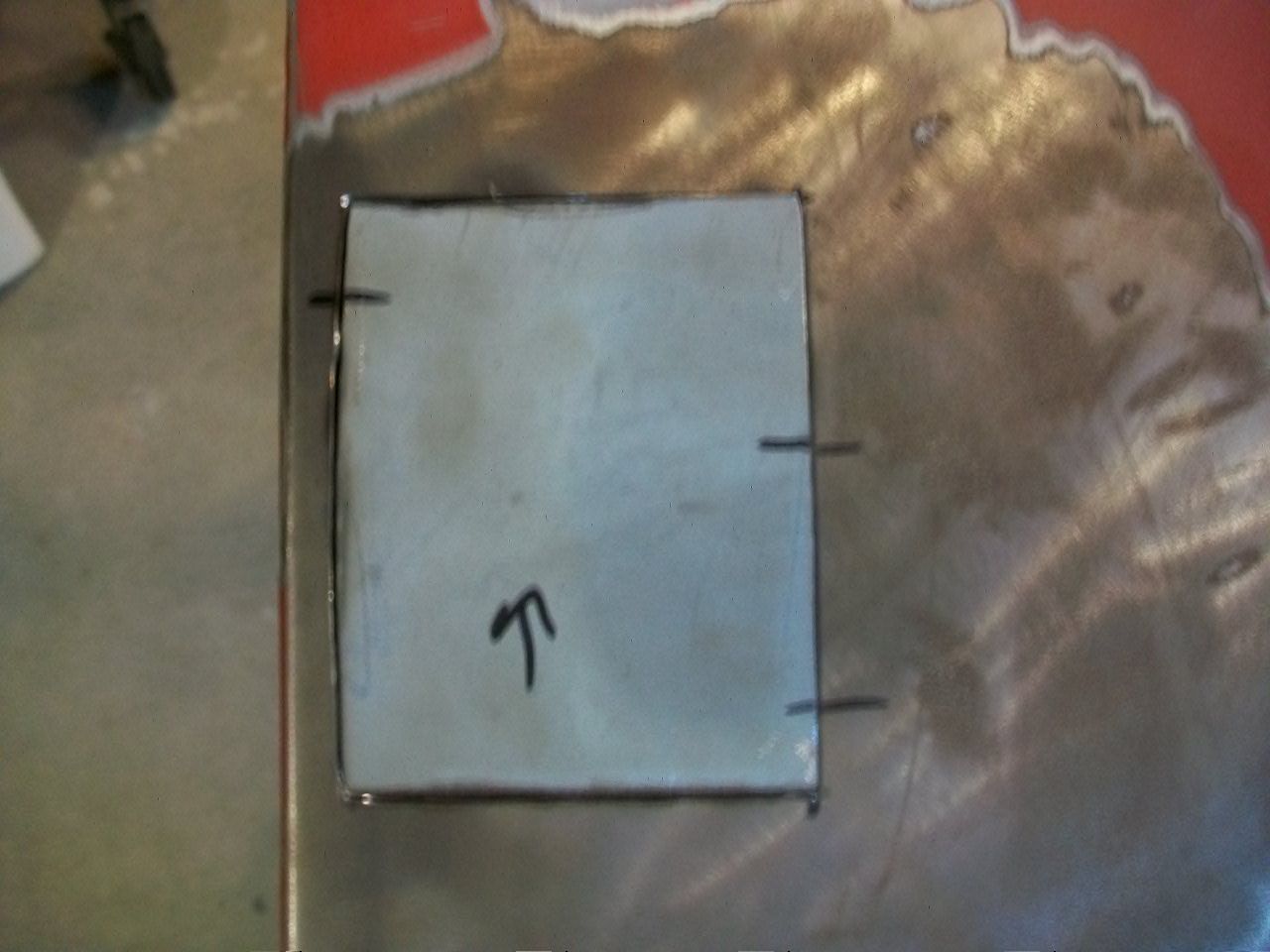
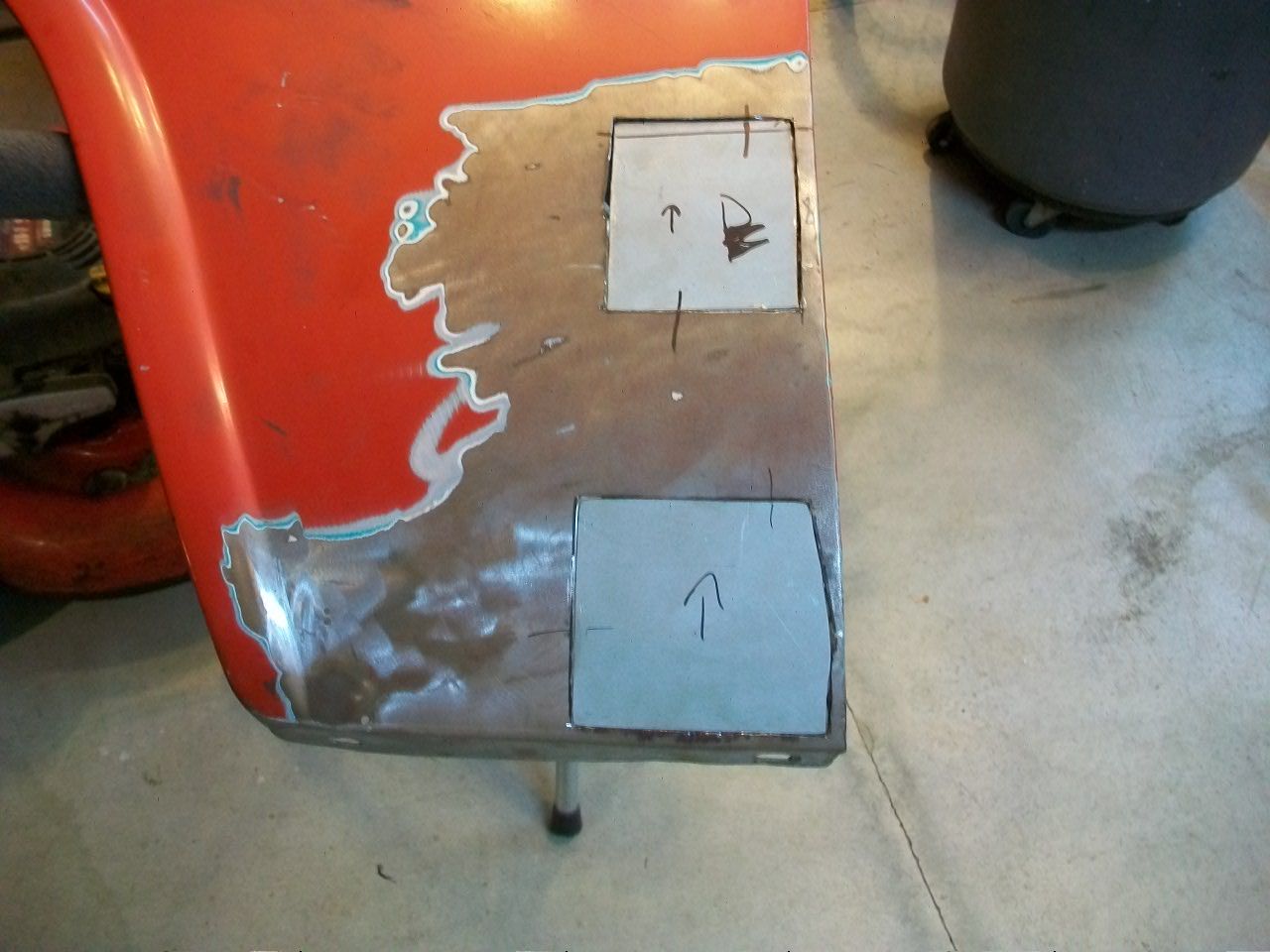
The patches were just cut from some left over stock I had that is the same gauge as the original fender. I was probably too cautious to cut it exactly true because I did have to do quite a bit of dressing and grinding to get each one to fit the hole with very little gap. I do believe for a butt weld with the mig it is best to get the metal edges to be pretty close to each other.
You can imagine how long the fitment took! :eek:
Hopefully I can blast soon, weld them up, grind them down, and get to spreading some body filler.
|
By Daniel Jessup - 9 Years Ago
|
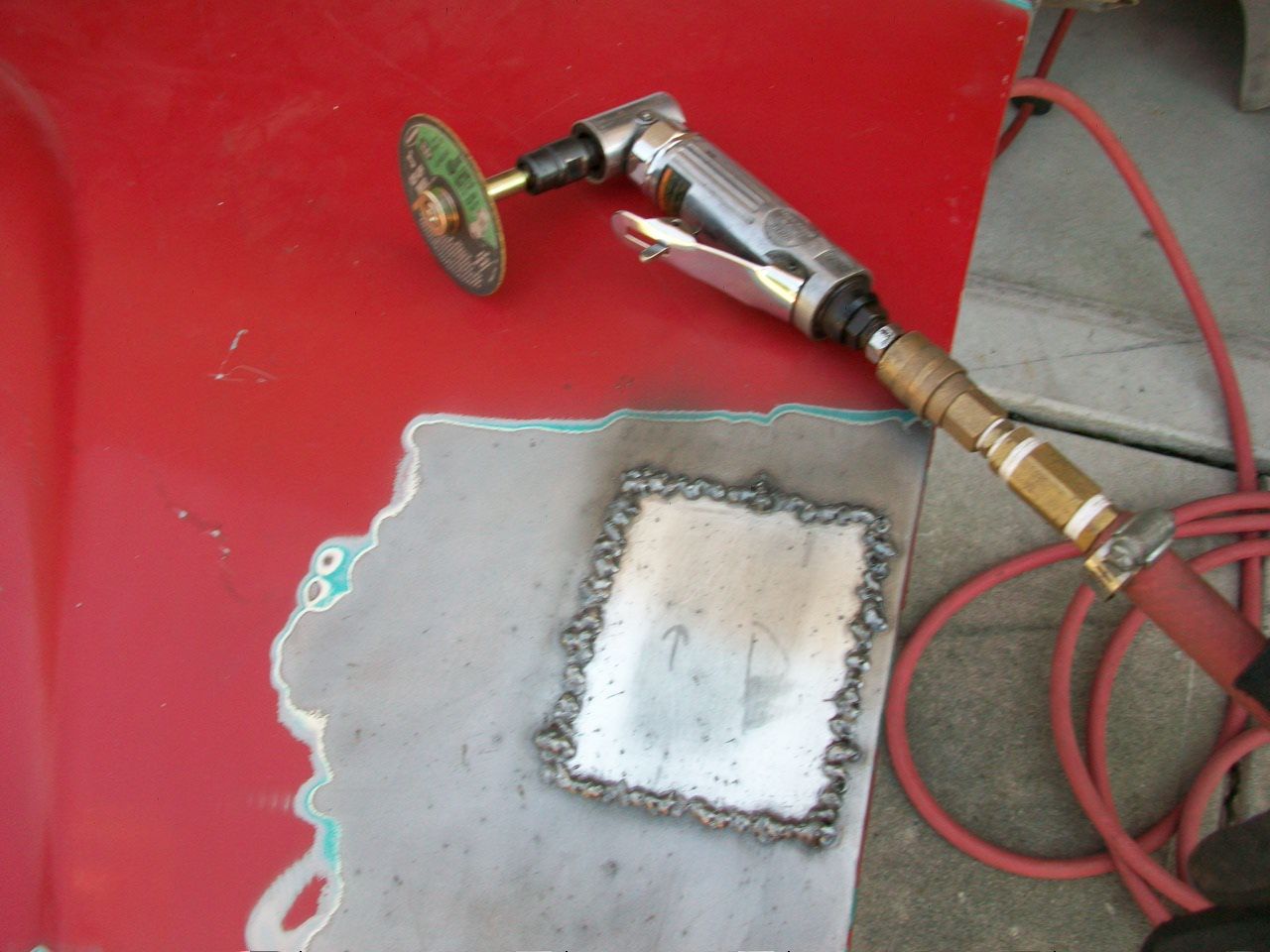
Took some time off on Friday afternoon to get on with the work on Driver's side fender. First up was the welding...
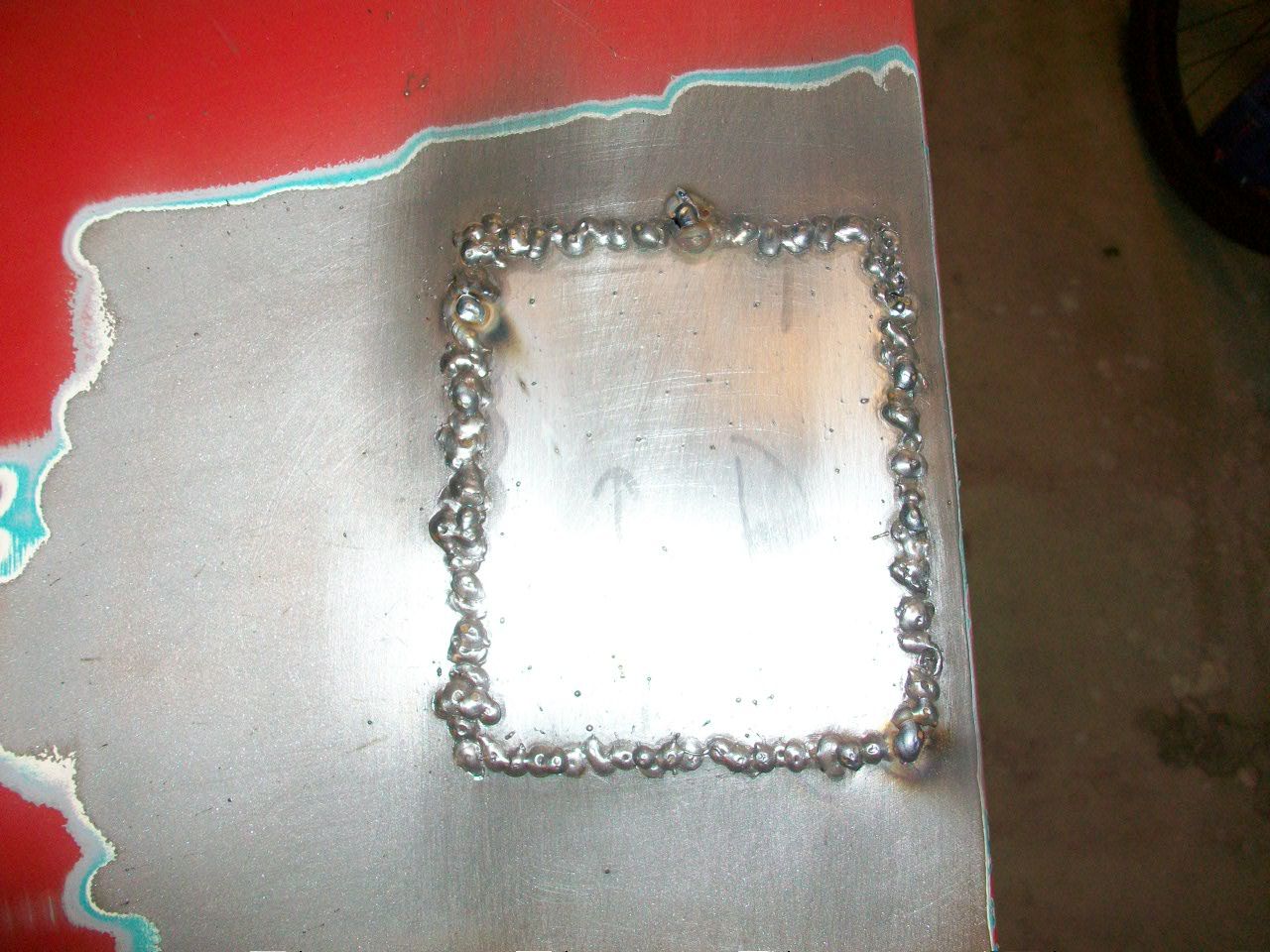
I also filled these small holes by using that copper spoon behind the panel.
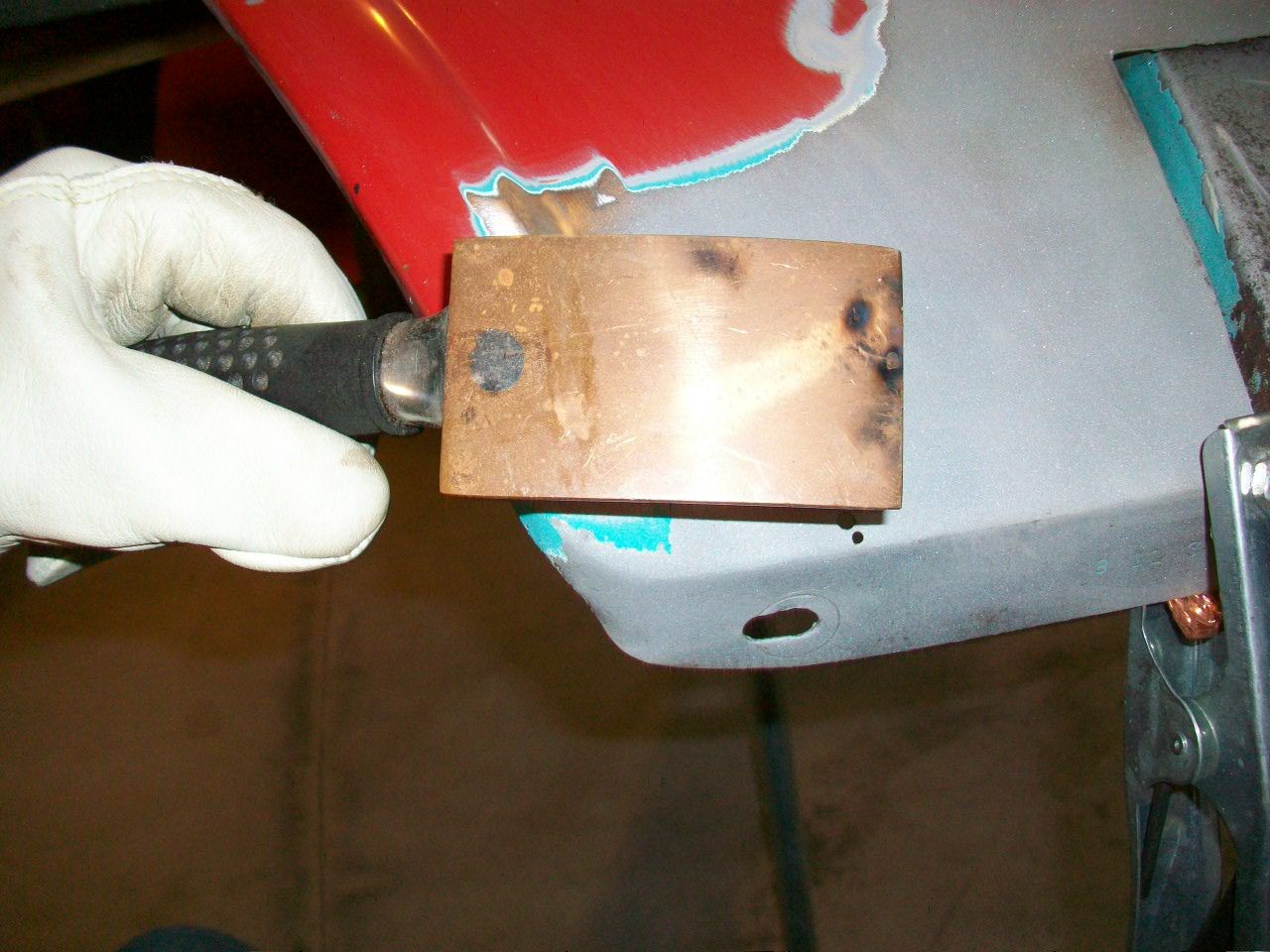
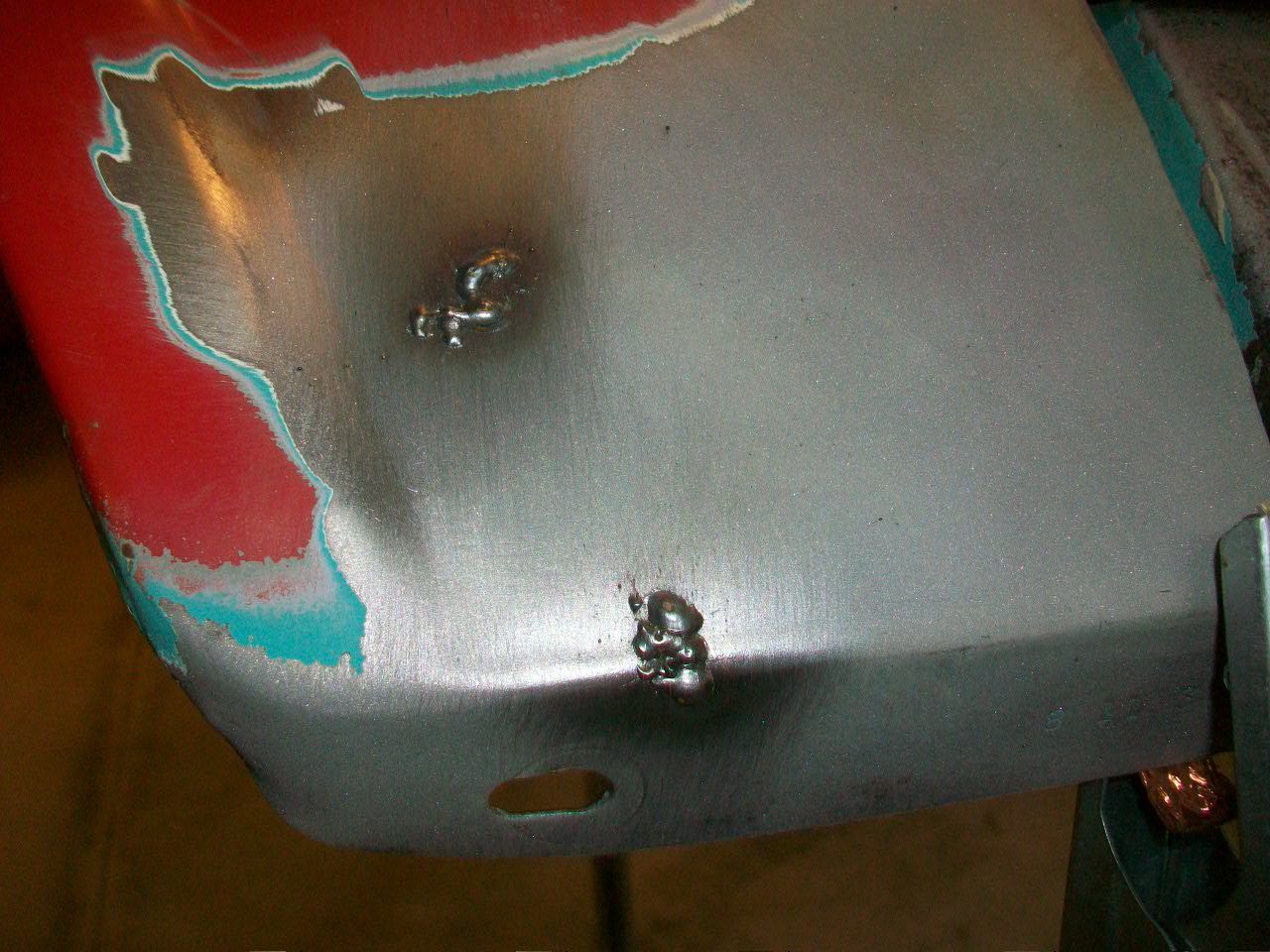
I admit I was pretty agressive here. I guess because I thought I had the copper spoon it was time to just pull the trigger and feed the wire into the thing... Of course that just meant more grinding - I am not an official welder, just a "trigger puller" who puts more metal into things than needed. It really showed up when I was stitching the panels in. I got carried away with the deal and let the panel get too hot. Take a look at the concave "warped" area.
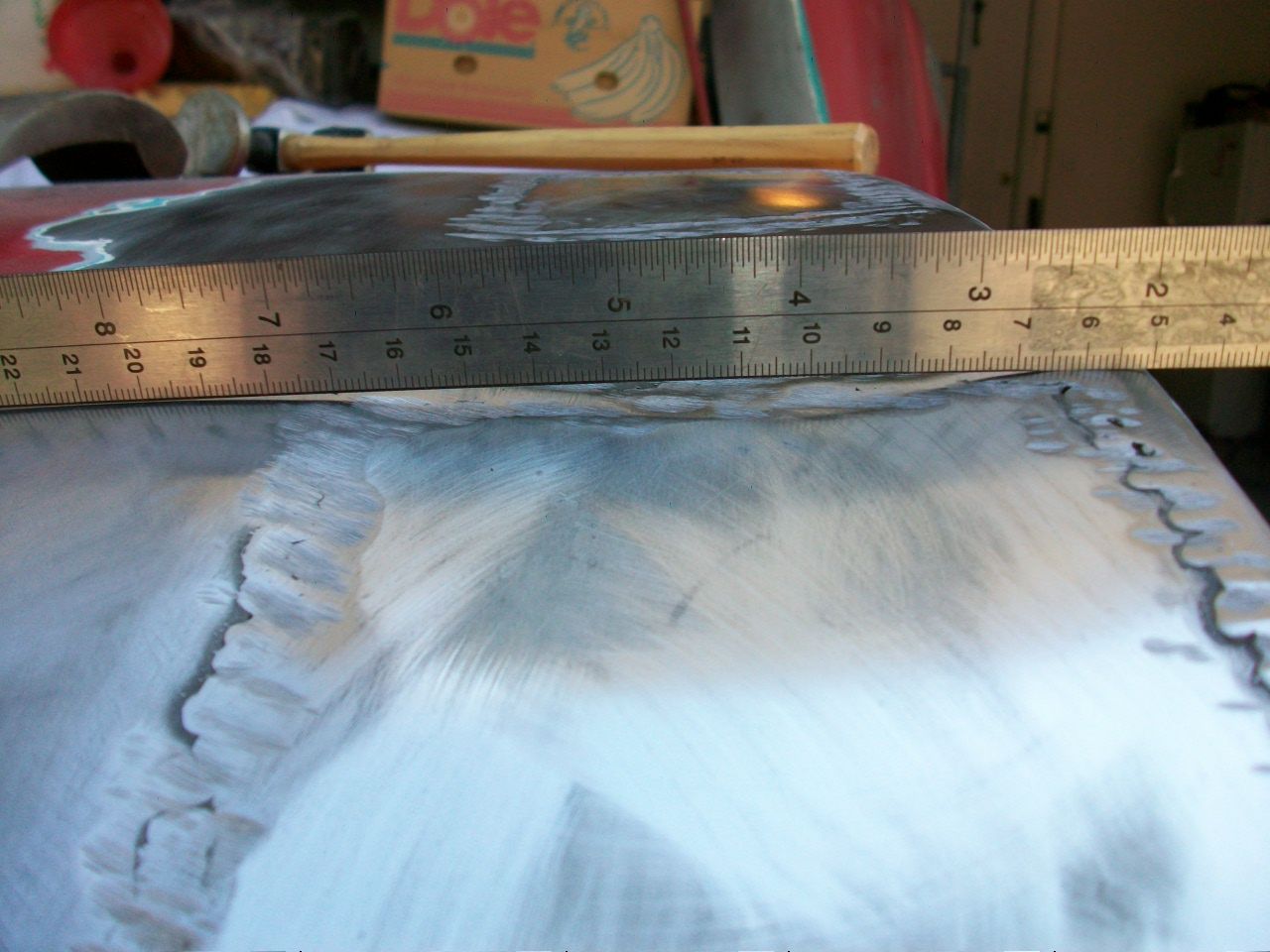
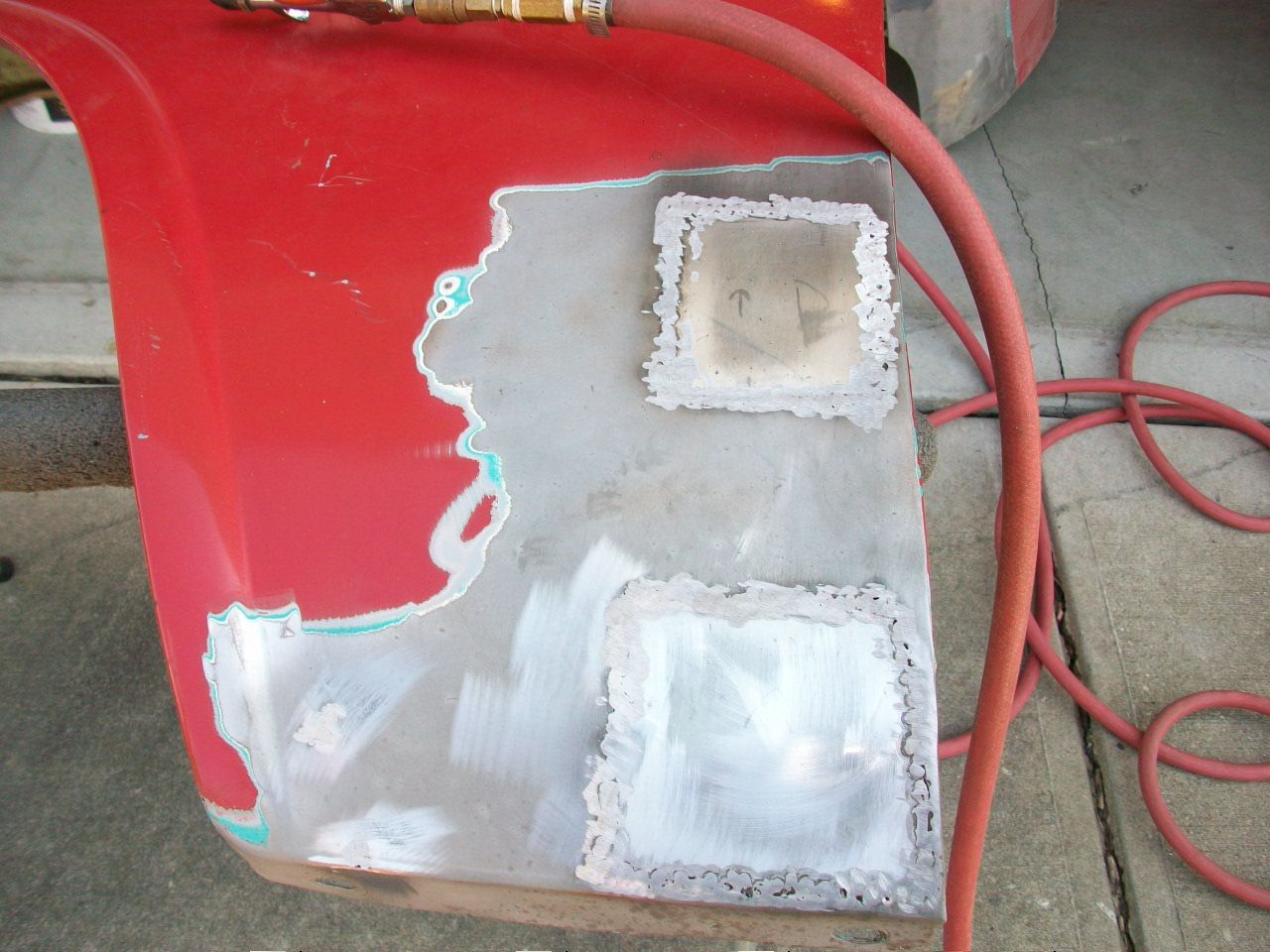
After grinding it all down and checking with a straight edge, it was time to get some filler on the thing and bring it back. Unfortunately that warped area could not be adressed from the back side because of the bracing. I reckon if I was not so lazy I would have removed the spot welds for the full length of the bracing, did some hammer and dolly work, welded the brace back on, etc, etc. Everything is a compromise between the time you have to do the work and what you plan to get out of it. Since the amount of filler needed would be less than 1/4" deep anywhere on the fender patch area I decided to get out the gallon jug and go for it.
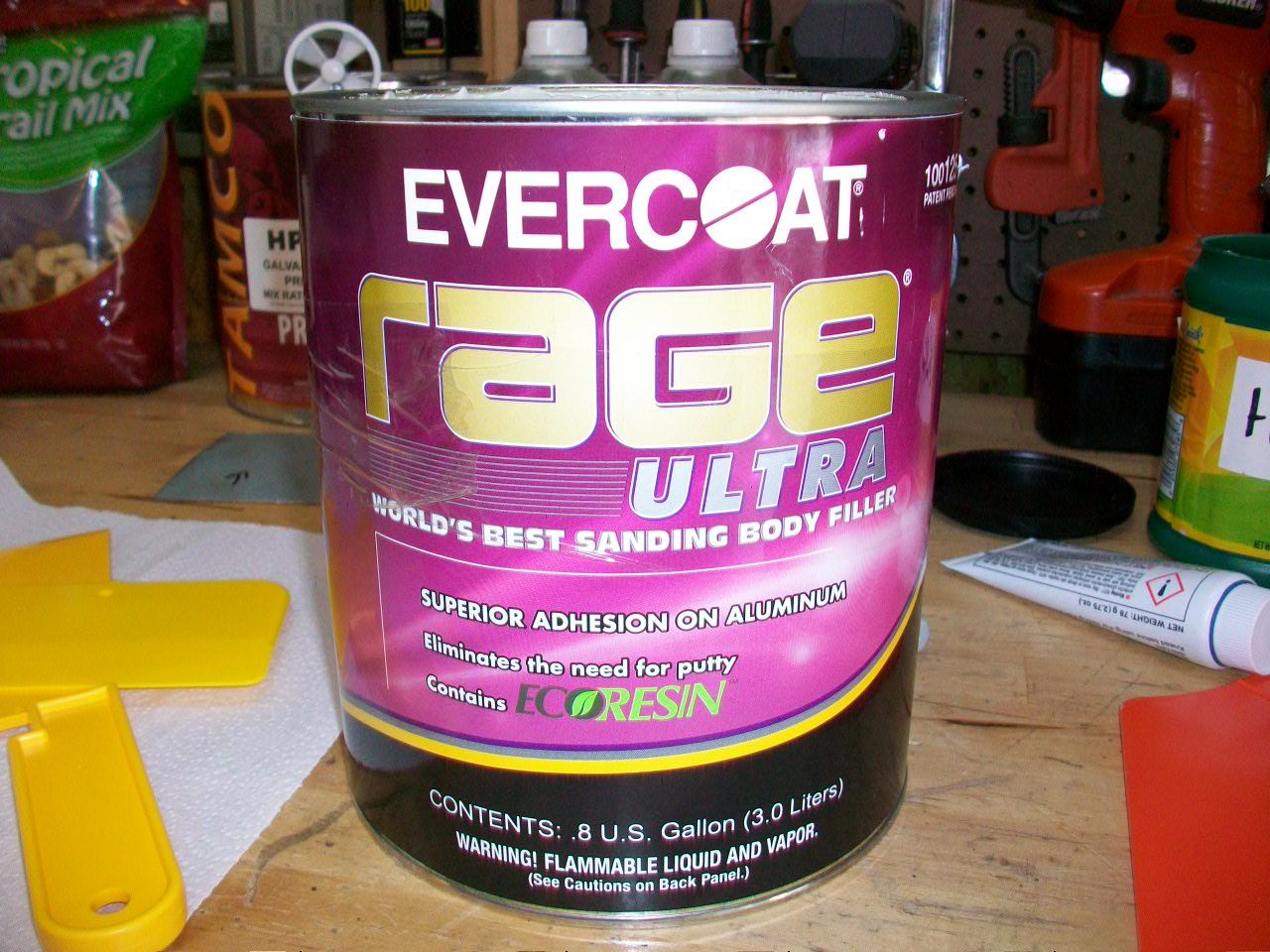
This stuff is worth the price! Thanks to Frank of Long Island for the tip. It has been years since I used any body filler and for this repair I thought I would need quite a bit. I didn't even use half of what I originally mixed. The depth of what I needed to fill was more shallow than it looked.
As I went along I did check things with a straight edge.
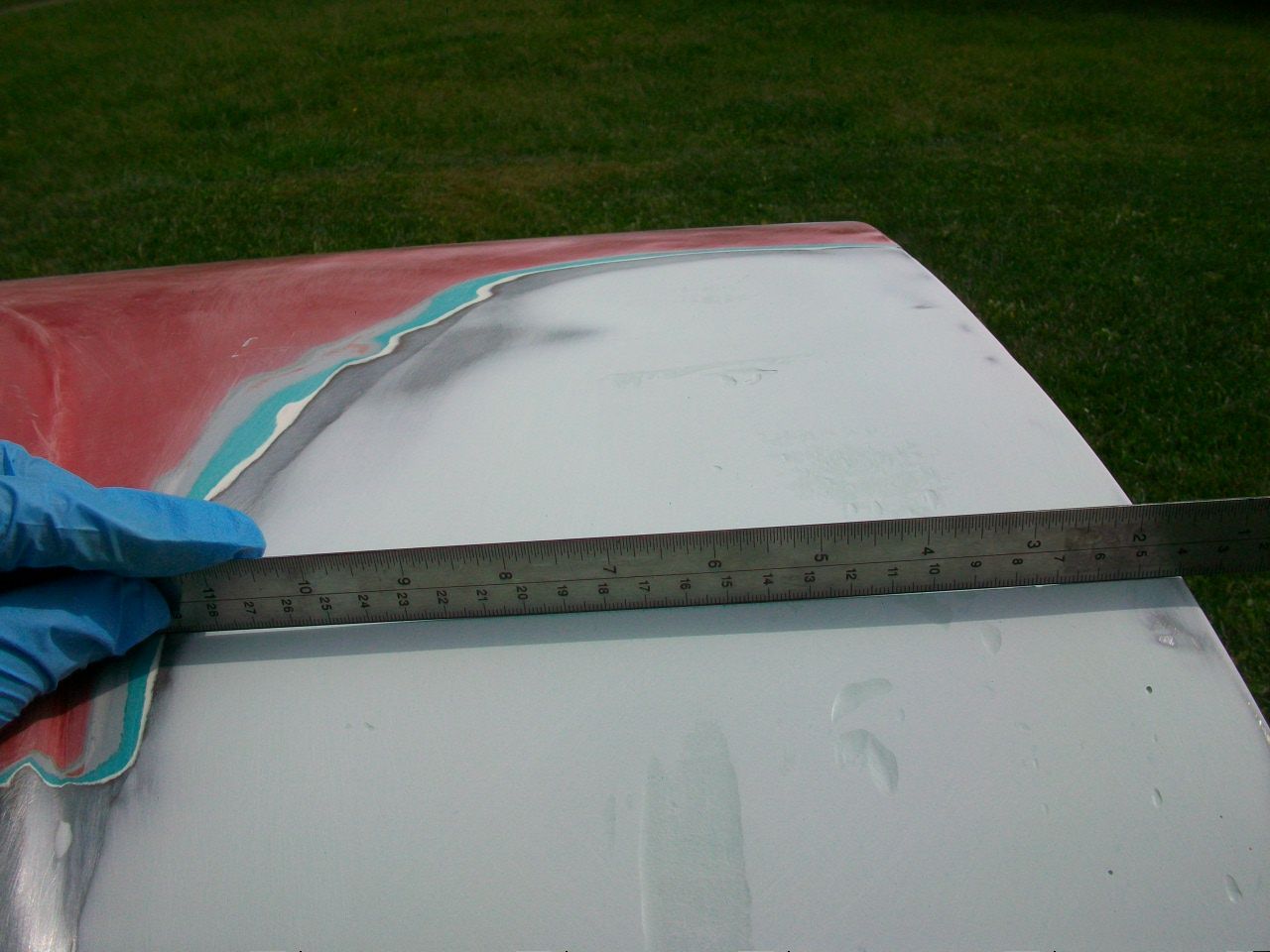
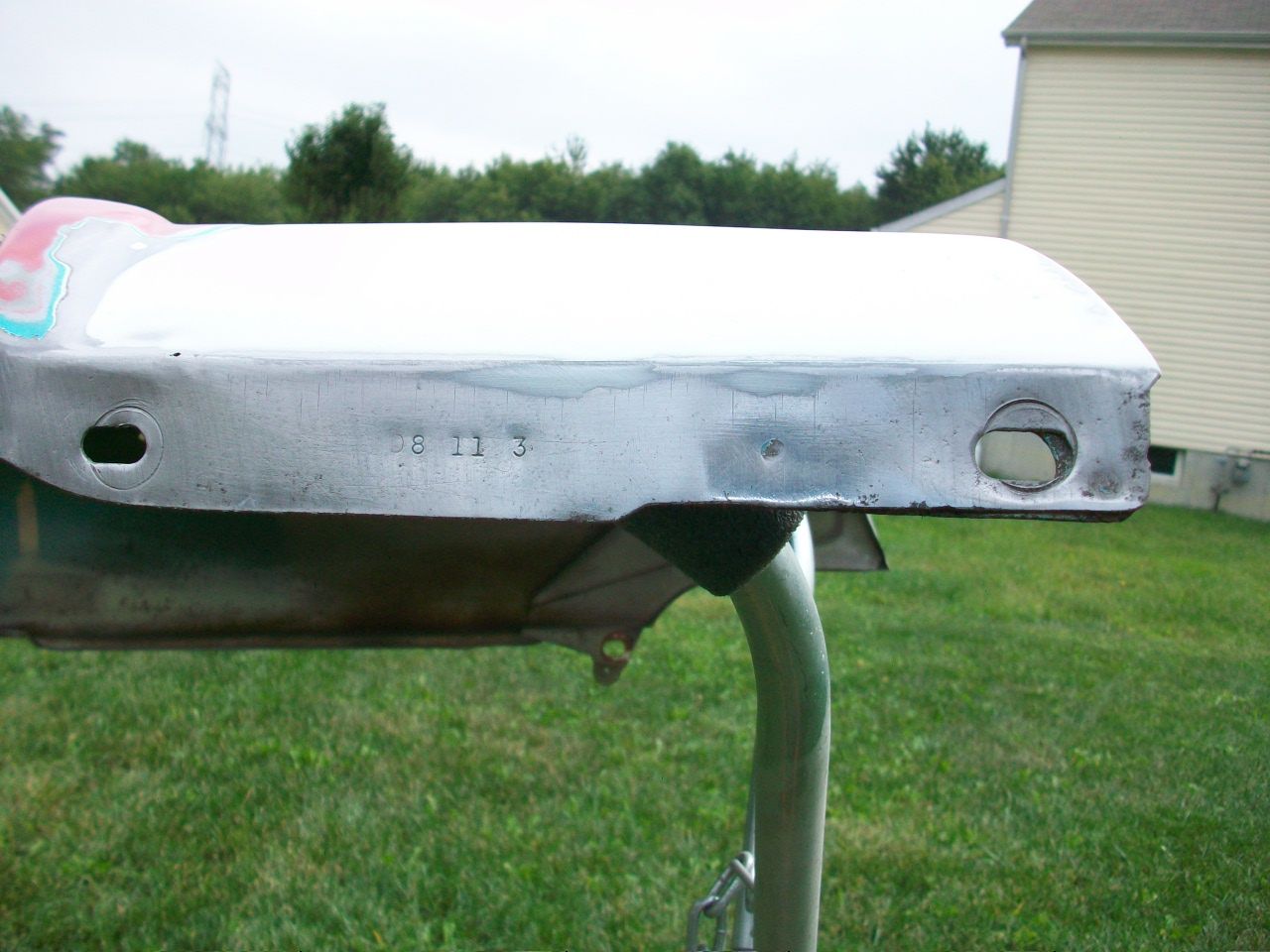
You can see I had some low spots yet to fill in, but that did not take too much. I used a DA with 120 grit to knock it all back down and smooth it all out. As you guys know, most of the filler ends up on the floor. 
I did have a couple of pinholes that needed some spot glaze but with this Evercoat product called Rage, the pinholes were few and far between.
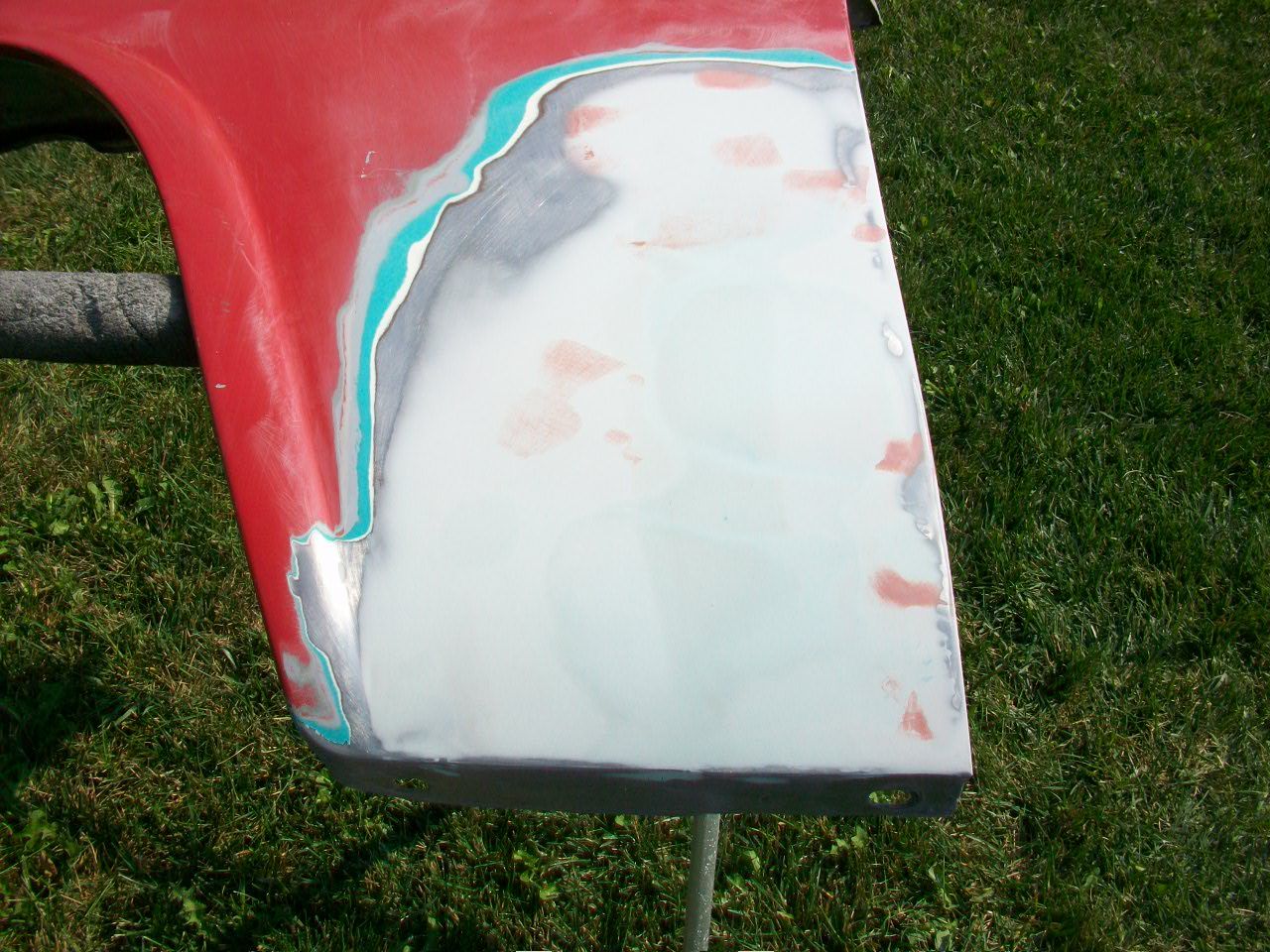
There were some other spots on the fender that got some attention too, a small spot I welded up underneath the headlight housing, a place under the stainless steel molding back towards the door, and another place up near the front under the stainless steel molding.
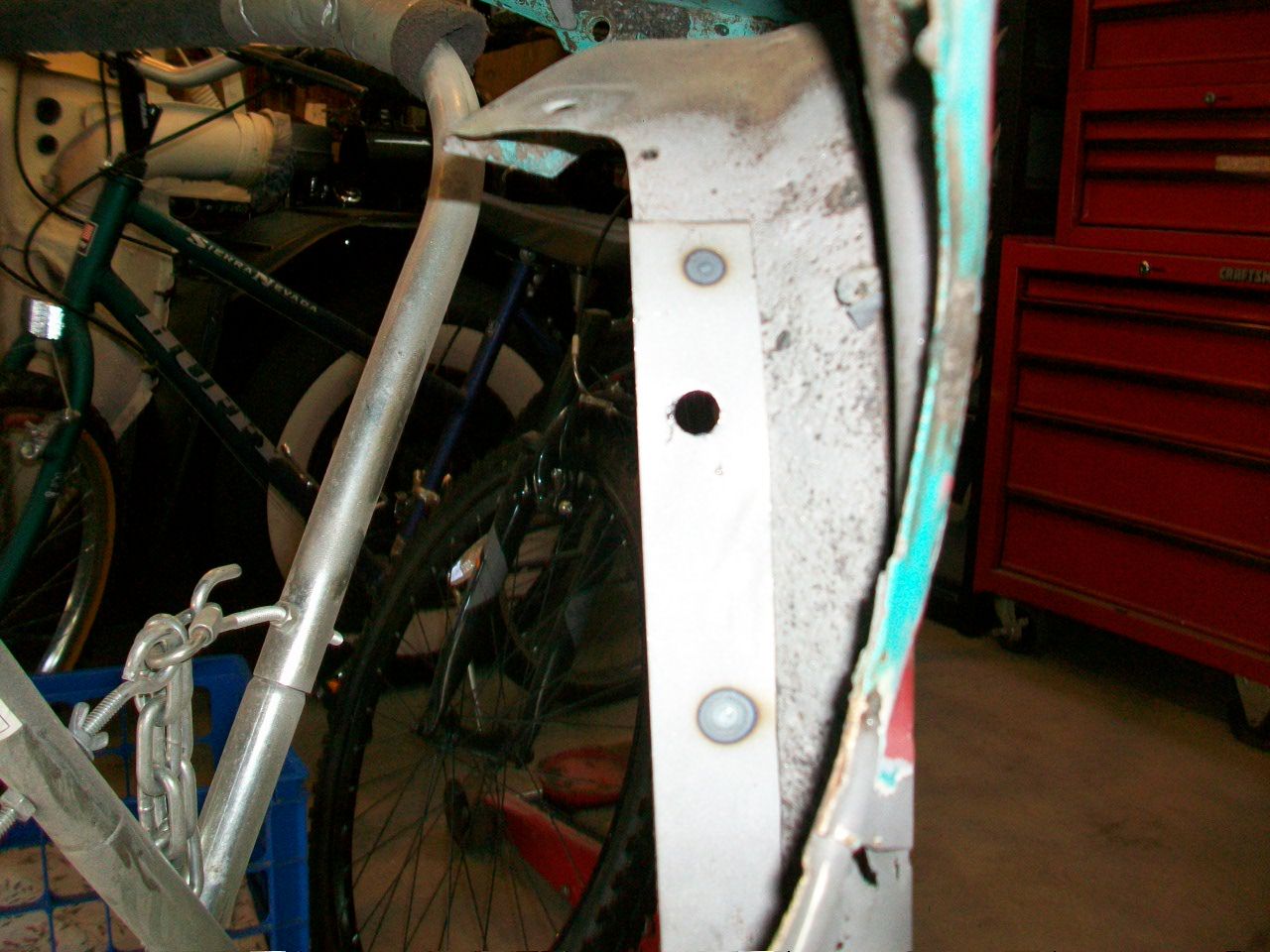
I do need to finish removing the white paint so that I can prime this thing. I am thinking that with some primer surfacer this fender should come out pretty smooth.
|
By Daniel Jessup - 9 Years Ago
|
The passenger side work went much, much better. You can tell from the photos - very little warpage, and the body filler went on smooth and set up well.
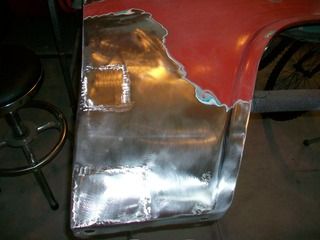
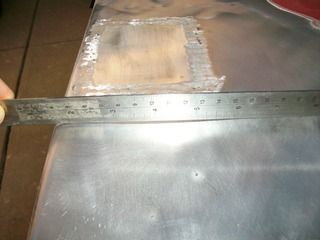
After the welding and body filler work it was time to remove the old layers underneath the white of the two-tone back on the driver's side. Whoever suggested that I take the white sections down to the bare metal was right on the money. There was various places where the metal had rusty pits and that had come up through the paint layers. At first I just used a plastic wheel to remove everything, but then after checking up on the pitting I decided to break out the sand blaster.
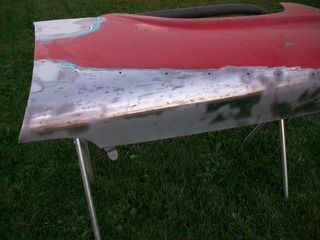
The passenger side fender was coated once in the areas where it was bare and then also in the places where the body filler was located. Upon sanding the entire exterior of the sheet metal, the whole fender was primed with two more coats of DTM primer surfacer. Time will tell on final sanding and how much goes to the floor, but I am happy with my initial look on the surface of the areas where the patches were welded in and the body filler work was done.
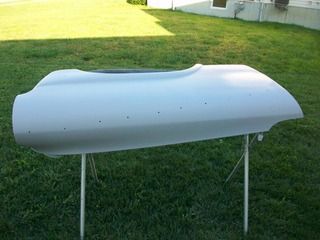
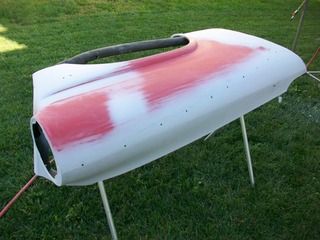
I haven't taken any pictures of the backside of the fenders, but they were cleaned up a little bit and painted with black rustoleum. I did thin the first coat pretty good to get behind the brace at the rear of each fender, and then gave it a good coat. Thankfully things are pretty stout with fenders - very little body work outside of the patches that were welded in.
|
By Daniel Jessup - 9 Years Ago
|
Are we having fun yet?
After scurrying around trying to beat a temperature drop and daylight wasting to prime the passenger side fender again and put a full coat on the driver's side look what I did...
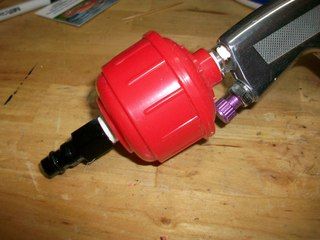
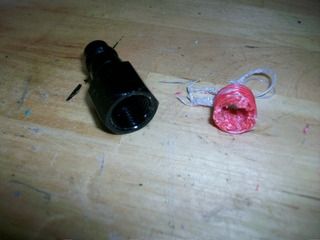
Dufus me happened to knock the paint gun out of its stand and although it did not fall far the tit on the bottom of the red bulb filter broke off in the fitting... aaaarrrrgggghhhh! Tonight was like one of those stupid reality TV shows where idiots play around like they can put a car together in a week. 
Ridiculous.
I did use the following glaze to prep my pinholes and what have you. This Evercoat brand is not cheap but I like its characteristics so far. It is super smooth and easy to sand. It set up quickly. However, I did not get the chance to paint until this afternoon so it did sit for quite some time.
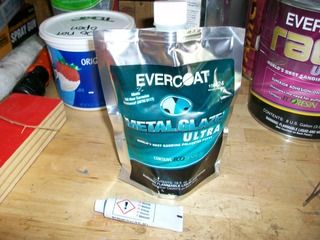
I don't know what everybody uses for a primer gun, but I do like what I am using. It is a cheap HF unit but it sprays very well and lays the primer really good. It has a 1.8 tip - the primer surfacer goes on pretty good and since this is a primer gun, not rebuildable (at least I don't think so), and it's cheap, once I get done with this project it can be tossed if need be. I have a Devilbiss Finishline gun to spray the SSU topcoats.
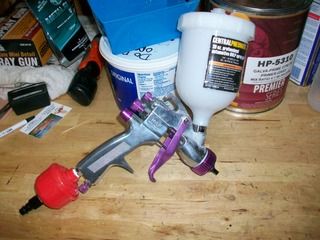
Before applying the glaze and next coat of primer surfacer I did some block sanding on the passenger side fender. Basically I sprayed the hi build primer on the low spots where I put in patches, used Rage Ultra, etc, trying to meet the red that was already on the fender. Things looked pretty good. I did wet sand as you can see. It's messy, I know, but when the water runs down the panel it is easy to see the high's and low's. Plus it keeps the sandpaper from filling up so much.
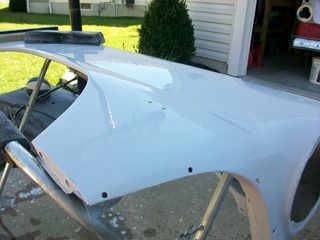
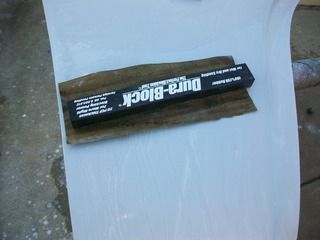
After everything was dry the next coat of primer surfacer was put on and then after a couple of days the glaze was applied.
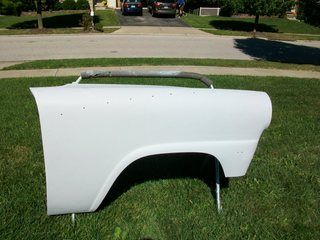
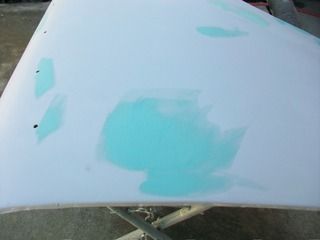
So.... to fast forward back to tonight if you are still following, the passenger side fender looks really good with the wet primer and looking down the panel as you can see.
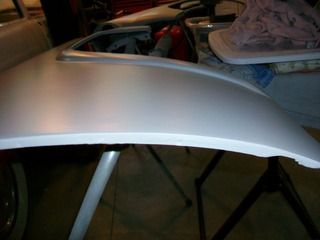
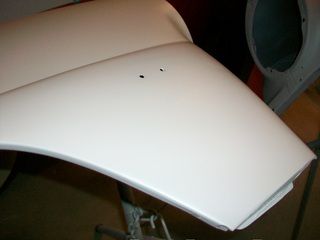
However, if you look at this photo here...
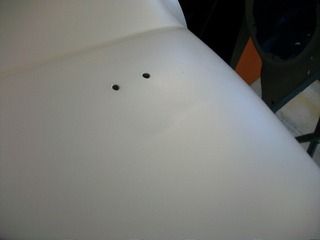
you can see that my Evercoat Metal Glaze is showing through. This is after two good coats of primer surfacer. I did reduce the surfacer a little more than normal, but not that much, so my build is not as much as the other coat of primer I put on this fender.
what gives? Anyone else use this glaze? I followed the manufacturer's instructions pretty closely. Maybe I should have put less reducer in the primer surfacer? :confused:
|
By Daniel Jessup - 9 Years Ago
|
After another several hours of block, prime, block, etc, I am reminding myself that we are saving quite a bit of money by going DIY.
The previous issue with the glaze showing through the primer was just simply too much reducer. Problem easily saved with the most recent coat of primer/surfacer.
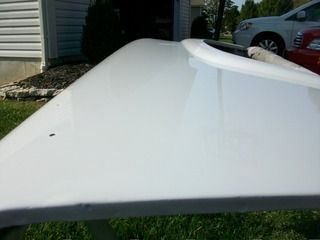
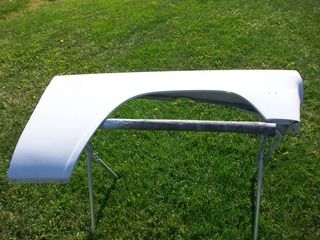
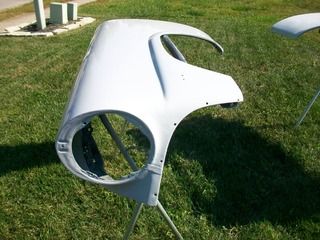
Passenger side is almost ready for a top coat, but the driver's side needs a little more attention. I did get around to mechanically stripping most of the white today. Some of the places I stripped on the door had over 1/4" of Bondo 3M Putty! I guess someone years ago had decided the best way to fill the mounting holes for mirrors on either door was to simply hammer the metal down and fill the dent they made. 
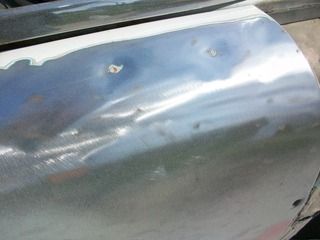
The plan next is to simply get some primer on this unprotected metal, remove all of the glass and door guts, and strip those edges without getting too much in the interior.
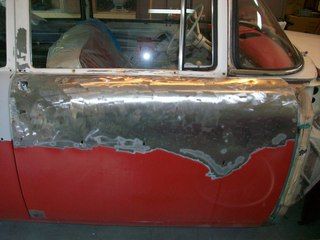
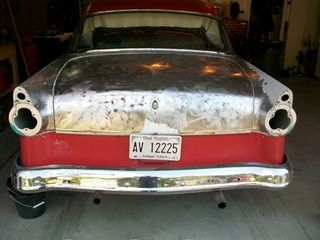
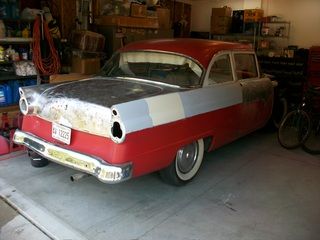
The stripping was done with a couple of these... http://www.harborfreight.com/4-12-in-polycarbide-abrasive-wheel-60571.html
and a few of these 80 grit... http://www.harborfreight.com/7-in-80-grit-sanding-discs-3-pc-69983.html
inexpensive tools to strip so much paint, no warp to the panels, and no sand all over the place - although there was quite a bit of dust. Most of the layers underneath of the crow's feet white paint were just fine, but there were places where pitted rust shown up. For those places I did spot blast with sand to get it all out, but things seem very solid and pretty straight.
Once we get going on these doors, it will be time to attempt an installation of 55-57 Thunderbird door handles. I read about the mild custom modification on another site somewhere and it seems pretty simple to do. (well, when I look at it anyway) The irony in the mod is that they are actually cheaper brand new than the passenger car door handles. Go figure.
the only thing I am missing is the video footage of the people that drove by the house and slowed down as they watched me work on this thing half the day :p. One guy with a 66 Fairlane showed up though - had a 427 cammer installed and that thing had ever appearance of an original restoration car (minus the keystones and nice tires) ... of course when you heard the thing coming down the street you lost any inkling that it was stock!
|
By Daniel Jessup - 9 Years Ago
|
Man this thread is huge! A few more photos of continued progress.
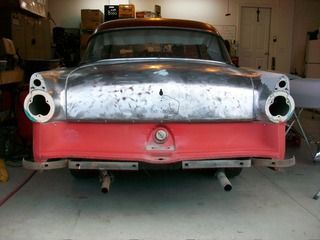
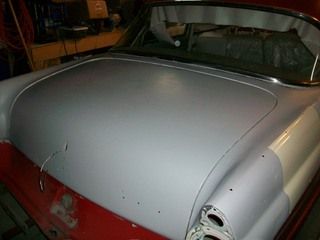
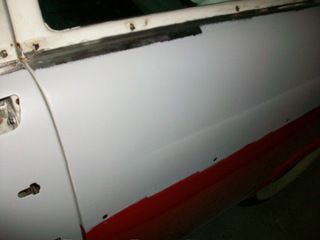 Hopefully I can get all glass out, the door guts out, and then strip the edges underneath the glass seals, etc. They have not been done since the car was new. I do have new seals, but wanted to remove all of the old stuff and then paint. That last paint job about 25 years ago was just taped up to the edges of the trim and sprayed. Surprised things have held up this long.
|
By Daniel Jessup - 9 Years Ago
|
charliemccraney (9/6/2016)
Sylvania off at least two types of sealed beams. One is standard. The other is a brighter Silver Star. The silver star draws more power, closer to that of a standard H4 bulb. They're in most parts stores.
Thanks Charley, I will take a look at what is on the shelf.
|
By Daniel Jessup - 9 Years Ago
|
slumlord444 (9/6/2016)
I've been running off the shelf halogen sealed beams in my T Bird for many years. Also ran them in a '56 Ford pick up many years back. No relay and no problems with the stock headlight switch. Large improvement.
That is what I hear about the improvement... would like to go that route, thanks.
|
By Daniel Jessup - 9 Years Ago
|
I decided last night to rub down the SS headlight trim rings with Acetone and buff them a little bit. The PO had this car painted a long time ago, and you can see from the one headlight ring how shoddy the masking work was. Red paint was all over these things. The rings are in good shape though, and do not show any dents or other problems. I decided to put some elbow grease into it and reuse them.
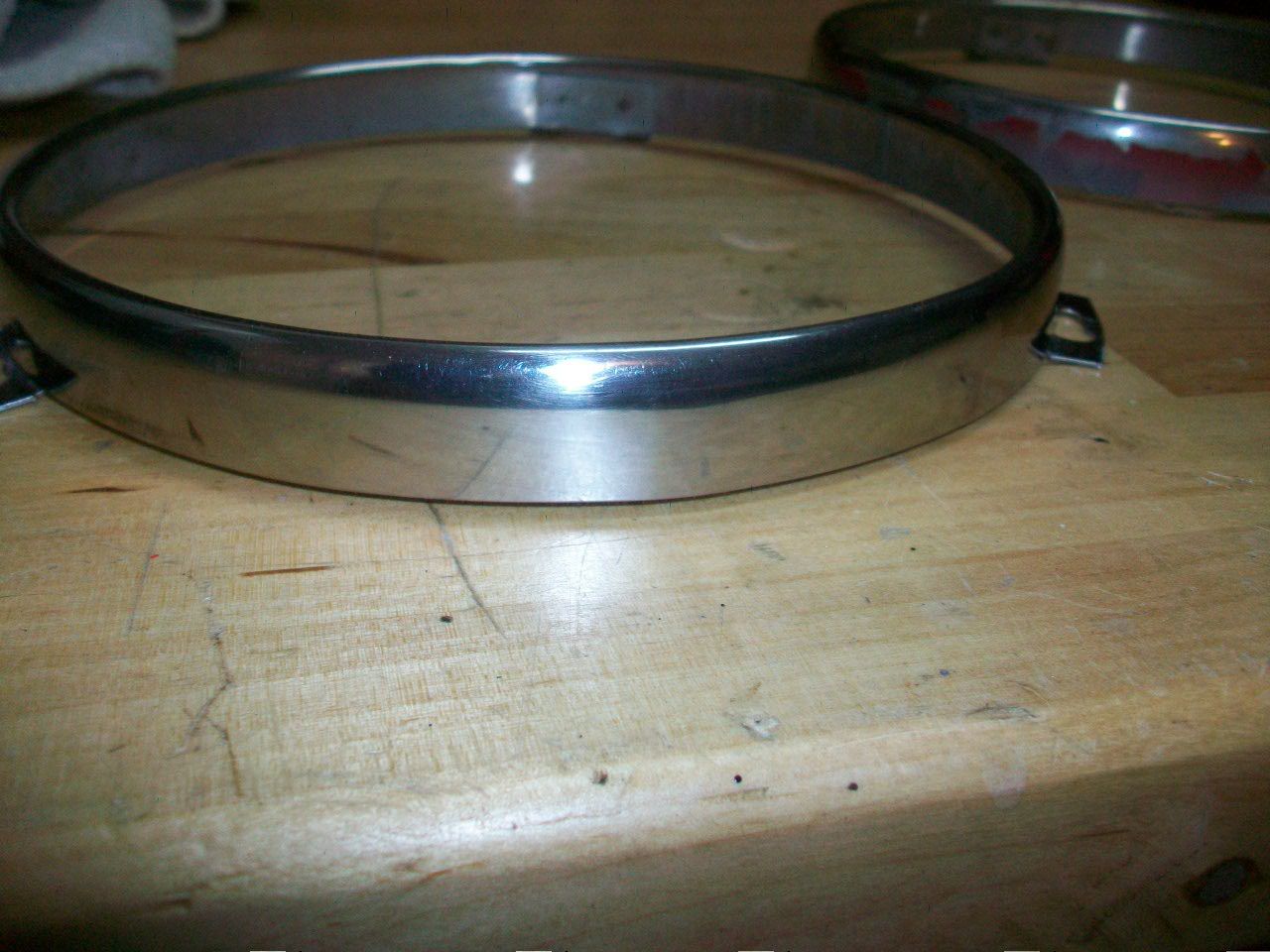
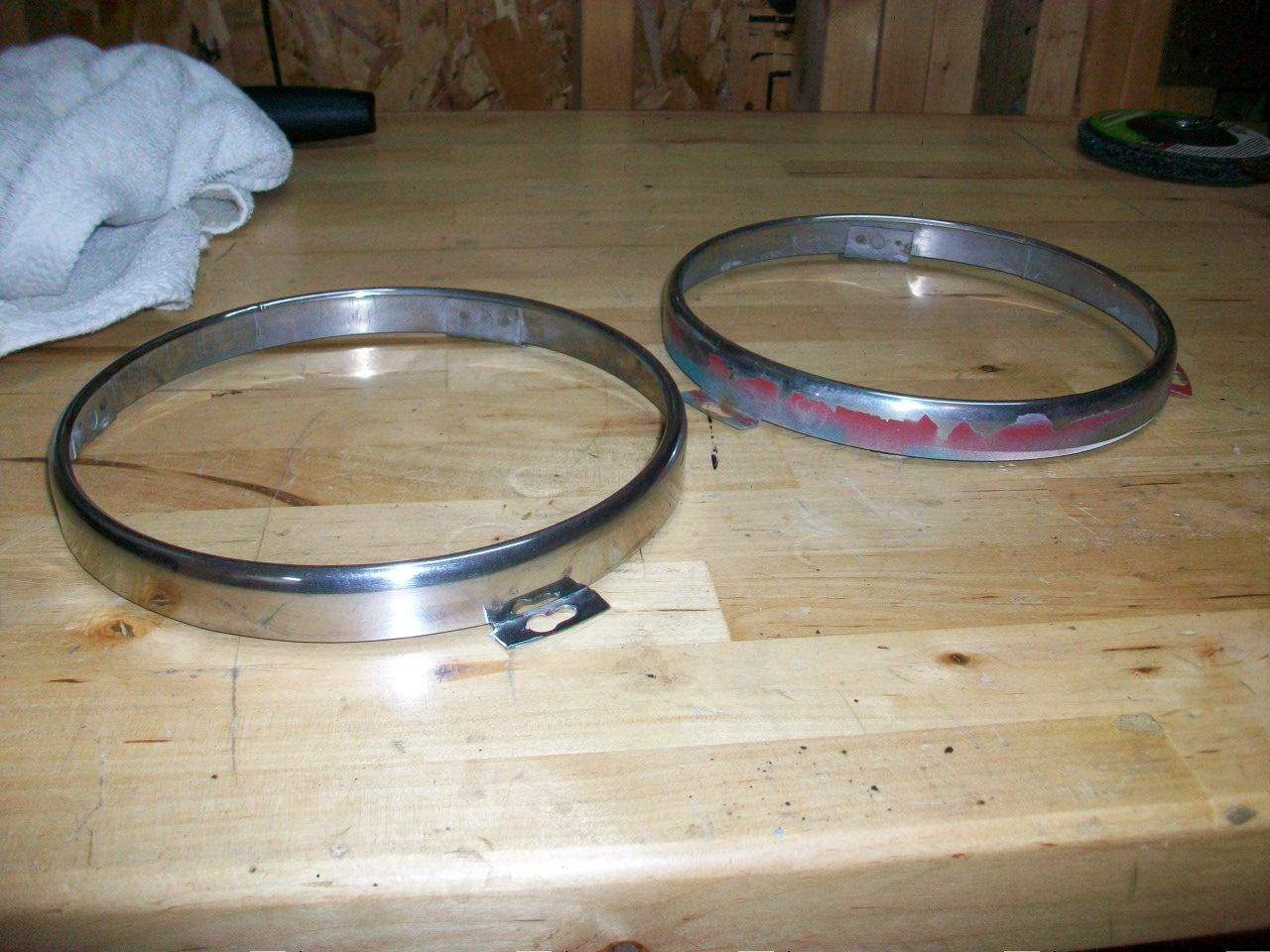
Before it got dark I decided to drag out that passenger fender and the sandblaster(s) to the yard and get some of that white paint removed. This was an excercise in futility. I had replaced the pressure blaster nozzle with the largest nozzle that TSC had (that is where I got the sandblaster from a few years back) and did not recognize the fact that the black diamond I had in the pot from before was 2040 - way too coarse. It kept clogging up obviously.
So, I whipped out the siphon blaster that has regular sand in it since it is only a spot blaster kind of thing and that was pretty slow, although there was no worry about heating up a panel lol! 
I am going to have to buy the finer grain Black Diamond to get things going on the sandblaster, but whoever had the idea that the white part of the body needed to be taken down to bare metal was right on the money. It looks like there is a thin layer of surface rust underneath the paint layer in places. The sandblaster cleans that up nicely.
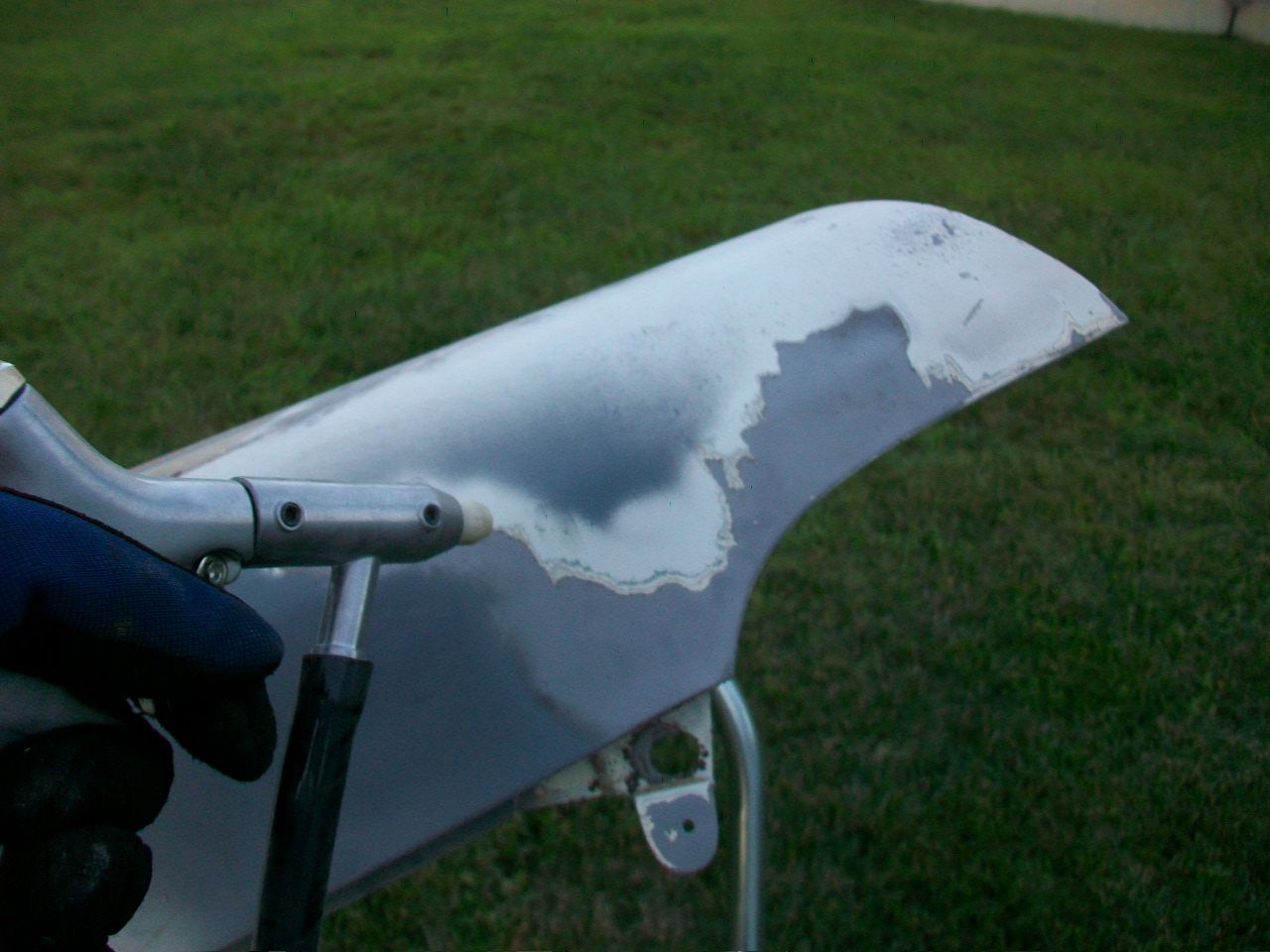
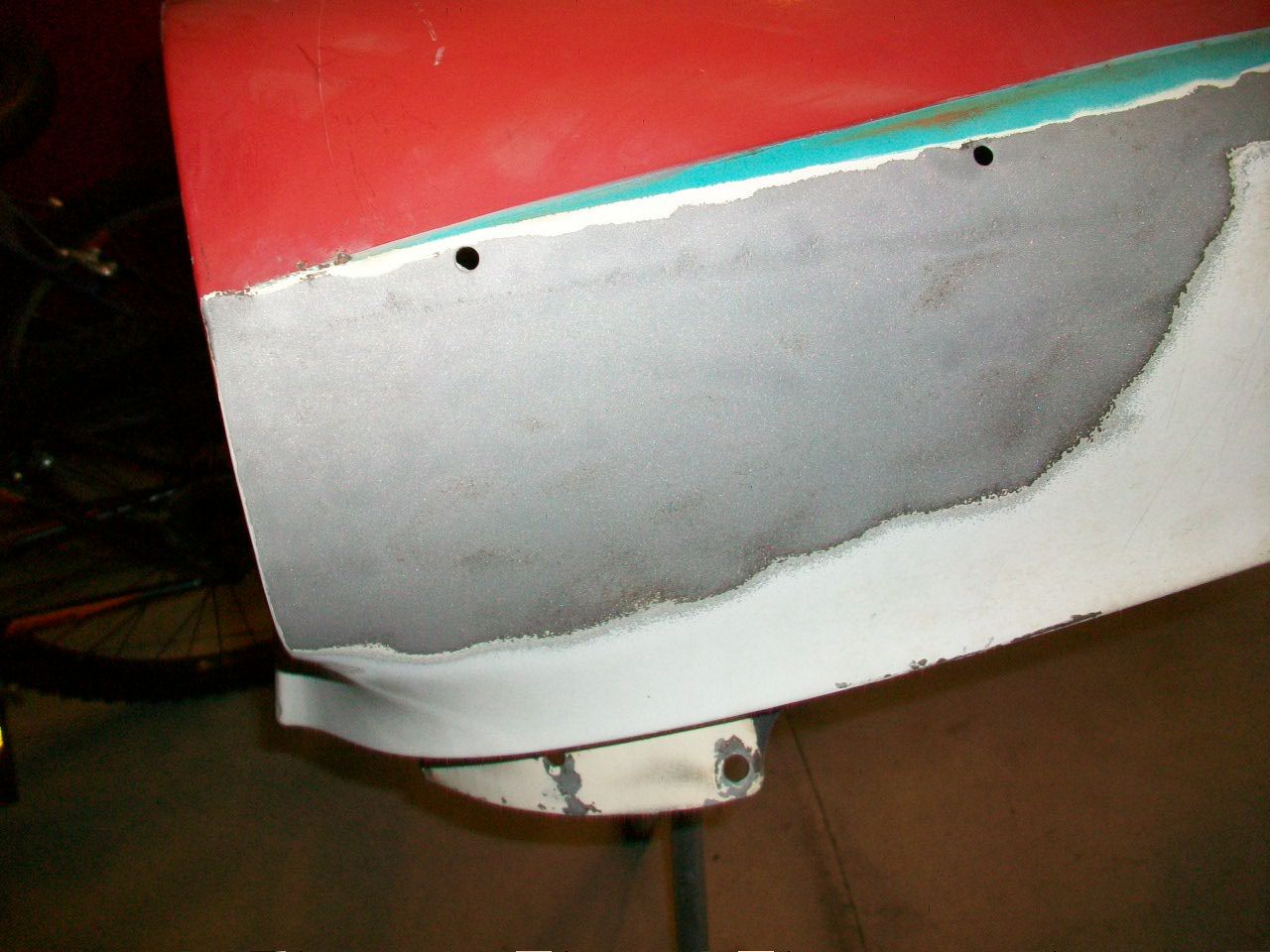
"On with the show..."
|
By Daniel Jessup - 9 Years Ago
|
We had some time on Monday night to get in the garage and do a little bit... and lo and behold a good lesson learned!!! :eek:
Check out these photos:
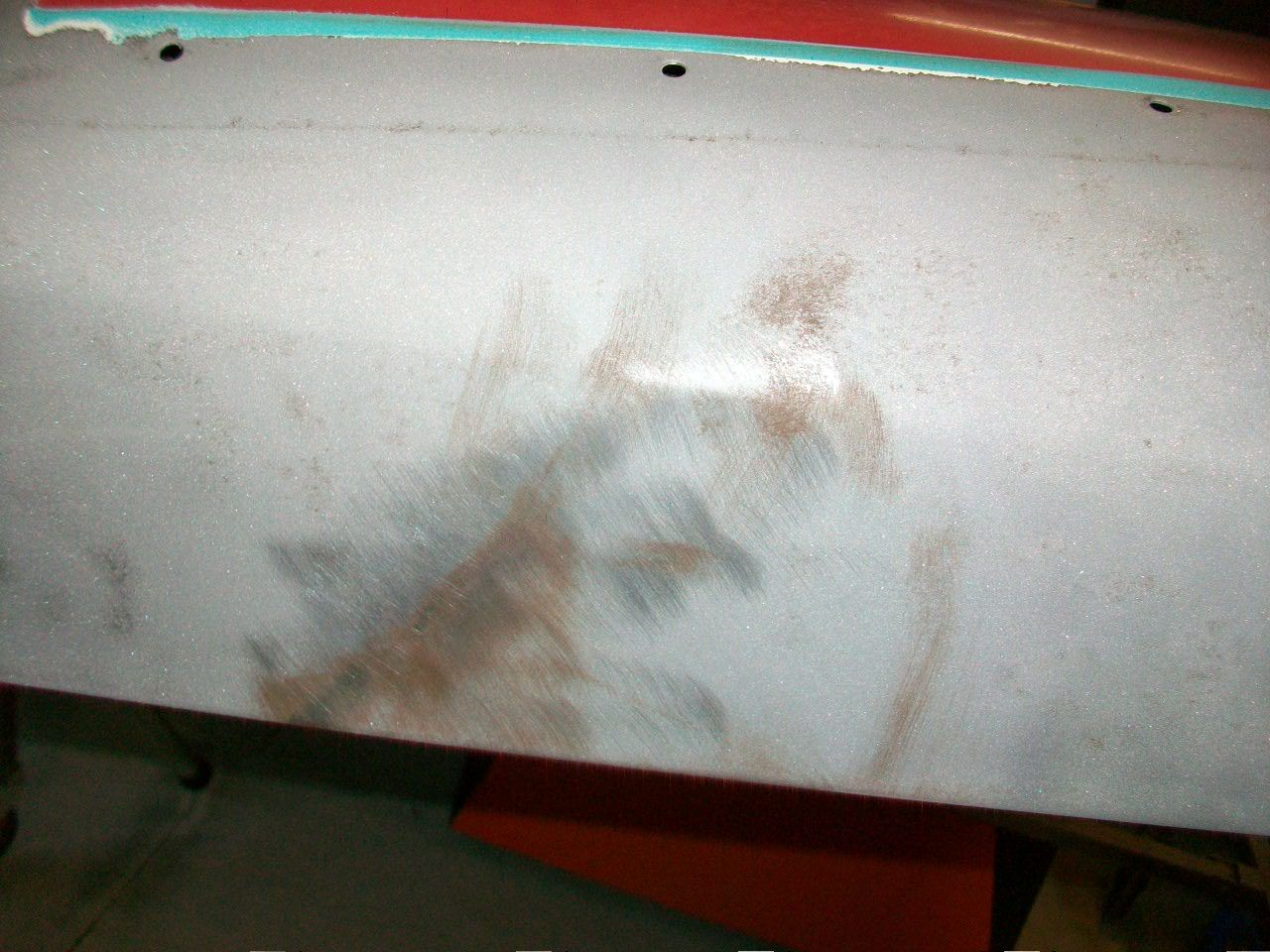
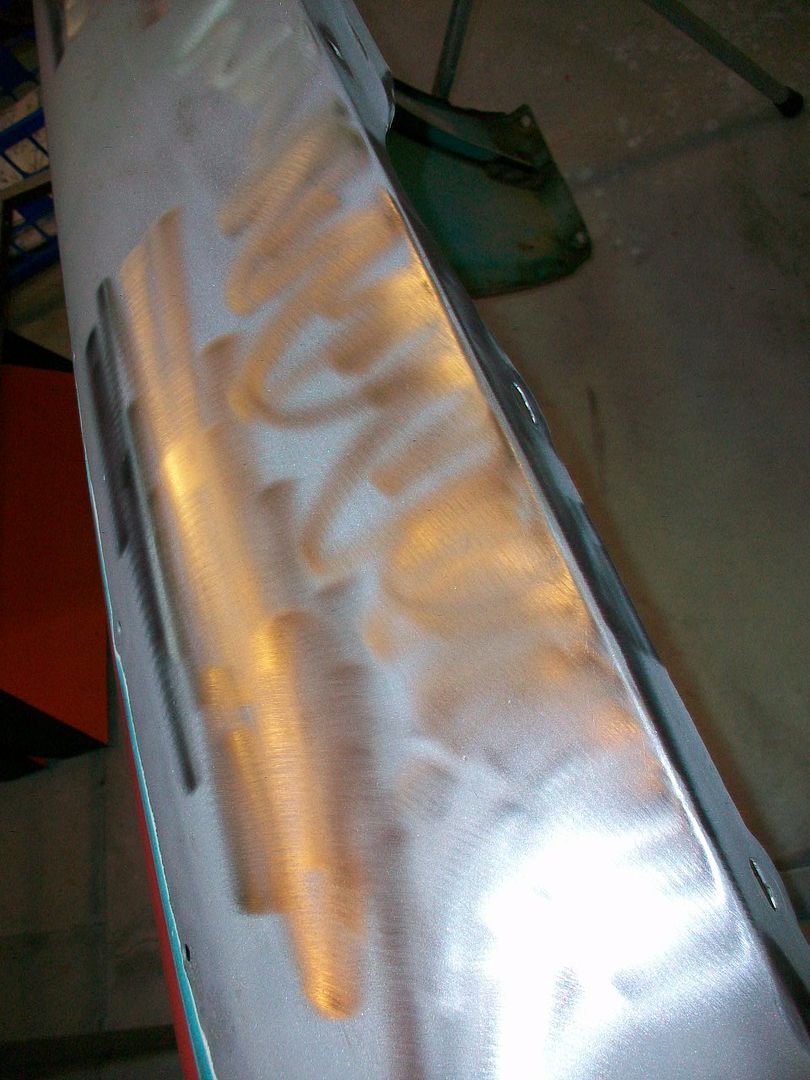
Yep, I was pretty dumb after I blasted this fender - got my sweaty hands all over the freshly cleaned metal and after a few days surface rust began to show. :mad: Just a couple quick shots with the grinder though and it's gone. I've got to get this thing primed soon. And of course, it always go to show - keep that metal clean and dry. Hopefully next time I will remember.
This passenger fender has a small problem with it's lip up front.
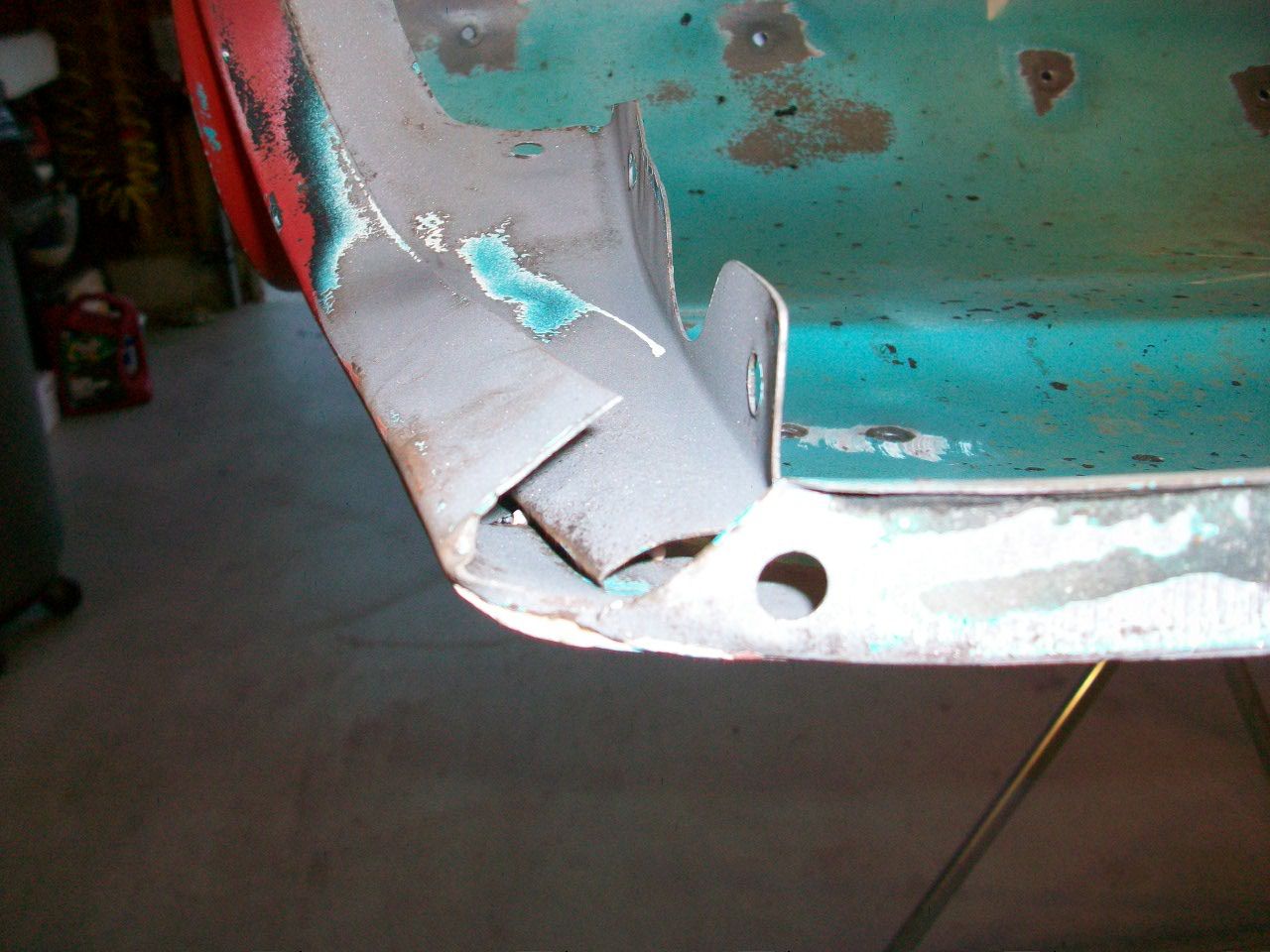
The original spot welds had come apart. This lip does carry some significance since it is in a place where the front part of the fender bolts to the air dam so the pieces have to be welded together to proceed. I drilled 3/16" holes in the overlapping sheet metal and got things lined up with a couple of my handy-dandy vise grips... these things are just the ticket. I probably have 8 or 9 different sizes, shapes, and ends with these things.
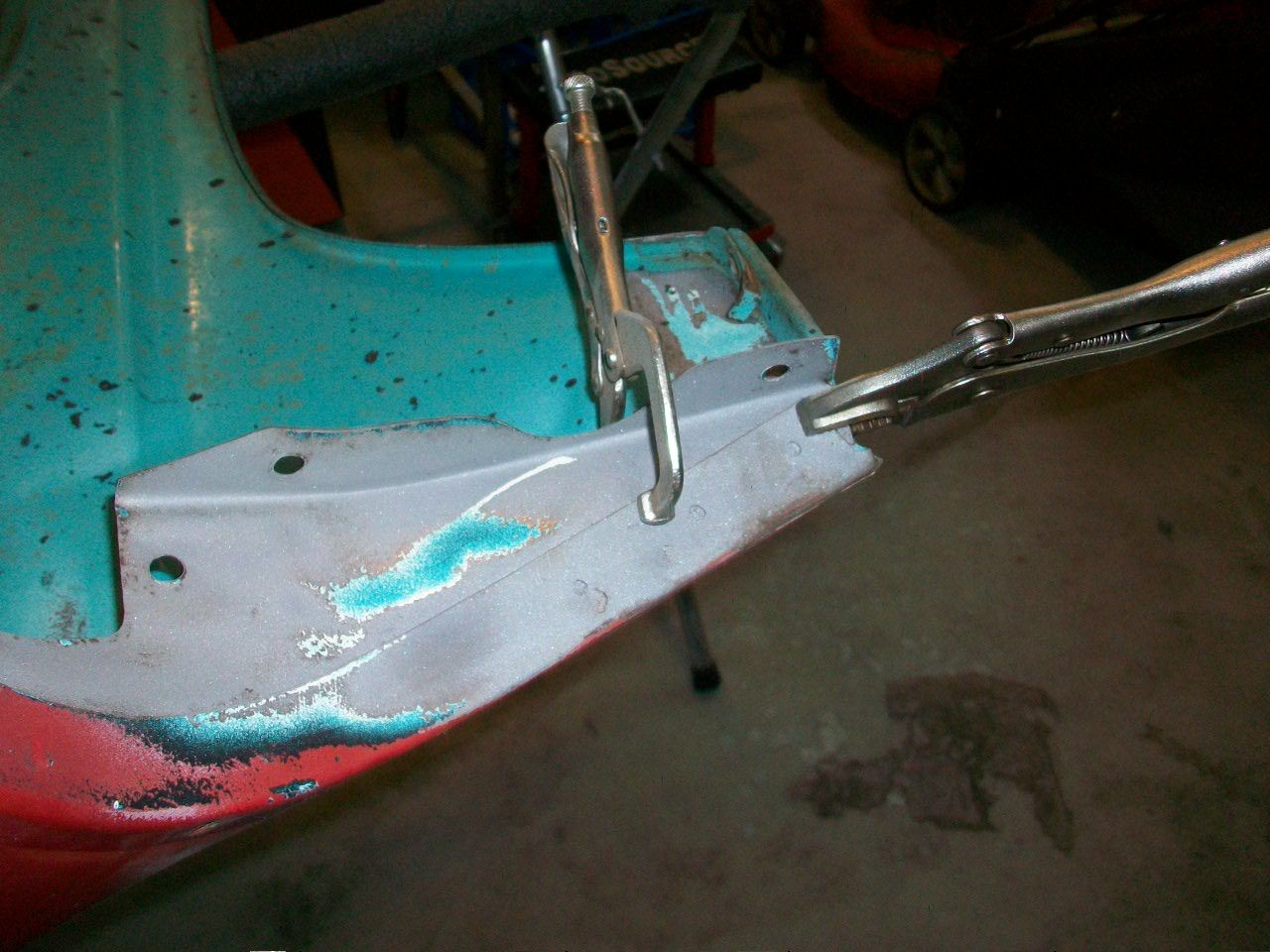
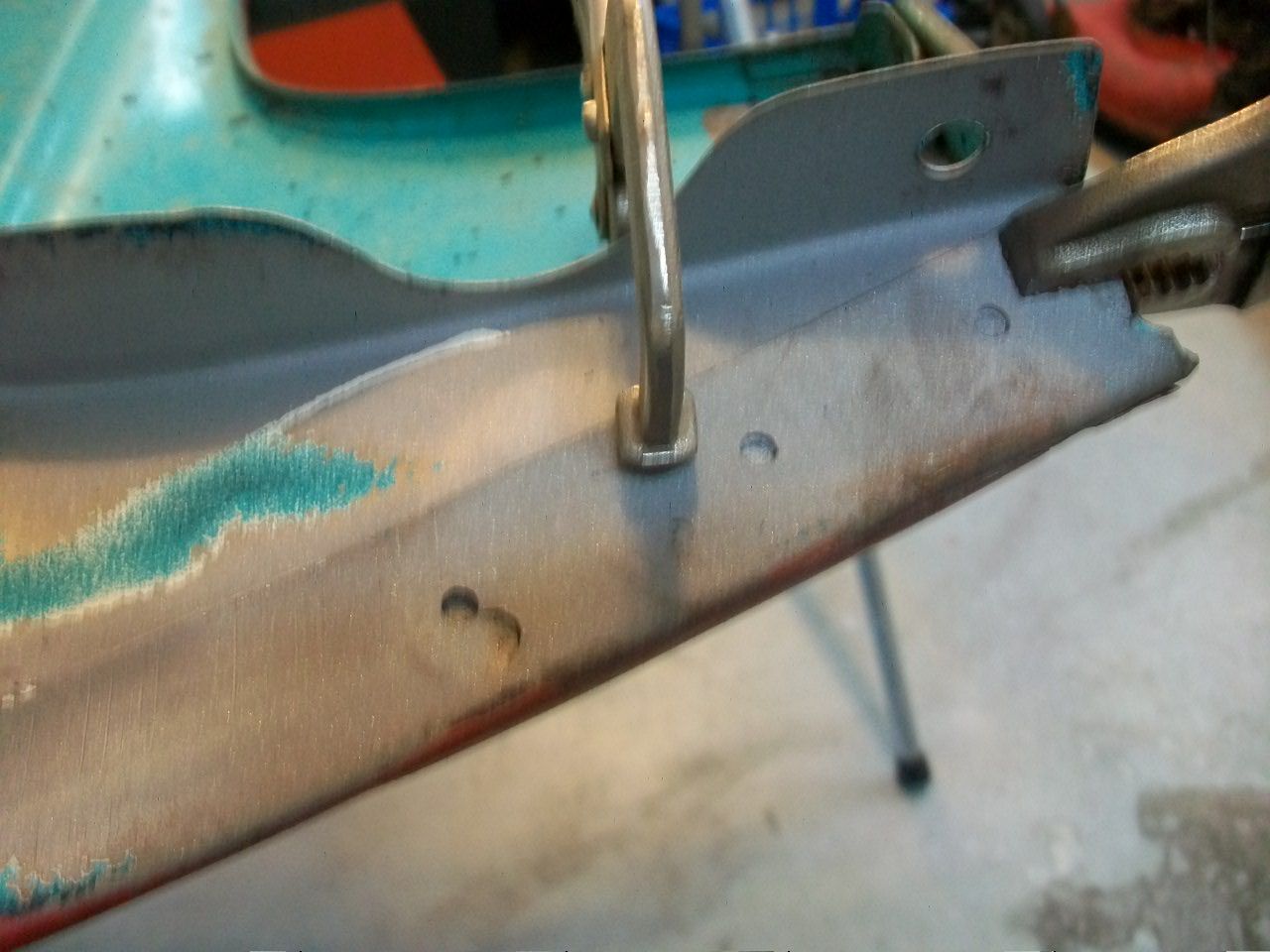
Aaaaaaaaaaand if you check the following photo you will see another lesson learned.
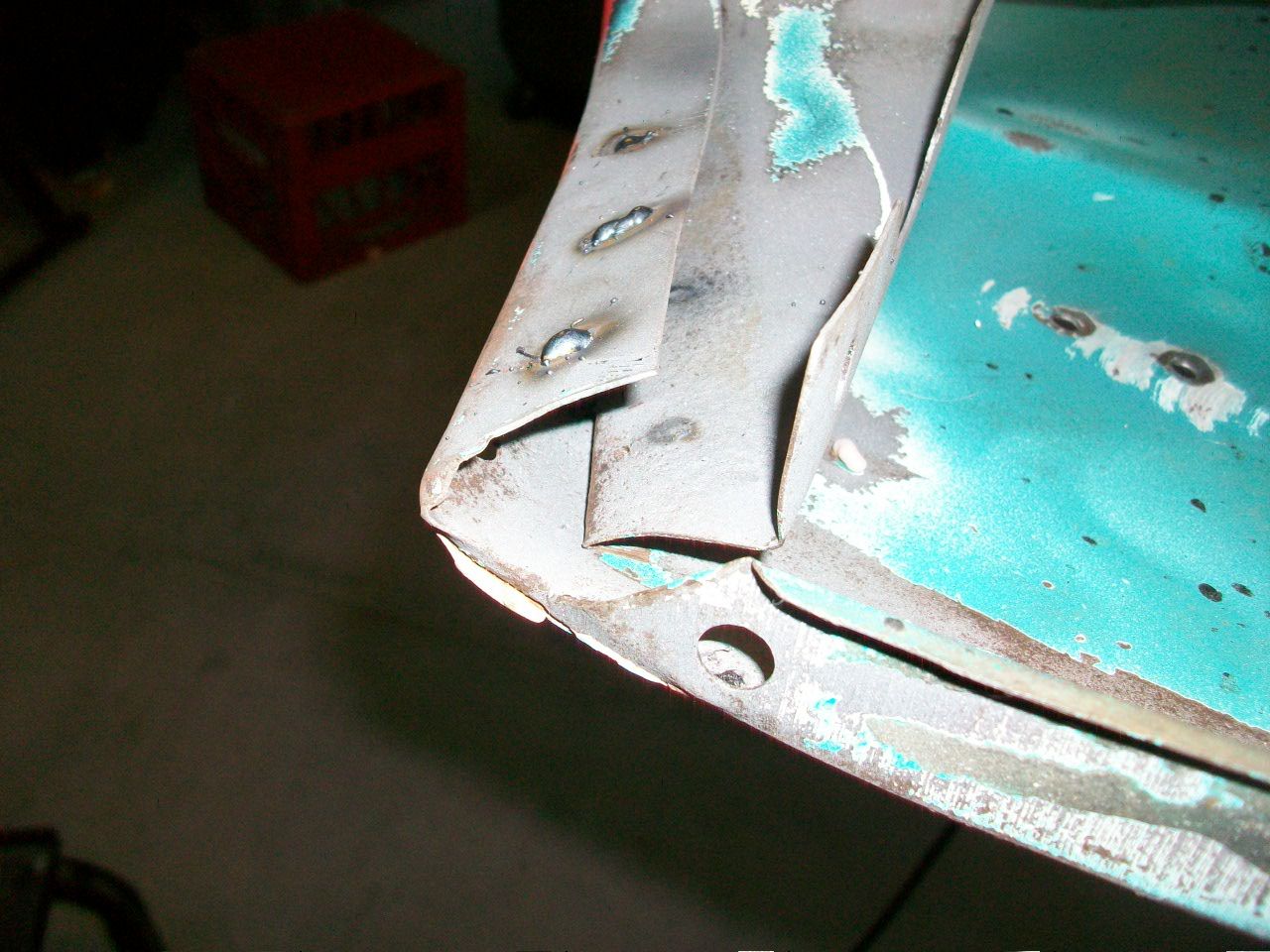
TURN UP THE HEAT! you can see in the photo above that my "welds" did not penetrate, and off popped my lip. So we ground down the proud welds, redrilled holes, and then ended up with this strong repair.
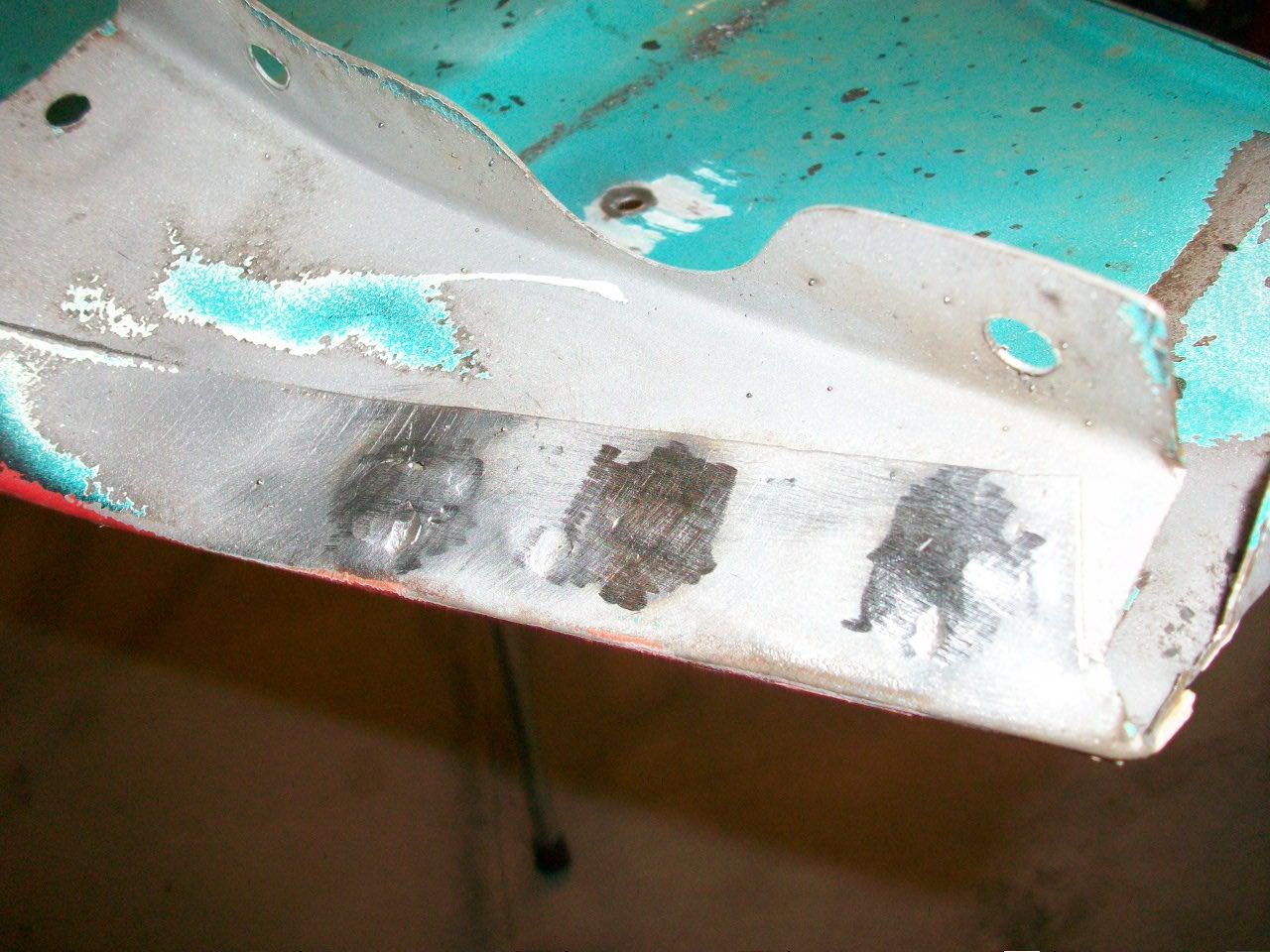
Next, it was on to the horns. What a fun way to wake up the neighborhood. First we did a simple test of each unit to make sure they were working. I broke out the battery charger and hooked up each horn. BBBWWWAAAAAAAHHHHHHH away we went. No problems there. Just a couple of neighbor's lights came on in the bedroom next door! :p
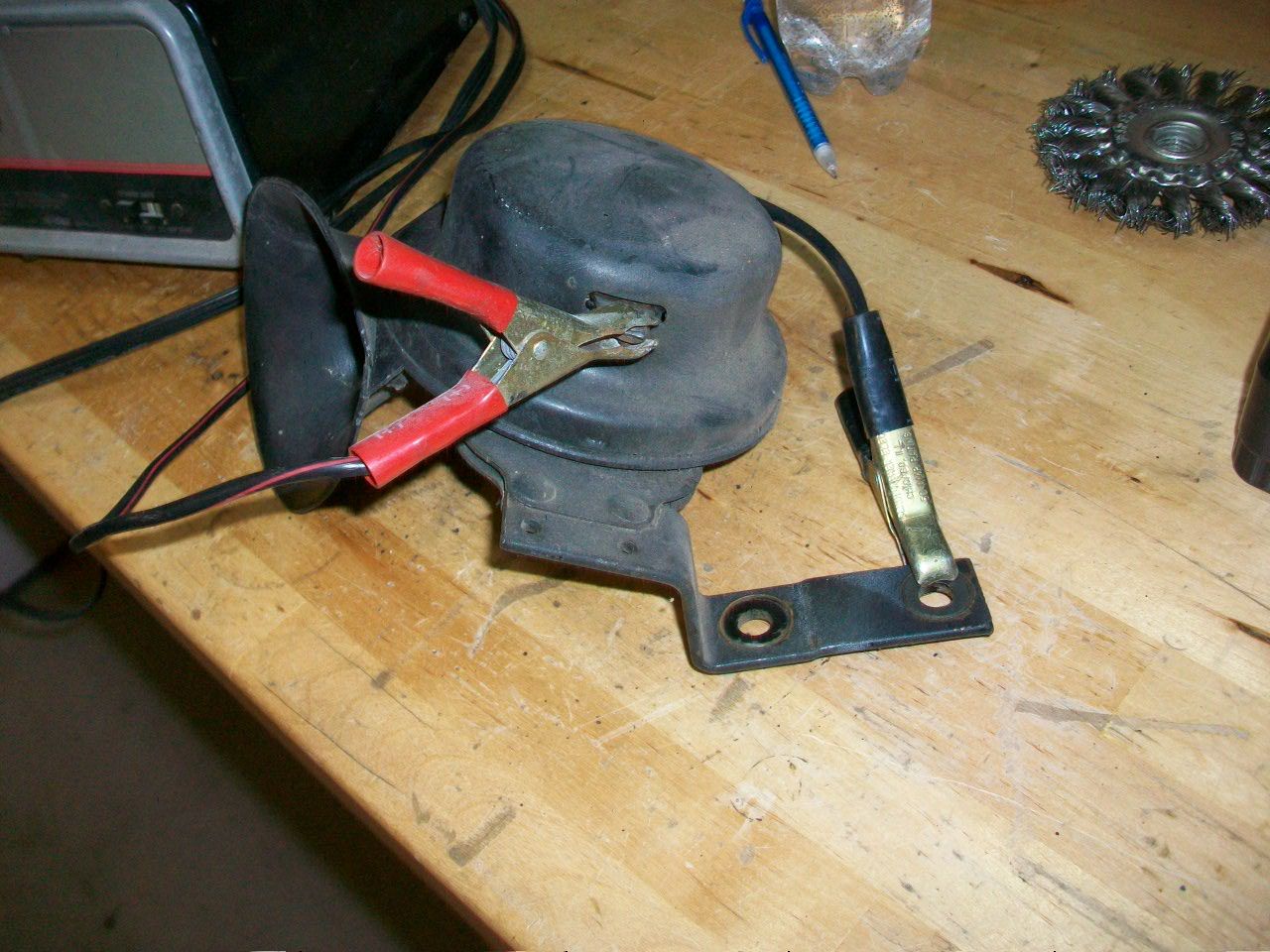
By they way, if you are putting together a basket case, make sure you have a set of Hi and Lo horns. You can find the "Hi" or "Lo" stamped somewhere on the horn itself. Of course, you can also listen to each horn and see what you have too. Note the "Hi" stamped on this horn here...

Next would be to disassemble each one. Basically the bracket just unbolts from the side. I like to either zip tie the hardware to the bracket as shown before blasting, or I use a cricket tube like the one in the picture. That way, nothing gets lost and it is easy to hold in the cabinet!
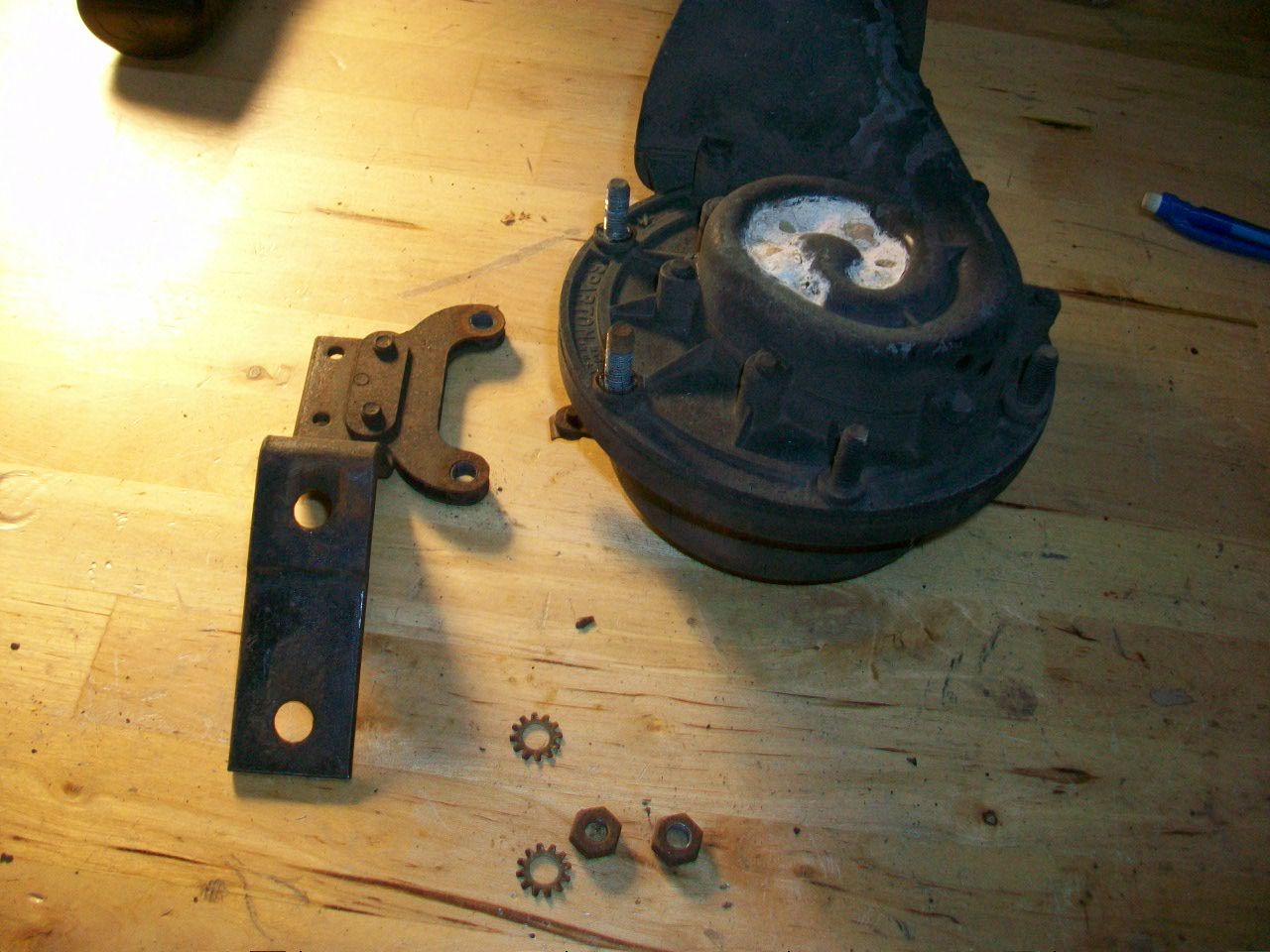
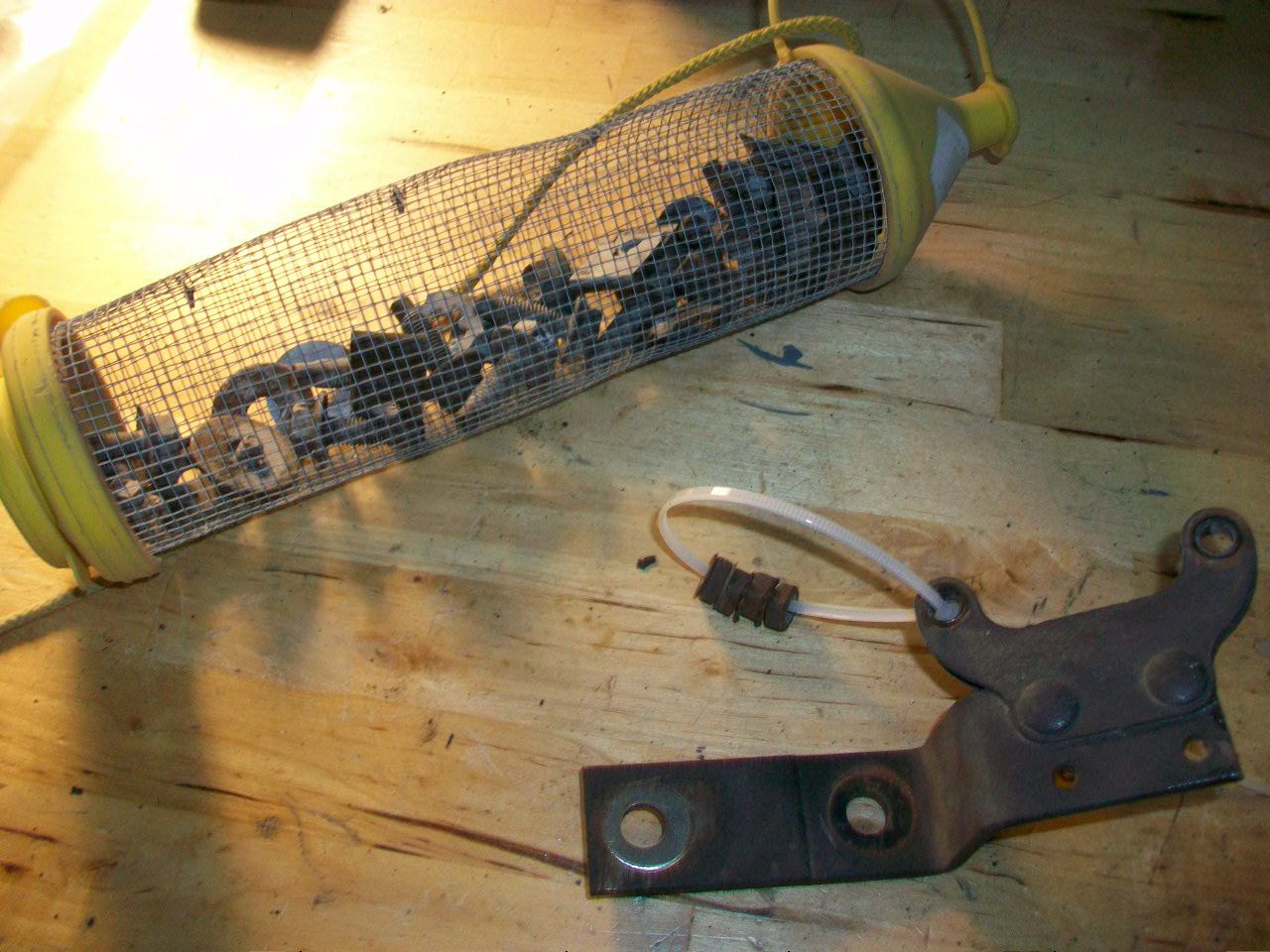
After you remove the bracket, go ahead and remove the cover. You should have a place on the cover where you can insert a flat blade screwdriver and simply pop it off.
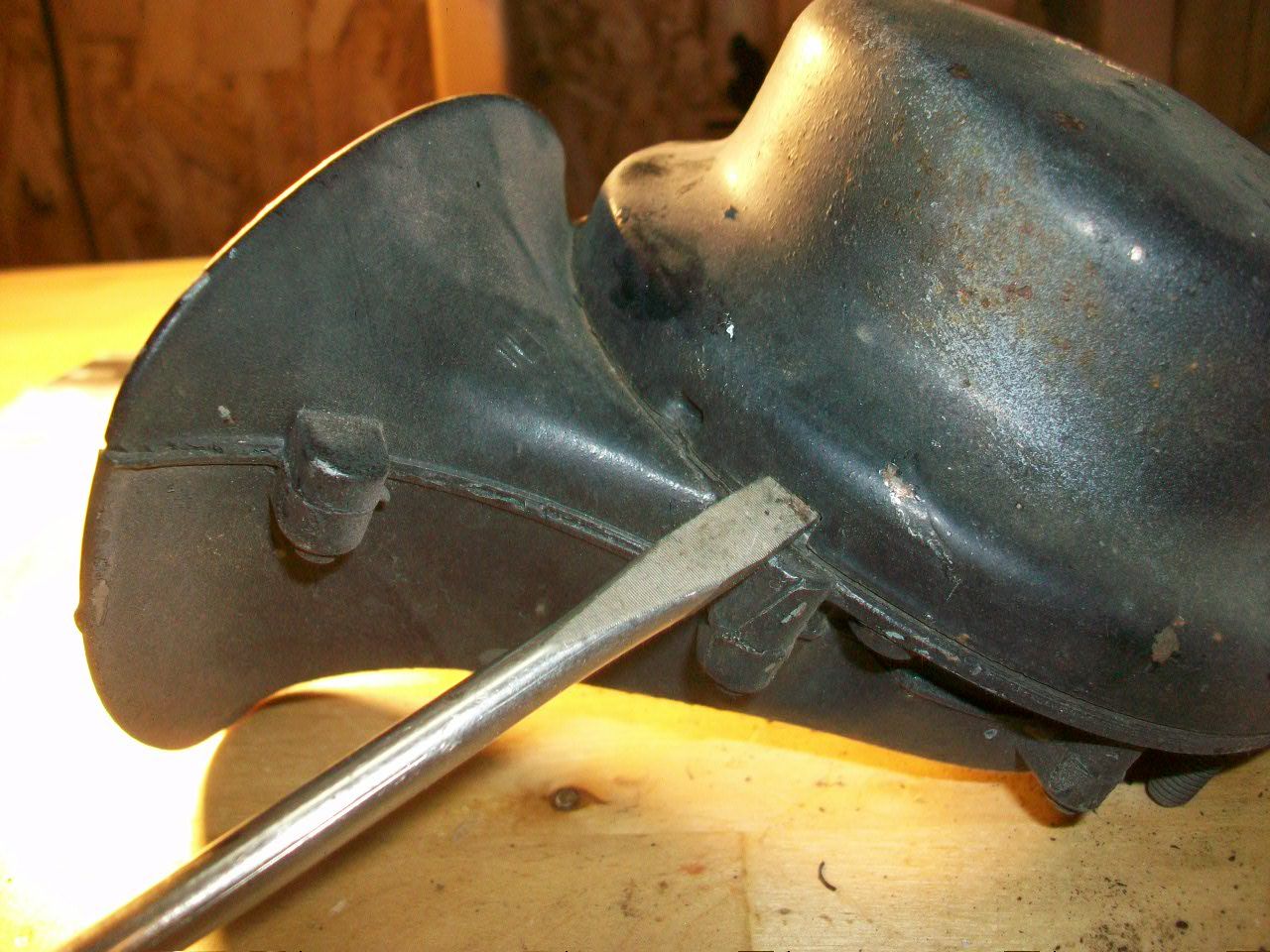
When I removed the covers, I had one horn that looked to be in really clean shape, and the other one had a little corrosion.
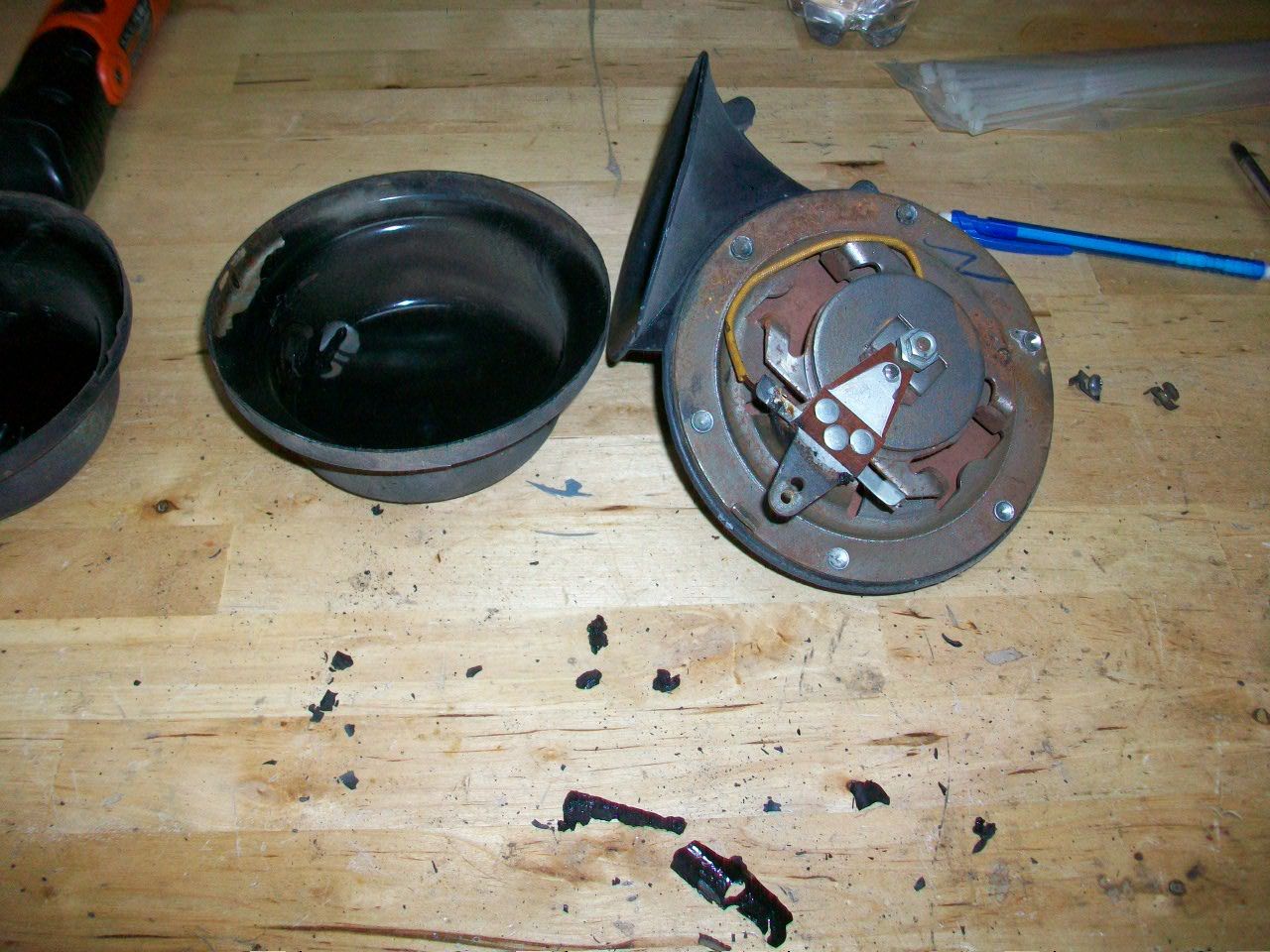
The difference? This small seal that goes in the slot in the cover where the "hot" side of things hooks to each horn. One seal was intact... the other was disintegrated. :confused:

I took the cover and the bracket/hardware and blasted them. But the horn assembly I basically took a wire wheel and other hand-powered instruments to clean so that no debris got into the contacts and what have you. We will paint these horns with Rustoleum Semi Gloss Black, make new seals and affix, and reinstall soon. 
Another small detail down, many more to go!
|
By Daniel Jessup - 9 Years Ago
|
Time for a "bondoscopy" of both the fenders, and the diagnosis/discovery ain't good. :mad: But it could be worse! 
When you notice some signs of cancer we just know how we can be.... keep digging until you find all traces. But little did I know I would have to grind away about 3 gallons of body filler and other "imitation metal" products that a would be body man used to form 55 Ford body panels. Oh my... check it out.
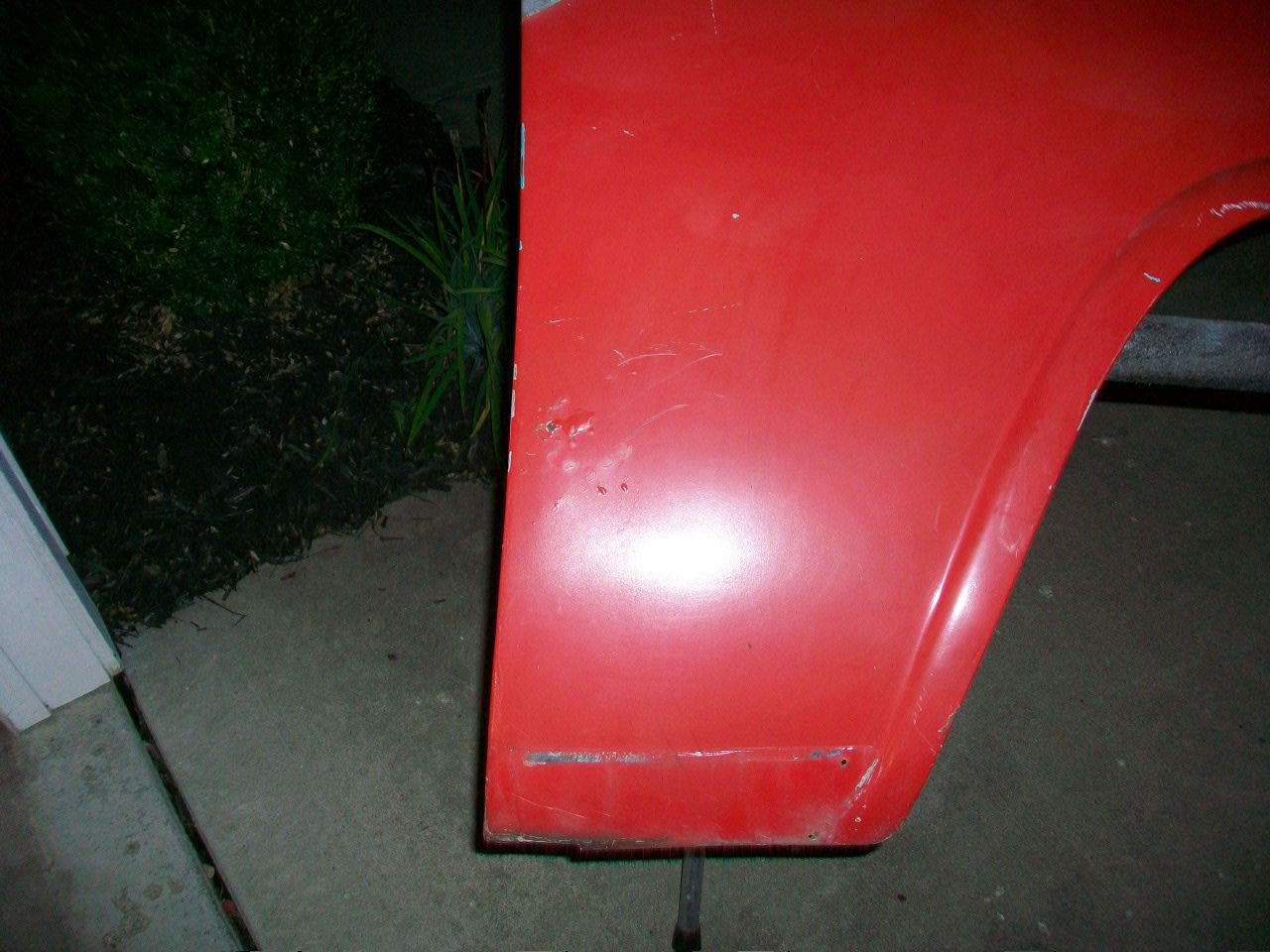
Both areas showed some sign of problems, so time to grind away...
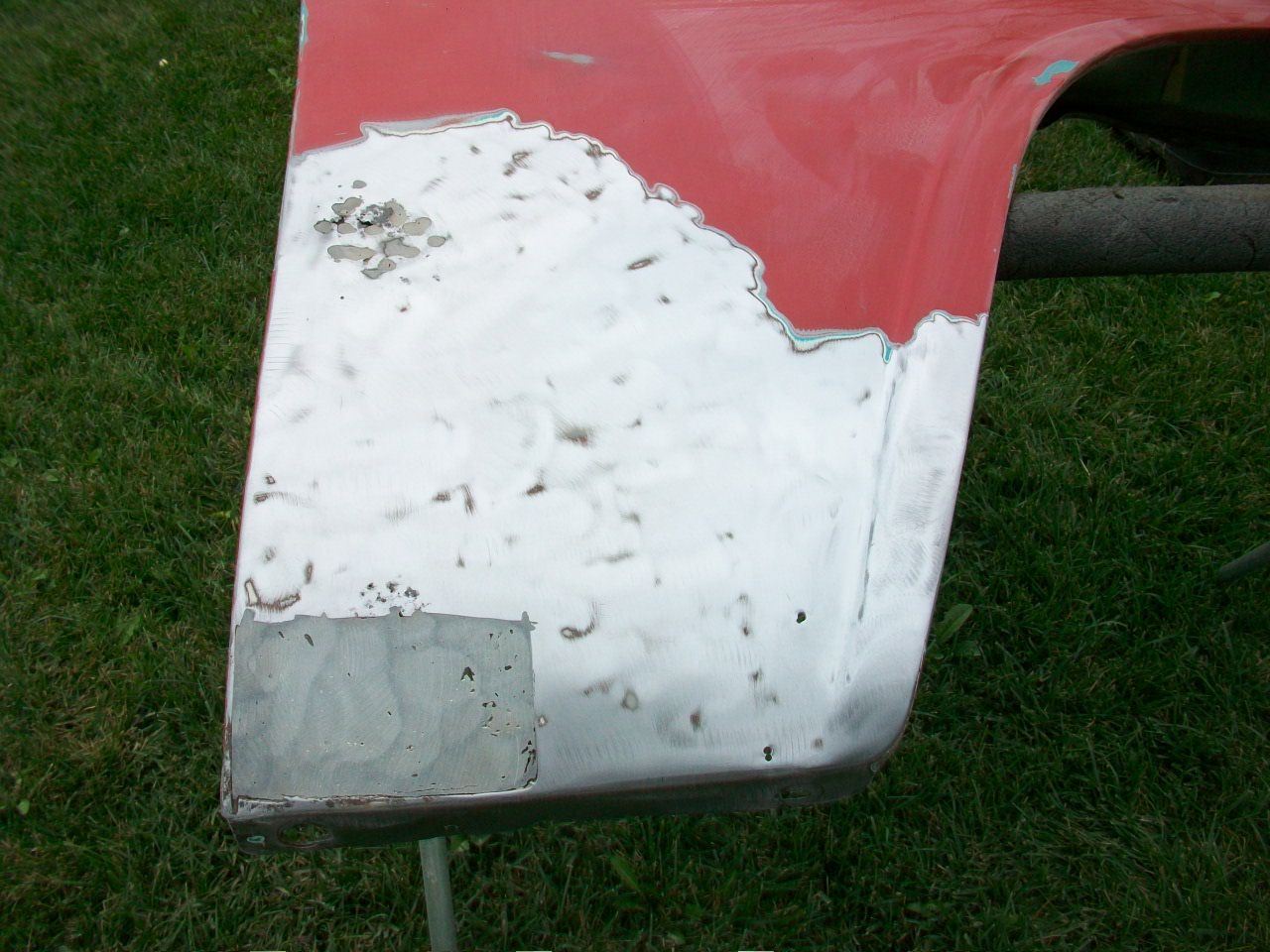
what this gray stuff is I do not know, but it was a different texture than the body filler like the Bondo brand and this stuff was very porous. Maybe it was a part of a kit to "build your own backyard body panel" from the 1980's - I have no idea. You can see this shot of the stuff getting chipped away...
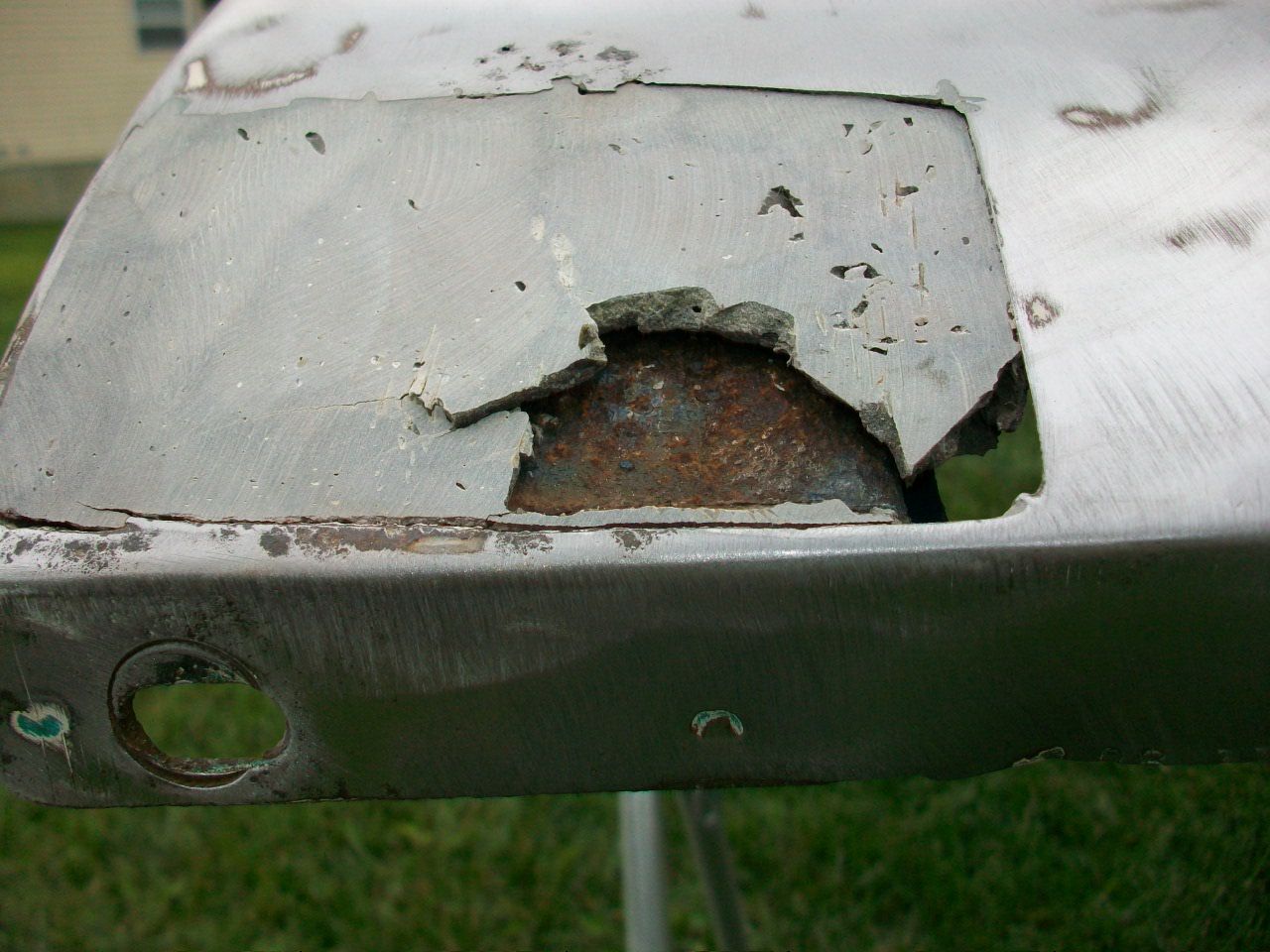
and then...
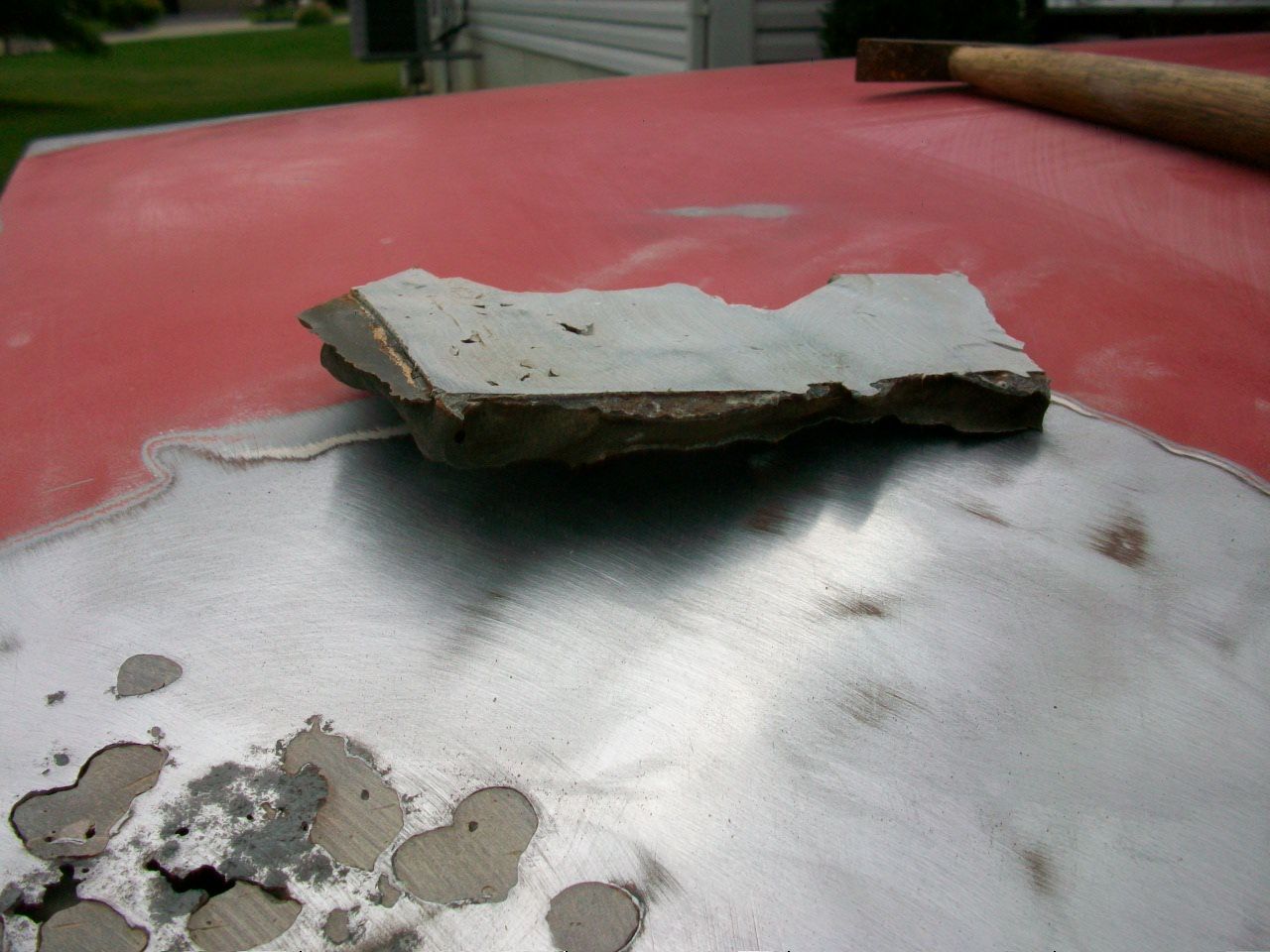
Yes my friends, at least a 1/2" thick in places. On top of this repair was about 1/4" of the regular Bondo brand filler and then primer surfacer, then primer, then base coat. Anybody know what this is? It is still "pliable" - in other words it was not really brittle and was still flexible. It did grind away with a lot of dust like regular body filler.
So we did the driver's side fender too, and wouldn't you know it, the same guy did the work!
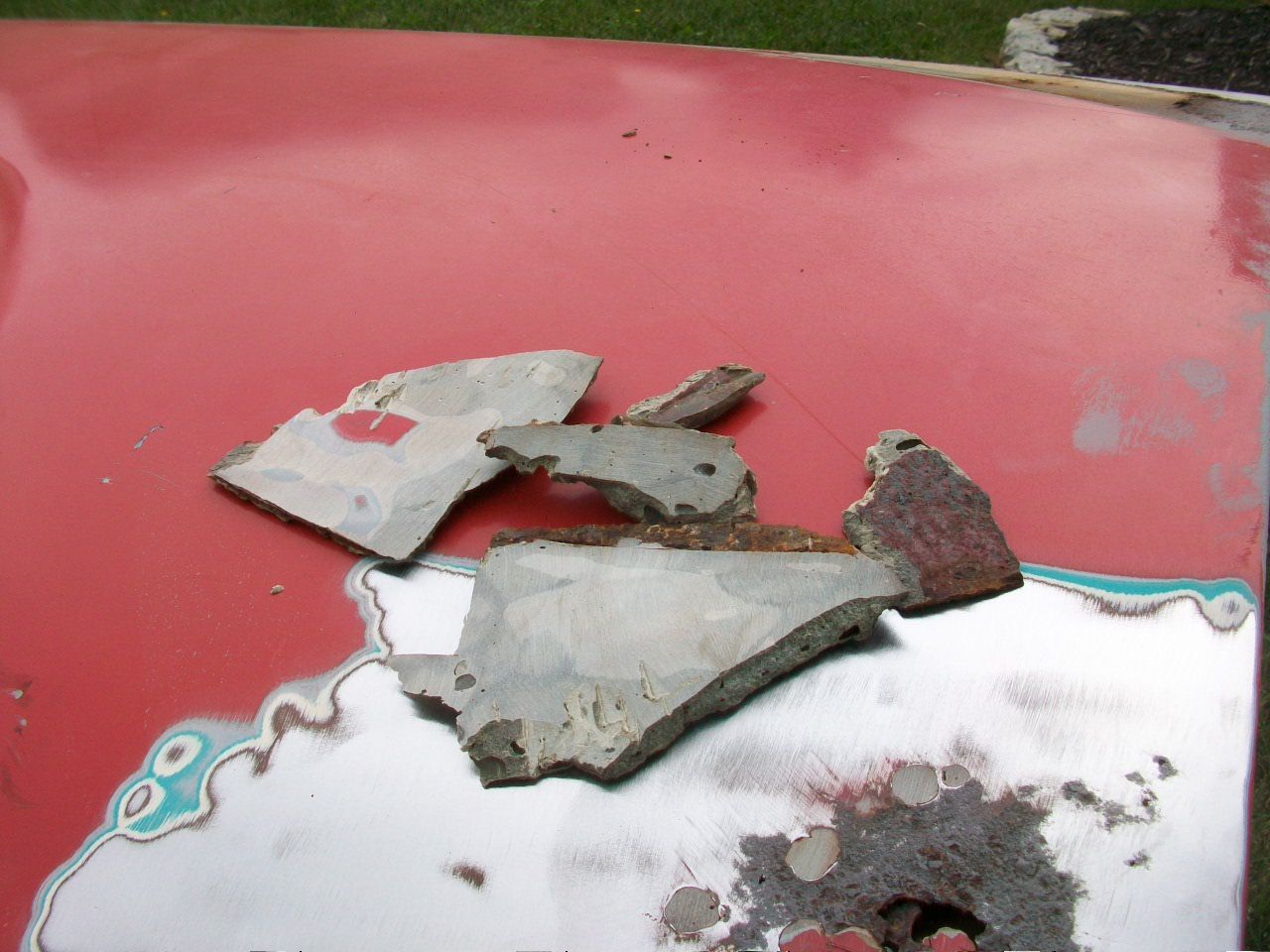
Only the passenger side had some body filler up front near the "V-8" insignia. No rot issues or anything, but it will have to be addressed to make it look it good. How much hammer and dolly I can use because of restricted access may make this one a little difficult. That lip may get in the way more than I want it to.
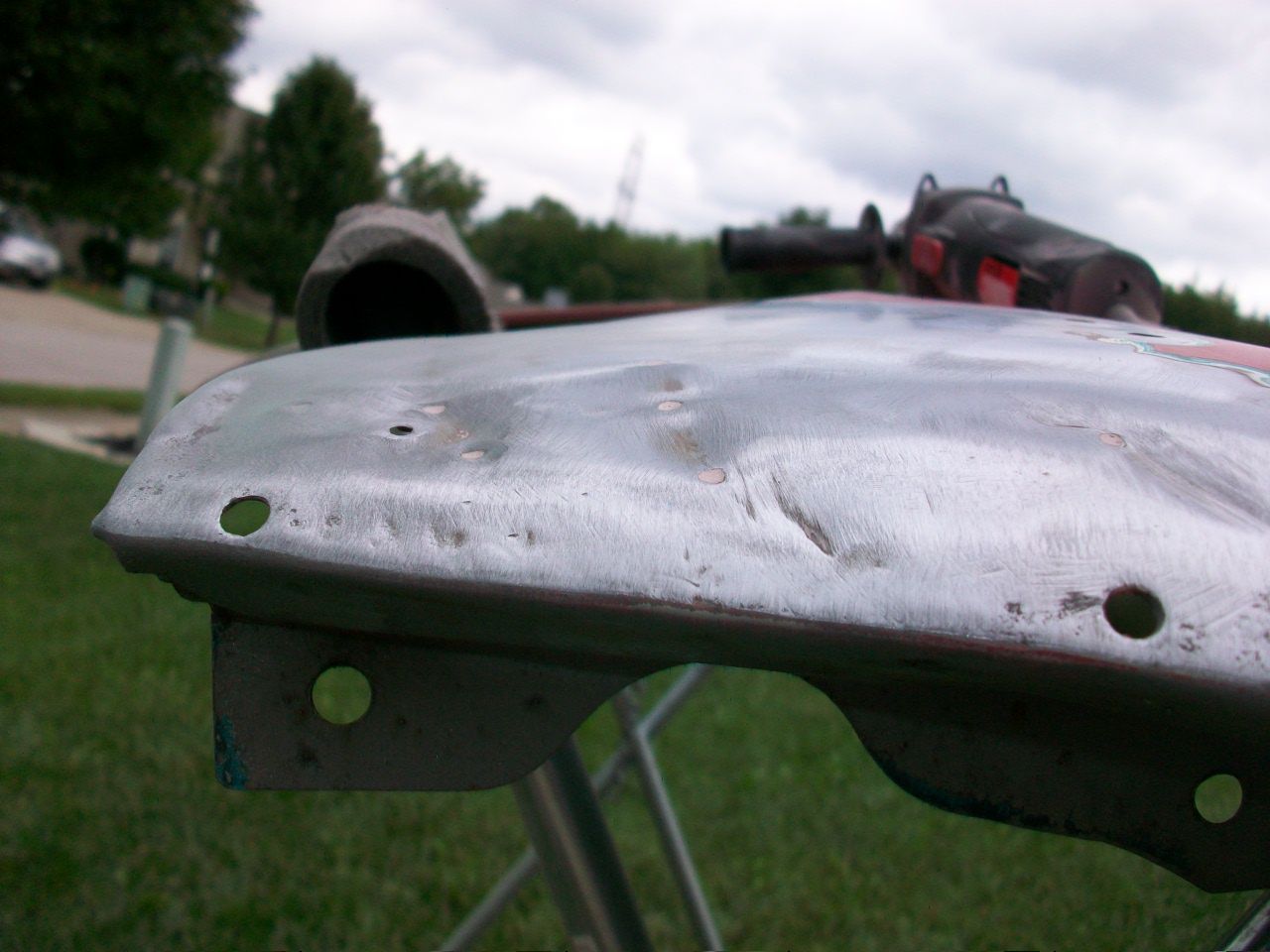
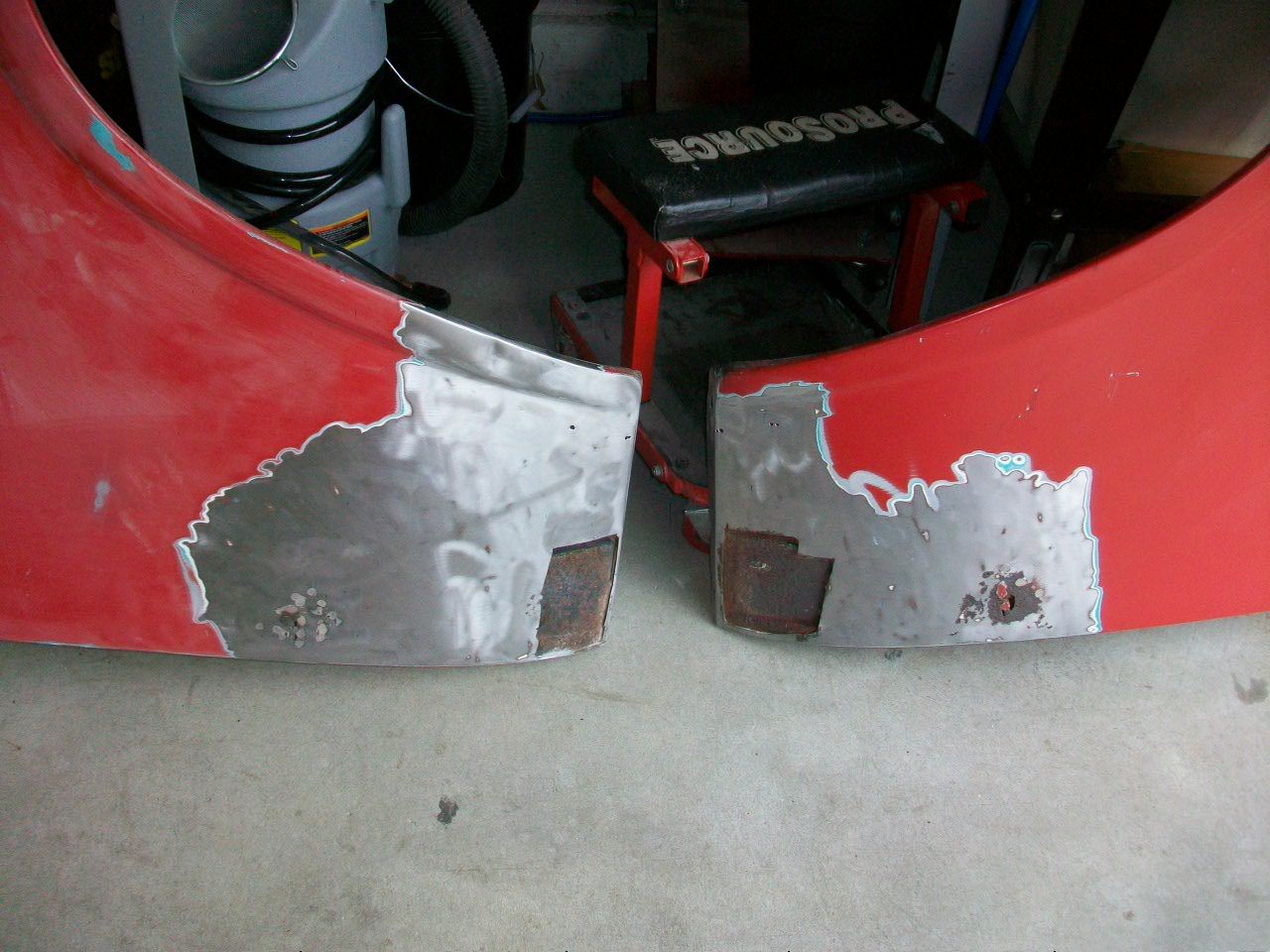
Next session I will cut out the rotted portions, blast the metal underneath as clean as possible, use some weld thru primer, weld in new patches, straighten, epoxy, apply some body filler and get ready for primer. Easy breezy right?
Learning as I go...
|
By Daniel Jessup - 9 Years Ago
|
Yep, ahead of you on that one, I wear a 3M dual cartridge respirator for that work!
|
By Daniel Jessup - 9 Years Ago
|
Not too much time spent in the garage lately, I have been traveling out more than I have been at home. I did get a chance to get in to things a little bit tonight before I head out to Easthampton, Massachusetts tomorrow (anyone live out that way? )
It shouldn't surprise me but I keep finding bits and pieces of sheet metal, brackets, etc that need to be welded up. Take for instance the gravel pan here. I had forgotten that the side piece pictured had just come right off with the passenger side fender. It looked to be spot-welded to the pan, but as you can see when I started it needed to be "straightened up".
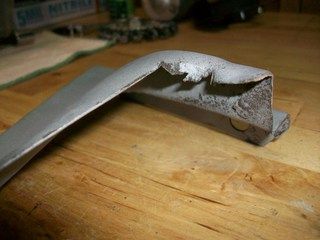
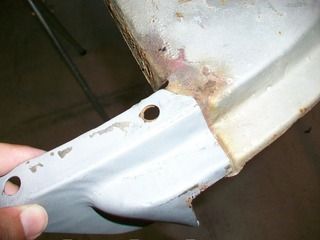
I ended up fitting it several times and doing some hammer work to get it nice and lined up. After that I drilled some small holes to the small apron piece and then put the vise grips on to keep it tight and in place.
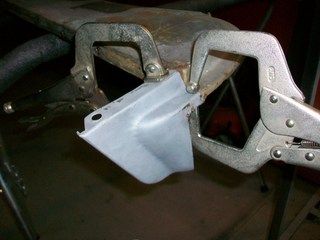
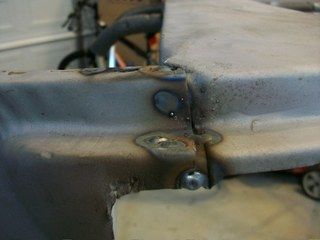
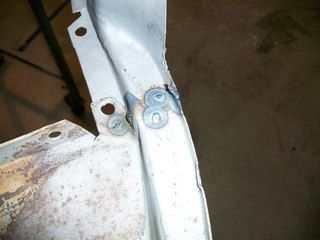
I don't think it is going to come apart any time soon. I did make sure to clean up as much of the surface rust as possible on both parts to give me a clean weld.
Next up was some blasting work in the cabinet on small brackets and the aprons that go over the top of the upper control arms.
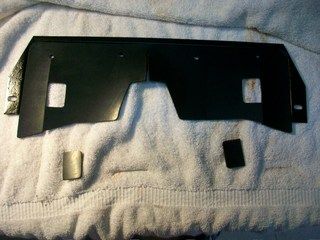
|
By Daniel Jessup - 9 Years Ago
|
These thin sheet metal flanges and the rubber was not on the 55 when i disassembled the front end a long time ago. I had to pick these up from another 55. So.... I had to find out that the flanges are specific to each side (drivers or passengers) and of course the rubber guard has to match as well. The originals were stapled, but the new ones came in without any staples. When I got to looking at, the cap screws should keep everything nice and tight so we will forego the staples on these pieces.
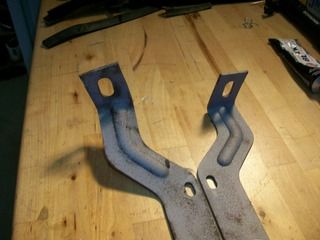
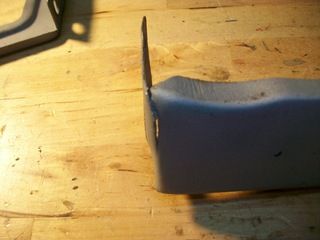
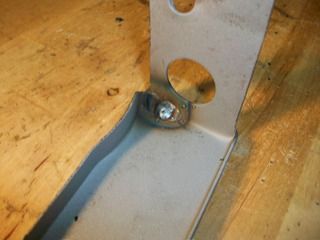
I cleaned up some of the grille and gravel pan brackets as you can see but before painting I had to weld up the cracked piece. I guess it will hold, the welds looked like they went straight through.
Got quite a bit to do... hopefully in September I can get down to cleaning up the fenders and getting that body work done. I have ordered the drivers side anti-squeak seal from two different companies, both back ordered - :confused: fun stuff.
About to place an order from C&G, but their dash bezel seals are on back order too. I guess everyone else is like me trying to get things done this month!
|
By Daniel Jessup - 9 Years Ago
|
It's been a very busy August - traveled thousands of miles literally and been in several different states. Nope, not vacation either - all work/church ministry related in training people. I have not been home very much at all. This weekend I am "off" like many of us so I decided to hit it hard with the 55 Ford and do as much as I can.
First things first - take a look at the sandblaster nozzle and stopper. Think it's time for a new one? 
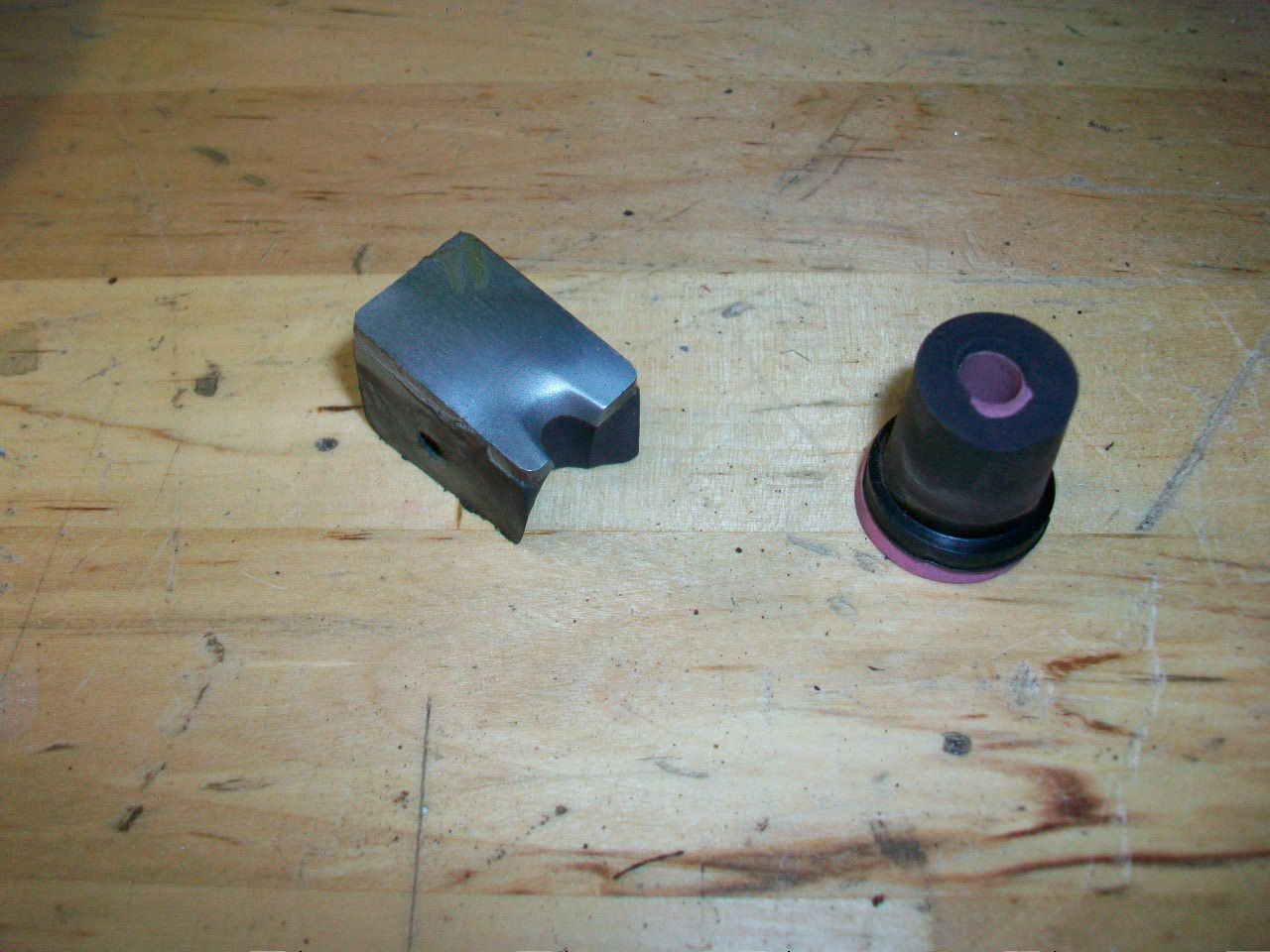
Found new parts at the local TSC and we are good to go.
On the Gravel Pan, I really wanted to find an Argent color that I could use but did not want to go the spray can route. I favor my gun as much as I can. So what to do? Let's see.... time to experiment and make our own. Here is a photo of the two colors I mated. The top is Rustoleum Aluminum and the bottom is ACE hardware gray.
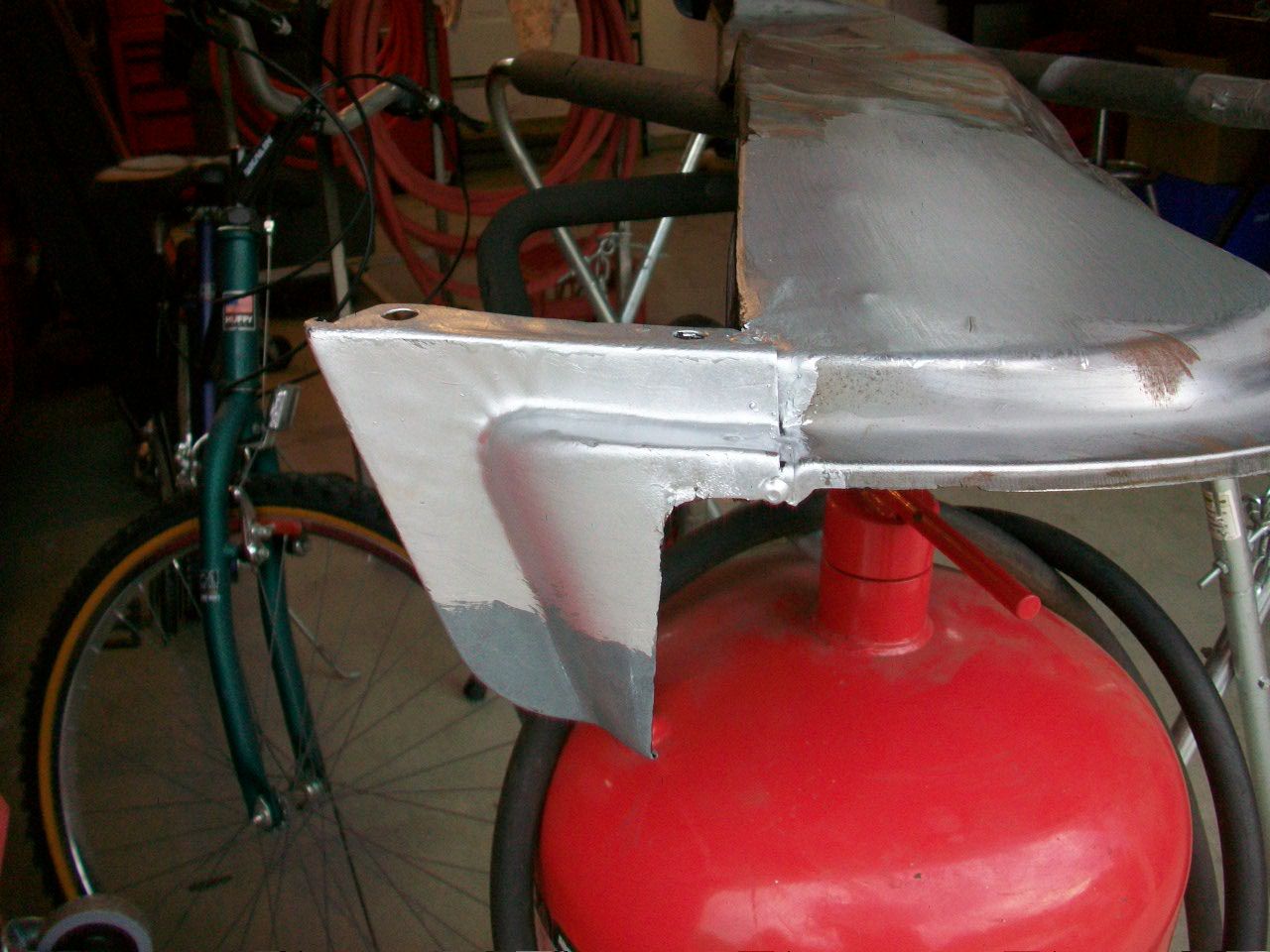
I put some of the dark gray in with the aluminum a little at a time and voila!
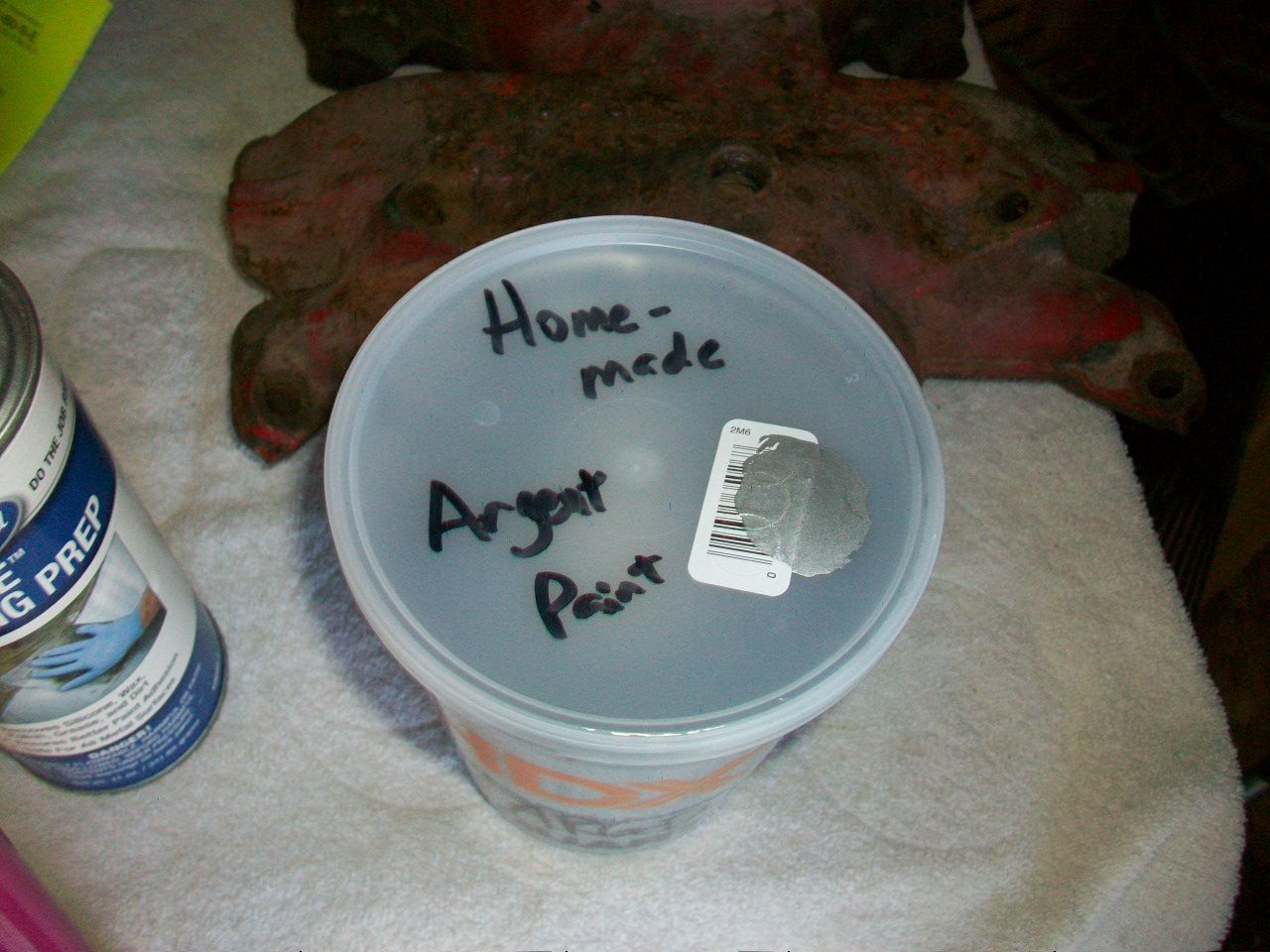
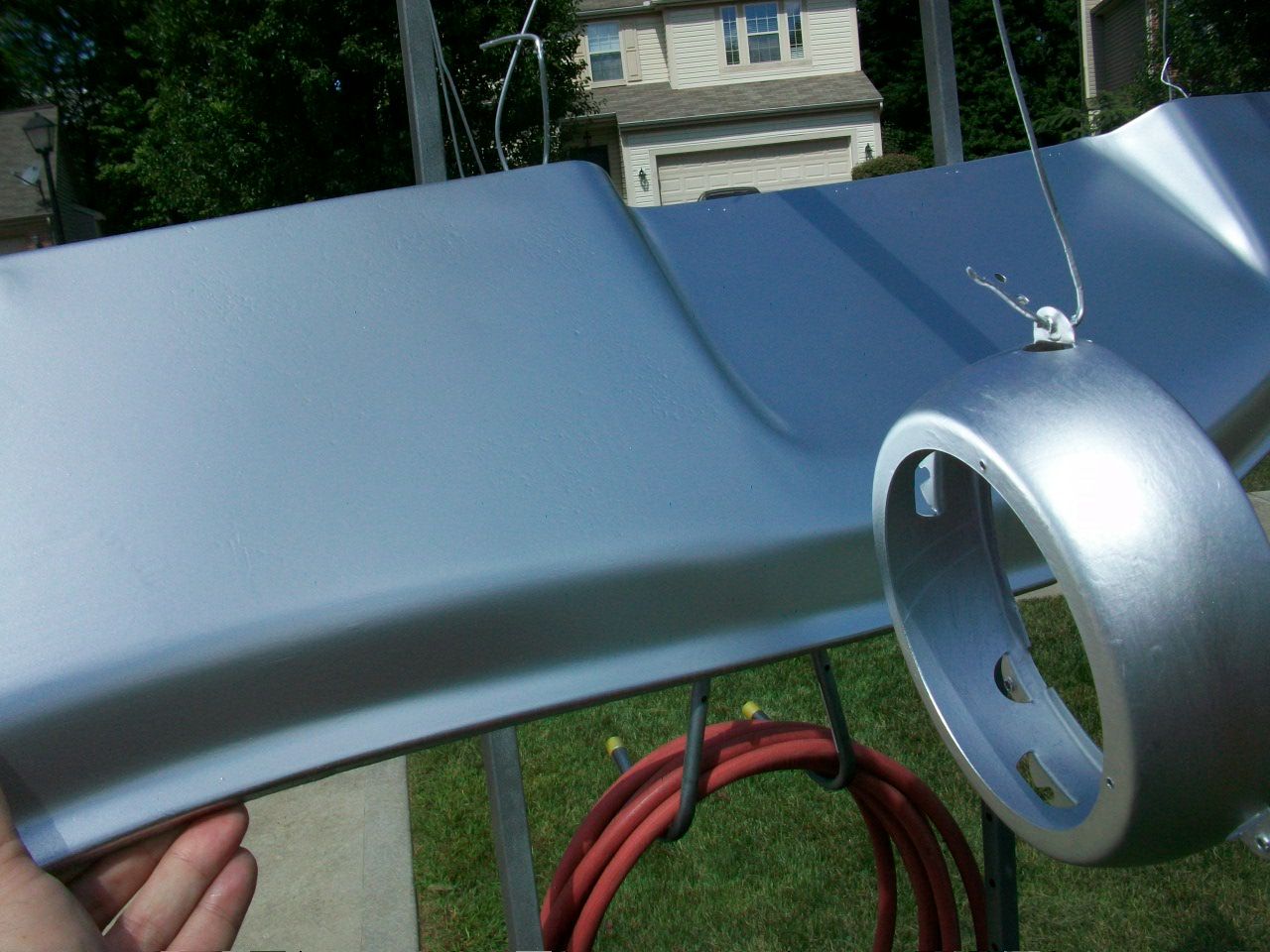
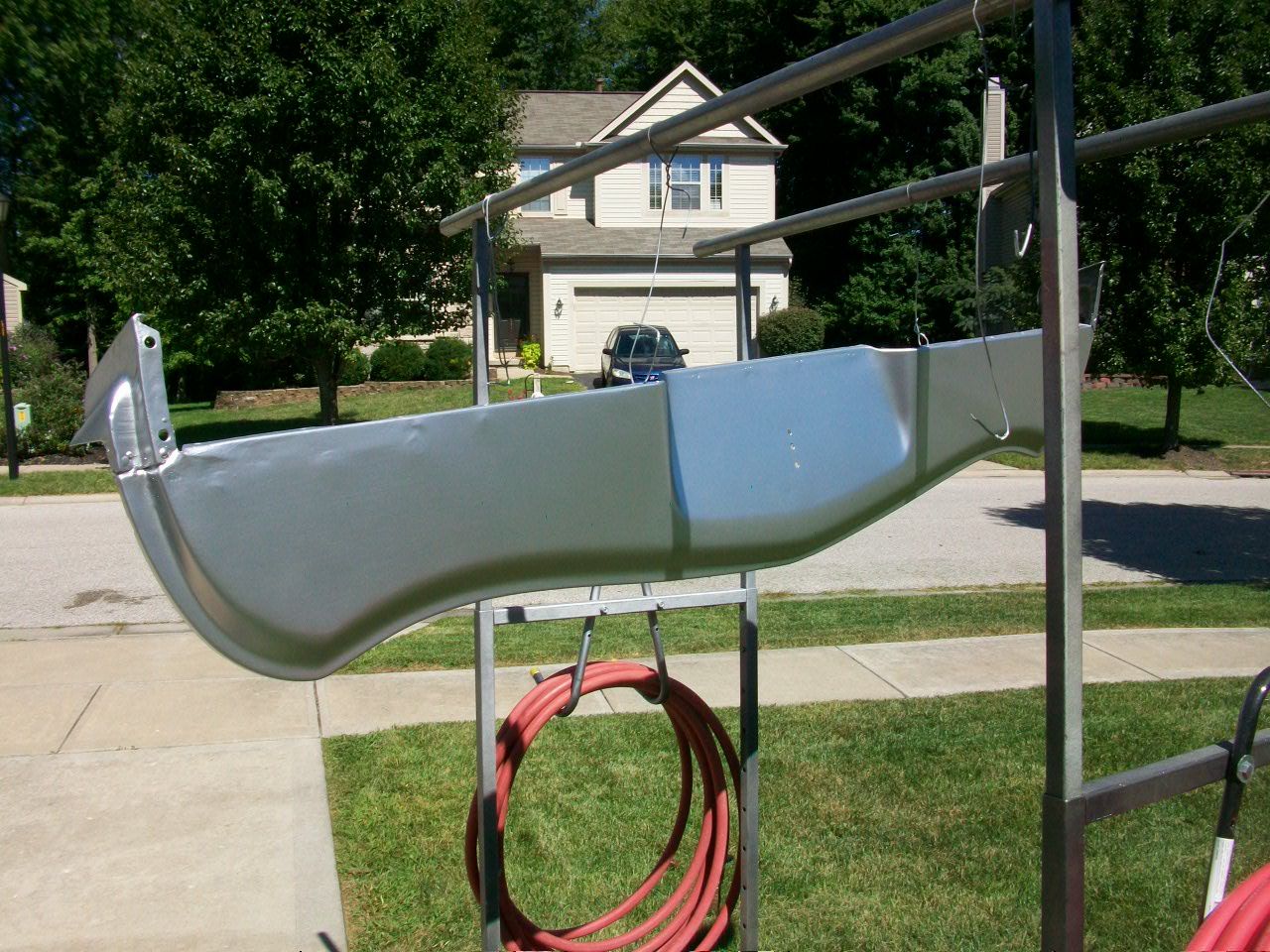
The photo of the headlight adjuster frame and the gravel pan together give you a point of reference. Hard to tell on a digital photo, but the headlight adjuster frame is Rustoleum Aluminum and the gravel pan is my Argent color. I like it, and I like the fact I can spray what I need through my gun.
Then it was on to tackling the passenger side fender. The PO had a pet chipmunk that had wallowed out a hole for the antenna. You can see how this hole was all cobbled into the fender here...
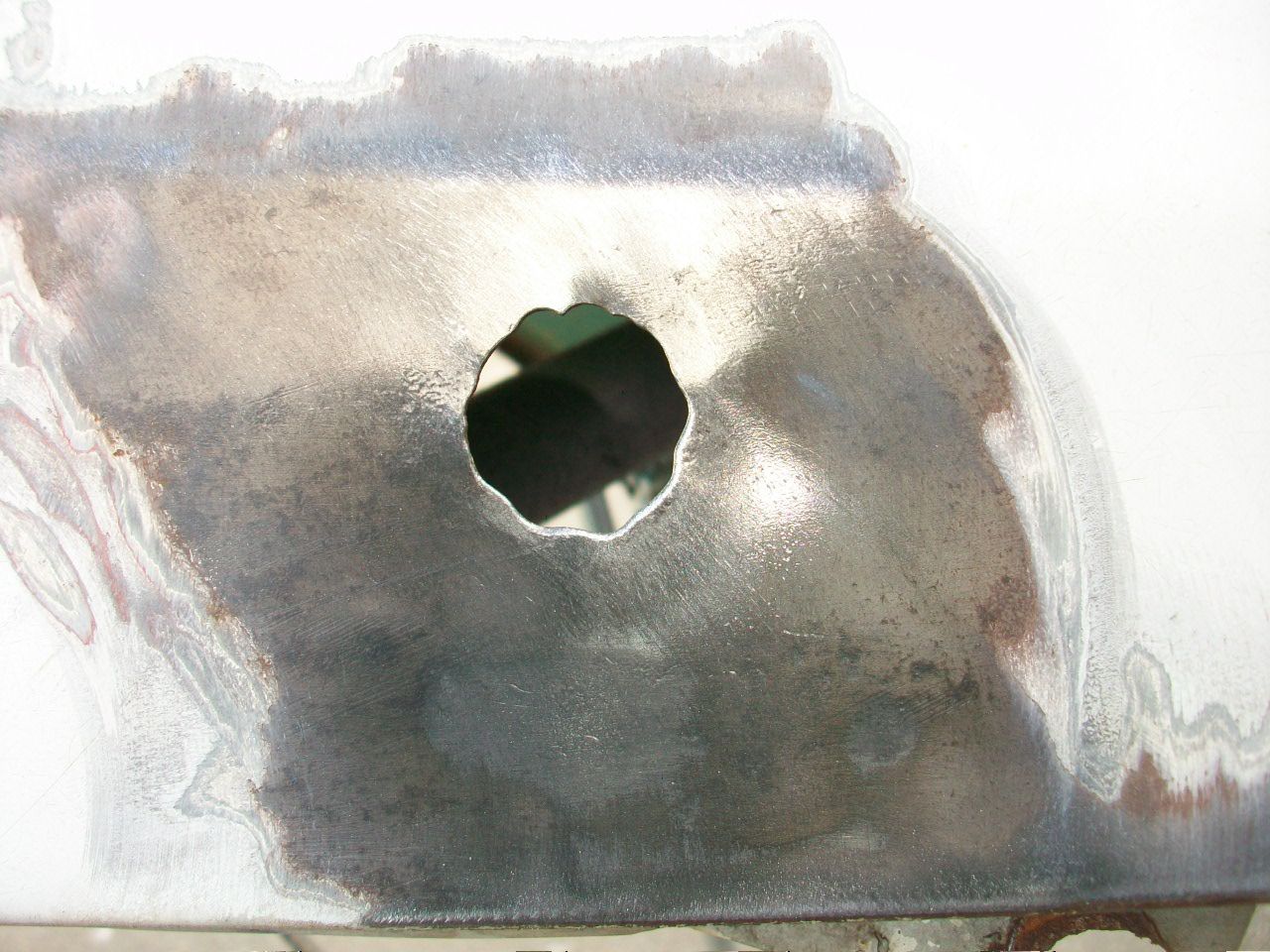
I guess it's not too bad, but I did not want to put an antenna there when I repaint... planning on using just one rear antenna. At any rate, it was time to cobble it back to flush with the sheet metal! 
I am no professional welder, but I will show what I did. You professional body men chime in here please. I am sure there is more of this work I will have to tackle at different points soon.
Basically, I took a wire wheel and cleaned both sides of the metal, inside and out.
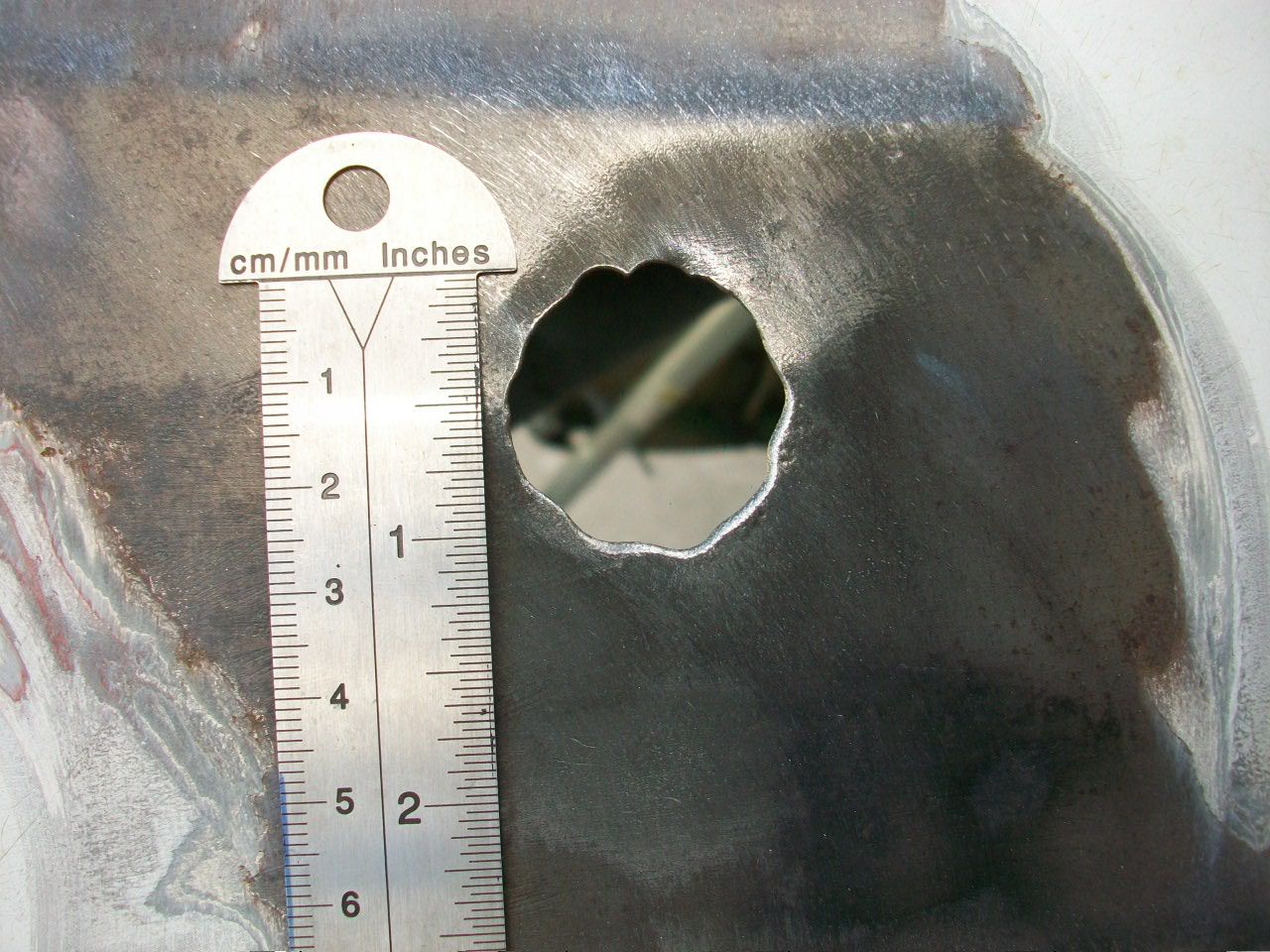
Then it was on to an air grinder so we could smooth out the hole.
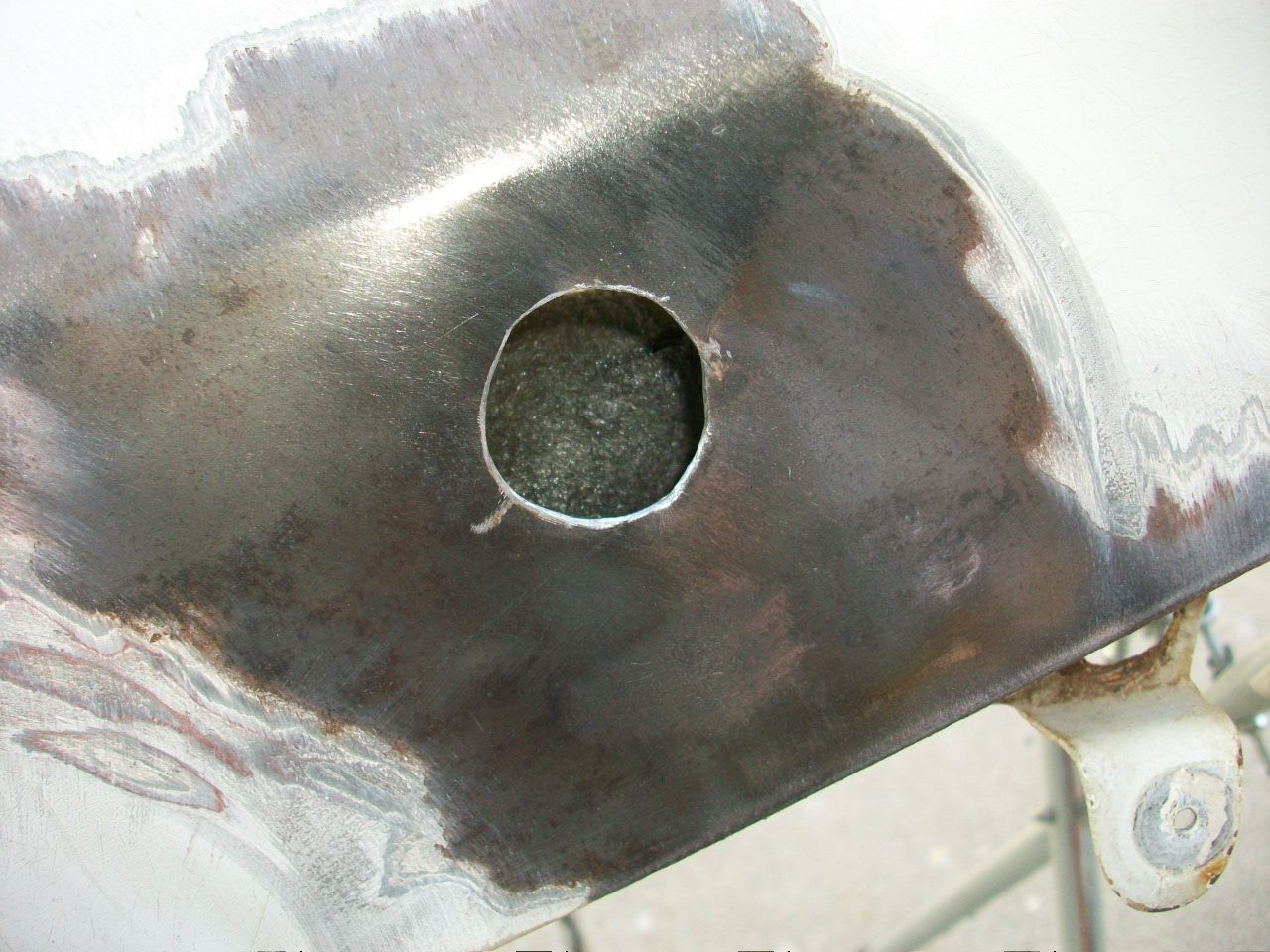
After that, I took a stiff piece of paper and copied the circle shape with a pencil, cut out the shape, and then transferred that to a piece of sheet metal the same thickness as the fender.
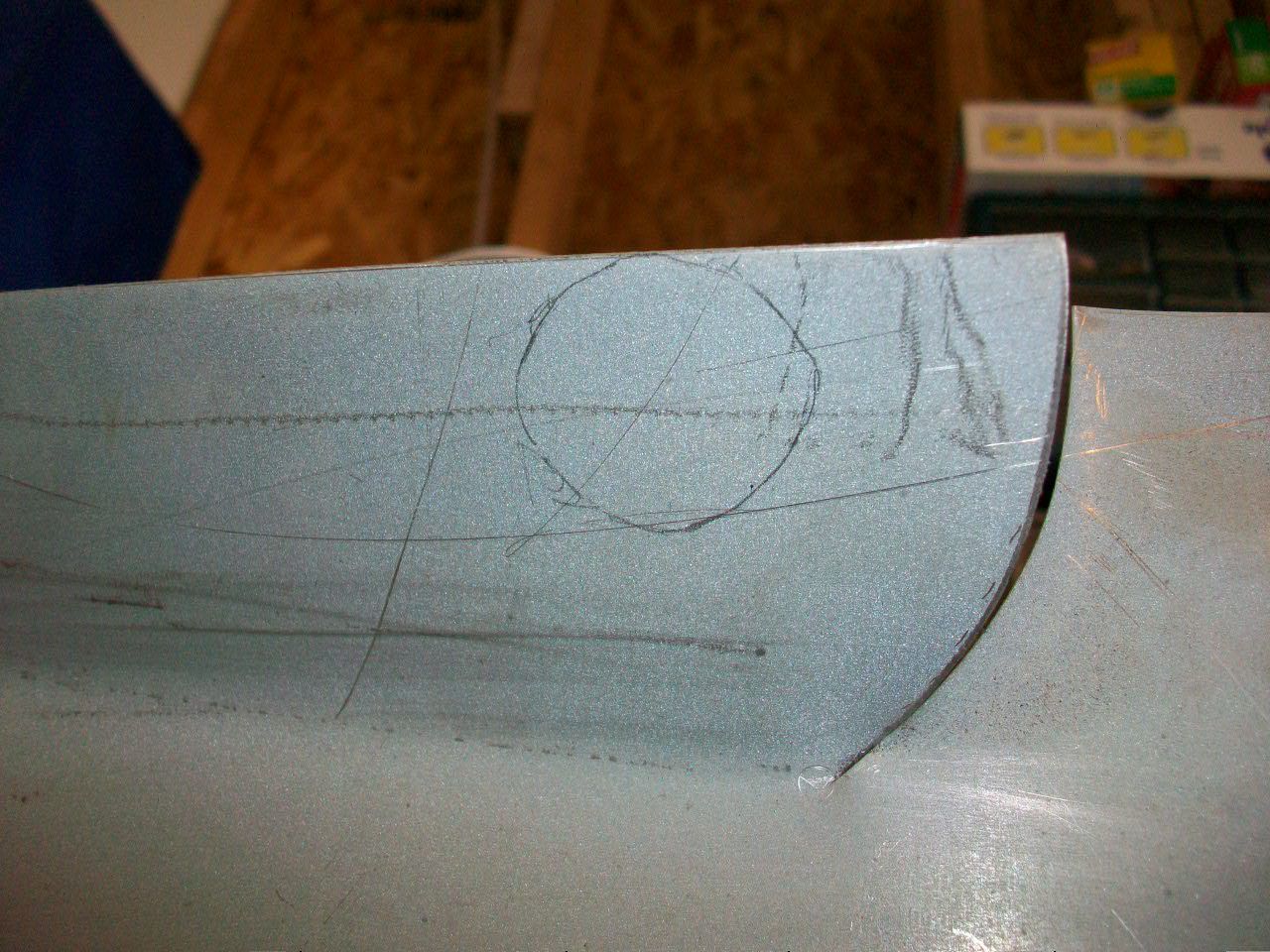
After some judicious grinding and shaping, we had a good fit to the hole. So i got out a magnet and put it flush with the fender like so...
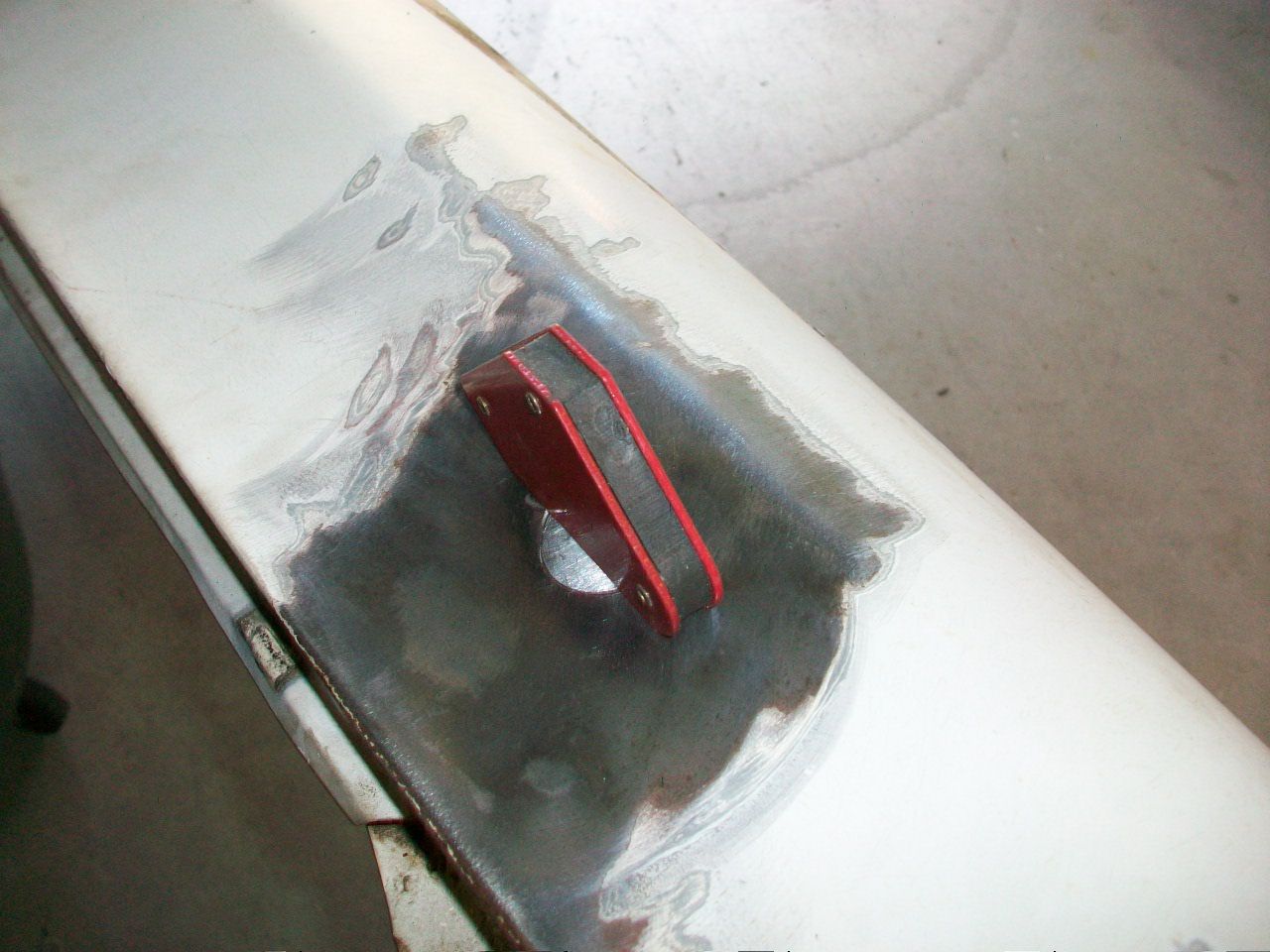
One tack weld and away we went with several. You can see from the photos that I blew a few out... if I had more experience I am sure it would have went better.
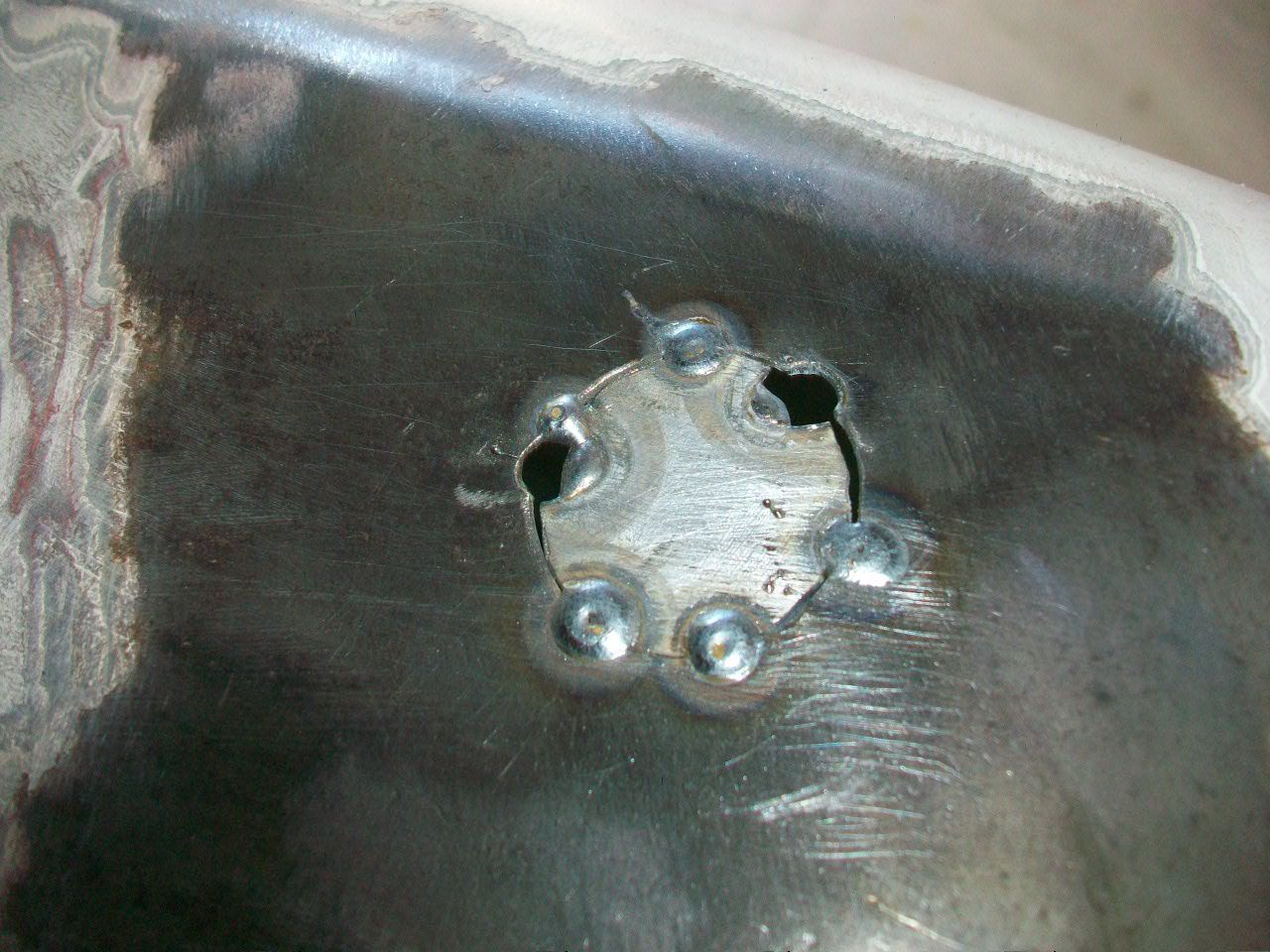
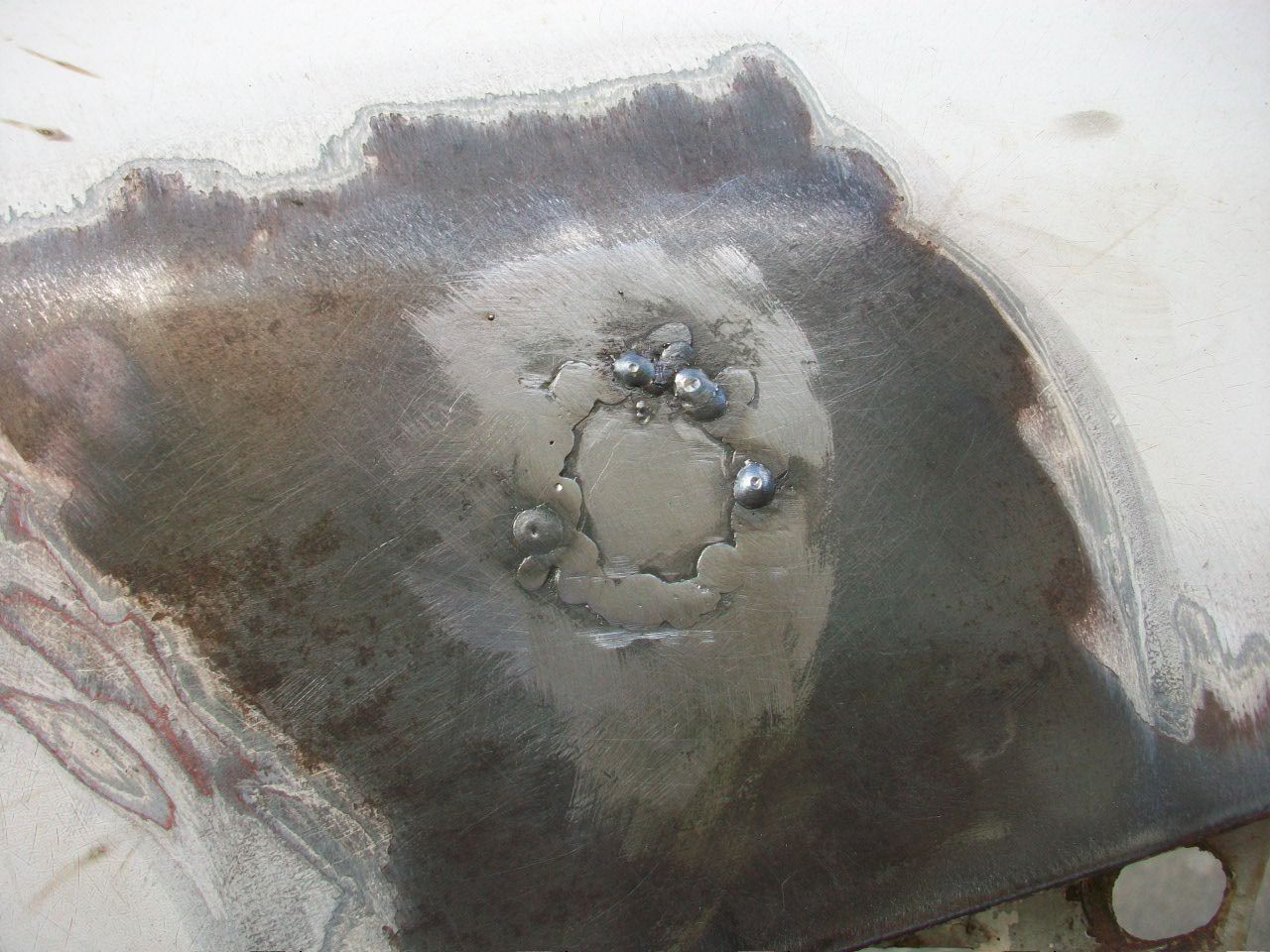
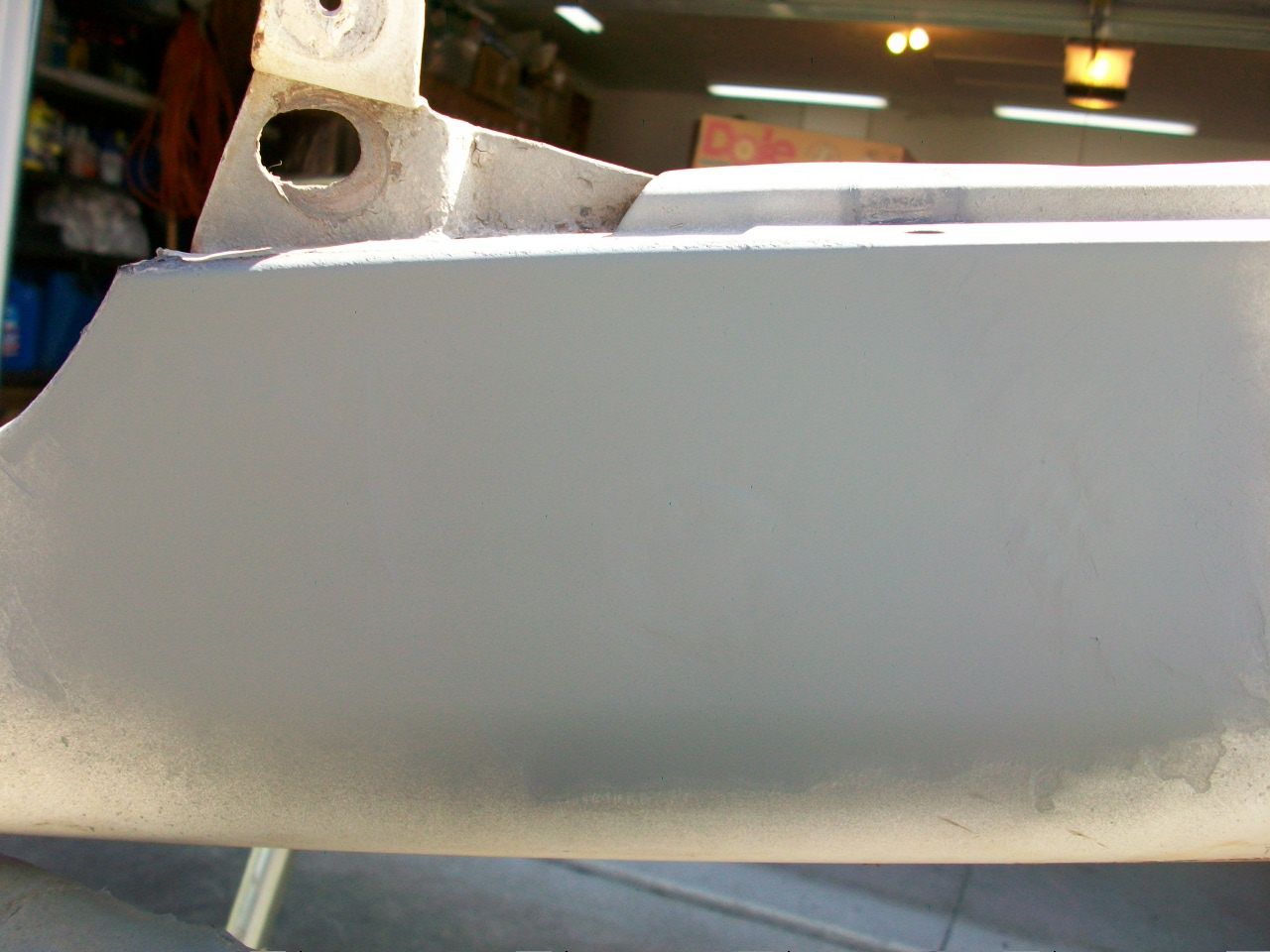
I would have had it all pretty flush and looking really nice but I got carried away with my grinder - pretty dumb to do actually. Don't follow my lead. It should be pretty easy to fill though with a skim coat when it is time to prep this fender for paint. I would like to get all of my welding done and then prep each piece for primer.
Hopefully I can get more done on this fender soon.
|
By Daniel Jessup - 9 Years Ago
|
On the installation of the gravel pan, or as Ford called it, "the stone deflector" I set out the hardware ahead of time, with two washers, a nut, and a bolt per hole. 12 holes across the front of air dams. 7/16" head on this hardware.
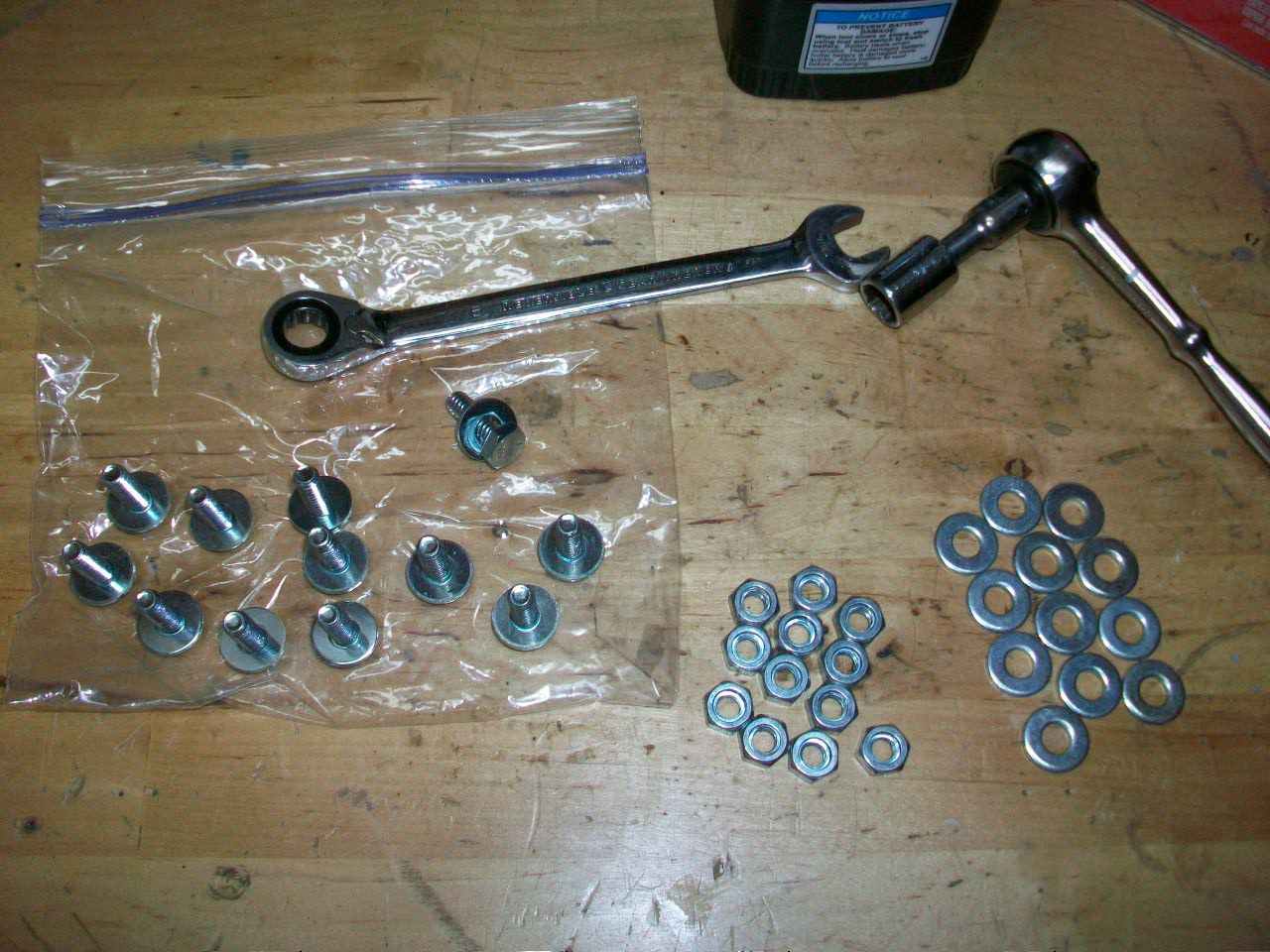
I also broke out some of these strips of caulk from 3M - thanks for the tips fellas. This stuff is easy to work with and seems to be industrial strength.
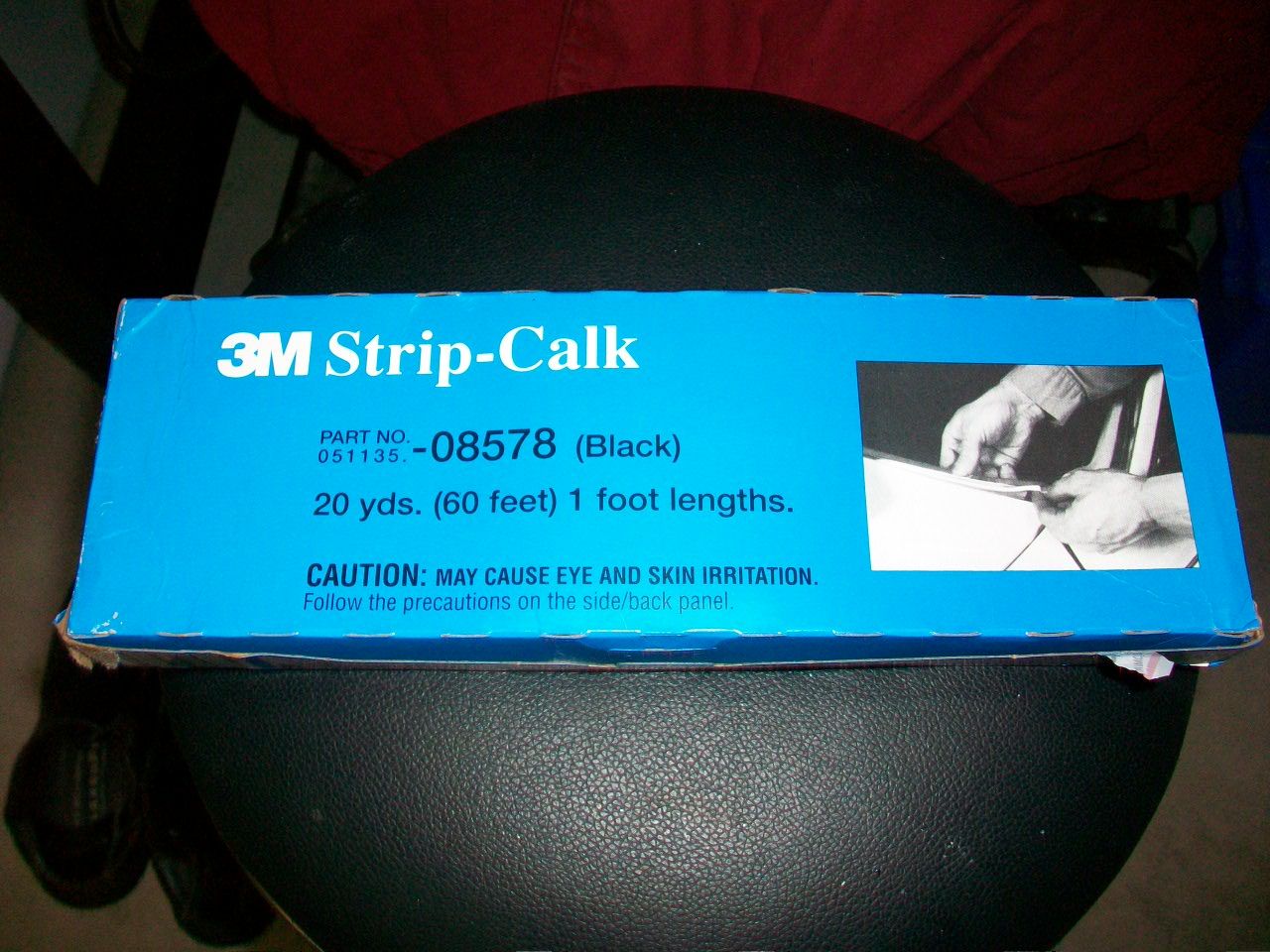
Just put the strips down the length of the air dams before fastening the gravel pan and then lined up all 12 holes to snug down the hardware enough to leave it there until I get the fenders back on.
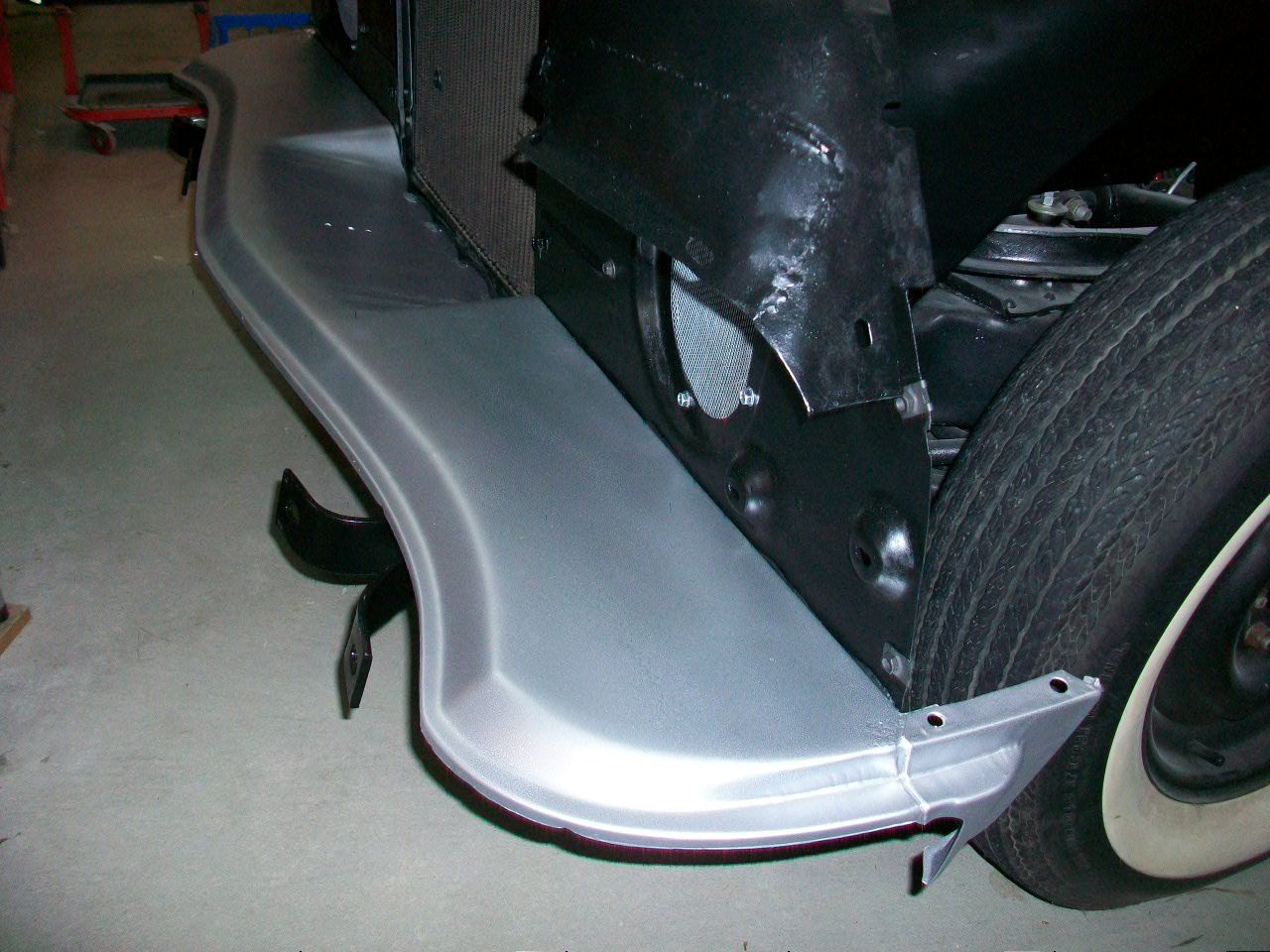
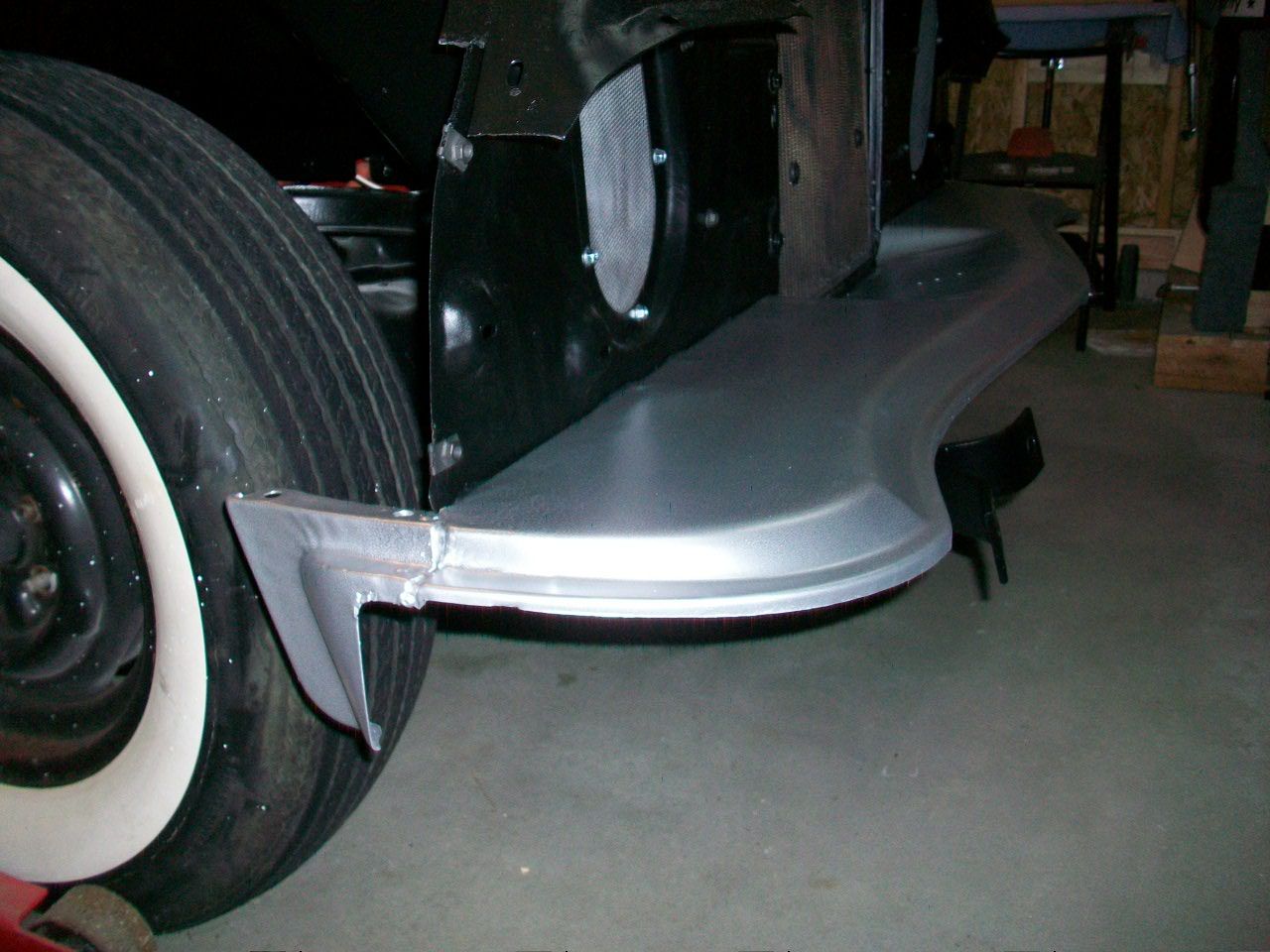
I also reassembled the headlight buckets with their springs and adjuster screws.
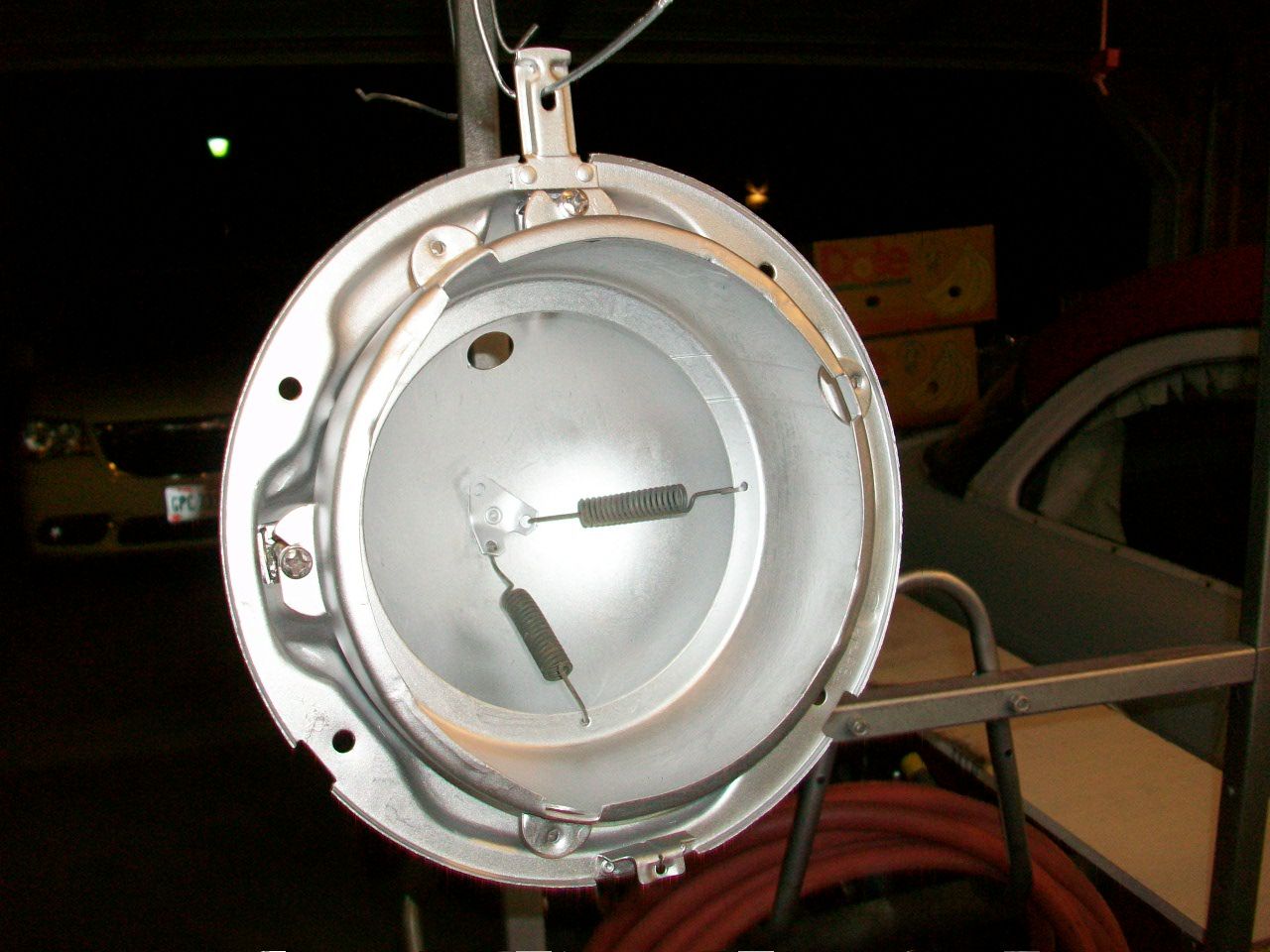
What do you guys use for headlights beyond the original setup? I would like to go the relay route and with some Halogens. Can anyone give some good reviews on what they have or maybe some installation tips?
|
By Daniel Jessup - 9 Years Ago
|
charliemccraney (9/5/2016)
Haven't done anything to upgrade the headlights yet. There are LED headlights now, and tried and true H4 halogen. For sealed beams, there are usually a couple options for brightness and that should allow for the easiest installation. I use Sylvania Silver Star sealed beams on my Firebird. They are quite a bit brighter than the standard version. They do draw more power, close to H4, so relays would be a good idea to go along with a higher powered sealed beam.
Thanks Charley for the information. All I had ever run were the sealed beams with stock wattage. Wanting to go brighter should mean close to Halogen and of course I would expect more wattage. Of course, I am out of the loop on what all is available these days for the 7" round headlights... I don't even know what those Silver Star headlights are that you spoke of. Some of the rod and custom shops have a relay harness available that can simply be tapped in to your original switch and then back to the headlights with full battery juice going to those lights. That sounds bright to me.
This will be a 12 volt setup.
|
By Daniel Jessup - 9 Years Ago
|
miker (9/6/2016)
FWIW, I've had good luck hiding relays in a hollow voltage regulator. Looks more like stock, even if you have two of them. On a 'bird it's even up by the headlights.
Now that is "trick"... I will have to take a look at that idea. The car has a one wire GM alternator with internal regulator anyway so no VR needed.
|
By Daniel Jessup - 9 Years Ago
|
The dog days of summer...
I did strip the quarter panel of the old white paint and spray primer on it to do a test of appearance, mil thickness of the paint, etc. I am very happy with what I am seeing although i did reduce the topcoat a tick too much.
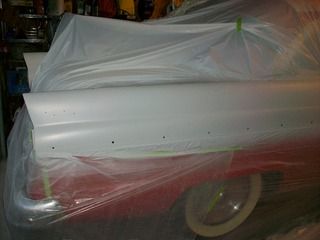
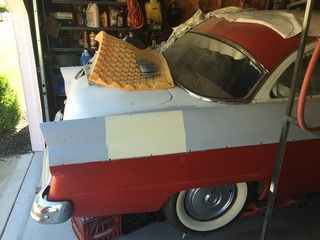
The test square of white paint looks yellow in the photo but it doesn't look that way in person. It is the Wimbledon White Ford paint code from the 60s Mustangs, kind of an off white I guess. The garage is going to be a mess for a while! And the garage is the way the entire family enters/exits the house each day. I think I am going to try to pull the car out side when I do the stripping, paint and block sand inside, etc. We will see how that works with momma! 
Last night I did reinstall the steering column and dummy shaft - the shifter is on the floor but I didn't want a hole there where the old column shift was at and I didn't want to leave it on there either.
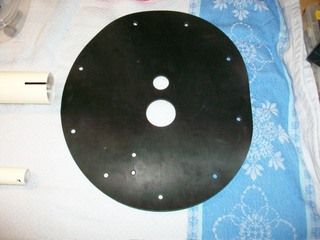
First, I laid out all of the column parts and the two seals that need to go on the column before you place it on the steering gear assembly. I used some masking tape to keep from scuffing things up on the new paint, but I wasn't perfect I can tell you that. Note the orientation of the large rubber seal - it needs to be oriented correctly. The photo is showing the FIREWALL side of the seal. Obviously I will need to cut a hole for the clutch release rod - We will wait until it all mounted up to do that but it should be pretty straightforward.
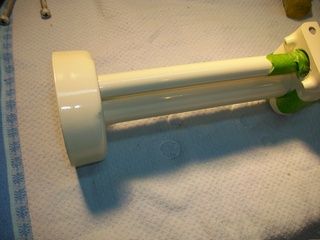
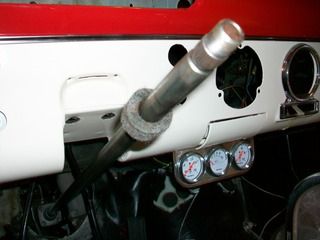
Don't forget that felt oil baffle that goes inside the steering column. Here it is pictured up top but it needs to go down to the bottom where you will tighten the tube to the steering gear.
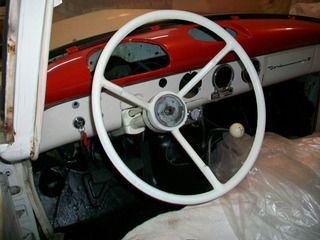
Before installing the steering wheel, make sure you place the white plastic bushing around the steering shaft - this bushing goes rests between the shaft and that bearing in the cup of the column tube. If you look closely in the photo above where the spring is shown in the cup you will find that small bushing in place. Here is the part number...
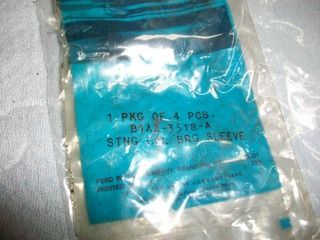
One last item to mention... After working on that steering wheel for a loooooooong time would you believe it fell off of the paint rack? TWICE! It cracked again and of course is dinged up. I hate to say it but for now since I need to move the car in and out and start getting this body work done I just gave up and installed it. It looks good in the photo - but trust me - IT AIN'T :mad:
I will locate another one and have it ready for after the car is repainted.
|
By Daniel Jessup - 9 Years Ago
|
I got into the garage early this morning, cleaned it out, washed the car with dish detergent as well as I could (before tackling this body work), and took the 55 out on the street in front of the house a few hundred yards or so - it is has been a while since she moved out of the garage (not since I installed the Hurst shifter). The floor shifter works like a new one and I was reminded that the 292 with goodies has a lot of get up and go!
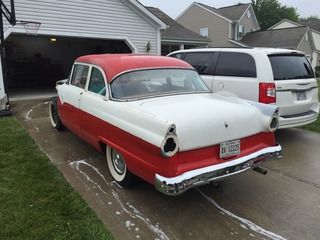
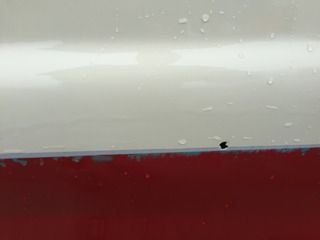
The fellas at the print shop where our church prints millions of Bibles a year gave me some leftovers of an industrial roll of high grade paper - this is excellent masking material! I mounted it above the workbench on 2x10's with conduit running through the middle to act as an axle. The weight of the roll is a little over 50 lbs. Probably more paper than I will use, but it's there and it is 36" wide.
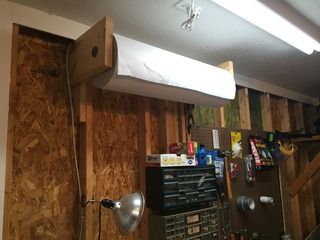
On to the grinding when I get back next week!
|
By Daniel Jessup - 9 Years Ago
|
Not too much to post today, but with this most recent paint job on the inner fenders AND the recent delivery of brand new front end sheet metal hardware it is just about time to start putting it all back together up front.
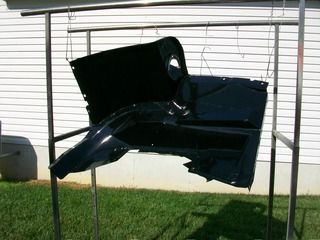
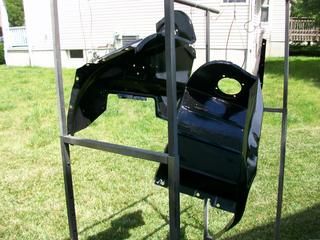
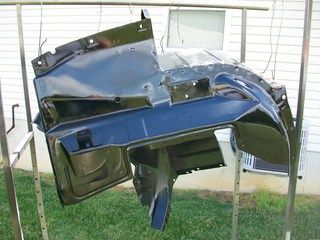
Any tips on getting this front end back together? One question I had was about the large pad underneath the "U" shaped radiator support. When do I tighten that one down? that pad is pretty thick as new, but it was as flat as a pancake when I removed it.
I assume everything begins in the reverse order of how it was all removed. Begin with the radiator support, attach both air dams and then attach both fenders?
|
By Daniel Jessup - 9 Years Ago
|
Got a few things done this weekend after being out of state for a whole week...
First plan was to make gaskets for the air tubes and vents. You can take a look at the photos - I had some neoprene stock lying around and a sheet of 1/8" rubber matting from a Canadian supplier, eh?
The holes were punched out with an old socket - seemed to work well and we saved a little dough on the "manufacturing" this weekend.
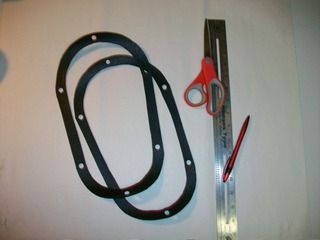
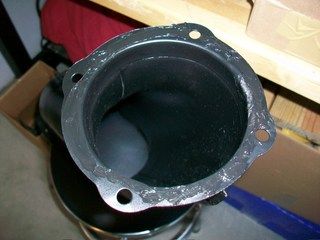
I used the sealer pictured above to seal all of the gaskets at the air tubes, but i used only the large gaskets themselves at the screen/air dam position.
I also began installing the rubber grommets for the wiring harness to come soon. The kit pictured below is extremely handy for your firewall, fenders, and other sheet metal holes where you will have wiring pass through. With an electric fuel pump, electric fan, A/C to come in a year or two, etc, there will be plenty of extras what with relays and all the like. I have a Rebel Wiring Harness that I will use on this car for more circuits as needed.
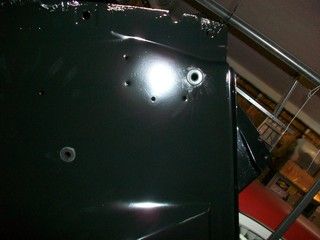
Back to the inner fender/air dam assemblies. Basically I decided to assemble the air dam, vent tube, air deflectors (small tubes that direct the flow of air), and the inner fender while all parts hung from my paint rack. Before I could get to hardware though the rubber splash guards had to be installed - you know the ones - they have those pesky staples that hold them in place. I had saved my old guards and referenced the original holes from the staples, punching small holes with an awl so that I could push a staple through. After doing that, the holes were lined up perfectly (well, as perfectly as the factory had done so!) and the staples were pushed through their original holes and then hammered down on the other side while a vise grip kept it tight. I am HAPPY with the installation and they are holding tightly.
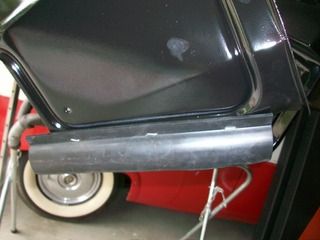
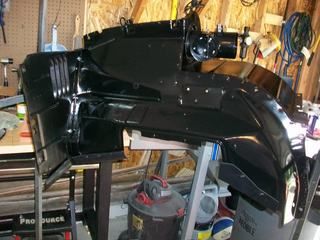
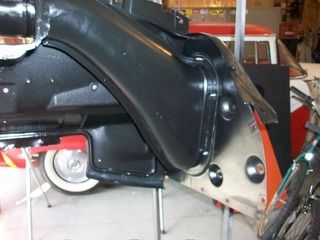
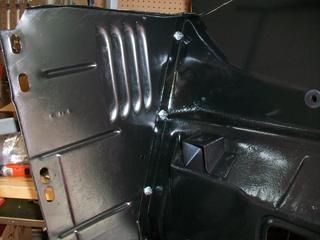
More in the next post... don't want to exceed any limits on pictures and what have you
|
By Daniel Jessup - 9 Years Ago
|
A little word about hardware. I had broken quite a few of the old pieces of hardware, be it a J nut for the fenders, a nut/bolt combo that I had to gorilla in two to remove it, etc.
I decided to purchase a kit that was advertised as being all of the nuts and bolts you need for the front end sheet metal....
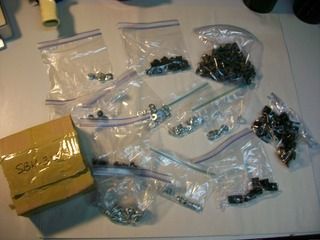
Do not be confused here. Every little bolt, washer, nut, etc, came in that box on the left AND WAS NOT BAGGED. The separation was done by yours truly, and alas we found that pieces are missing. First up:
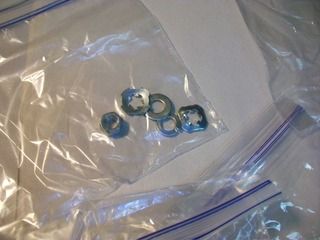
If you know your fenders, the above picture is the hardware needed to bolt the rear of the fender at the middle THROUGH THE BODY and access the nut by removing the kick panel. Note - we have enough to do one fender... thankfully I saved everything so I am sure I have what I need, just have to dig it out.
Next up... this little photo:
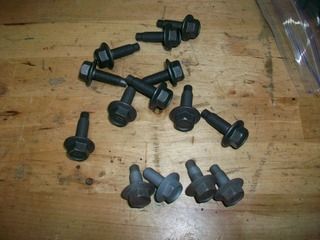
When bolting the air dams to the U support of the radiator, I discovered that there were none of the shorter bolts included in the kit. All were the same size, and too long for the U support (bottom'd out pretty easily with room to spare at the head). YOU WILL NEED the smaller bolts I have pictured - these are half of them.
Kits may save time because you don't have to sit and measure, count, inventory every little piece you need, but when the kit does not meet your needs... well, that ain't fun. 
Said kit ain't cheap either.
Ok, rant over. That was basically the worst of it today with the installation.
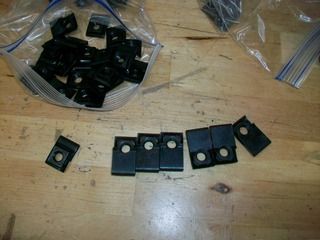
Note the photo immediately above. The 6 longer J nuts are in the picture being shown against the shorter size of most of the J nuts that go on your front end (the 5/16" diameter J nuts anyway, you do have some smaller 1/4" elsewhere) well, anyway they go on the inner fender at these locations, 3 a side:
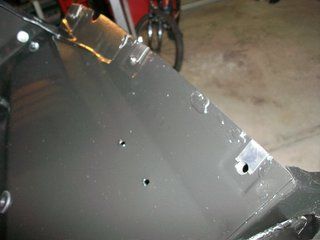
Here are some photos of my makeshift battery tray, battery, and starter solenoid removed and both sides of the inner fenders and air dams/tubes installed! 
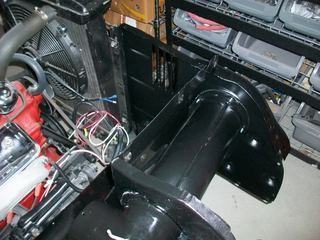
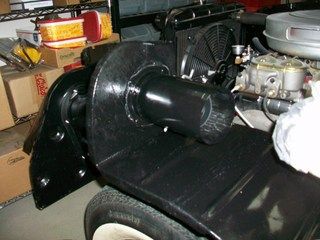
Next up is to get the seals on both sides installed (if your eyes are pretty good you may have noticed in the photos that these are not yet attached) rear splash guards installed, work on the gravel pan and get it ready to install, ready the bumper brackets, and then grab the fenders to see what we've got! :eek:
|
By Daniel Jessup - 9 Years Ago
|
Got around to installing what Ford called the "anti squeak seal" on the inner fenders. I used the original holes for the staples and a little bit of sealant where I thought it was needed. Only had enough to do one side. I guess when I ordered this stuff last year I obviously did not read very well - needed two "kits" to get one car completed.
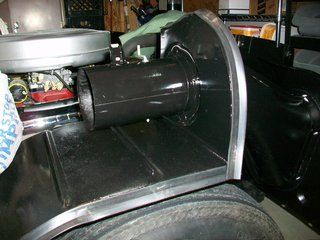
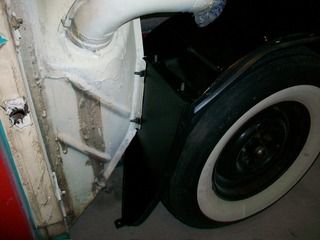
It has been so hot out here lately I decided to work on the fenders in the basement this evening. They both needed to have all of the hardware and stainless removed. I was amazed to find the original clips had held the SS to the fender so tightly. When I began removing the nuts on the under side they began disintegrating - this is about 1/3 of the dust. The driver's side fender was much worse than the passenger side concerning surface rust. You can really see the rust after the SS trim was removed... and of course the original Sea Sprite Green and Snowshoe White.
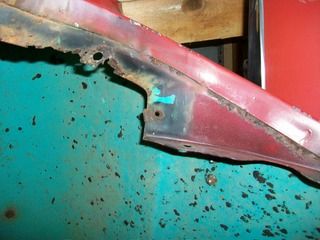
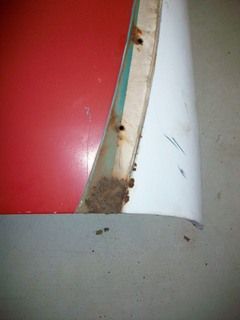
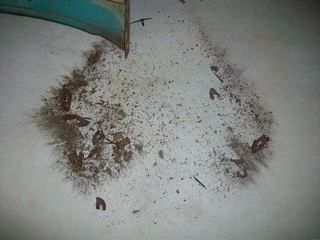
I feel embarrassed to say that I cannot make out completely what the original shape of the clips actually is supposed to be. I do have some idea. It looks as though there are 10 a side of course, but the two at the very front had a very different shape/size to them. I got out a Restoration Specialties Catalog and looked at clip number 2517 - that looks like the original 8 one each side, but I have no idea about the other two. Anybody have any ideas? Or is there a better clip somewhere?
|
By Daniel Jessup - 9 Years Ago
|
Got back from being out of town and just had to get in the garage for some therapy. I decided to remove all of the trim (save the rear bumper and the windshield/glass trim) so I could begin the body work and paint process.
Some photos and some questions for you fellas that have more experience than I ...
First up, the doors. The passenger door is the "worst" of the two but won't require much. I am going to treat some of the rust on the inside cavity and then paint inside, making sure that the drain holes are good.
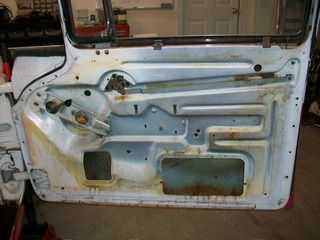
Next, a wonderful find... the previous owner decided to hold each of the Fairlane Crowns on the doors with this goo :eek: Must be pretty good stuff. After 25 years or so they never fell off!
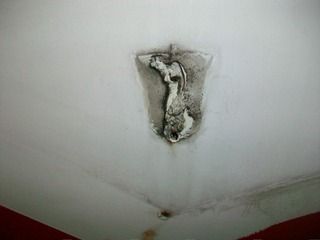
All of the upper window openings have rust like this:
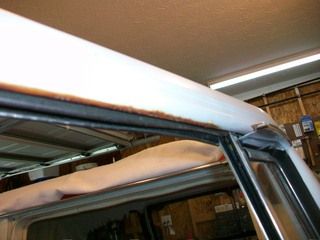
That will be fun.
Of course we had a slew of clips and fasteners to deal with but I've gotta ask a question from this photo
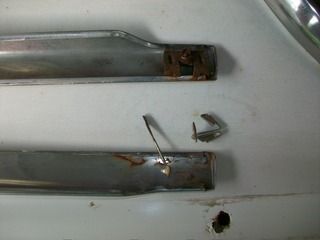
Which one is original? I assume the one on top that is "square" right? The other one (like some of the other clips) simply broke off in my hand when I gave a gentle tug on the SS trim pieces.
And then how about this? Check out the paint - serious crow's feet pattern going on. This paint job is about 25 years old but the white is in serious trouble like this all the way around the car. The red is in excellent shape and looks like it could have been painted 3 years ago. What gives?
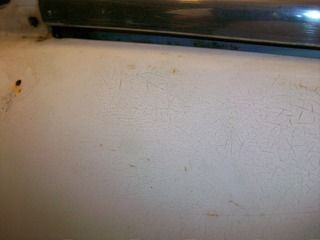
I went ahead and took 120 to a patch of the white paint on the rear quarter panel just to see, then I took it to 400. I cleaned it with thinner and this is what it looked like still, although you could not physically feel any crow's feet you can still see them.
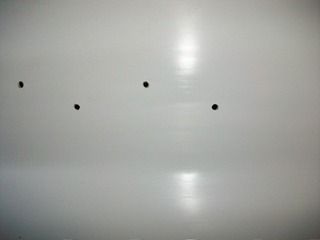
Can I paint over this if I knock it down with something as serious as 120 and then maybe follow up with my 2K primer surfacer?
|
By Daniel Jessup - 9 Years Ago
|
Sometimes while working on this project I like to take some time out and do something to a sub-assembly or rebuild a few items to get some sense of "completion". This can be a carburetor, a set of rocker arms, oil pump, and the latest was just another rendition of a wall clock for the office.
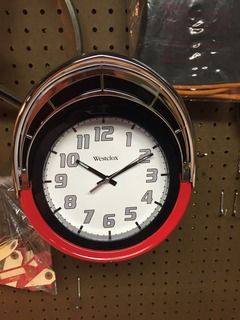
This one was a little more challenging in setting the clock in the cavity because of the eyebrow trim, but it turned out nice and I like it.
Ridiculous price on those new Chrome Headlight Eyebrows - I am embarrassed to even say.
|
By Daniel Jessup - 9 Years Ago
|
Last night I did some "testing" with two forms of paint removal on the White Tutone where the crow's feet is all showing up. The first was a simple heat gun and razor blade scraper.
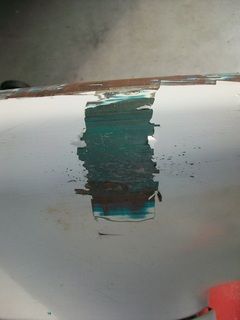
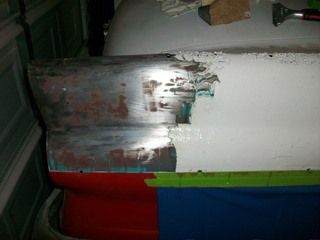
It took me over an hour to move that far along with that method, but it was a "no muss, no fuss" way - simply sweep up the chips on the floor. I was concerned over the idea of heating the paint being so close to the Red Tutone which is in excellent shape. Once I got through those layers you could see where the paint had followed this idea - FoMoCo primer, FoMoCo Sea Sprite Green, ? FoMoCo primer? and FoMoCo? White, then aftermarket primer, aftermarket White. How did Ford do their Tutones? Were all bodies painted a solid color and then if doing a Tutone car the white was painted over afterwards? All of the FoMoCo paint is really on there and really stable - no problems except for the few small places I am going to deal with where there is rust pitting.
Next was brushing on "Klean Strip" - it took me an hour and a half to get only this far. :confused:

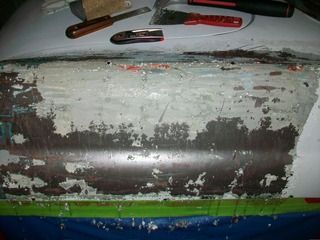
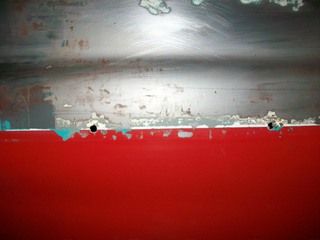
A few items of observation:
1. It took THREE applications to get the paint removed from where you see the beginning photo to the ending photo, and even at the ending photo there was some sanding with 60 grit done just to clean it up. 2. The aftermarket White Tutone with the crows feet came up as fast as you please. With all of those cracks in the surface it took no time at all. Within 5 minutes it was bubbling up and peeling. 3. The original FoMoCo paint is some tough stuff. Even after following paint stripper manufacturer's directions to the letter it still did not remove all layers after THREE applications. 4. What I had feared about the seepage of paint stripper down to the Red Tutone was true. It eventually worked its way under the paint and ate into it a tick. 5. There is an obvious mess on the floor - 
Next up is get out the 7" disk electric sander and go to town. It will be interesting though to see how much dust I kick up here in my little "harry homeowner" garage that is not made for this type of work. :eek::eek:
I also have a DA I can try, but I think that will yield the same results as the electric sander.
I do know this - it might be best to remove the white Tutone from the fenders (in storage right now) by using my sandblaster. Not sure of what it would take to get that done on the entire body - I really don't have a place to do that here and the fender will be fun enough as it is. I guess the neighborhood will have to deal with the black dust cloud coming out of the Hot Rod Reverend's house!!
|
By Daniel Jessup - 9 Years Ago
|
Ummmmm, ok after a little more "testing" I think we have a winner, winner, chicken dinner! :p
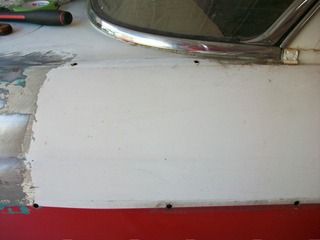
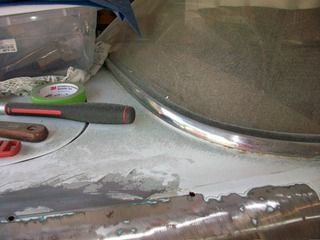
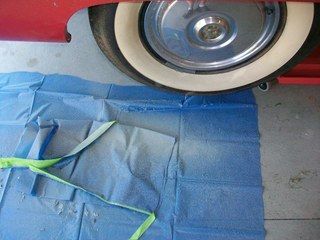
That took what.... 5 minutes if that? But check out that dust! It's everywhere. We will keep moving along here and see what we can do today.
|
By Daniel Jessup - 9 Years Ago
|
More photos... it did not take too long to get this done, but boy the mess! It looks like I am going to have to start pulling the car outside and take care of this mess in the driveway where I can hose down the dust. The surface on the sheet metal continues to look pretty good. Why the white tutone when "crow's feet" after all those years I am not sure.
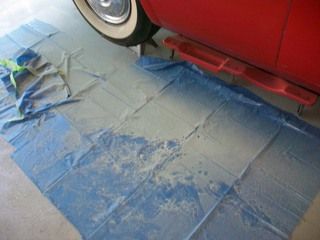
Got to put the column and steering wheel back on first!
|
By Daniel Jessup - 9 Years Ago
|
Thanks for the tip...I do move the head of the sanding disk around quite a bit so as not to build up too much heat in one place. The grit is 80 also.
|
By Daniel Jessup - 9 Years Ago
|
Wow - I did not know that. Most may balk at that price but I can certainly see why the wheel is so valuable. This Bakelite material is pretty old.
|
By Daniel Jessup - 9 Years Ago
|
those crestliner wheels are all out beautiful. I don't know if Ford ever made a better looking steering wheel in the 50s!
|
By Daniel Jessup - 9 Years Ago
|
The son and I had a good afternoon together. We did not get too much down on the car or any Y block parts, but we did get to use our brains, hands, and a little math to put together a 2x4 shelving unit in the basement. My garage is just too full of parts, tools, and the like to be able to move around there without my fat rear end knocking something over, getting grease all over me, etc. It is like working in a can of sardines. You guys that have smaller workshops I don't know how you do it!
Anyway, I enjoyed the time with my 13 year old boy, EJ.
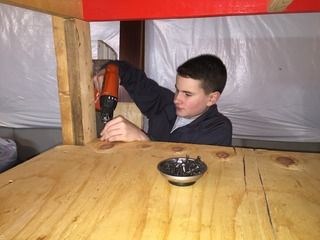
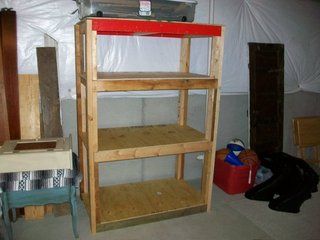
We just made it from scrap lumber and all as you can see. The measurements are 72" high by 29" deep and 48" wide. She is straight and true on the level. We started putting some boxes and totes on the shelves before I had a chance to grab the camera. She will sit in the basement for a good while - pretty heavy shelving here.
The kits for the vent seal replacement came in while I was out of town...
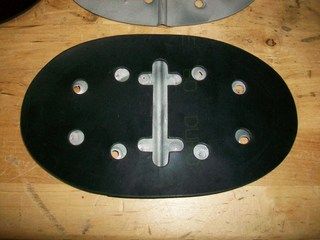
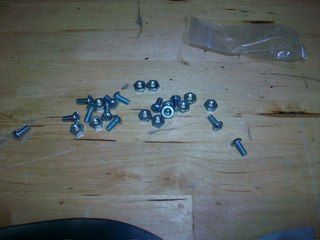
Whereas the originals were in two pieces (I am pretty sure the originals were installed as a two piece assembly in each tube) the new seals are one piece. Also, there are a good number of machine screws and nuts to put the flappers back together. However, methinks I have one too many holes and will need some more hardware! Ouch.
|
By Daniel Jessup - 9 Years Ago
|
Here it is May 7th and I feel like I've got nothing done! My air compressor (the heart beat of the shop) went down and I chase the problem for a week or so. It ended up being the start capacitor. No biggie, get it ordered, be here in 4 days, etc. Capacitor shows up - wrong one. Right box, right label, wrong capacitor in the box! Aaarrrrrggghhhh, another 4 days and we have what we need.
Pressure washer went crazy blowing water everywhere. Seems Karcher uses a lot of molded, high density pvc in their units - this one had a cracked elbow. 5 days and replaced that.
My wife drove through some truckers' explosion and she says the smoke and debris made it where she could not see a thing, van covered in all kinds of good, plastic?, black dots, and I don't know what all. 10 hours of a buff job and we are all shiny again - just in time for Mother's Day. 
I did get those vents squared away. They look good. The seals went into the units without much fanfare, and I put a tick of white lithium grease on the pivots.
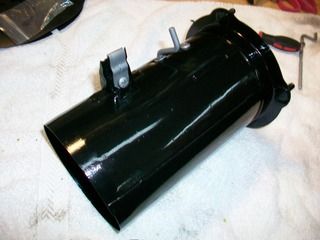
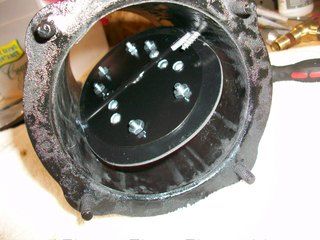
I also got a chance to mount an electric fan and plumbed a thermostatic switch after a visit to Lowe's and the plumbing section. You can see the tee I put in right there behind the thermostat housing on the intake. I could not figure a way to get a good tee and still have good access if I used the original sending unit location on the head at the rear (there is already a sending unit there for the mechanical gauge.)
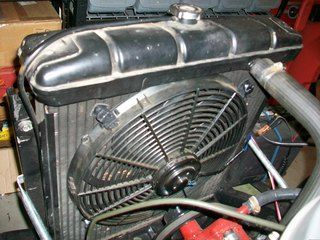
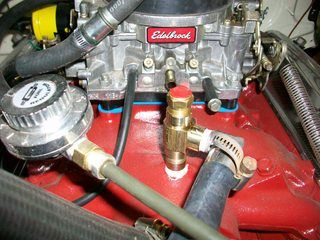
The electric fan went in without too much trouble as well. It is a pretty good unit that I had been using on my portable engine run stand. Would you believe you can get a very good mounting kit on ebay shipped to you for $1? that's right, that's what it cost me - and it looked pretty healthy too and held up that fan nice and tight.
And then we have everyone's favorite job - the dreaded steering wheel! :o
I used PC7 epoxy to fill in those cracks and crevices after opening them up and then took a dremel tool to the thing to sand it as level as I dared...ended up using a drum roll. (queue stupid joke :rolleyes
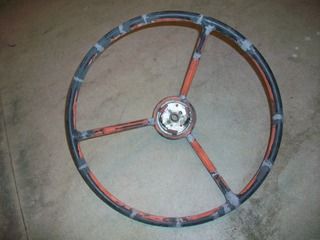
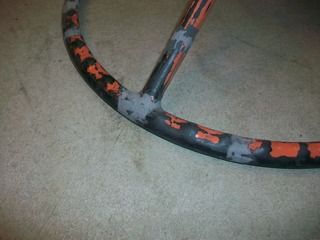
After I knocked down every bulge I took 120 grit sandpaper to it. Once I got down with the whole hour and a half job (man this is tedious work!) I was a dusty mess! Good thing I used a dual cartridge filter mask. I need to paint the wheel with some primer/surfacer after wiping it down with Acetone. After that I will probably have to fill in some low spots here or there with some glaze. I am not going to spend a whole lot of time on it - it is a driver after all not a show car.
Plan to see my father-in-law soon, but it looks like it will still be a little while before the 55 is back on the road...
|
By Daniel Jessup - 9 Years Ago
|
Alright, so after a few private messages, some public messages, and my own research on that Mr. Gasket Fuel Pressure Regulator finally I caved in and purchased one - it is a 12-1803 unit. New in the box from Holley, it has a mounting bracket, screws to mount the bracket to a firewall or other stable mount, and two "self-tapping" screws to secure the regulator to the bracket.
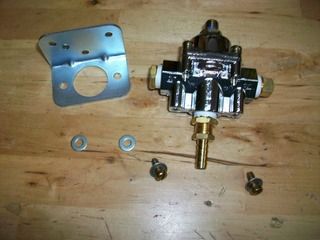
Not impressed with the hardware - the sheet metals screws had too large a head - they kept hitting the regulator housing. Next thing, the "self-tapping" screws were too long but we did trick that one out quickly. (the fittings and washers in the photo were from my own stash)
What I like up front - TWO outlets (for what I am doing here I can put a gauge on one end and of course the line to the carb on the other. When I got to looking at what I was going to do to mount it, I decided to take this route as you can see. Even with the air cleaner on the carb, once I install a gauge it will be easy to read when we pop the hood.
Steps taken...
Fabricate a support bracket from stock
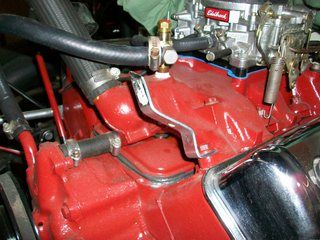
Next, attach the regulator bracket to the support bracket (on the level )
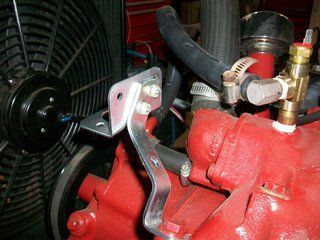
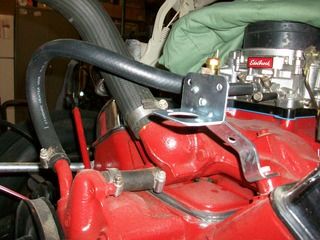
Now fit the regulator to the bracket assembly with the fittings already installed from the bench.
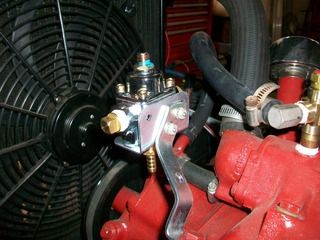
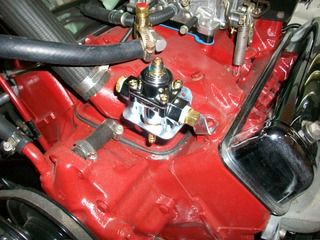
Ok now for some plumbing. After removing this mess...
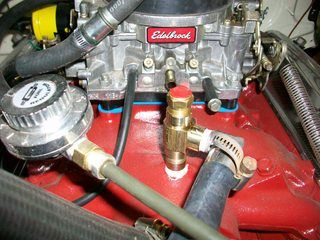
I bent up some hard line to go from the regulator to the carburetor. It basically goes underneath of the upper radiator hose (at thermostat housing), takes a dive to the other end and turns back towards the carb just before the passenger side head. Then a couple of roller coaster "dipsy-do's" to get some clearance and then up to the carburetor.
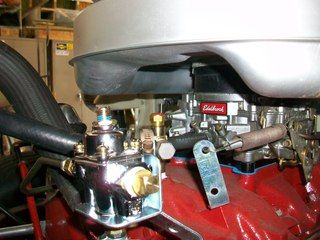
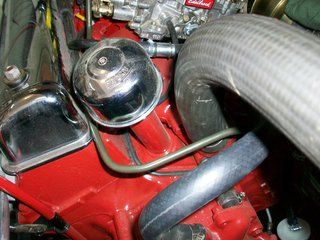
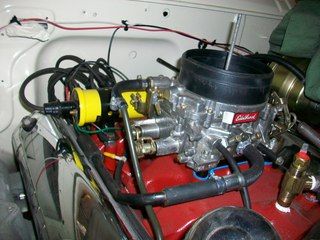
I did put a filter just after the pump as pictured here...
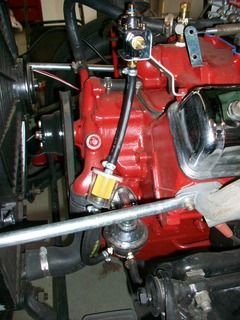
All I had on hand was a cheapie - will have to get another one before this old 55 is put on the road permanently.
I do like the clearance now though and this is a much better routing back to the carburetor. We also have more room for the connection made at the thermostatic switch for the cooling fan.
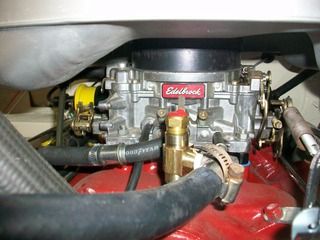
Oh and I am still sanding and working on this guy too!
|
By Daniel Jessup - 9 Years Ago
|
Great! do you have a photo or two to put up on the website forum here? I would like to see it.
|
By Daniel Jessup - 9 Years Ago
|
The installation of the shifter took quite some time. Checking clearances, attaching the lever, setting the tilt, etc. But this is what I ended up with concerning the amount of "throw" from the shifter...
First Second
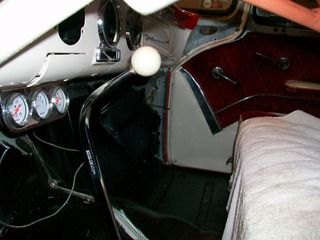
Third Reverse
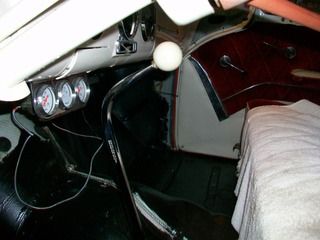
And Neutral...

So now that I had all of that squared away it was time to install the rods that attach the shifter to the Hurst levers on the pivots on the side cover. The First/Reverse rod installed without too much issue - no problems there. But, check out the interference on the Second/Third gear rod -
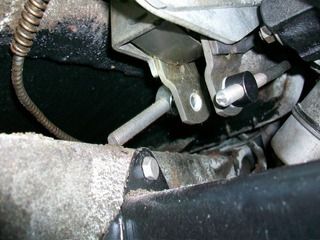
So..... out it came and put into the vise to be "modified"
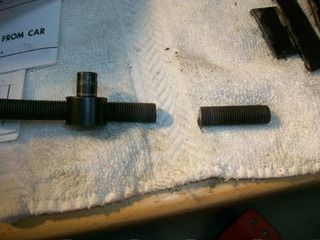
Now we're cooking!
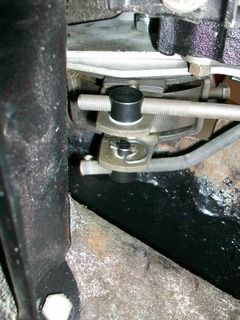
By the time I got done with all of this it was too dark outside and this 55 has no headlights so I could not swap the gears to see how we're doing in that regard. I need to set the stops anyway.
The hole I made for this thing is approximately 5.5" by 4.5" and it is on that weird angle where the shift lever will be oriented far to the right and up the tunnel. Time to go shopping for something sizeable.
Glad it's in and I am pleased with the results so far. I did sit down in the seat several times and swapped through the gears to make sure there was no binding, etc. At first I thought the shifter might be too close to the side of the driver but I think I am going to like where it is oriented and the height of the shift lever is near perfect.
|
By Daniel Jessup - 9 Years Ago
|
Here is a photo or two of the boot I picked up that will cover the shifter and the hole. It is a whole lot larger than I want it to be, but with the footprint of the shifter mechanism coming up through the floorpan I really have no choice here.
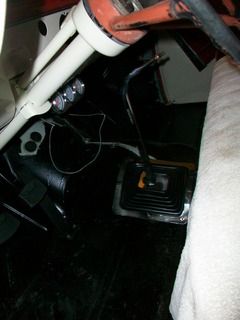
I plan to install Dynamat, or something similar, under the carpet so I guess these small sheet metal screws that came with the boot and chrome retainer are not going to work... should be easy to find a few. I am taking note also that I will have to be very careful not to harm the wiring harness sitting on the trans tunnel when I drill the holes for the boot later on.
Hopefully I can get in the garage tomorrow
|
By Daniel Jessup - 9 Years Ago
|
Back in the garage today for a little while, but mostly to work on these...
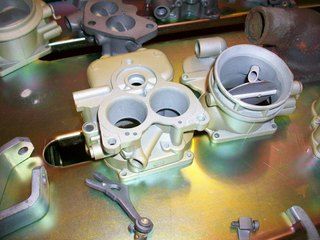
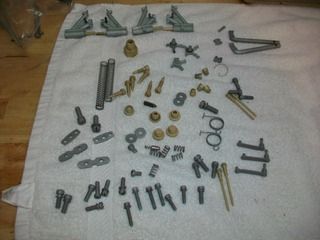
I rebuild at least one Holley 94 or more each month, some passenger car variety, some of the truck variety (different air horn of course) - but I sell every one I build. I completely go through them, have a very good parts stash, and use an ethanol compliant kit for each one of them. The funds help the project along.
Oh, and I also found one of these to make myself a clock too. Now that my dad has one I thought I would make one too. I already have the clock for the headlight ring.
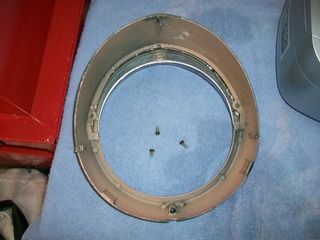
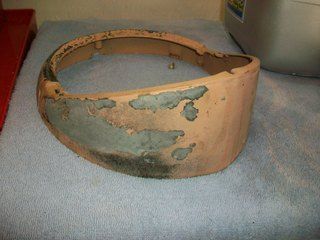
I did spend a few minutes removing the shifting shaft on the column. To maintain some sense of appearance I believe I am going to get a tubular steel shaft that is 5/8" ID and 3/4" OD to mount on the column.
http://www.onlinemetals.com/merchant.cfm?pid=7765&step=4&showunits=inches&id=283&top_cat=197
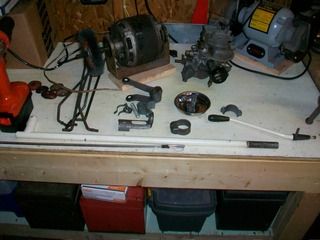
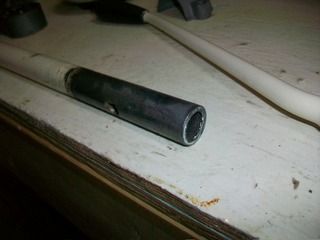
I measured the post that is under the cup on the top of the column and it is 5/8" OD. It looks like my plan will work and I can just prime and paint one up to match (I need to touch up the column anyway since I boogered it up a little bit when I put it in the first time.
I took a photo of the top of the column and the cup. There is a bearing at the top of the tube. At first I thought it was for the steering shaft but the shaft does not even come close to the diameter of the opening. Am I missing a piece or something? I am going to have to check my diagrams and take a look see. The parts all 56 passenger car pieces, column tube, shaft, steering wheel, etc. One thing I just thought about... is there a spring between the bearing up there and steering wheel?
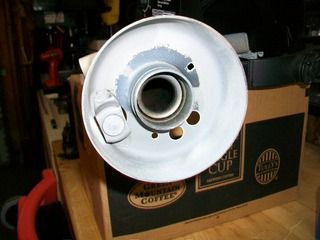
|
By Daniel Jessup - 9 Years Ago
|
Got home tonight and what was this?
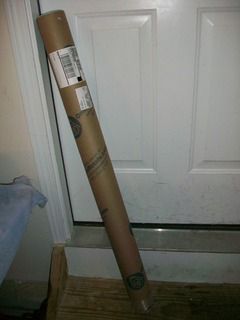
My order from Online Metals was already here! It is a steel tube 36 inches long, 3/4" OD and little bit less than 5/8" ID.
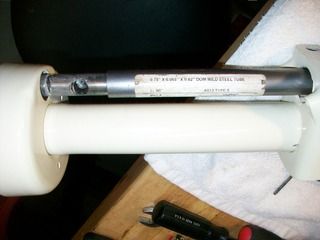
Ok, so what to do here? I need to get the ID to match up to the stud on the bottom of the steering column cup (5/8" OD exactly). I happen to have a 5/8" drill bit so into the vise goes the steel tube. I wanted to use my drill press but this tube needs to be at least 29" long so I could not find a way to use it. Back to the handheld drill... 
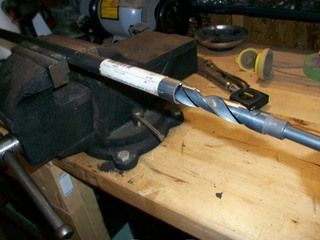
I made a mark to let me know how far I needed to go into the steel tube to give me 5/8" ID to slide over the stud.
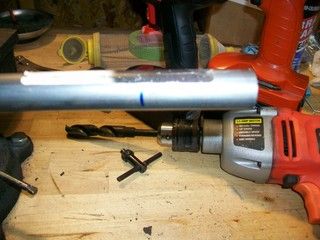
I watched the drill a good bit during the process to make sure I was getting deep enough, but the label on the tube told the story as the further I went the more burnt the label became - easy breezy! After the ID was widened a little bit the tube was slid over the stud to check fitment.
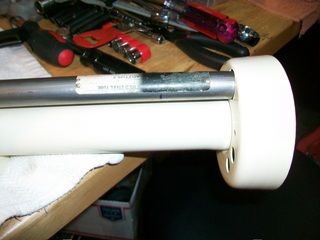
Next, we went to the lower portion where the shift levers were located and the end cap fits to the steering column tube. At that point we eyeballed the location to give us a cutting reference for length. No need to be so precise here - this is not a service part and will not function. This is solely for aesthetics.
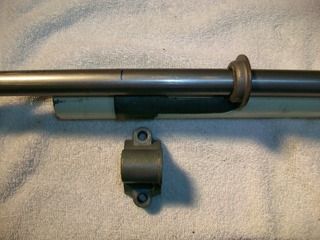
Back to the vise and a cut off wheel and we were in business. The tube fits extremely well and when it is primed, prepped, and painted no one will tell the difference. It will resemble a factory part.
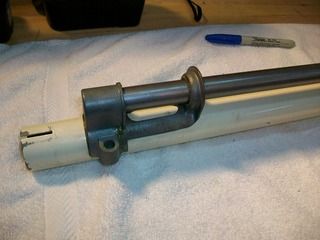
|
By Daniel Jessup - 9 Years Ago
|
Been a long time since my last post ---- my thread is starting to get buried on the forum!
The situation with the steering column bearing and bushing was resolve. A few friends here on the site gave some direction as to what bushing should be used, spring, placement, etc.

The second photo shows the bushing surrounding the shaft and resting in the bearing. This will keep the wobble out of it for sure. For some reason, this was missing in my parts lot I got some time ago when I bought a 56 Ford steering column, shifter, z bar, and manual transmission car parts. I think we have this sewn up now.
I did prime and prep the fake shifter shaft that I am going to install to replace the original since we put a Hurst Syncro Loc in the floor. I have only shifted on jackstands, but with the wheels and transmission moving we liked the way she shifted.... smooth.
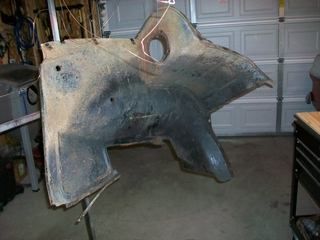
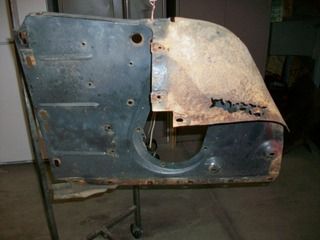
Now to start putting the front end sheet metal back together. But first we needed to assess what we have and take inventory of the clips, hardware, and original rubber seals. I hung the inner fenders and deflectors up in the air and stripped, bagged, and tagged the parts that came off. The air deflectors took a trip to the bead blast cabinet (barely fit in there) and then we set about a plan to work on that nasty driver's side rot.
You can follow along in the photos to see what I did. It is certainly no professional repair, but I liked the results. I need to purchase some sheet metal forming tools - that would help lol.
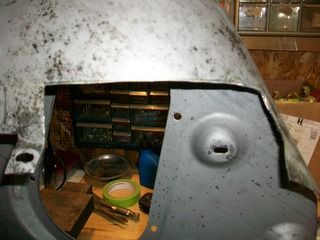
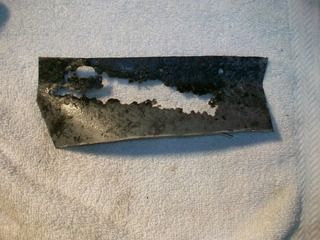
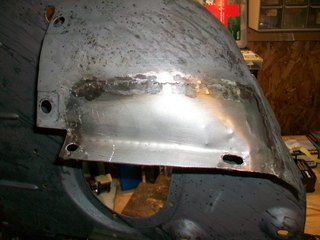
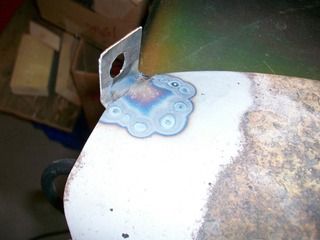
I also had to weld a tab on the passenger side inner splash pan, just a photo here to double check weld penetration.
Next we were off to paint since the weather was so good...
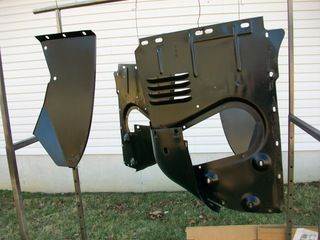
And since we were feeling froggy today and looking for a challenge, I decided to attack the steering wheel with a dremel tool to open up the gaps - I also took 120 grit sandpaper to it (not shown). I am going to get some PC7 Epoxy and start working on it next week in the basement. I did a 55 wheel for someone on California about 5 years ago ---- yes, this is work. 
|
By Daniel Jessup - 9 Years Ago
|
I have been out of town for a few weekends but during some of the weeknights I have been able to get a few things done. I did take steering wheel and fill all of the cracks with epoxy as you can see. The cracks around the base, or inner circle where the spokes meet, were very bad and there was much to fill. I am beginning to see why NOS steering wheels are so pricey. I wonder when a company will start casting OEM Steering Wheels for our cars? I think the tri-5 shebbies have a few companies that offer them.
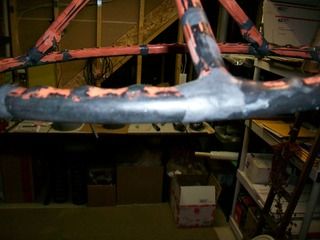
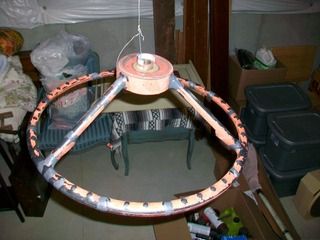
I am going to let the epoxy cure in the basement tomorrow, so I just hung it from the rafters.... along with the panel that holds down the hood. Would you believe it fit in my blast cabinet? After blasting I brushed it with a new metal prep and primer. I will scuff sand it later after it cures and plan to paint it gloss black.
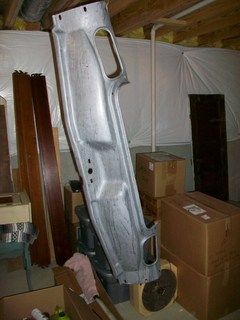
On to those pesky vent tubes that let in the fresh air or heated air depending on which way you turn the flaps...
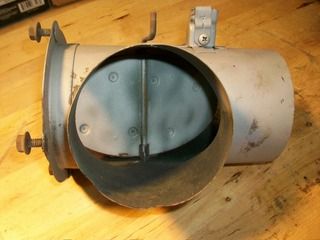
The one above is for the passenger side "magicaire" heating system that doubles up the passenger side vent tubes for fresh air, heated air, etc. Both sides actually need new rubber seals. I was planning to blast these pieces and repaint anyway so no big deal. However, drilling out the spot welds can be very tricky when the seal plates are attached the pivot inside the tube. (NOTE: another helpful car guy said that I could have pulled the pivots straight out of the door seals without drilling any spot welds and simply drilled out the plates on the vise - DUH... can anyone else speak to that?)
Anyway, I guess trying to make things hard on myself, the plan was to drill out all spot welds WHILE THE PLATES WERE STILL IN THE TUBE. How could one accomplish this feat of unneeded skill and expertise? well.... check out the 2x4 cut for the purpose of keeping the plate at a good angle of access.
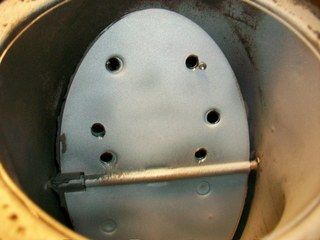
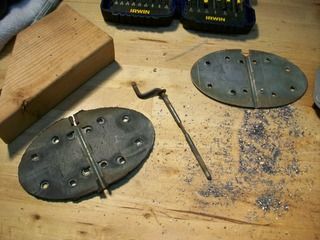
That was all good and well for the passenger side tube. Since access could be gained from 4" hole on the side of the tube, I guess a monkey could have done that with one arm tied behind his back. Ok, so what to do with the other side?
I could only drill out a weld or two, and as you can see there were six a SIDE. So, I got the Dremel out and wallowed out the spot welds only on one side of the pivot. This made it easy to push the "opened" side past the pivot and then remove the plate assembly from the tube. I could then put the plates on a vise and drill out the spot welds pretty easily.
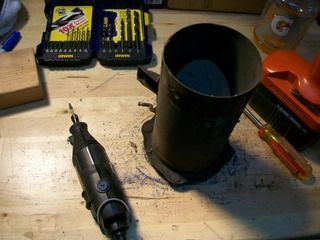
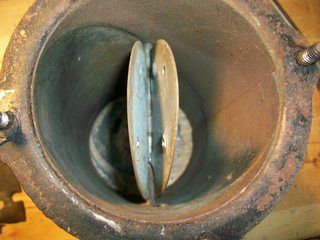
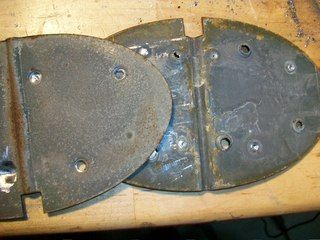
I also took the "insulated" sheet metal tubes that are made to connect the 90 degree elbows off the firewall to these tubes and cleaned them up pretty good. Another member, Mark T, gave some really good advice on using something called Armaflex and then a picture of some material to make a homemade cabin filter for each side.
We will keep you "posted"
|
By Daniel Jessup - 10 Years Ago
|
Also trying to figure out a Hurst Syncro Loc Shifter that I just had delivered... not quite sure I have it all right. Maybe I can put a post up elsewhere to get some help in some questions. I could not get the shifter to go into 1st or R (just sitting on the bracket, no arms attached). Can I hook the arms up with the levers on the side of the transmission in their current position or do I have to turn these upside down. It looks as if they need to stay down from what I can tell. How do I get the OD lockout lever in a position to move because of this bracket setup - will the current position work?
check out the photos and fire away with any helpful comments. The shifter is only 12" above the mechanism (including the ball)... not sure this is going to be tall enough in the car.
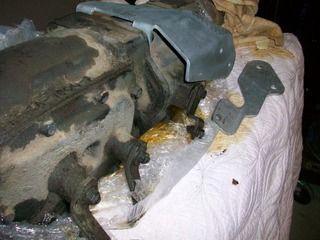
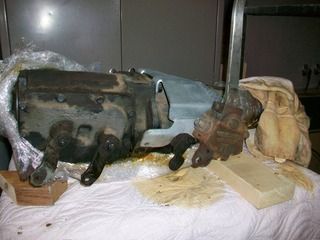
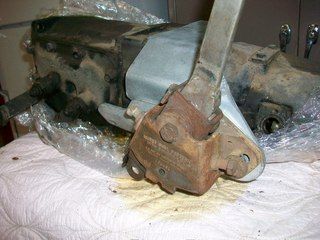
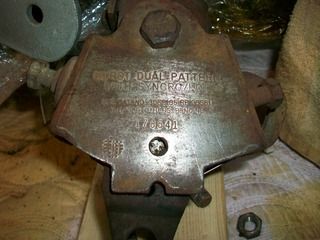
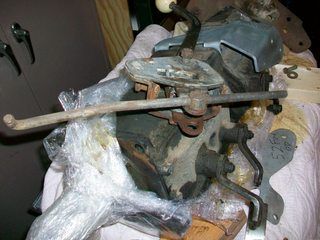 Any ideas on what the bracket and rods below might be for?
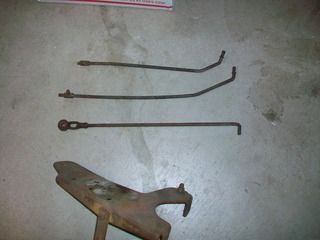
|
By Daniel Jessup - 10 Years Ago
|
Here are a couple of photos of the interference from the bracket/OD lockout lever.
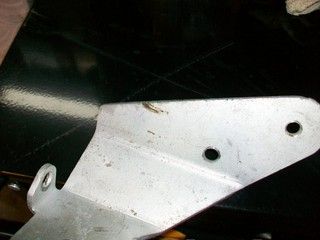
You can tell by the photos above that the lever was hitting the Hurst Bracket and leaving that small arc of grease. I put the bracket in a vise and carefully nudged it over with the vise to make the bracket widen out a little bit. This gave me about an 1/8" clearance and I am pretty happy with it after bolting everything up it looked pretty good.
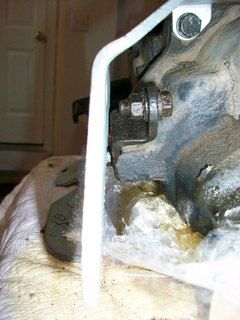
The shifter shifted into all positions just fine tonight with 0 play - nothing seemed sloppy at all. I did have one shifter rod from Hurst and kind of mocked it up in the shifter and put it up to an original lever on the case (after flipping it upside down). I know that Hurst made levers to replace the originals but I think these were all flat stock right? Seems like the offset of the original levers would help you keep a straigther rod since the line looks very good. Maybe Hurst uses levers that essentially have a shorter arc because they are smaller?
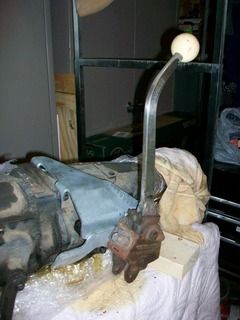
|
By Daniel Jessup - 10 Years Ago
|
Before I give you part 3 here, let me say I am very happy that I have a duplicate transmission out of the car. The constant adjusting, fiddling, bolting/unbolting, removal, installation, etc is quite easy since there is a transmission on the bench.
Ok, so today the postman leaves me a couple of boxes on the doorstep (actually 3 boxes but the third box contains a pair of Holley 94's to rebuild). One box holds a very nice Mastershift with a nice handle that is LOOOOOOOONG compared to the syncro loc I have and the other box contains Hurst shifter hardware arms and the like, prebent specifically for this overdrive transmission.
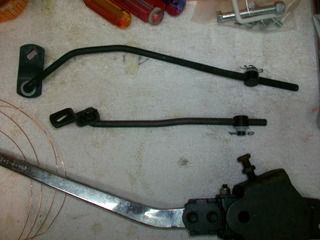
Photos of the rods installed on the syncro loc....
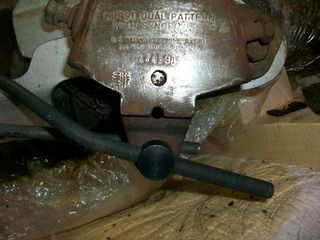
And photos of the Mastershifter (I am told it is the updated version of the syncro loc)
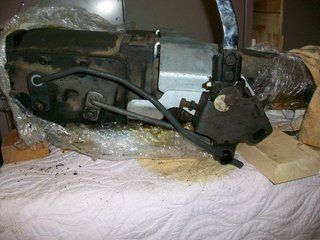
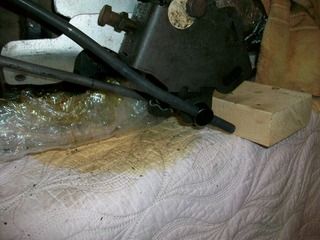
While things look good if you look closely you can realize that when the shifter is in second the rod is interfering with the shifter case... reason? The Mastershift case is slightly larger than the old Syncro Loc. Also, if you look at the bracket you will find that where the pivot hole lined up for the Syncro Loc, the hole does not line up for the Master Shifter.
I like the Mastershifter and the option to change out shifter arms pretty easily. It is definitely "larger and heavier" than the Syncro Loc.
Back to the benc and more modifications... time to elongate some holes and to bend a rod ever so gently.
|
By Daniel Jessup - 10 Years Ago
|
Look what Santa brought me for Christmas...
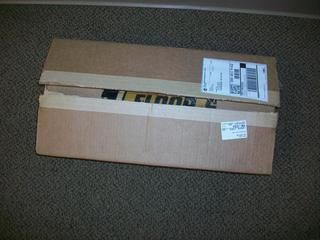
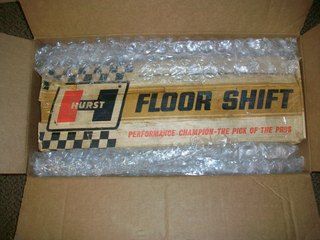
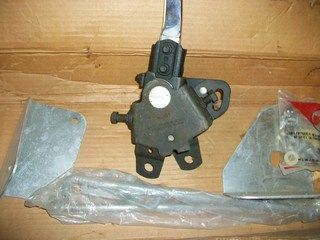
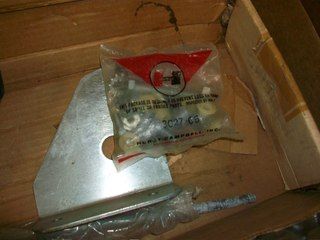
Yep - it is a Syncro Loc shifter, NOS, with a removable shift lever. The brackets and arms in the box are for Pontiac, but the bag of hardware should also be handy!
|
By Daniel Jessup - 10 Years Ago
|
And here is the install of the Christmas Hurst Syncro Loc...
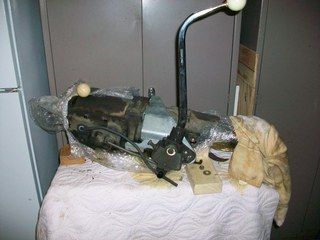
for the sake of reference, here is neutral
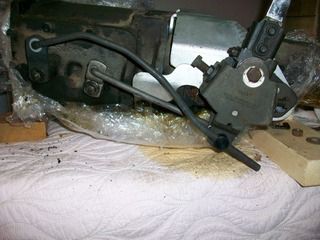
1st Gear
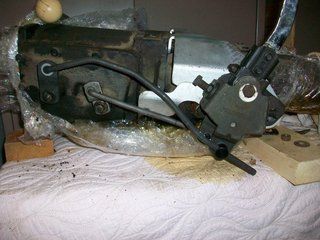
2nd Gear
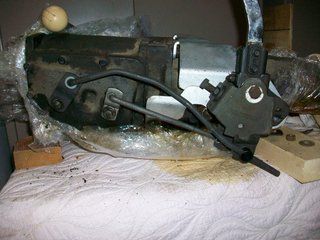
3rd Gear
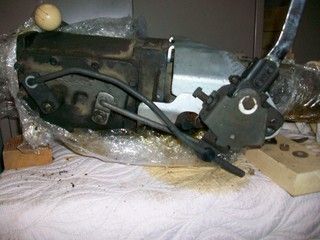
What a smooth little shifter she is too.
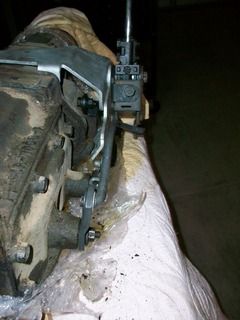
The line up looks good and all things are finally normal. I guess the 3rd time, er... 4th time is a charm? Now to get down to brass tacks and get this installed on the transmission in the car. Hopefully I will have some time to do it this weekend. The installation looks straightforward enough.
Anyone out there in need of a Master Shift unit or the other Syncro Loc I tried? they are for sale for what I got in them. danaxjessup@yahoo.com" class="SmlLinks">danaxjessup@yahoo.com
|
By Daniel Jessup - 9 Years Ago
|
You know those times when you hear someone say, "This won't take long, only an hour or two?" and then you end up spending most of your day tackling a job that throws every problem in the book at you? Your situation defies the odds and unlike the average completion time for the project you end up adjusting, tweaking, cutting, drilling, adjusting some more, assembling, installing, re-installing, etc, etc, etc. To top it all off I even lost about 7 important pictures from my crazy camera that somehow "corrupted" photos I took!
I lost track at the amount of time I spent under the car today but the end result was extremely SATISFYING! 
We will start from the beginning.
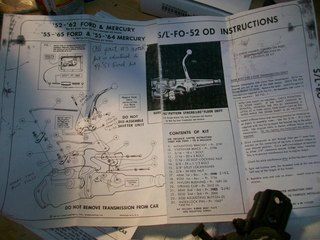
Since the old transmission on the bench was an excellent means of mocking up all of the parts for the Hurst Syncro Loc floor shifter, it was time to remove the stock Ford shifter rods and install the assembly. Easy breezy right? 
After removing the original shifter arms and levers on the side of the case I installed the Hurst levers as pictured here:
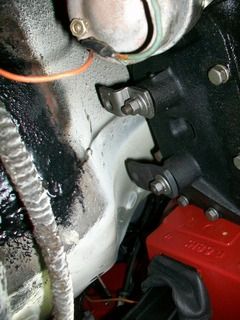
That part of course was pretty easy and went well. I made sure they were on the correct pivot and oriented correctly. Next, time to remove the two upper bolts on the case and install the main bracket that looks like this...
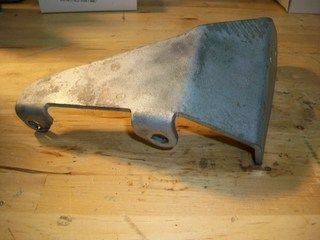
That was a little more difficult than I first expected - there is very little area above the transmission tunnel and your hands get awfully big under there when you are trying to ratchet on things and get everything connected!
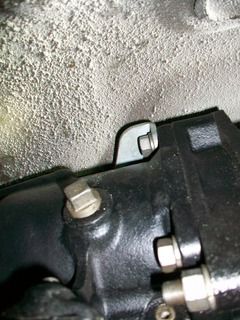
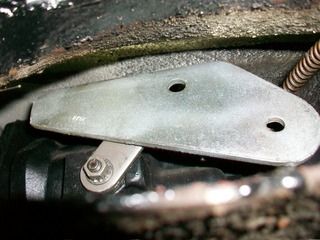
The passenger side attached pretty quickly but the driver's side was a bear - that is the side where all of the shifting, hardware, and speedometer cable go. I had to make some adjustments but as you can see at least the overdrive lockout lever still moves freely. Glad I got that one corrected on the bench! 
Next came this bracket...
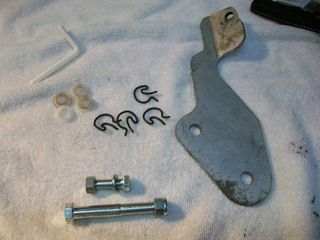
It attaches up front at the top bolt that secures the solenoid to the transmission...
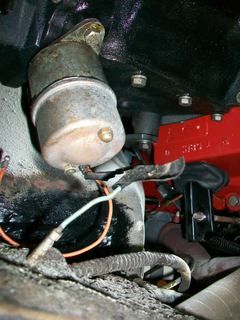
The two holes at the rear of this plate line up with the main bracket and both holes are the attachment points for the shifter itself. This part went well - no hangups.
Now we come to the shifter. The first thing I did was to put the neutral rod in place (white, L-shaped rod in the photo below)
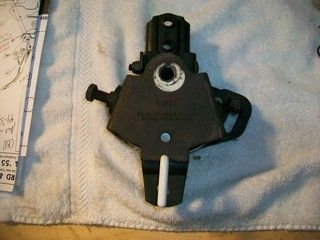
This white rod needs to be in place when you are lining up your shifting rods that go from the shifter to the transmission levers at the side cover. Also, keeping the rod in place while adjusting the TILT of the shifter (towards the dash or towards the front seat) is an added bonus.
Next comes the hack job on the floor pan. The idea is that the shifter needs to be installed on the bracket, then using a punch mark the center of the hole you need to cut so that the shifter arm can be connected through the floor right? WRONG - not with this setup. The clearance is so small that the Syncro Loc could not even be attached to the bracketry.
Great....
What to do? I decided to orient myself from above by drilling two holes. One at the pivot of the shifter (center line of shifter) and one immediately above the second hole on the bracketry (this is where the slot is located on the Syncro Loc). This took forever, but I wanted to be sure I cut out NO MORE THAN WAS NECESSARY to install the shifter. Check out the picture below...
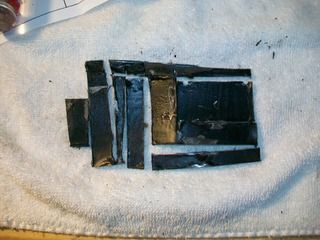
:p Those are all of my cuts. I started with the large rectangle you see, but each time I kept finding out that something else interfered, one of the stop bolts got in the way, etc. Crazy stuff I know, but I ended up with what I think is the smallest footprint for the shifter going through the floor pan.
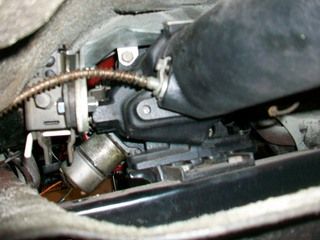
more in the next post
|
By Daniel Jessup - 10 Years Ago
|
Been over a week since my last post, but man have I been busy. We celebrated my wife's 40th birthday, I have been packing up boxes in the house and the garage like a Tazmanian Devil because we close on the house on Wednesday the 24th, and oh yeh - I am trying to get this ol' 55 moving on her own before we haul freight here. Of course Father's day is also coming up and I shipped off a nice little load of antique truck toys and some cards to my father down in NC, I am sure he will like them. My family gave me my gift early - a new creeper. My son was so excited he talked the rest of them into it. So, Ethan came out to the shop and decided to assemble it for me. Nothing like working with "Lug Nut Junior"! He helped me quite a bit this week - bleeding the brakes, putting on the finishing touches, etc. He even dropped a wrench on his head while under the Y block.
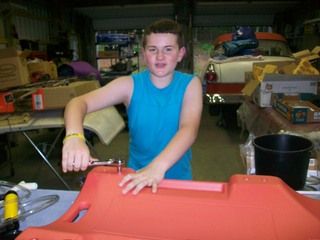
Long story short, the son and I pulled her out of the garage under her own Y block power yesterday with loads of success... no leaks, no trouble, and we had a lot of fun together in the midst of the moving melee. I will have to record video when we pull her out again on Monday to load it up for the trip to Loveland, Ohio.
Earlier this week we bled the brakes and tightened down some of the fittings that were dripping... I thought I had them all cinched down but there were a couple of leaks where they needed a quarter turn or so.
I did wire it up just for a "hotwire" with the original switch and keys, a "batt" line/"start" line/"ign" line so that we can just hook up a battery to a relay and off we go. You can see my zip ties in the photos here. I would have liked to have had the Rebel Wire harness in and ready but I ran out of time (along with other things I wanted to do).
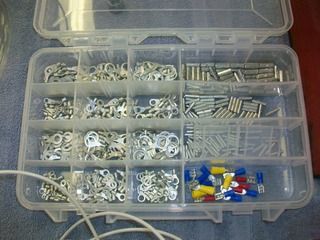
I don't know about you, but I like using the uninsulated wire terminals, crimping, and then using the heat shrink tubing to seal it off. The box above is a custom kit that I put together and then organized the ends in a lure box from a big box store. 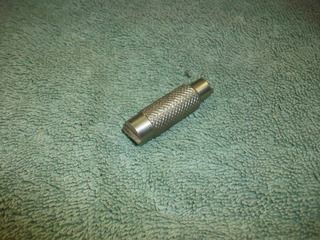
Don't start working on dash parts unless you have that little tool above. It is a must when taking off the collars and chrome fittings for your dash switches! 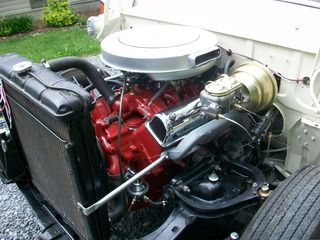
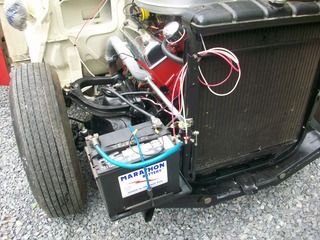
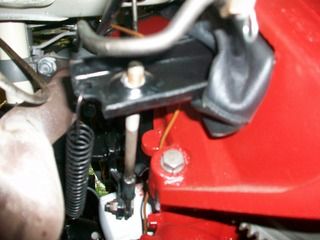
I did get the "3 on the tree" all figured out and at a stand still the shifter will put the transmission in all gears. I did use some nylon washers to tighten things up a bit but you can tell by looking at the push rod that when the clutch pedal is depressed the clutch fork gets too close for comfort with the narrow rod that is actuating the lever on the transmission. I lengthened the push rod by cutting the rod in two pieces, welding a sleeve to one side, inserting a 3/8" stud in the center, and then welding the other side to the sleeve. A very solid piece indeed. As you can see though I did not need too much room, only about 1/2" to get the actuation I needed. After hooking up some conduit to the radiator frame and the first exhaust bolt on either side I placed a starter relay on the radiator frame and got the battery secured to the car frame. The plumbing for the fuel was pretty straightforward but my son and I had a hoot trying to the fill the transmission case. I guess I need to get one of those drill operated pumps or something. We ended up running a hose from above the firewall to the main case and emptying a few quarts in there. Then we went to the tailshaft where the overdrive is located and I ended up using a small squirt bottle. It held more than I thought it would back there. Most of the linkage work was temporary. especially the steering column tube. That collar that attaches the tube to the dash was pretty tight. I think next time I am going to cut it in half, that should work better. 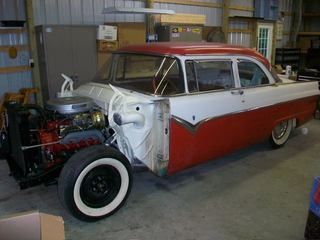
|
By Daniel Jessup - 10 Years Ago
|
It has been quite some time since I have uploaded any photos to this blog about the 55 Ford Club Sedan front end refresh but we have been swamped with this move. It took 3 U-Haul Trucks. First trip was a 17 footer, the next trip was a 26 footer, a 20 footer, a two dolly, and of course a trailer. (I now own stock in U-Haul ) What a mess.
Here are a few photos of loading up and the actual trip out to Loveland, Ohio from Winchester, Virginia.
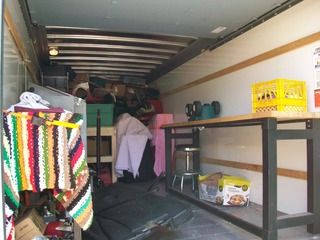
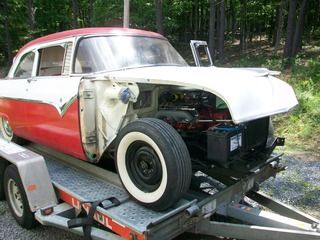
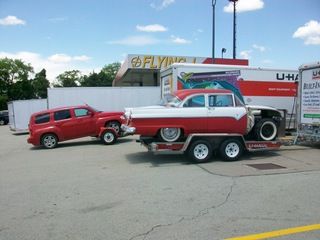
We made good time and everything traveled well... pretty much uneventful. The big event was actually the week before we left when I loaded up the truck that had all the parts and tools. I had decided to load up my son's basketball goal. That sucker was filled with sand at the base and very heavy. So, I decided to take it apart to load it in sections. After beating on it for 30 minutes I finally got it apart and got it loaded. It just so happens however that I forgot to restrap my tool box that I had to get into. I only the drove the truck in the driveway for about 60 feet, but that was all it took - you guessed it. The thing went careening out the back end and onto the pavement. DESTRUCTO box now. No, there are no pictures, I was not in the mood. I guess the heat had gotten to me that day.
When we showed up in Loveland at the house, (Loveland is right next to Milford) I could not find both of the wheels to the basketball goal. I felt like backing over it with the truck since that crazy thing had been the cause of so much grief. Oh well, the trip was good and everyone is safe and sound. Tool carts I can replace - people I can't.
|
By Daniel Jessup - 10 Years Ago
|
I have moved into a nice development called Ashton Woods. The kids and the wife like it - I personally don't care for it. Everyone is right on top of each other, no room for anything, etc. That crazy basketball goal even got egged early this week. There is a nice pond just behind the house though that we have already been fishing at and it lays pretty nice. We are renting for now and are going to spend some time looking around the area at different properties.
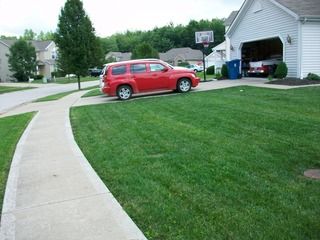
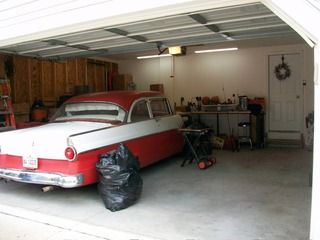
The big deal - I now have less than HALF the space I had in the old Y block skunkworks out in Capon Bridge, WV, where we lived. The garage had ONLY ONE OUTLET and then only two light bulb fixtures. We fixed that pretty quickly. No subpanel in there, no wiring for a compressor, etc. I am lost. I had to rent a 10x10 storage unit in Milford to hold the extra parts and what have you.
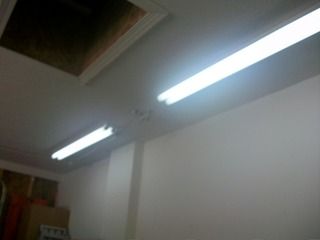
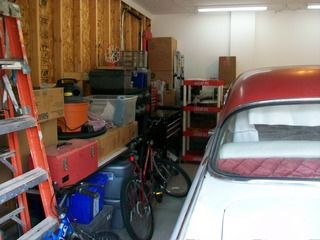
There is a large, dry basement though and you can imagine how much I have stored away down there.
If you have any tips on storage solutions and space-saving ideas - let me hear them!
On a different note, I am putting a youtube video of the 55 rolling out under its own power on the trailer. Once I have it loaded up I will post a link. I have not run it in 2nd or 3rd, but of course the thing was only wired and plumbed to be loaded on the trailer and go into the garage under its own power. I am kind of thinking though that we have a binding problem with the extended clutch push rod. I wanted to go with a floor shift anyway.
|
By Daniel Jessup - 10 Years Ago
|
Thanks fellas for the encouraging comments.
Here is a link to the load up.... https://m.youtube.com/watch?v=iKFOQ0RzxMk
Enjoy lol - it's pretty mundane
|
By Daniel Jessup - 10 Years Ago
|
I am still alive if anyone cares to know. I have not had much time to do much of anything what with the new move, setting up a garage that only had one outlet when I started, etc. I reckon I travel quite a bit more too. Hopefully I can get back to things by the holidays. I hate I missed Columbus being so close.
|
By Daniel Jessup - 10 Years Ago
|
Been a long time and this move has been a real kicker, but I have finally been able to get back into things here and there. First up are a few photos of a Christmas present for my dad. I took a 55 Ford Mainline Headlight Hood and turned into a clock... I think he will like it.
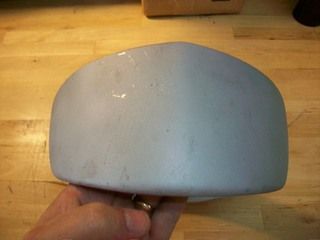
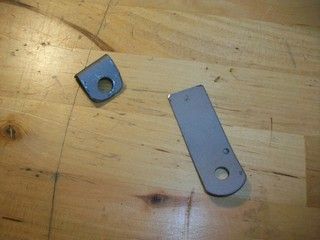
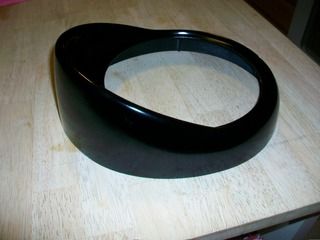
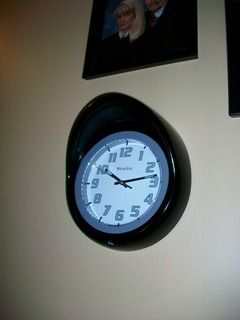
|
By Daniel Jessup - 10 Years Ago
|
Big hangup... check this out:
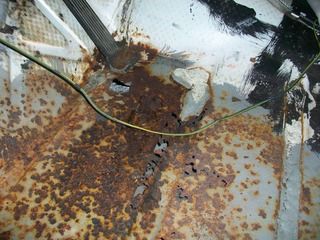
The driver's side floor pan is rotted completely through. A little bit of a setback on the timing here. I thought for sure the floor was pretty solid but that was only by looking from underneath and not really "banging around" with anything. However, when I pulled back the old carpet to throw it out about 2 lbs of rusted metal STUCK TO THE JUTE UNDERLAYMENT and just came right out. I have already had a replacement floor pan shipped in:
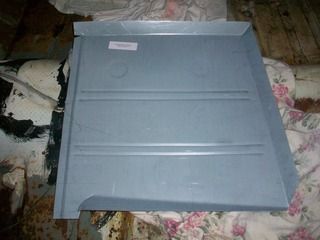
I did get the dash installed but only have this photo of some of the assembly on the bench
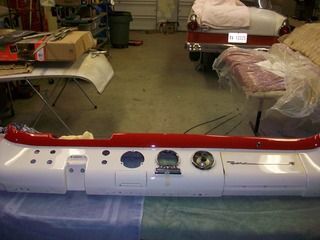
And, this wiring harness came in today so I have some work ahead of me!
|
By Daniel Jessup - 10 Years Ago
|
Been real busy lately. Found a place to live in Milford earlier this week, and we go to closing on our house here in about 2 weeks or so. I did get the chance to get back with it last night though. I built a "cocoon" around the area that I worked on for the floorpan because I already had the new dash installed and I did not want to ruin the headliner, the door panels, etc. Basically I wrapped the dash in plastic and then put cardboard up all the way around - even to protect the headliner. When I weld and stuff starts spattering hopefully it will protect things.
![]()
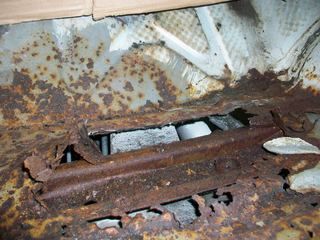
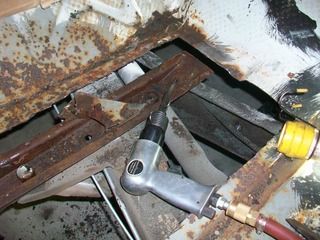
The old rotten floor came up like butter. However, I was surprised to find how little of the floor was rotten. There was better metal in places than I thought so the section I had to cut out was not too big. I use the holes in the strut as a reference point so that I could trim the new floorboard to size. 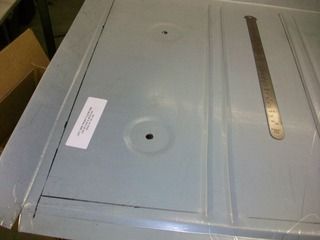
The floor brace/strut is very strong so I just took a Roloc to it to clean it up for a sold arc for the mig welder. I did transfer the measurements of the strut to the new floorboard so that I could drill 3/16" holes so that the floorboard can be spot welded to the strut. The rest of perimeter of the new metal was also drilled out for spot welds, but I am going to see what I can get with lap welds in some areas. I primed the new floor with Weld-Thru Primer as well. I have sealer and I also have chassis black paint all ready to be applied once the repair is made. The only thing I will have to do after all of that is redrill the holes for the accelerator pedal. Hopefully I can get to all of this over the weekend.
|
By Daniel Jessup - 10 Years Ago
|
MoonShadow (6/6/2015)
Daniel, Milford, CT is about 3 hours from me in New Hampshire and 5 hour from Bill Myrand in Maine. We will have to meet up someday. Maybe at the nostalgia meet at New England dragway. Chuck
Chuck, I would love to but I need to let you know - the Milford I am speaking of is in OHIO (Bob Martin country out there I reckon). So, in all actuality I will be moving farther away from you. sorry about the confusion
|
By Daniel Jessup - 10 Years Ago
|
You can follow along in the photos below to see the floor pan work. I did cut out all of the rot, checked on the condition of the remaining, and then cut the panel to fit. The panel was then drilled with 3/16" holes for spot welding and then fitted to the floor, shaped, fitted again, shaped, cut, filed, and then fitted one last time. I used the orientation of the body bolts to help with measurements and orienting the new metal correctly. 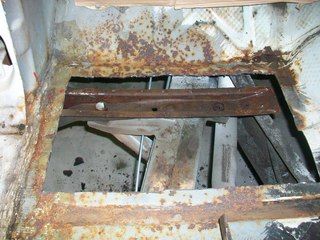
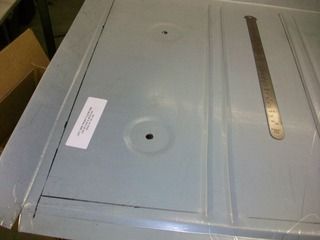
I did use a "weld through" primer on the top and bottom and it worked pretty well. The conductivity must have been good because I had to dial back my welder because of early blow throughs and all. I also used self tapping sheet metal screws to keep the panel tight to the overlapped floor so the seam would hold pretty good. 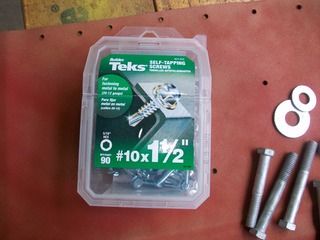
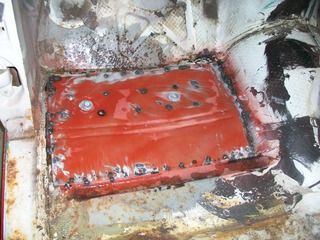
The panel is not perfect, but she looks good from underneath. I still need to hit it with sealer and then I will paint both top and bottom with chassis saver paint. On to other things... I was glad I had restored the pedal assembly sometime ago. It felt good to just pick it up and bolt it in. I did try to duplicate Ford's original "anti-rattle" fixes by using a spongey type of neoprene for the bracket to rest on the dash (I believe the factory used cloth?). I did that same thing when I mounted the dash too. 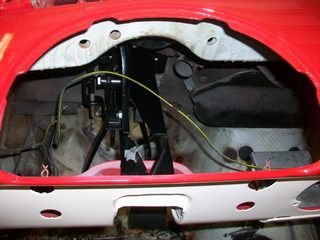
Next came the mounting of the aftermarket MP&B Power Booster and Master Cylinder. The instructions given on paper were good, but not very thorough. There was something they missed on their sheet - namely the adapter plate that bolted to the firewall. It held the rubber grommet for the brake pedal rod/lever. 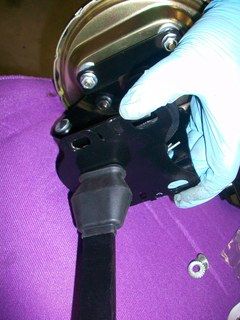
I got everything mocked up and wondered how the lever was going to be sealed to the firewall because the instructions never mentioned. I just figured it was because it fit so many years, blah, blah, and I would have to make one. I actually took measurements and started wondering where I could find some generic grommets so large. I went back to the shipping box to put the MC box back inside and what do you know? The adapter plate was lying there in a plastic bag. I picked it up and knew immediately what it was for. Then I sighed and said, "Yep, you've got to take it all apart Dufus!" here is a photo of the booster assembly with the special bracket for the firewall 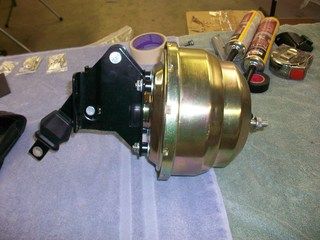
All went well until I mounted the MC just to check on my bends and mockup for the brake lines. All went well up front - no issues - just the right amount of distance. However, you can see what happened at the rear. 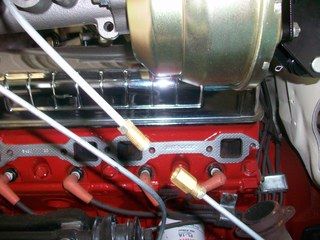
Aaaaaaaaaaaaaaaaaaaaaaarrrrrrrrrrrrrggggggggggghhhhhhhhhh! I am missing just a couple of inches. So... back to the store to get a longer brake line. I will say that the brake lines I had were a complete set from Jackson's Auto Parts but they were a set for original brakes - not for this FrankenFord I am putting together. However, the booster and MC do fit well and although it is kicked it into the engine compartment more than I would like, it does not interfere with anything. 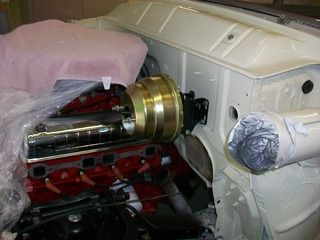
I did check the fit of the exhaust manifold and what have you just to be sure. When I get more photos loaded I will tell you about all the fun we are having with the clutch linkage!
Here is the little booger that is so much fun:::: 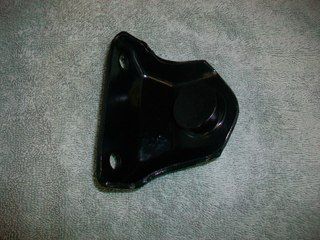
|
By Daniel Jessup - 10 Years Ago
|
The floorpan and quite a bit of the surrounding floor has been cleaned and now painted with Chassis Saver Antique Satin Paint. I had a whole mess of it so I figured why not. I am probably going to use Dyanamat (or something similar) anyway. 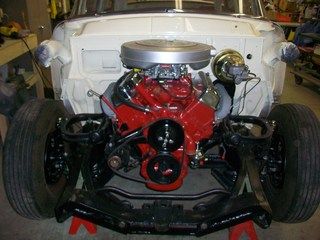
The engine compartment is looking better too. 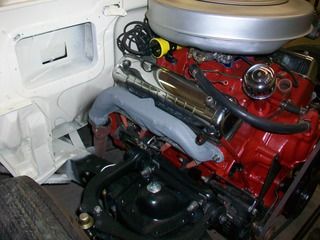
I made up my own bracket for the return spring. You can see it below. 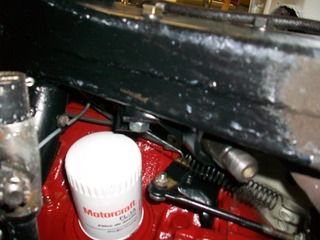
It sure is getting tight around the clutch pivot/steering gear area! 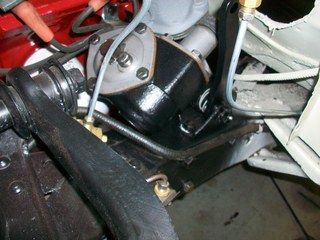
|
By Daniel Jessup - 10 Years Ago
|
crownvic55 (6/11/2015)
Daniel, If, as the saying goes, cleanliness is next to Godliness then you are in very good shape. Your work is immaculate. Ben
Sirstud1 (6/10/2015)
Love the build! I also have a 55 I'm working on... mine will be ratted out tho.. check it out... hope I can turn to u for some advise if things get complicated... lol. https://flic.kr/p/uaF8bN
Thanks fellas, my wife quipped the other day, "Why don't you just put the fenders back on and run it?" Too much pride in all this I guess. I want it to be the best driver it can be. It's not a show car but my FIL should be pretty happy with it.
|
By Daniel Jessup - 10 Years Ago
|
Believe it or not, the Harbor Freight "special"  You would not believe how well it sprays. It is not too versatile as it only comes with a 1.4 tip, but it sprays the urethane topcoat very nicely and evenly... NO DRIPS at the gun either. When I get to painting the exterior I will probably pick up a nicer gun. Maybe the Eastwood Concours gun - it has good reviews.
|
By Daniel Jessup - 10 Years Ago
|
I do wonder Dennis if that will work with this Urethane. It comes from Eastwood and the Tech Sheet says that no reducer is required (it seemed pretty thin before mixing with activator/hardener). When I added hardener to it, I mixed per the 3:1 ratio and then sprayed about 10 minutes after that. Would you believe that within 30 minutes the paint had already hardened? I had a devil of a time cleaning up the paint gun. It ended up getting filled with crud once I poured paint thinner in the cup to clean it out. I think next time I will go with the disposable cup. Once I am done, remove the cup and trash it, install the clean cup, fill with thinner and then spray to clean out the gun itself.
Have you ever used a Urethane product like what I am talking about?
|
By Daniel Jessup - 10 Years Ago
|
For all the drama around here when I set out to get something done on this old Ford, I know I could talk to one of these cable/satellite stations and get my own reality TV show dagblastit!
For starters, two days ago I was prepping to remove the Y block from the engine run stand so that I could put it on free standing legs, mount the flywheel, clutch, bellhousing, and transmission with every intention of dropping the works in on Saturday (yeh - is that tomorrow?). When I get to pokin' around I look things over and see a shiny thin line at the front of the valley pan where it meets the block...
"Is that just silicone?" I say to myself. It was so thin I had to get a screwdriver to touch it and see what it was made of. "Dagblastit!" I said as I smeared the oil off the tip of the flat blade screwdriver. "That valley pan is leaking!" 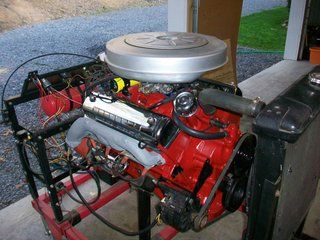
You may recall during the initial run all things were good, just something small at the oil pump that needed one bolt tightened. I even checked all the way around after that episode... nothing. Until the other day! So... long story short I removed the intake and parts, removed the valley pan, cleaned all surfaces and REMOUNTED the sucker. If it leaks now I am going to take a CAULKING GUN to it after it is in the car. As a side bar, I did notice that the very front corner was a tick higher than the rest of the pan so it was NOT perfectly flat when installed originally. Ok, so on to bigger and better things. I looked over in the corner of the shop and my eyes met the hard fuel line from Kingdom come - yep, it was time to take a look at this thing and get on it. After all, I paid MORE FOR SHIPPING than the line cost itself lol. That sucker is HUGE. I jacked up the driver's side and took a look-see. "You have got to be kiddin' me," I said right out loud (by myself no less, just me and the tools, parts, and God). Seems the factory put the fuel line between the body and the frame in the rear of the car so there ain't no way in the place where Satan sets up shop am I ever going to get it on in one piece unless I RAISE THE BODY OFF THE FRAME. So much for a front end r&r! This is getting ridiculous. After a few helpful fellas on the internet chimed in to confirm, I said I give and it will have to be "snipped". I guess now I am going to install an electric pump just because I can and maybe I just like the greater opportunity for another ISSUE!  Alright, so no big deal, let's keep going. "What else?" I say to myself... "There is plenty to do here." And so there is, I have brake lines waiting to be installed, new wheel cylinders, got to get the 3 speed on the tree all cleaned up and connected. (By the way when I shot the firewall the other day I also primed and painted the steering column... vavavoom baby! She looks real good.) 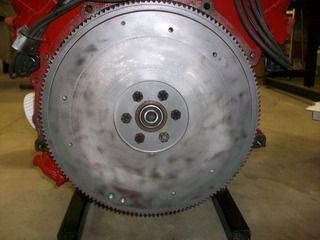
I sauntered over the engine I had finally got all buttoned up and off the run stand. It was sitting on its free standing frame unassumingly by the workbench just minding it's own business waiting for its tail end. I cleaned up a very good flywheel that had already been turned, installed a new pilot bearing, torqued the flywheel to specs, and the looked for the clutch and pressure plate... "Uh, where is the clutch and pressure plate?" I looked around for a LOOOOONG time. "Jessup, how do you lose something that large? I mean the small spring clip for the clutch fork, I get it... but a clutch disc and the pressure plate? Really?"  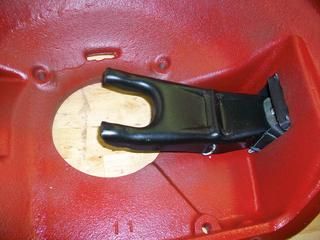
Still can't find them. I don't what I did with the box or the parts. I do have the throw out bearing. With the move going on and all the packing, slinging, tossing, kicking, beating, and what have you I have no idea where it got off to. Ridiculous. So now where are we... oh yeh - at a stand still on the engine and transmission. I could have sworn that the old 292 just sat there and winked at me when I wasn't watching!  At least I manufactured a decent clip for the clutch fork... just a couple snips and turns with an old coat hanger and there you go - that's good for 15 more horses right? Well, whatever the case the Y block follies continue... However I did want to leave you with a photo of an invisible part I NEVER had but do need... It is the clutch equalizer bracket that bolts to the block at this location (I took two photos - one in darkness and one in the light, trying to get one of those ghost shots but it didn't work!) 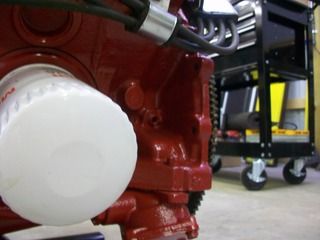
Let me know if you have this apparition.
|
By Daniel Jessup - 10 Years Ago
|
I think I have located the "ghost of a part" from two different sources and it looks to be the booger. You can view the part photo over at y-blocksforever.com. Hopefully we will have that soon. Since I could not find that stinkin clutch disc and pressure plate I had to order a new set. They are on their way. It is a 10" version to match the flywheel... hopefully.
Since the hard fuel line kicked my butt on installing it without any splices, I decided to kick its butt back and place an inline electric fuel pump on the frame rail. I am glad I decided to replace the fuel line - it was nasty inside and out and was very brittle in several places, but let's be honest - it is 60 years old! (sorry to all of you "mature" folks out there - no insult intended for you!) 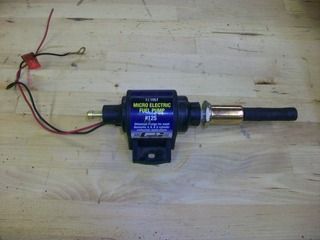
The old fuel line had to be cut in two different places to be removed, but all of the clips were in good shape. Also, I had the gas tank boiled out and coated several years and it is great shape. However, when I got to the fitting at the gas tank, it was a tight little booger. With little space afforded me, it even rounded off with a flare wrench. So, I broke out the set of Crafts man brand easy outs for NUTS (the drill easy outs NEVER work for me lol - I've got a load of stories on these pieces of junk). 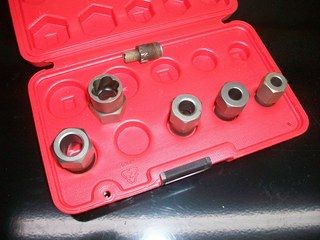
Suffice to say, the idea is that you take one of these "doohickey's" and place it on your nut or fitting (that is right I used a plumbers pipe cutter to cut the line just at the fitting) and then use a wrench to turn the doohickey counter clockwise. It grabs the fitting and presto - you've got it out. Miracle of miracles - this tool lived up to its promise this instance. I ended up cutting the new line (boy that was fun - hacking up a line that costs about $150 when the shipping was included) in two different places. One for the frame rail where the electric pump would be installed, and then one for going over the hump and between body right there above the rear axle housing. Tight I tell ya! The cuts I made on the NEW line were exactly in the same locations as the OLD line so I had point of references and I knew how the bends and curves went in and over the frame neatly. SAVE YOUR OLD LINE before you cut your new one! Also, remember that you will need to take out extra hard line to make room for your pump or even for your rubber hose at your splice. When we got down to mounting the pump on the frame, another "little used tool" came into play. Check this out... 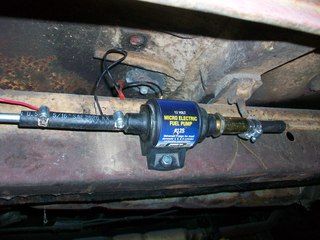
I have owned this tool 15 years and have used it..... twice? But let me tell you, it worked flawlessly. If you look at the fuel pump mount above you can tell the mount uses two holes, top and bottom. The drill would go in straight on the bottom hole, no issues. But the for the top hole the rocker panel was in the way big time. Break out this little tool and away we go! After the holes were drilled I tapped each hole with 1/4" 20 tap so that I could bolt the fuel pump to the frame. By the way, I also used dielectric grease on the top bolt because it is holding the ground. The plan is to eventually wire this to a relay and then have a switch under the dash. On to other things... One thing we were missing in the steering column change out when I bought the 56 version - the bracket that holds the column to the dash! So I dug out the old 55 column and disassembled the column. You can see from the photos that the assembly was pretty nasty. It is interesting to note that the 55 column has a two piece cup at the steering wheel mount. 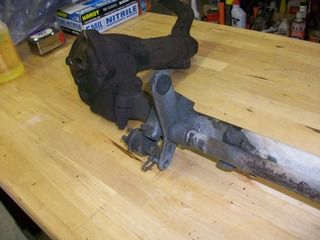
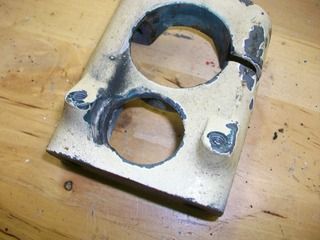
I got the bracket removed with very little fanfare but as you can see the hole for the shift column is oblong. Something rubbed it out. I "think" it was the shift indicator for the Fordomatic? The part has been blasted and I did prime and topcoat a few pieces as well to end the day. Next up - Brake Lines! I already have the front lines off, removed the side line when I took out the old fuel line, and have yet to remove the rear line on the axle housing. I do have all new lines to install though. Again, most of those lines that I removed are original to the car. Scary.
|
By Daniel Jessup - 10 Years Ago
|
I have got so much done in the past two days I am going to need to make two posts... 
Last night I did the same routine on all of the brake lines that I did on the fuel line earlier. Would you believe half of the hard lines were still original? I had replaced the brake hoses about 5 or 6 years ago and they are in great shape so I reused those. Most of the parts were all doing pretty good. I had used silicone brake fluid the last time I added a Master Cylinder and replaced all wheel cylinders, so this is a great time to "purge" out the old fluid and put in DOT 3 since I am going with a power brake setup.
While I was on the rear axle replacing hard lines, I took the time to drain the fuel tank. The fuel had been in there about 3 or 4 years, and although I had added the ethanol treatment and Stabil, I decided to drain it all out. It looked like pee so I took a photo of the Fairlane taking a leak.
![]()
Maybe this would be a good time to talk brakes on a 55/56 Ford. Most guys my age and younger have no idea how to "adjust" their brakes. They are so used to either calipers/pads and self-adjusting drum brakes that all of the other stuff here seems foreign. Most people that wrench on cars can "do a set of brakes" but there are some things peculiar to 55/56 Fords that I did take a few photos of...
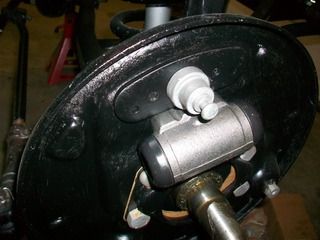
Installing the new wheel cylinders is pretty straight forward, just make sure you know what side you are dealing with and all of that. I will say that up front that small mounting bolt behind the spindle upright is a PAIN to install if you have big fingers. That thing is right in the way.
The first thing some folks need to know is that the anchor pin shown above and then here,
![]()
is an adjustment feature. If you noticed how the hardware looks when you reinstalled it, it is made in such a way as to slide up and down in the backing plate boss. The reason it has that oblong washer is so that it can slide. You will need a 15/16" wrench to loosen/tighten the nut behind it. Although the shop manual is not very clear the idea is that when installing new brakes you lower the pin as much as possible in its bore. I use a small amount of white lithium grease to help this out. Once you need to adjust your brakes later on and move the pin up you will be glad that it can slide.
There is also an eccentric on the primary shoe. Speaking of the primary shoe, it ALWAYS goes towards the front of the vehicle.
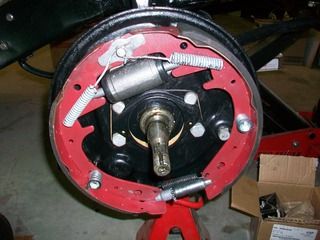
The eccentric is turned by the head of the bolt ON THE BACK SIDE of the backing plate. If you spin it one time you can see where this would tighten the other side of the shoe as the brake linings wear. Of course you have your star adjuster at the bottom also.
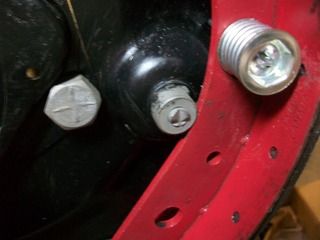 One thing I dislike... the bleed screws are 10 mm and not 3/8" on the last several wheel cylinders I have purchased. What gives? The threads for the mounting and for the brake line are all SAE??? any ideas?
One frustrating thing that happened. I got a new front and rear hardware kit for the car from Jackson's Old Time Auto Parts out in the Midwest. The kits came in two bags. I opened the one marked "FRONT" and proceeded to reinstall the shoes. You can tell from this photo that I am glad I saved my parts. When I was fiddling with those spring hold downs that fly out all over the shop I was wondering why I could not get those boogers to lock down.
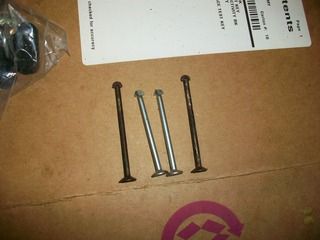
Well..... DUH! They were different sizes (after I started throwing things I decided to check my old parts.) On a whim I got out the other bag that was for the REAR. What do you know? They had the front/rear mixed up. I just sighed and kept on lol.
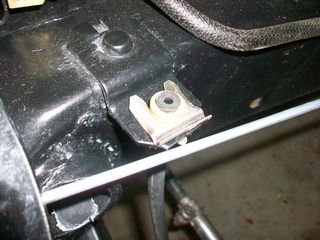
If you look at the photo above, you will see a good reason to save those rubber stoppers that come on your new wheel cylinders. While you are waiting to install other parts or to come back to your project you can pop them in the hole and keep junk out!
One last photo for this post...
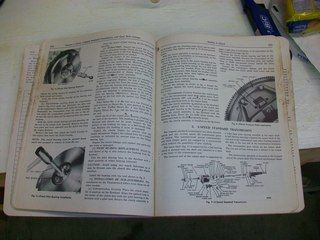
The shop manual is an invaluable tool! I hope you have one.
|
By Daniel Jessup - 10 Years Ago
|
Now comes the part a lot of you have been waiting for... "How in the Devil is he going to get that engine and transmission back into that car?"
Welp, fighting the Devil just happens to be my area of expertise!
Take note... and let the Y block follies resume:
It was late last night, er... early this morning about midnight to be exact when I wrapped up the other work and decided to get prepped to install the engine and transmission in the car together. We all know the drill - it tends to be the question that pops up frequently on the forums. "Do you pull the whole engine and transmission out together?" "How do you take it out with an automatic?" "Do I put them both back in at the same time?"
Well, let's get rolling. The car has had an original Fordomatic ever since I can remember, and I have only ever pulled/installed a Y block in the car with an automatic. Since that original Fordo is CAST IRON and weighs about as much as the car , I have always split the two (engine and transmission). However on the umpteen parts cars I have fooled with I have always pulled the Y block out with the transmission and to be frank it has always been quite messy, a lot of bumping, groaning, metal grinding, etc to get them out. The angle has to be pretty steep.
So what to do? Well at midnight "I ain't thinkin' about that." Let's just get this clutch (remember I lost it ... had to order a set but it was only $100 shipped) "only", bellhousing, and transmission all back together and we'll just throw it back onto the frame tomorrow. No trouble.
Yeh right.
Dufus me at midnight ... I was really not thinking straight. So with the nice Y block on the stand and all of my other parts painted up and what have you, I mounted up the clutch and pressure plate with my pilot tool. No problem. I had installed a new pilot bearing, had nice, clean bolts, and even got the torque wrench out to check my specs. We're good.
The fun ensues when I make the bonehead mistake of trying to install JUST THE BELLHOUSING first and then try to mate the transmission to the bellhousing and the clutch and the crank, etc. NO GO! A real Devil of a time I tell ya!
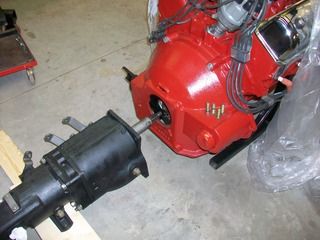
So after I wake up a little bit and tell myself, "You ain't turnin' in until you get this thing all together son," I snap my fingers and remind myself to mate the bellhousing to the transmission and THEN MATE THE BELLHOUSING TO THE BLOCK.
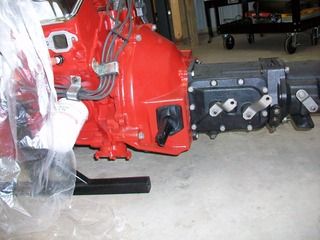
Literally 5 minutes later and the Devil was gone. Nice - turn out the lights and call it a day.
---------------------------- Next morning.... ---------------------------- First things first, WRAP THAT TRANSMISSION'S TAIL! I acquired some bubble wrap and went around the tail shaft a few times as you can see. I tell you - this idea saved my bacon and my firewall paint a few times during the install.
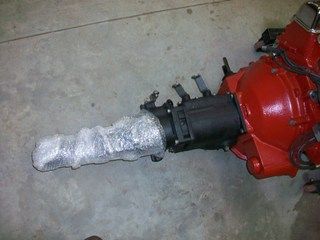
A couple of caveats... 1. I have not installed an engine and trans combo before and 2. Sometimes a blind hog finds an ear of corn
Now back to the blog.
I contemplated going out and doing the tool loaner thing to get a leveler to attach to the engine hoist. Seeing as how the nearest auto parts is literally 20 miles away from me, "I don't think so!" We will get this done if we can get the right angle. Don't ask me how I did it, but the angle created by my attachment points on the block (front and rear) and the weight of the transmission were absolutely perfect. That, coupled with the fact that there was not front end sheet metal on the car made this doable. I am sure this would not work with front end sheet metal on the car... just not possible.
Anyhow, after clearing all concrete of debris (you don't want your shop wheels stubbing over gravels or other tiny substances that will make your engine sway when you stop suddenly!) I got out the shop jack and placed it strategically so that I could make sure the tail shaft cleared the welded crossmember (see photos).
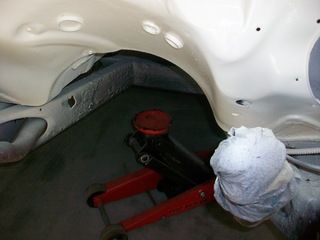
The idea was to keep the attack angle the same until the tail shaft got to the jack and then go back and forth between jack and engine hoist so that the trans cleared and the engine mounts got lined up at the same time. For the record, I did wrap the threads of the engine mount studs with duct tape for a little protection.
How I did this by myself I don't know... I guess it took 30 minutes from start to finish. Constant checks on the tight tolerances ARE a must. I had to get a bungee cord and wrap the exhaust pipe on the drivers side to the sheet metal so that it would be out of the way. I had to remove the levers on the transmission because they were about to hit the firewall tunnel, etc, etc. Follow the photos below and rejoice with me!
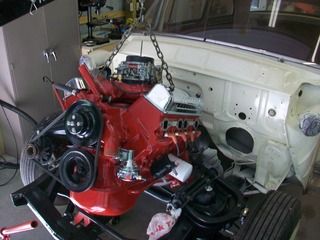
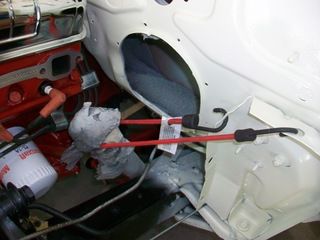
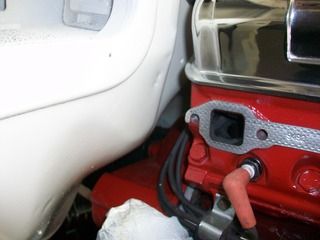
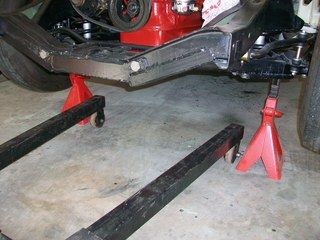
Yep, everything was tight. Sometimes it seemed that clearances were so tight when you were moving the whole works that you couldn't even swipe a credit card!
It all went very well and here she is all fastened down...
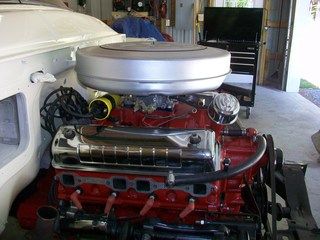
for the record I got excited when I thought, "Man, I made it here and no dings on the firewall and not even a scratch!" Well I have to be honest to you fellas. I have no idea how when it happened but there is a small 1/16" inch of scratch on there. It is hard to see and I think the driver's side head makes it to where no one will ever see it so we are ok.
Gotta get the dash and then the steering column/pedal bracket in next. Any pointers?
|
By Daniel Jessup - 10 Years Ago
|
Last night I got back into the shop and installed the valley pan, exhaust manifolds, and the fuel pump.
First the Valley Pan: I used some acetone to remove the paint around the rim of the block where the gasket goes. After that I used a very small thin bead of black hi-temp silicone gasket maker, aligned the rubber gasket on the block and then prepped my pan to make sure we would mate up well to the block. As you know, sometimes these things can be interesting because of warpage over the years caused from overtightening. Put a thin bead of gasket maker on the pan as well so that both the top and bottom of the gasket have a thin coating of silicone so that you will get an excellent seal.
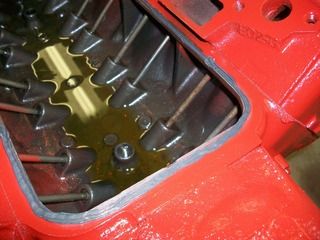
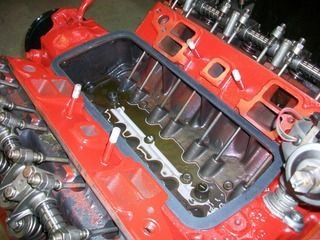
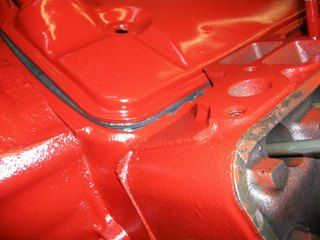
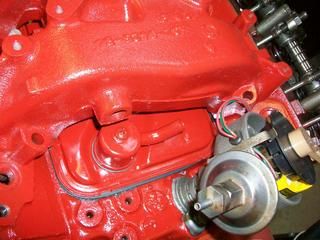 The trick with the valley pan is to get your gasket to cooperate as you slide the pan over the block, between the edges of the intake ports on your heads (if you know Y blocks this can be a pain - especially if you have shaved your heads). I use a very small flatblade screwdriver to position the edges of the rubber gasket before I install the two grommets and bolts. Once the pan and gasket are positioned properly all the way around, I tighten down the bolts alternatively until the goo just begins to squeeze out of the gasket/pan mating area. Stop and let it rest for a while and go on to tackle something else while the silicone sets up. I like to install the teapot PCV mount at this time...
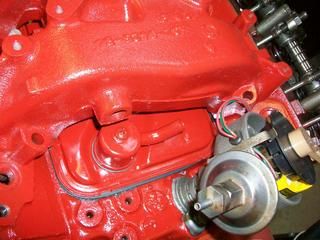 As you can see I have the intake manifold on the heads in the above photos. That was simply to see the placement/orientation of the spout so that I did not come too close to the intake. Obviously these photos show the location being too close, so I loosened up the screw and turned the spout clockwise so that is was between the distributor and the intake. I removed the intake and got back to the valley pan. If you will look at the above photos you can see more photos of the intake resting above the valley pan. This was to check for clearance and to check BOLT LENGTH! For instance, in the photos below certain holes on the head go right into the passage way of the push rods. I suggest you double check the length of your bolts so as not to be in harm's way. Obviously, you will need the valve covers off to verify this.
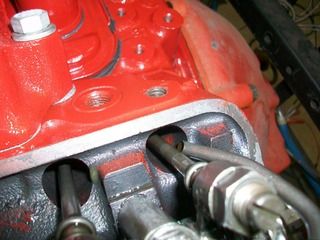 Be sure to check the front and the rear of the manifold. I like to do this check without the gaskets even, knowing that I will have a bit more clearance when the gaskets are placed between the heads and intake. By the time you get done fooling around with all of this, you can probably go ahead and give a final torque on your valley pan. To be honest here, I really don't follow any specification, but I probe around the pan with my small screwdriver to see if the gasket is tight against the block/pan area. That really is the best way to check because you need to make sure your pan is sealed around the perimeter.
More later...
|
By Daniel Jessup - 10 Years Ago
|
I am flying to Florida tomorrow morning and had to get quite a few things ready tonight so I did not have much time. Here is a video link if anyone is interested:http://s249.photobucket.com/user/danaxjessup/media/Initial%20Cold%20Start%20-%20Retarded%20Timing_zpsii8vh96c.mp4.html I will try to put up more tomorrow. I have quite a few good photos and loads of video. I do not have a youtube or vimeo account so I reckon I need that to embed video here. Long story short ... I am very happy. Virtually no oil leaks during the 20 minute or more run, and the only water leak I had was water out the overflow tube when the tstat was taking its time opening up (195 degree). The only drip I had was from the new oil pump cover plate which I did not rebuild/install, I just installed that out of the box. Once I tightened up the offending bolt, she was all sealed up good. In the video, the timing is RETARDED a tick, but I got that sorted out quickly. She came to life quickly on a dead cold start so I was glad for that. Here are some quick photo shots of the action tonight. Only water was used. I will be gone an entire week so I drained the block and the radiator before I came out of the shop...
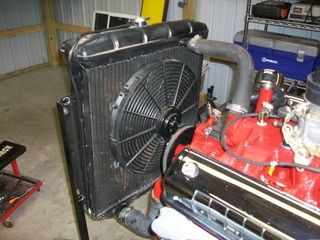
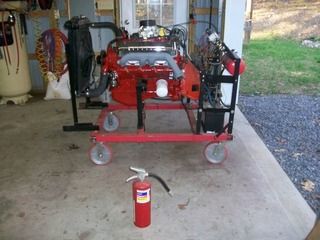
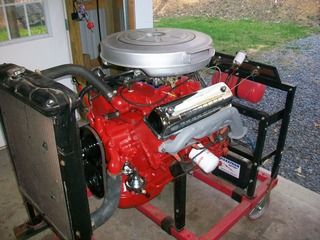
More later
|
By Daniel Jessup - 10 Years Ago
|
The above is a link and a test to see if the video will embed (this is a video with just a slight rev on the enigne). Below is a link to the photobucket website and where another video is located. I have 3 or 4 posted so far. For some reason I am still getting a square with a circle/hash in the upper left hand corner? Can anyone else see the video?
If not here is a link to the photobucket account too. http://vid249.photobucket.com/albums/gg208/danaxjessup/100_3125_zpswv99hevy.mp4
|
By Daniel Jessup - 10 Years Ago
|
<iframe width="420" height="315" src="https://www.youtube.com/embed/YpHDSxaQR1E" frameborder="0" allowfullscreen></iframe> How does this look? Can anyone give me some feedback? I don't think my screen is showing the links correctly.
|
By Daniel Jessup - 10 Years Ago
|
I am working on putting together a Youtube channel for all of you who have requested videos. I am at the airport in Washington Dulles right now and the internet speed is pretty fast. Here is the latest link to my videos... https://www.youtube.com/watch?v=Ecyn583wPEI
I have several on there. If you want to see the rest of them just click on my channel name and it will show you the rest.
|
By Daniel Jessup - 10 Years Ago
|
Tonight I had a really comedic episode with painting the firewall and other interior parts. Last Saturday I had shot a little more TAMCO direct to metal primer surface and wet-sanded (yep, wet sanded) the firewall down to prep for the topcoat. I don't know about you guys but my sinuses sure like the wet sanding route. I know it's messy and you could put what I know about body work in thimble and still need a microscope, but it beats the dust and all. I have dust masks, the 3M charcoal filters, etc, but if I can get away with not having to wear them I am all for it. By the way, the TAMCO primer is the real ticket - it sprays nicely out of the gun and it is easy (soft) to sand.
Welp, after getting everything prepped for paint I decided to shoot some tonight. You guys know the drill, you get home (about 5:30 pm), eat some supper with the wife and kiddos, then remember you have to mow the lawn because there is a house showing tomorrow, do some general yard work outside, etc. Ok, now what? is there enough time to shoot some paint before it gets dark? Well, everything is masked so let's roll the car out and get the parts out on the paint rack, mix some paint and give her a go! I'm using the Eastwood brand (I think it is made by Kirker) single stage Urethane paint. I chose to go with the original tutone so we mixed the 60s Mustang Wimbledon White and away we go. As I pour the paint and make sure I get the right ratio I hear this rumble outside. "No way," I say to myself. "Ain't no rain in the forecast and I just came in from mowing and we are clear and we are good." Yeh right... anyway, as I pour the paint in the cup and start sealing the lid I kid you not... THUNDERSTORM! Aaarrrgghhhhh You have got to be kidding! I looked like Scamper the Squirrel running around grabbing parts, the 55, tripping over the air hose, and what have you. Now what? I have all the paint mixed so what to do? Throw away the paint and wait another day? Nah, too much Scotch-Irish in me for that! I got things set up quickly and shot in the garage after covering a few things. It really was not too bad but suffice to say it is next to impossible to get every speck of dust off the firewall before you shoot the paint! I need a paint booth for sure. Here are some photos. I was surprised by the high gloss look of the paint - we will see what she has when it all cures. The paint shot well, NO RUNS... imagine that! My wife even came out to give her A+ on the thing! I sent a photo to my FIL and we will see what he says when he takes a look at it. 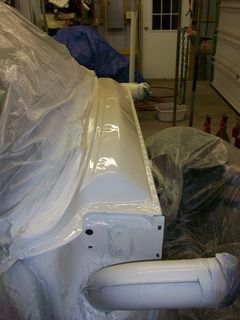
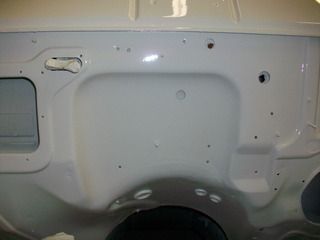
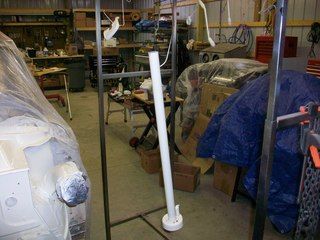
|
By Daniel Jessup - 10 Years Ago
|
My lens protector on my TP Tools Skat Blast Cabinet was getting kind of fuzzy. I have to replace it about twice a year. I have owned the cabinet for about 8 years, and it works very well. I have only had to replace the nozzle 3 times, and I would imagine I use this cabinet about 4-5 hours a week on average. I have had to replace/refill media also on 3 different occasions. I have tried all kinds of brands from TP's glass bead media (the best I have used in my opinion), to Harbor Freight, to Tractor Supply Company. I have only ever used glass beads in the cabinet. I would like to find a way to put another light in the cabinet because of the "shadow" effect with just one light bulb in there. Sometimes it is difficult to see what you are doing in there.Whenever I replace the lens protector, I always get off all of the old adhesive. Goo Gone works the best for that job, and the new protector sheet always stick to the lens very well. It takes more work, but I never have my lens protector falling down on my gloves and I have never had to replace my lens!
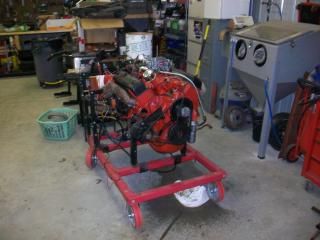 The cabinet is the grey unit along the wall to the right of the engine run stand.
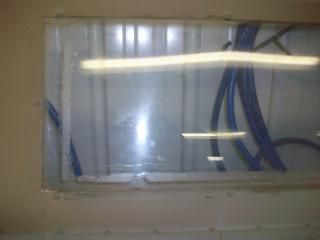
|
By Daniel Jessup - 10 Years Ago
|
Wow, it has been a long time since my last post... I have been busy getting my house ready to sell, making a transition to Ohio, and all that comes with a move. Half of my shop has already been cleared out and many things put into storage or sold. By the way, the most recent contract did fall through. The buyer wanted me to change a window's location, complained about code, went after documentation/permits on my shop, etc, etc, etc. I think he just had a simple case of buyer's remorse.
At any rate, this has left me some time in the shop and the last few nights I have been a little busy. I reinstalled the tie rods, idler arm, and drag link after a serious cleaning and installation of new seals and grease.
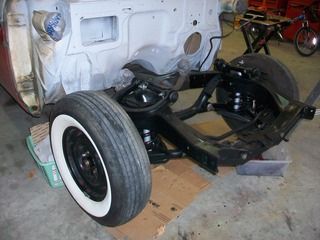
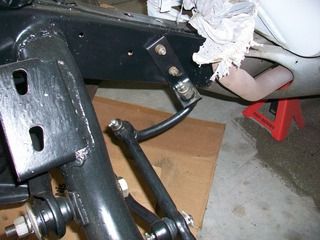 The front brake drums and hubs were cleaned up and painted, and the bearings and seals cleaned, greased up well, and reinstalled. Nothing too exciting to show concerning installation, I guess this is all pretty boring material. I did not put in the steering gear just yet because I want to finish up that firewall. Hopefully the rain will stop coming, but it is April after all.
I did get in a brand new fuel line (tank to fuel pump) from Tee Bird Products. The shipping was outrageous - I will leave it at that. I also got a set of bushings in that shipment so that I can rebuild the shifter arms on the column. While I was at it, I ordered a set of brake lines (specific lengths all ready to go) from Jacksons' Auto Parts - the box showed up today, CRUSHED, and all of the lines in the box were bent at a 35 degree angle. They were all supposed to arrive straight. Now what? I guess I will contact them tomorrow and see what we can do. I guess I can bend them back but you know once a line is bent, it's bent.
While the front end has continued to receive treatment, I have also been attacking the 292. I degreased it, removed quite a few bolt on's down to make the engine a "long block" so I could clean it up easier. The timing cover and water pump I just left on the block. I did put on another oil pan that was in much better shape, and I added a NEW gerotor oil pump. There are not many miles on the engine (just several hundred) so cleanup was not too bad and the parts are all in great shape.
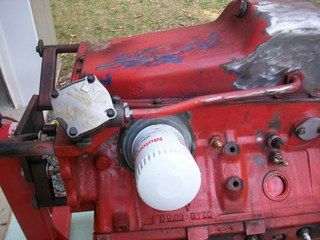
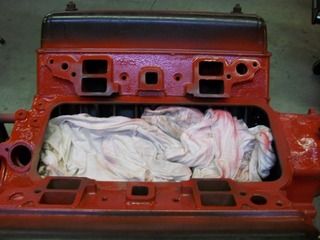
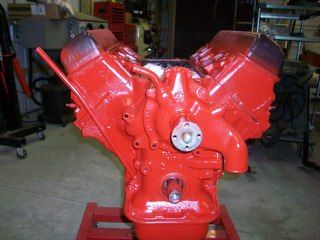 The whole "wire wheel" episode was long, messy, and just downright tedious, but that metal was clean by jove! I am not going to reuse the pitted valve covers, so I Ieft them on. I have rubber valve cover gaskets and chrome valve covers to install anyway. When I paint an engine like this, I like to put clean rags in the lifter valley just to keep out the crap. The engine paint is a simple Duplicolor Engine Red. I don't think it is 55/56 Ford correct but it looks good and it was available. The car is not a show car so what's the difference. My father-in-law came over tonight and likes the look of it so on we go.
I have some of the bracketry and other parts on my paint rack so hopefully I can get to install those soon. I also have two good sets of exhaust manifolds that I just brought out of the blast cabinet, cleaned up, and then coated with the Eastwood Hi-temp coating. I have two sets because one is original to the 55 and the other is a 57 set. I will most probably use the 57 set depending on what I do with the power brakes situation. I have not decided what to do about that yet, but will most probably get an aftermarket set up instead of the original master cylinder and Ford's way of doing it in 1955. We want to put a dual master cylinder on it anyway.
Once I get the engine running again I will have to post a video. Hopefully I can figure out how to do that.
|
By Daniel Jessup - 10 Years Ago
|
MoonShadow (4/15/2015)
Do you have a part number for the sway bar bushing sets? Chuck
Let me check on that... they are from energy suspension. The sway bar I put in is a 7/8" from a 56 Ranchwagon. The part number from energy suspension is: 9.5158G (it comes as a kit)
|
By Daniel Jessup - 10 Years Ago
|
Ok fellas... back at it again for the last two nights, cleaning things up, installing new gaskets and even had the chance to put the 292 on the run stand tonight before I got ready to turn in. First of all, I thought it good to cover something that gets asked quite a bit by newbies... "How do you prime the oil pump?" I don't know if my answer is the best but I will show you what I do when I get a Y block ready to go and then after that I will take you through what I do to get the distributor ready for initial start up. Here we go: I put an NOS oil pump (gerotor type, not the "spur gear" pump) on this Y block when I put a new gasket on the oil pan also.
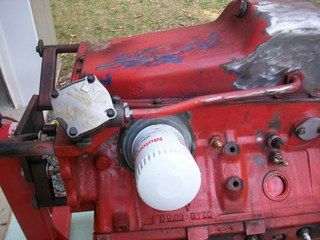 Look to the left in the photo above to see what I am talking about here. The gerotor has a smooth cover, the spur gear has a sizeable "bump out" for the gear.
When you put one in, the best advice is to submerge the entire pump and prime the pump itself before installation. Well... I'm pretty lazy and did not want to have to clean it up to paint it, etc. So I did put a little oil in the pump inlet just to make sure it was not dry at all. I then installed a new gasket after I cleaned the block surface really well. It is not recommended that you put any silicone or sealer on the gasket for the oil pump. However, I must say that I always use high tack gasket compound (the red stuff) on the gasket at the oil pump to get it to seal nicely. Careful - a little goes a long way here! After the pump was installed, I cleaned it up with acetone before painting. Another word on the oil pump and the oil pan tube that feeds the pump. There is a very delicate tube seal that goes on your inlet tube as it mates to the pump inlet. Be careful to get this situated correctly and do not overtighten or crush the seal. If you have a leak here after priming or after initial startup it will be a PAIN because you will either have to remove the oil pump or oil pan and then reaffix the seal. You really don't want to have to do either, trust me.
Back to priming the pump. Make sure that you installed the oil pump drive rod (get a new one when you put in a new pump - cheap insurance!) correctly in the bore. The catch washer is used to keep the shaft from coming out of the pump when you pull the distributor, so the washer needs to go on the shaft BEFORE you place it up inside the bore of the block. Please don't leave it out - you will just be swearing like a sailor the next time you pull your distributor out and find that the shaft came right on out too... OUCH. That shaft is pretty thin but it is a hex. You can use a 1/4" socket to turn the shaft so that you can prime the pump. Get yourself a long 1/4" drive extension or two, and then a THIN-WALLED socket like the one shown. TAPE THEM TOGETHER so that you don't lose anything while you are messing around in there.
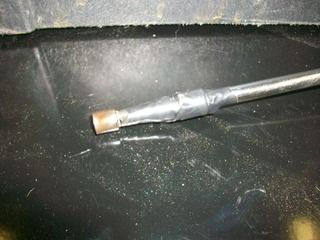
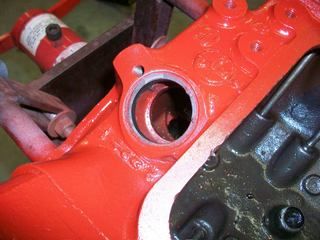 You can see the distributor boss pictured above. That is what we are shooting for here. If you look down in that hole you can see the top of the oil pump drive rod. Take your drill, set it to REVERSE (remember that counterclockwise is the way the distributor and that hex shaft will rotate when the engine is running). Now take your 1/4" extension setup and place it on the shaft... HOLD IT! Did you fill the block with 4 or 5 quarts of oil? Thought so. You did - but I almost forgot. By the way, another thing you should do... ahem, is uh, to walk around your block and make sure you are BUTTONED UP! (see Y block follies post for explanation here lol) You don't need to go at super fast rate of speed, just touch it off and let it rotate a little bit. You can actually do this with a speed handle for a socket but this certainly takes the sweat out of it. While you are spinning the drill it will be about 10-15 seconds or so and you will feel a load... yep, we struck oil. "Drill baby drill" Keep going and watching your rocker arms to make sure you are getting oil up there. If you have a new build, it is going to take some time. The rockers are the furthest point away from the pump that the oil has to travel, so every other orifice and what have you will fill up first. If you have an early cam that is "cross-drilled" then rotate your cam so that you can mate up the feed holes.
Now on setting that distributor. With your valve cover off the passenger side head, take a look at the # 1 cylinder and the corresponding valves. You want to get TDC at the compression stroke so that you can give that ignition initial time. Go back to your crank dampener/timing pointer and bring up the TDC mark just as the intake valve has closed (exhaust will be closed as well... double check this by checking valve lash on both rocker arms for #1). Most guys like to set their initial time to exact TDC on the timing pointer. I guess this is good practice, but since Y blocks like a lot of advance I usually bring the timing pointer to 4 degrees or so and then get ready to install the distributor. You will note my timing mark on the crank dampener. I have removed the black paint where the timing marks are located and I have sprayed it with Clear Engine Paint to highlight the difference from the rest of the dampener.
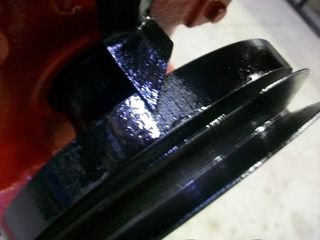 Next, I take the distributor and mark the location of #1 Cylinder/Plug Wire by fitting the cap to the distributor and making a sharpie line right underneath the center of where #1 is located.
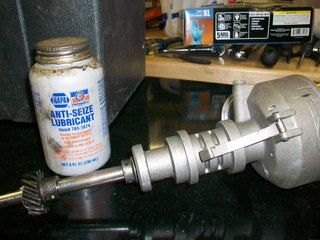 Something else I like to do is get some anti-seize on both lips of the distributor boss on the block and a little on the distributor itself where it will mate to the block. How many times have you tried to pull a seized Y block distributor? I don't know why particularly, but the Y block is NOTORIOUS for seized distributors. In my lifetime of probably dealing with 15 different Y blocks I have never owned, seen, or worked on one that had the top end oiling problems. But about half of the ones I have dealt with had a seized distributor. You may also note the ACCEL pointless ignition. While everyone and their grandmother go the Pertronix route I have used the ACCEL kit with 100% success and no ignition failures over the past 10 years or so. (lol I say that now, wait until I crank this thing up or take the father-in-law out for the initial ride after all the work is done! Seriously though, I do like the kit and with an ACCEL super coil there is no resistor needed. You can leave the key on with no problems, etc. That's all for tonight - I'm beat. I did get more done in the shop but until next time, here is the engine finally back on the run stand...
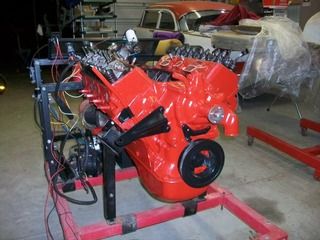 You guys out here late at night can take over for me...
|
By Daniel Jessup - 10 Years Ago
|
43mike (4/15/2015)
You're doing a great job on this, what with the comments, pictures, and advice. I'm getting ready to do the same with my '55 Townsedan, so I'm watching this with great interest. What your doing is almost exactly what I have planned for mine, to the letter so far. Keep up the good work. Mike, Lanett, Alabama Mike, I appreciate your comments. I know I always enjoy reading the posts of others and have learned quite a bit (I still am by the way). Do you have any photos you can post about your 55?
|
By Daniel Jessup - 10 Years Ago
|
Just to follow up from what I posted last night, here are some photos of the Exhaust Manifolds. Now that I look at the casting numbers, I know that the EDB is not a 1955 number. I believe they are to be ECH if they are original to the car right? anyone know? I am not quite sure why the different numbers in the earlier years - maybe you guys can chime in here. I bought a set of the B9's, blasted them too, and have now coated both sets twice and are letting them dry out. This stuff works pretty good in my opinion.
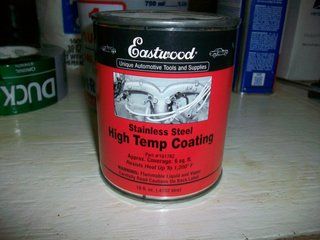
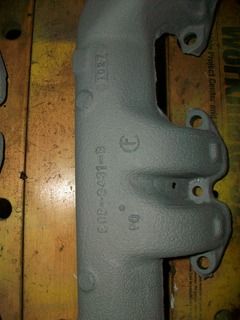
I also cleaned up a couple of nice chrome valve covers and used some contact cement to set RUBBER valve cover gaskets to them. The gaskets work very well when you need to remove your valve covers a few times over their "life" when you are setting valve lash, etc. I know some guys will use cork and seal the cork to the valve cover, then grease the end of the gasket that mates to the head - that works too. I have done that with intake manifold gaskets before.
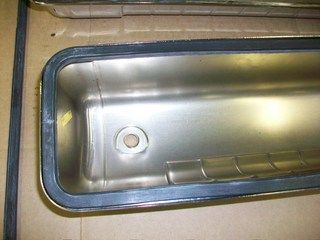 I need to find some chrome or stainless acorn nuts for the valve covers - they would look better with those. I do have new decals to put on the valve covers - I like the 1957 "Ford Interceptor" decals - kind of my favorite FoMoCo look. I did get the Valley Pan cleaned up last night, and I have a rubber gasket for that too. As you are aware sometimes these valley pans you find can be bent up into a banana shape by the last gorilla who wrenched it down. Since there are only two bolts that hold it down to the block, they are prone to leak also so make sure there is a good seal all the way around. If you use silicone or some kind of a gasket maker, go sparingly with it.
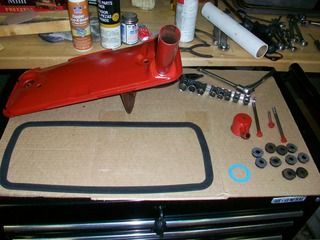 Hopefully soon I can start installing the other bolt-on parts and get this thing fired up again, check for leaks, make sure the plumbing is good, time the engine and get it ready to reinstall in the car.
|
By Daniel Jessup - 10 Years Ago
|
Sometimes you have moments when you stand back and admire your work. Other times you stand back and look and you say to yourself... "There's a reason I don't make a livin' doing this kind of thing."  If you are a very observant individual and know your 55/56 Fords very well, you noticed that I left out the two "collars" that surround the front bushing on the lower control arm. I really do not know what overall purpose they serve, but I reckon since Ford installed them originally I should probably put them back. So... off with the arms and on with the collars and reinstall the bolts and nuts! 
Here is a photo of what I am talking about...
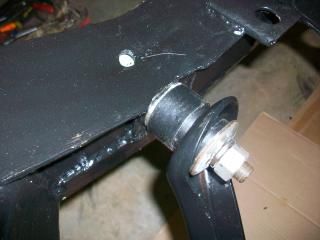
I did get the upper and lower ball joints installed, but I did not have the bumpers for the upper joints. The irony is that the kit I received had 3 bolts, nuts, and washers per upper ball joint, and then 2 bolts, nuts, and washers for the lower ball joints. There are 3 holes for each joint. I have the lower bumpers.... guess I need to order the upper bumpers or is there a reason why they are no longer needed?
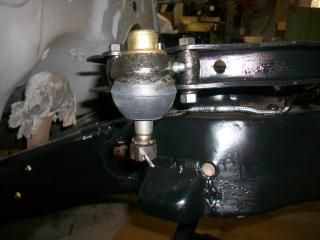
I have a set of the Aerostar coil springs and new rubber to insulate them in the frame all ready to go. They are waiting their turn. I did get the spindles cleaned today and gave them their first coat of paint.
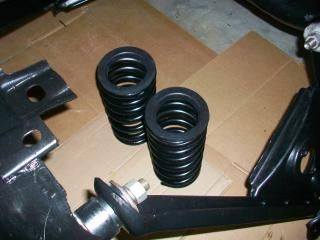
|
By Daniel Jessup - 10 Years Ago
|
I got off my rear end last night and reinstalled both spindles and the new coil springs. My 11 year old son came in the garage and said, "Dad, it looks like a new car!" J And so it is looking pretty good. To install the coil spring and spindle, I basically set up a floor jack with some cardboard so as not scratch the new paint on the lower arm. The coil spring rubber goes on the top of the spring where the coil is flat. The other side of course matches an indentation in the lower control arm where the end (and bottom coil of the spring) rests. I was sure to get it into the groove as the lower control arm made its way up. But before I started jacking anything, I took a good look at the ball joints and decided to take a small punch into the cotter pin hole and orient the stud so that when the spindle was installed I would not have a problem inserting/removing the cotter pin. There is very little room behind that upright on the spindle.
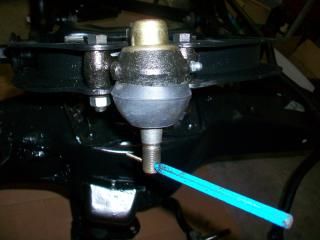
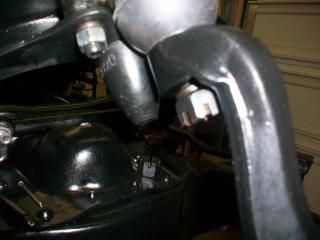
You can tell that I cut down the lower bump stop about 1" and I did decide to install the bumper for the upper control arm. For the record, I cut the lower bumper before installing the spindle and spring. A sawzall made quick work of the problem. With the lower ride height that I am expecting from the Aerostar coils the car is going to need the extra room. Thanks to fellas on this site for that recommendation.
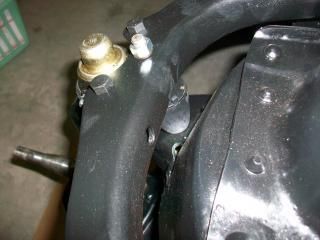
After orienting the studs, I actually install the spindle to the upper arm and get the nut as tight as I can. Then, I pump the jack and bring the lower control arm up to seat the coil in its pocket. On its way up the lower hole in the spindle is filled by the stud in the lower ball joint and with just a few more pumps the stud is all the way through. The top nut is 7/8" and the lower nut is 15/16" socket size. When the stud is all the way through I do like to rap the upper ball joint with a hammer/wood combination to get it to "seat" and take out play (if there is any). That may not be the most ASE certified way to do it, but it gets the job done. I will most probably check those nuts again after the engine is reinstalled and before the car goes to the alignment shop. The large bolts that connect both the upper and lower arms to the frame will be left just tight enough to hold until the full weight of the engine and front end is put back on the suspension and the car is sitting at ride height. Then we will tighten all four down before it moves out to the alignment shop.
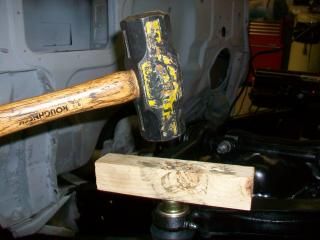
I snapped a couple of photos of the differences in front sway bar bushings as well. The old bushing and bracket that was used for the wagon bar was original and was "wallowed" out, dry rotted, and just plain useless as you can see. The new bushings from Energy Suspension (again, due to a lead by Jeff on this site) are made of polyurethane and are also able to be greased. Once my tube of Super Lube grease arrives in the mail thank you Charlie for that tip also) I will reinstall the front sway bar, but again only just to keep it on snug until the full weight of the car is down. I did see a big difference between the old bolts and bushings that held the bar to the control arm when I compared the old ones from the wagon bar to the new ones I received. Hopefully it is just a difference in the size/compacting of the rubber grommets.
|
By Daniel Jessup - 10 Years Ago
|
Today I had some time to install the sway bar with the new Energy Suspension brand polyurethane bushings and the stabilizer hardware kit to attach the sway bar to the lower control arm. I had snapped more photos but my camera went haywire when I got back inside the house and my SD card was EMPTY! go figure. The nice things about these ES bushings are: polyurethane, the 7/8" size was in stock, they come with new brackets, and the bushings are greasable! I used a synthetic grease from Super Lube. I also like the small plastic caps that cover your Zerk fittings but I don't know how long they will last. No modification needed for the brackets - they fit the frame perfectly. Basically, I laid the sway bar in position and let it rest on the lower control arms. I then slipped a bushing on each end (I greased them inside first too) and slid them into position on the bar so that they would go right up the frame. Next, I put the brackets on loosely and checked the fitment. Once I was satisfied with it I pivoted the bar in the bushings back and forth to get the grease worked into the bushings and bar real good. Then I installed the hardware kits on each lower control arm. Notice that the hardware kits were not cinched down too tightly. I think it will be best to tighten those down once the weight of the car is back on the front end like it should be. I did cinch down the brackets to the frame however, and after doing so I greased them with synthetic lube. The sway bar is a station wagon sway bar with a 7/8" diameter. I think I got it from a 56 Ford Ranchwagon. The hardware kit and the bolts that attach the brackets to the frame have a 9/16" head by the way.
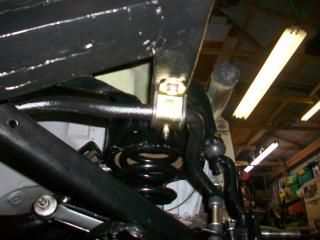
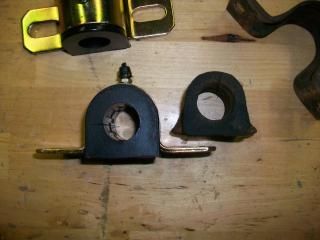 The photo above is the difference of the old worn out bushings in the station wagon sway bar and what the new ones look like. Think it will help?  On to the Backing Plates and the Spindle Arms. They cleaned up nicely. I only put one coat of Rustoleum on the inside of the backing plate. Not too sure how the paint will hold up in there anyway but thought it would be good to at least try to control some of the rust. I use silicone brake fluid anyway so we should be ok. I think it worth mentioning here again about the location of your bolts that hold the castle nut and cotter pin. I like to make sure I have mine oriented all the same way and in a location that I can get to just in case I have to start fishing those cotter pins out again anytime soon. I face them up so I can find things easily and see how to twist/turn the ears made by bending the cotter pin so as to get the cotter pin back out more easily next time. I also used a little anti-seize on the threads. You will need a 3/4" and a 9/16" wrench to tighten them down, but only one each... the grease guard plate acts as a head stop on the front side.
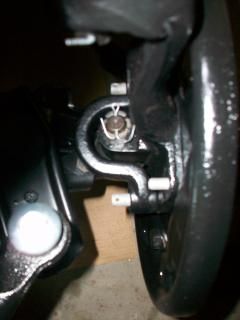
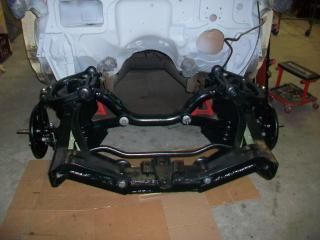
A quick word about hardware and some photos to explain. I like using as much of the old hardware as I can, provided it is in good condition. Two reasons... odd ball sizes as far as lengths can be a pain to locate at the local hardware store and it saves money in the long run. A while back I started using a small Ultrasonic Cleaner to degrease hardware and parts. You would not believe how well it does with carburetors!!! I stopped using solvent and Berryman's a long time ago. Basically a bottle or two of the $ store "Awesome" brand cleaner and some water in the tank. Heat it up with the touch of button, set the unit to run for several minutes and you are good to go. Take out the parts, rinse, dry, and then over to the blast cabinet. Blast cabinet you say? what about all those washers and nuts that fall through the cracks? Well, here is the answer - a cricket tube from Wal-Mart. It is the perfect size to hold in your hand. You can rotate the tube while you blast and you can see everything in it. There is no way for any part to escape. Shake the tube when done and all the media falls out and you are left with clean hardware. I like it and it has served me well. Bolts that need to be chucked because of wear or corrosion show up pretty easily as you can see.
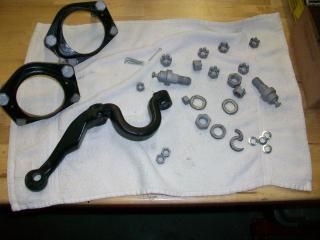
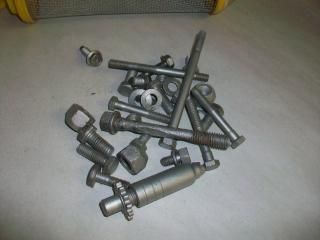
|
By Daniel Jessup - 10 Years Ago
|
steinauge (1/15/2015)
I cant speak for anyone else but I am thoroughly enjoying this thread! Thank you for going to the trouble of putting it up.
If my camera would do a better job it would be a lot easier! Thanks for the motivation on the blog here
|
By Daniel Jessup - 10 Years Ago
|
thanks Ian. I believe I have this shock thing figured out so we should be ok in that department too.
|
By Daniel Jessup - 10 Years Ago
|
Been down and out the past few days with a serious sinus infection. I started antibiotics yesterday and only just a few hours ago have I felt any better. At any rate, my KG4503 KYB front shocks finally arrived so I was a little motivated to move out to the 18 degree garage and install them up front. I must say, those things are gas charged and tight! It took me quite a bit to force one in on itself to bench test its "action" The shocks came with new washers, nuts, and rubber grommets of course, but they also had instructions written in about 57 different languages with plenty of "well duh!" diagrams so you get the mounting correct. What in the world could be the issue with mounting shocks you ask? The only thing I see that someone could goof up would maybe be the grommet positioning? Either side of the grommet is different as you can see in the photos. The larger lip goes towards the washer and the smaller diameter lip goes toward the bracket or the shock tower mount on the frame. I assume most people know this but I thought I would point it out. I had already cleaned, blasted, and painted the original brackets even though I thought I had a lead on shocks that had its mounting tabs on the lower end that would work for the lower control arm. So, I simply pulled them back out of storage and mounted the brackets on the bench, making sure I did not get the "grommet bulge" past the washers. As you can see in the photos the shocks came with two nuts per stud, so I assume that one is to lock the other down. To be honest, most of the stud shocks I have ever seen only had one nut, I am not sure why this came with two unless there is something for a different application or what have you. I obviously decided to use the extra nut as a lock nut on each stud. I must admit that I cheated when installing the shocks. I used my floor jack to raise the bracket into position after I had attached the upper stud to the shock mount on the frame.
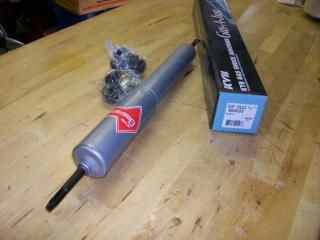
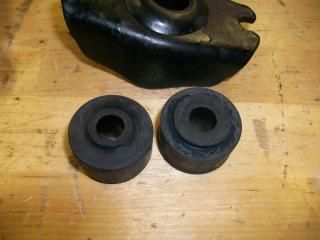
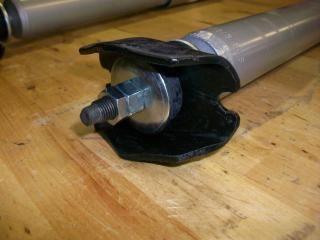
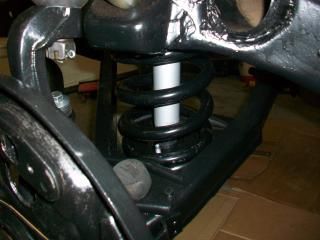
I also decided to replace the lens in my bead blast cabinet from TP tools. I will post photos on that later. Some of you have asked about the cabinet before so I think it a good time to show some of the maintenance work that needs to be done from time to time.
|
By Daniel Jessup - 11 Years Ago
|
I had a little time to hit the shop again today and I was able to get the upper control arms all back together and ready for paint.
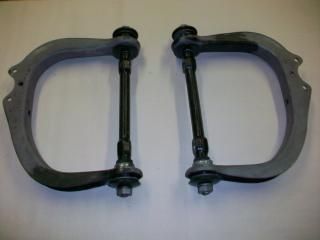
I blasted them in the cabinet and then coated them with the solution you see pictured. It is an off the shelf product from Lowe's. It took some time to dry, but that could be because of the lower temperatures at this time of this year.
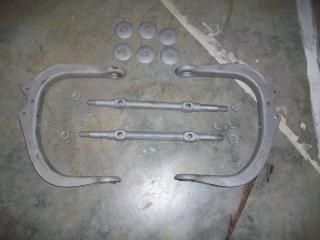 After that I fitted the rear bushings to both control arms. The rear bushing is the one with the "step" that will stop you from driving it all the way to the lip. I advise you to be careful if you ever replace your bushings... that step on the bushings I had did not look too pronounced. It looked more like a "line" drawn around the circumference of the bushing.
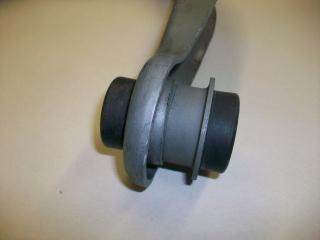
Since I don't have a press, I decided to drive the bushings home with some pipe that fit just over the rubber, but met the lip of the bushing head - on. 1 and 1/2 inch pipe is what I used. It worked very well as you can see and I simply placed the arm on the vise and hammered each bushing home. I did do some preliminary painting to a few parts, but that was just so when I painted after they were assembled I could already have paint in those hard to reach areas. Also, beating and banging with a hammer on anything painted is going to mar it up big time.
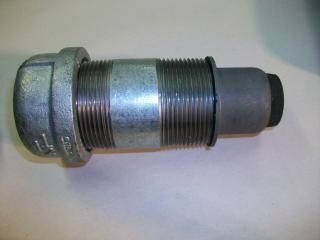
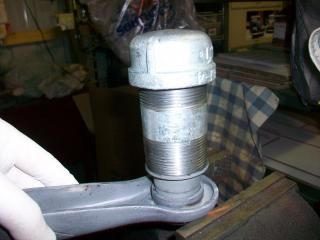 I used some anti-seize on the shafts and the threads, but I was able to reuse all of the hardware. You can probably see that one of the old lock washers were broken - that was replaced from my hardware stash. Also, of the 3 washers that pertain to each control arm, one of them is larger than the other two. The larger one goes on the inside of the control arm at the rear after you slide the washer on the shaft. The other two washers go on the outside of the control arm on either side of course. One note here... the control arm is "springy" - in other words you can't get the second bushing on by simply "tightening down" the busing on the shaft using the threaded stud because the arm will bend with it. Both bushings have to be either pressed on or hammered on like I did.
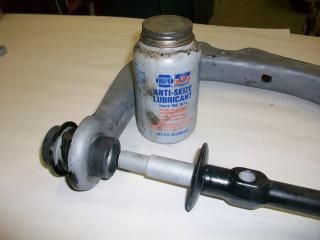
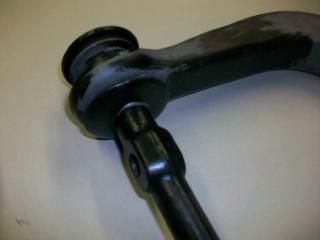 I plan to paint them pretty soon, and I have started on the lower control arms with clean up. My sandblaster went out on me the other day because of the "el-cheapo" dead man valve so I am having to put those in the glassbead cabinet. The lower control arms are in a whole lot worse cosmetic shape than the upper control arms were. The passenger side arm is clean, blasted, and was just coated with the Prep Primer tonight. On we go.
|
By Daniel Jessup - 11 Years Ago
|
For all of the success I have had, I did experience a "DUH!" moment last night when I was installing the bushings in the lower control arms. Note the photos... Maybe it was because it was thanksgiving week and I was distracted with deer hunting, smoking a turkey, having folks in, baking all kinds of food with the wife, Christmas decorations, blah, blah, blah. I don't know. The 55 Ford shop manual is a tick misleading when you look a the diagram. It shows the lower control arm bushing coming in from the front side, but if you look at it closely in the manual you can see a faint, dashed line, showing insertion from the BACK! Yep, I didn't catch all of this until I had fully seated the first bushing!!! When you do these, remember that both bushings, front and rear, are installed from the INSIDE of the arm facing out.... the large cupped washer should compress up against the rubber that is on the lip side of the bushing.
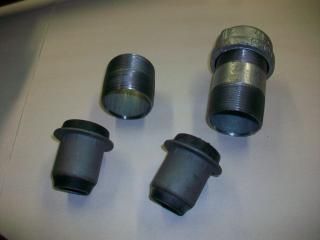
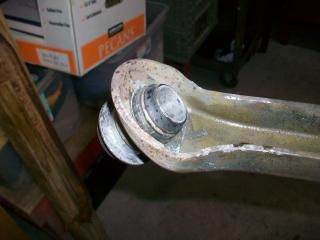
How I ended up getting that bushing back out of there without damaging it, I do not know. Patience and Henry Ford's spirit I guess...
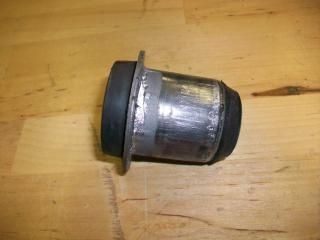 Here are a couple of photos of the CORRECT installation
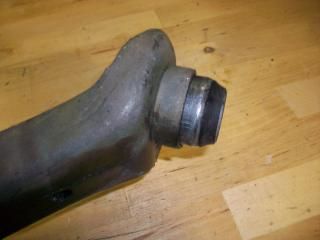 The other bushings and the other control arm all went well so we are about ready for paint. I did have to weld a nut onto the other control arm, but that was really a piece of cake. I will post photos later. I am about ready to clean up the spindles and start installing some of these items back on the frame. It will feel good to do that soon. Pilgrim's Progress lol...
|
By Daniel Jessup - 11 Years Ago
|
Basically one of the nuts had dislodged itself from the shock mounting location on the lower control arm. I think this happened when I was like 18 or something. Anyhow, I did get the nut to tighten down by sticking a screwdriver between the coils and hold it down while I put the bolt through. That was a long time ago. When I disassembled the front end, I knew I wanted to make sure those nuts were secure and that I needed to weld the loose one back to the control arm. Mission accomplished, and I decided to tack the other one in as well just for good measure.
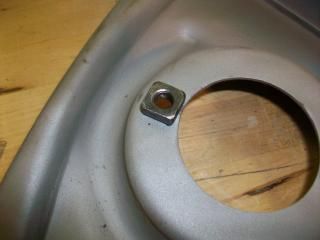
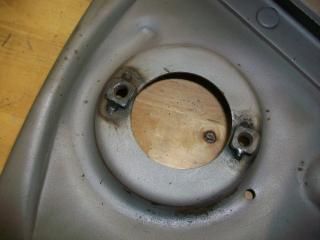
|
By Daniel Jessup - 11 Years Ago
|
Thank you Mark -- no wonder I was confused. I did kick myself though because I did take photos of the disassembly and should have seen it.
|
By Daniel Jessup - 10 Years Ago
|
Well the Christmas and New Year's Holiday was good - we had an excellent time with our kids, and a lot of in laws and out laws showed up. I had planned to spend some time in the shop since I would have a few more days off for Christmas but my plans were made in vain. I looked at my calendar and most recent post... it has been well over a month since I have accomplished anything out there. Anyhow, I decided to fire up the diesel "turbo" heater in the garage (you know the kind - it sounds like a jet aircraft taking off and when you run cheap fuel in it you gag over the fumes ). I have owned the one I have for 5 years. I believe it is 210K BTU and all if you run the higher pressure. Over the past 5 years - no problems... until tonight. I hit the switch and the spark plug makes it usual noise, then the fan and fuel pump engage, but no FIRE... when I look inside the cavity--- there is raw fuel on the bottom and it eventually runs out and down the side of the tank. What gives? I thought "Well, that's probably the fuel being sprayed that would not ignite so where else could it go?" I look at the display panel on the side of the unit and wouldn't you know it, the panel reads "E1". I get out the trusty manual and it looks like it could be a dirty photocell that needs to be cleaned off. No biggie. I take off the top cover of the tube and have a "look see". I was shocked at the condition of the two fuel hoses - no wonder the thing was leaking fuel. I took pictures of the hoses and posted them below. Dry rot central. I have never seen rubber hoses go so bad in only 5 years and with very limited use at that. I guess I should have inspected under the cover each year before firing it up just to check on things, but there never has been a problem with this thing and I keep it very clean. Word to the wise if you own one of these units - the manufacturer uses CHEAP hoses and get this... NO CLAMPS!!! on a fuel pump that runs 8 psi!!!. I looked through my bins and found two, new, fuel injection, automotive grade hoses to install. Much more rigid and probably overkill. Suffice to say, the unit fired right up when I put it all back together and we were ready for action.
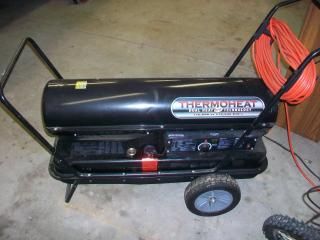
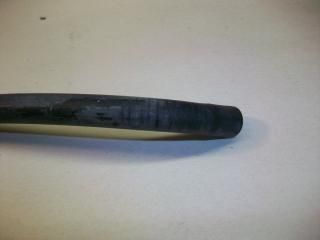
After the garage warmed up a bit, I decided to drill the drain holes for the front cross member and take a look at the Internal Frame Coating product from Eastwood (is it a 14 oz load of crap or is it the real deal? - I have no idea). Anyway, the idea is that the long narrow hose attaches to the aerosol can and using the 3 hole tip on the end, the user can slide the hose into the frame and coat the interior walls of the frame as he pulls the hose back out while he is spraying. Let me tell you that if you have any notion to use this kind of product, be prepared for a mess! I believe it worked well. As you can see from the photos, I did enough heavy coats to have the product coming out the drain holes of the cross member. It was messy enough that I need to go back and repaint the satin black on parts of the frame, but that's no bid deal. This cross member is going to out last my lifetime that is for sure! I already have the upper and lower control arms painted so we are getting close to beginning reassembly. I need to get the car rolling again so that I can move it in and out of the shop for body work.
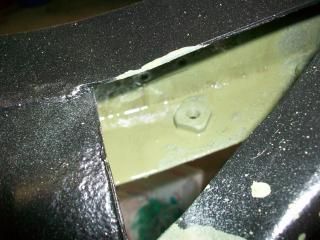
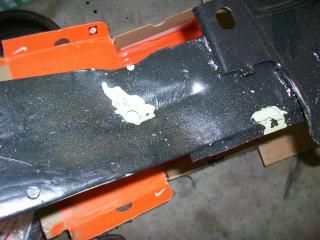
|
By Daniel Jessup - 10 Years Ago
|
I like progress! Last night I cleaned up the mounting bolts and did some work to the front end by installing the upper and lower control arms. When you get to a stage like this, it makes you very happy that you took notes and bagged and tagged your hardware. For instance, I decided to bag and label those shims that are used to align the wheels on the upper control arms. I also did that for the lower control arms where the large shim washers are used for the front of the control arm where it attaches to the cross member (more on that later though).
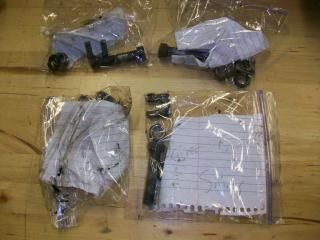
The hardware was blasted where needed and threads cleaned with a wire wheel. I also used copious amounts of bearing grease on the large shoulder bolts and a good does of anti-seize on the mounting bolts for the upper control arms. I started with the driver's side lower control arm first. After laying down some fresh cardboard to keep my arms from getting scratched by the floor, I put the driver's side into position. Immediately I noticed that it was not a tight fit, and that if I installed the arm there would be play back and forth as the arm's bushings would slide on the shoulder bolts. Thinking I would rather have some "springiness" in there and make it tight rather than letting it slide around, I chose the shim(s) I needed to take out play and even had to use a pry bar to wedge it back in (not a lot of prying but enough to bring 1/8" in to meet up the holes). So I slid both bolts into the holes but did not put them all the way through. I then got the holes of the arms to line up with the holes on the cross members. After that, the bolts went through with just a little tap and we were set to reinstall the cup washer, lock washer, and nut. A word of advice on the shim--- grease the side that goes towards the crossmember. It will stay put for you as you align the arms since they are very snug. I did take a photo of the bolt being placed in the front crossmember and where the shim washer goes. Note that the straight edge goes towards to the top to fit up under the lip of the cross member itself. It would be a good idea to check the fitment of all of your bolts and hardware before starting the installation process anyway. The shoulder bolts have a whopping 1 1/8" head and the nuts are 15/16". I decided to NOT tighten these arms to spec on their torque, just leaving them a little loose until I install the spindle and ball joints. I am not so sure whether or not anything will bind up, but I thought it wise to wait. Maybe someone out there can tell me different on that.
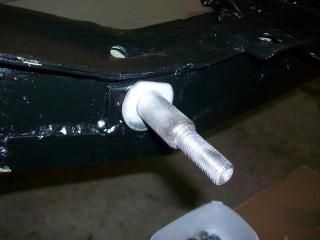
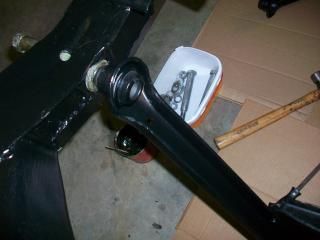
The upper control arms attach to the frame mounts with out much fanfare...especially if you kept your shims labeled. I am not sure how much this will help with the front end alignment because of new parts, etc. But I believe it will help things out until I get the car to the shop and they are able to put it on the alignment rack. Note the orientation of the upper control arm also - the mount for the upper ball joint goes towards the REAR of the car. You need a 3/4" socket and/or wrench to meet the head and nut size. I put each control arm up into position and then slide the bolts through. I attached the lock washers and nuts, leaving things loose, and then I placed the shims in their correct locations. After that, the arms were torqued to spec and allowed to rest.
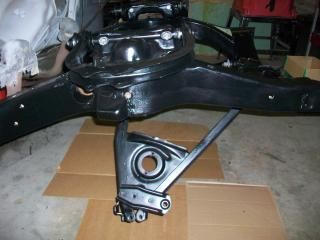
The picture below has a little back story. As I located all of the shoulder bolts and hardware for the lower control arms, I could not find one of the cup washers. "What did I do with that thing?" I asked myself. "Surely I didn't throw it away!" I groaned as I rummaged around. I finally decided to check my junk pile. Wouldn't you know it but one of the bushings that had basically disintegrated and fell off in my hands during disassembly CARRIED THE CUP WASHER with it. Glad I didn't just chuck it all in the trash! I rescued it, shook my head, and the cleaned it up for reinstallation. 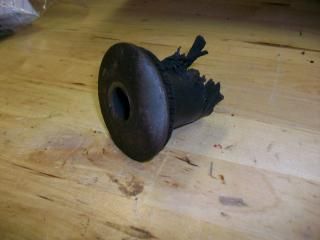
The last photo here is of the extra shims. I did save all of the shims and bagged them for which side, etc, when I removed the lower control arms a few months ago. So, why didn't I need to reinstall them? I figure it had to do with this... installing new bushings meant that the overall distance from end to end on where the arms would mount up to the crossmember holes CHANGED. There is no way I would be duplicating the same distance from the factory and I believe that is why the shims are there in the first place - to take out the play from front to rear so the arm itself does not slide. The only movement it should have is rotating on the shoulder bolts themselves.
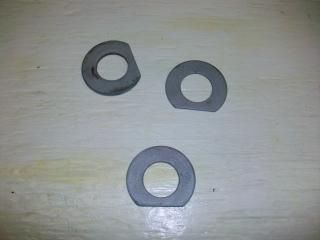
Time to get those spindles cleaned up! They are soaking in the parts washer as I write this post. And... I have new front springs to install. I have not yet purchased the shocks for the front end. Any suggestions? The springs are the Aerostar springs that will lower things about 2 inches. I already have new upper and lower ball joints and hardware.
|
By Daniel Jessup - 11 Years Ago
|
I got quite a bit done on the 55 Fairlane last night. The front end of the frame is about completely bare save a couple brake lines. I did not have a coil spring compressor but I opted to leave the shocks INSTALLED until after I had disconnected the ball joints. This left some tension on the shocks but since I used my jack underneath the lower A arm to offset the pressure and the upper shock bolts were removed first. After that the jack was released and the coil just slid right out. I will disconnect the shocks from the lower A arms once I have them on the bench to remove the bushings.
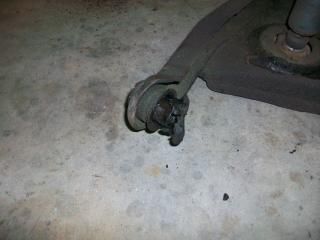
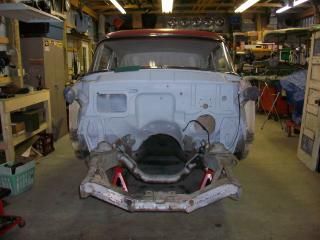
Speaking of bushings, some of them were so old and worn out they literally fell off in my hands once the bolts were removed. The only difficult item to remove was the large shoulder bolt holding the front of the lower A arm to the crossmember. It was rusted pretty well and once I had it removed I noticed it was pitted badly. I think I have a good used one somewhere. The reason for the rust? As you can see from the photos, years ago a previous owner had made a repair to the crossmember by welding in good metal that seems to be thicker than stock. Unfortunately no weep holes were never drilled in thebottom so all these years the moisture had collected in the crossmember with no place to go. The crossmember is very stout and I beat on it with a hammer all night long, but I think I am going to have a welder friend of mine look at it and shore it up in a couple of places. I made a note to myself to drill a few holes when he is done. I also started disassembly/cleaning of a 1956 Ford steering column and gear I had purchased a few months back. I like the 56 wheel better, and from what I understand the 56 steering gear had a 3 tooth sector over the 55's two.
Does anyone know why Ford had to put these shims in the FRONT of the Lower A Arm pivot point? I am wondering if they have anything to do with alignment (like the shims used on the Upper A Arm) or is this just something that Ford used because the crossmembers were never square? I don't think they have anything to do with alignment but I could be wrong on that.... I plan to put them back in because they were there when I disassembled the arm.
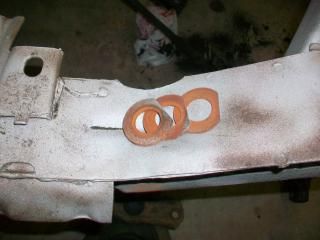
I did get a little hungry last night while working in the garage for a few hours and decided to break out the deep fryer and throw down with some homemade apple pies... yep - I put together the crust and all from scratch. You can see my kids tearing into these things. Nothing like a snack before the youngin's go off to bed! 
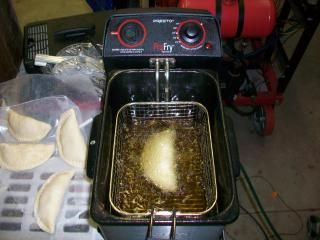
If any of you have any tips on disassembling, cleaning, and inspecting the steering gear I would appreciate it. When I took off both of the covers of the gear housing last night, the gears themselves looked pretty good, I think I saw only 2 or 3 pits as I rotated the gears on the shaft and knuckle.
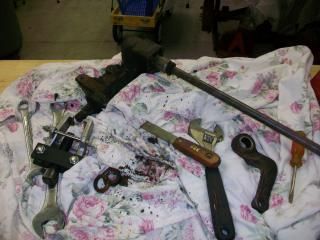
|
By Daniel Jessup - 11 Years Ago
|
Thanks for the replies fellas -- I was looking at the crossmember yesterday and decided to go into the depths of crossmember hell. Healthy repairs had been made to the crossmember before (20 years ago) with metal plates about twice as thick as stock. Unfortunately no one had thought at the time to drill weep holes for the water to drain out and I suspected that there was some rot. So, after showing a few photos to my welding buddy (that's his full time job) he said it looked ok and he would bring some plate over to weld to the crossmember so long as there was good metal to weld to. After removing the very front angled "bumper" with my cutting wheel, I snapped a photo or two of what was behind it...
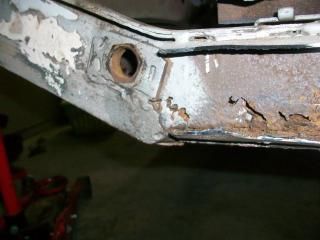
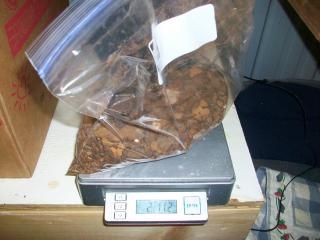
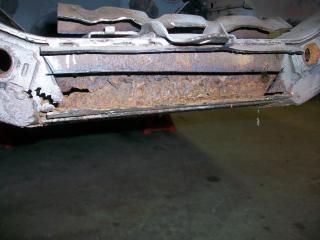 Yep if you look at the photo of the bag of rust on the scale, you will see the readout - 2 lbs and 11 oz of rust and scale !!! The irony in all this is that the metal from the repairs 20 years ago is as stout as it can be and I can take a hammer to it all day long. The crossmember itself is still very strong but I am glad I opened this up. I plan to sandblast the inside and get where I can. After that I will treat the rust and then paint. My welding buddy will come over and put good metal plate to cover the front from top to bottom and from the thick reinforcement of the shoulder bolts from side to side. The other side is not quite as bad but I will have him weld there too. I did try to remove the bushings from the lower A arms, but not having a shop press, I spent 30 minutes with a ball joint press, a hammer, and gorilla type force. I got one of the bushings to move about 1/4" -- that's it. Any tricks to removing these bushings or am I going to have to take them to a shop to have them all pressed out?
|
By Daniel Jessup - 11 Years Ago
|
Fellas thanks for the advice and ideas. I too decided to push out the inner bushing/sleeve by heating up the rubber (some of it was so worn it had just about disintegrated!) and just yanking it with a pair of pliers. After that I cut a deep groove in the ID of the metal bushing to get me started and then just simply tapped them out. One of them I obviously separated. It was not too difficult to say the least and now I can go ahead and blast those arms and then paint them up pretty. I barely nicked the edge of the ID on the arms, but I don't think it is going to be any big deal. Looks like those were the original bushings on the car.
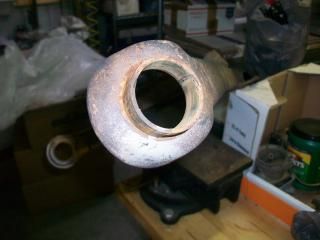
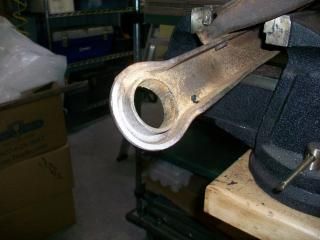 Mark, I like that idea. I will have to see if I have a screw assembly long/large enough to press the new bushings in there. Gary, I don't know why I didn't think of the air chisel! duh! That would have sped up the process for sure.
|
By Daniel Jessup - 11 Years Ago
|
My welding buddy talked to me the other day and he said he wants to get on the project so that motivated me to get out the sandblaster again and go to town on the metal in question. You can see the photos below (looking from the firewall) I only need a few plates welded in and we are good to go. Could I get another crossmember from a repro shop? Yes. Would I feel confident in getting the geometry right? No. I am sure there is a good way to do that with the measurements and all, but I figure if my buddy is telling me that it won't take much to "shore it up" why bother - he's the metal man, not me. The front is pretty simply - one long piece and we are good to go. The rear will need 4 pieces as the lower metal is very solid and does not need to be replaced but the wall itself needs attention.
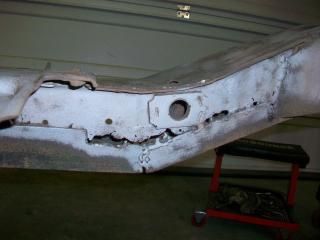
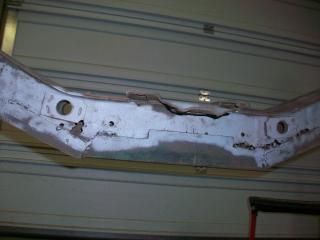 I also did some work on those front end parts as you can see... blasted with glass beads and painted with semi-gloss black Rustoleum. The center link was in very good shape and disassembled easily. It should be a breeze to put it back together. The other parts in the box are just the start to the rebuild of the front end of course - gotta get this thing back on rollin' wheels before I put the 292 and 3 speed overdrive in the car. The steering gear is ready for a new sector seal, worm and shaft, shims, etc. I soaked it in solvent in a parts washer for quite some time and then cleaned it thoroughly. I took a wire wheel to the exterior and painted it in semi-gloss Rustoleum as well. All of the parts I need for the rebuild are on their way and hopefully I can have that thing buttoned up by next weekend. Can't wait to feel that steering tighten up. The original was as loose as a goose!
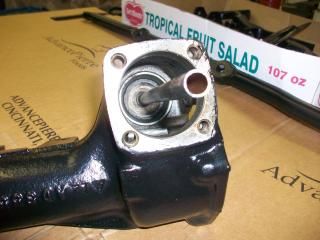
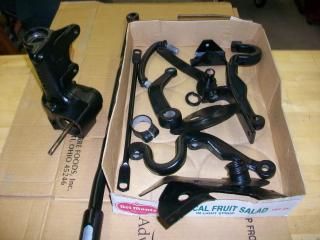
|
By Daniel Jessup - 11 Years Ago
|
My buddy Mike came over, looked at the crossmember, tapped around a bit, and told me he didn't think it needed to be replaced - let's weld her up! It didn't take him 20 minutes with my MIG 135 from Eastwood and Mike had it finished. We used 1/4" ad 1/8" plate cut to fit. He had good penetration throughout and I have already starting doing a little judicious grinding in a few areas to clean things up a bit. This thing is pretty strong and definitely stronger than stock. I have some Inner Frame Coating on the way from Eastwood, and will hopefully finish cleaning up the frame for paint soon.
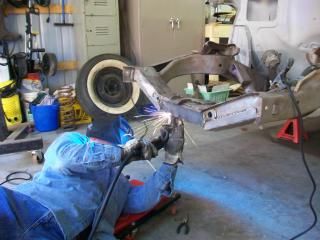
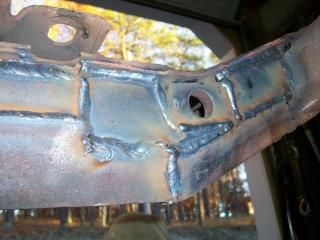

|
By Daniel Jessup - 11 Years Ago
|
It has been some time since my last post, but I have good reason - believe me. There are things more important than our cars, that's for sure. However, the time I can spend in the shop is a good opportunity to meditate, relax, and unwind after dealing with so many people all day long and helping them with their problems. I have been known to crank up a good southern gospel music CD or even one my favorite sermons from a preacher of yesteryear and have at in the garage with all the work (er, fun).
Back to our blog After the cross member was welded up by my friend Mike, I decided to smooth it up a bit and paint it with 3 coats of Rustoleum. I like the semi-gloss sheen on the frame and will use that for the sub assemblies as well.

I finally got back in the shop last night after spending a few weeks with other priorities. First up was the steering gear box and the rebuild. I had all of the parts I needed. The worm gear on the shaft was a used unit I found, but it was very near pristine on the grooves and fit perfectly. The bearings were already in good shape so I cleaned and kept those. I ordered a new seal for the sector shaft that holds the pitman arm. I got it from fleabay for something like $4 shipped and the thing fit very, very well. It was a US brand name seal, but memory fails me at the moment to tell you which one.
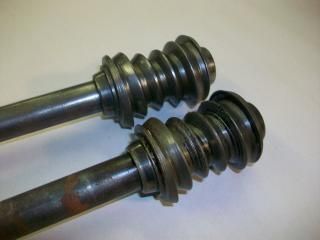
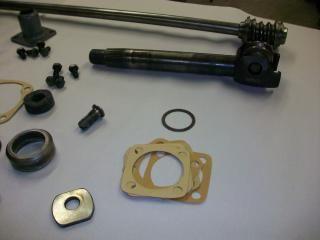
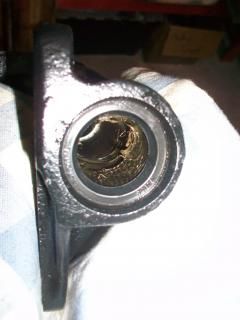
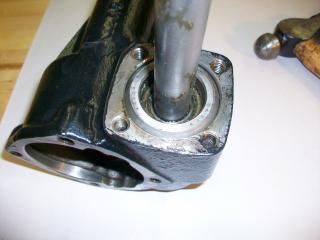
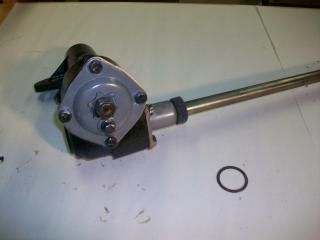 When I got it all completed, I was scratching my head over an "extra" part that I did not recall. After a few minutes it dawned on me that the large washer was actually the keeper for the original rubber seal for the sector shaft. I had forgotten that the seal was actually two pieces, so that large washer was obviously not need because the new seal was now one piece. The shim pack was interesting to deal with. I looked at the original number and thickness of the shims that were installed originally and I tried to install new shims that were an exact match. After torqueing down the bolts I spun the steering shaft and thought it seemed loose. As a matter of fact it was so loose that it actually had a little but of runout (vertically). "Well that can't be right," I muttered. After I looked at it crosseyed for a moment... "Hey bonehead! The replacement worm gear - that's what making the difference here." So I removed one of the original 3 shims and just checked to see what would happen if there were no shims.... TIGHT as it could be! No wonder there is a little frustration over getting the pre-load right. I guess it is a little tricky. I went through my pack of shims and just kept working on it until I found 3 that didn't have any play on the runout vertically but still kept it spinning "right"... now, what "right" actually is, I have no way of knowing. Someone had suggested using Ford's shop manual for the load, but that is with the leverage of the steering wheel. And... I don't have a torque wrench that goes to a very small inch/pounds. I guess I need a spring scale anyway. However, I would like to get this right on the bench before install... any ideas?
I greased the gears up pretty good and wrapped it all in plastic until it is installed. I have gear oil for it 80w90.
While I was at it I decided to put together the drag link. It was already in good shape - it just needed to be cleaned up.
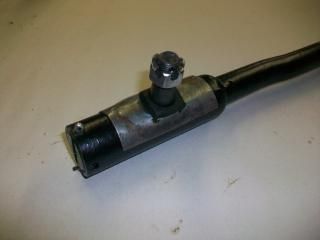
Things were going so well I decided to tempt fate and dismantle both upper control arms. I needed heat on one occasion but things went reasonably well. Again, some of the rubber was about ready to disintegrate so it was a no brainer to replace all of this stuff up front.
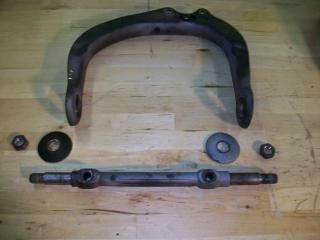 For those of you that really know your stuff.. yes there are 3 large washers per upper arm. The third is in the box.
|
By Daniel Jessup - 11 Years Ago
|
56_Fairlane (9/1/2014) Does your compressor have a water trap or water separator? Your compressor can be the source of moisture especially in high humidity.
I have 2 water traps before the rubber line/hose begins and I have another water trap right before the tank. There is about 60 feet of 1/2" metal pipe before the 2nd trap, and there is about 50 feet of rubber hose before the 3rd trap. I have never had any moisture problems before. I paint all the time with an HVLP gun and get plenty of dry air. I think the sand blaster tank had sat UNOPENED all winter long and what with repeated heating/cooling cycles in my uninsulated garage there was condensing in the tank. I also noticed that the sand valve is pretty small (IMO). Don't know now to remedy that since the bottom of the tank looked like a small threaded opening too. I guess when you have a big tank like that the issue is going to be the "funnel" where all that sand has to hit a valve at some point.
Maybe I can get back into that thing this week.
|
By Daniel Jessup - 11 Years Ago
|
DryLakesRacer (9/1/2014) I use Summit Urethane restoration shop paint for our race cars. It works great; I always add fish eye to it.. California is getting to be a pain to buy paint unless you want to put clear over it which I don't like to do so mail order has become my life line....Good Luck
Sounds good. I am hoping that this stuff does well on my firewall and if so, I will use it on the rest of the exterior. I am not looking for a show car, this is an all weather driver car for my Father-in-Law.
|
By Daniel Jessup - 11 Years Ago
|
Not much done today on the '55... I completed a project that the wife and oldest daughter have been begging me to do - an antique headboard for my daughter's bed. The story goes like this... My parents moved out of an old home that was originally built in the 1850's, had been used as one of the hospitals for Stonewall Jackson's army, etc. In the scrap pile when they bought the place years ago and put stuff into storage was a very old door and 6" trim pieces as shown. When they sold the place and moved out they gave me the old door and trim pieces. "What do I want with these?" I said to them. My parents just smiled at me because they had gone behind my back and talked it up to my wife and oldest daughter about the idea of making a headboard out of this old door. Little did I know! 
Anyhow since it was labor day I had some extra time to examine this thing and get the ball rolling to crank it out and get it done. You can google this idea for more photos on the internet - I am sure there are better ones than mine, but suffice to say I turned the door on its side, trimmed off both sides (what was the top and bottom), MADE CROWN MOLDING OUT OF THE OLD TRIM (please don't ask how that went lol - I finally worked it all out), and then put a piece of trim on the top for a shelf. My wife and daughter were thrilled to say the least and it all passed inspection. Best thing is the girls decided it did NOT need to be painted since the old patina was exactly what they were after.
|
By Daniel Jessup - 11 Years Ago
|
Been a long time since I posted anything, but to be real honest it has been a long time since I did anything in the shop. This past weekend I did some more blasting after I got my issues with the sandblaster sorted out. Once I changed over to a finer grit (I use that Black Diamond black sand from Tractor Supply Company) we got to cooking with gas. No worries and it went well. I am pretty sure the frame and front end will clean up pretty easily. I did make the mistake that weekend of not priming right away so after a few days flash rust had set in. A little bit of Naval Jelly and the rust dissolved right away. I removed the steering gear and column this morning - the three bolts that hold the gear to the frame were in excellent shape. I have seen pretty rough examples because moisture has a tendency to get trapped up inside there. After that I did some more blasting and prepped for "direct to metal" primer/surfacer. I have used the primer before on some stand alone parts but never on a panel... It sprays very well out of the gun and I like the coverage. The company is called "Tamco" and is based in the Richmond, Virginia area. The white paint for the tutone color is a 66-69 Ford Wimbledon White Mustang SS Urethane from Eastwood (made by Kirker). We will see how that shoots out of the gun. I plan to paint the hood hinges first and see how that goes. I might get the 56 steering column out, clean that up, and then paint that with the WW topcoat also.
I also had the chance to blast in the cabinet this past week so I got some of the frame pieces finished and linkage rods finished. I also sprayed the Tamco primer on the hood hinges. After doing so much dismantling it feels good to finally have something ready to go back into the car.

Question: I need to modify the split cover plate that goes around the column and screws to the firewall. My cover plate is obviously for a Fordomatic and not for a manual transmission car. Does anyone have good measurements on where that hole goes and its size? Does anyone have a split cover plate they would "part" with?
|
By Daniel Jessup - 11 Years Ago
|
He is supposed to be in to see me this Christmas. For some reason,,,,, I can't reach him on his cell phone????
|
By Daniel Jessup - 11 Years Ago
|
Spent a few hours today with the trusty sandblaster and the front end. I was surprised at how well my air compressor held up. I didn't blast continuously and would try to let the air compressor "catch up" from time to time, but I was happy with how it did and happy with the results. I also blasted a bellhousing - the pressure pot made QUICK work of that piece and the engine paint turned out nice. I only have about 5 to 6 hours on the pressure pot sandblaster I got from Tractor Supply a while back but I am not impressed with how quickly the "stopper"? is wearing out on the deadman's valve. The sand has worn away the tip on the closer (not just the ceramic tip - that is another story) but the top piece that slides over the tip - that piece is so wore out that the blaster now will leak air when the spring loaded lever is completely closed. I guess it is cheaply made. If there is anyone out there that has any good suggestions on a quality tip/closer I would appreciate it. I am going to look at TP tools. I have one of their Blast Cabinets and have used glass beads for 10 years now. I reckon I have spent countless hours using that gun and have only had to replace the nozzle about 3 times. I know sand is more abrasive, but come on... 6 hours???? Maybe I should take some close up shots of the tip just to show the erosion that has happened pretty quickly.
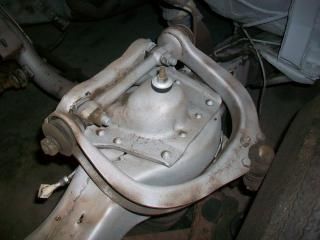
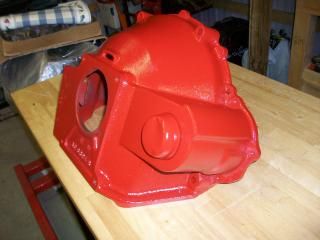
Next up - disassemble the front end so that I can paint the frame and separately blast the pieces in the cabinet. I have new rubber for up front and I have new Aerostar coils as well. I did locate a split sheet metal surround for the steering column and shifter column, and I have started preparing the 56 column and other shifter parts for painting. I also have those hood hinges about ready for topcoat.
If you have been wondering where some of the time goes for projects like these and why it has been a while since my last post, at times my wife gets me side-tracked on things like this.
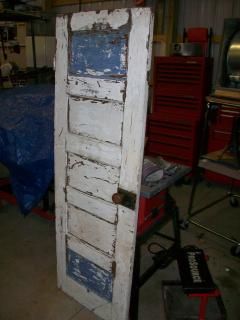 She found this door today at an Apple Harvest Festival about an hour away from us. "It was only $10," she gloated as I unloaded the thing from the van. "Where do you want me to put this?" I asked, knowing what she would say.... "Oh, just put it in the garage, honey." And so the buffet the garage has been on for the past several months continues. I have never seen a garage hold more crap.... let's see - all the camping gear, outdoor gear, snowtubing and snowboarding toys for the kiddos, gardening supplies (yep - I likes me my peppers, padre!), woodworking tools and table saw, several golf bags, bicycles, fireworks, MY grill/smoker, etc. And my wife laughed when I originally told her we needed a 60x40 instead of a 40x24. What was it she said, "How much room do you need for crying out loud?" Maybe I'll just take the latest project she found and put it in the bedroom! I'm sure that would fly!
|
By Daniel Jessup - 11 Years Ago
|
Things went really slow this week but when I look at these photos, I say to myself, "who cares?" My boy (I have 3 kids, 2 daughters and a son) came into the garage with me last night to work on one of his projects - he was making a homemade trailer to go behind one of his small Tonka type trucks. "Hey dad, can I help?" he says. "Sure thing," I tell him, and my 11 year old son Ethan (we call him EJ) grabs the air ratchet and asks what's next... . I laughed a little and patted him on the back and we spent a couple of hours removing the front bumper, the hood hinges, various hoses and wiring, the sway bar, etc. It took me a whole lot longer because while he has his own hand tools he had never used an air ratchet before... I guess he has never really asked me to. Looking at the photos here I guess I should have made him wear a pair of safety goggles - will have to do that next time. He always knows to wear a pair when he is at the grinder or using a cut-off wheel or a Dremel tool.
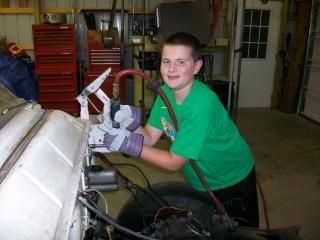
I did take some photos of the front sway bar after removal and of a sway bar that I had on the shelf here. As I recall, it was from a 56 Station Wagon... can I mount that front sway bar with the same metal brackets? It looks like the bushings are the same but the ID of the hole is probably different. It looks like I will need new a kit for the hardware also. Those rubber washer bushings are WORE OUT lol. The bolts from the wagon sway bar look like they are a little longer. I guess there is such a thing as a kit for a wagon sway bar?
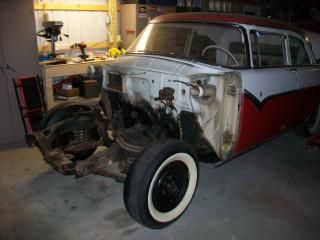
I will have to say that with my son's interest here this week things have gotten a whole lot more "fun". We'll see how long he lasts. The last thing he told me before we went in for a shower last night was whether or not he would be allowed to drive it when he got his license. I laughed and said, "You are going to have to talk to your Papa about that one!" I'm sure he will.
|
By Daniel Jessup - 11 Years Ago
|
pegleg (8/17/2014) You may have created a monster! Good for you.
Let's hope! Here comes the Hot Rod Reverend Jr. 
|
By Daniel Jessup - 11 Years Ago
|
Well I finally had a half day off today and got a chance to get in the garage for a few hours to turn some wrenches on this old Ford. Right now my life is very busy what with school starting up (I administrate or church's academy), the new volleyball season (yep - I coach girls' volleyball... don't ask me how I got talked into that but it has to do with my daughters lol), and everything else with a family of 5 I don't know how I have time. No complaints,,,, just letting you know the reason for so much time between posts.
I removed the transmission and the crossmember along with the drive shaft. It took a little more time than I anticipated - stuff was really gunked up under there. I remember years ago that a rear main seal was dumping oil everywhere for while - guess it made the floor pans last a long time! I did find one small place on the driver's floor pan that was not solid. Everything else is good.
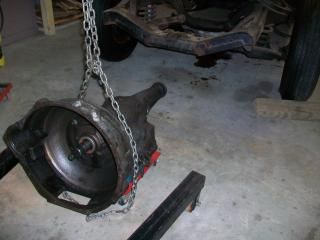
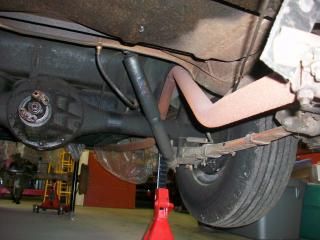
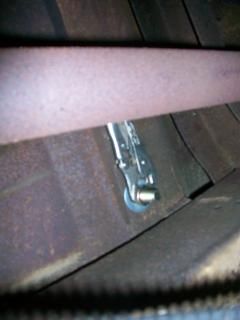 If you are wondering what is going on with the photo of the vise grips... I was looking around under there and found them clamped to a nut! I think the vise grips were left under there when the seat belts were installed. That's what I get for having teenagers help me turn wrenches! I should have counted all my tools after that project was done. I took them off... they are still good after 7 years or so and all the road time. That crossmember weighs an extra 5 lbs from all the crud, grease, and road grime collected on it. Gotta get that thing cleaned up and painted. I guess the transmission mount rubber is near perfect because of being sprayed with oil so much over the years. Hopefully I can get the firewall cleaned up soon and then start prepping the firewall for paint. I would like to do that before weather sets in here.
The photos of the tail pipes are a for a member who asked for them sometime ago but I could not find his post. If you know the member or remember the post... can you direct him here?
thanks
|
By Daniel Jessup - 11 Years Ago
|
I did have one of our graduating seniors over to the house one afternoon because he was a troubled kid, had some issues, his mom couldn't handle him, yada, yada, yada... the boy helped me with some disassembly and I taught him to use a few tools, etc. We actually had a great time, he learned some things, and fast forward to today he is proudly serving in our US Navy based somewhere outside Chicago (one of the Great Lakes maybe?). Anyway, he lost one of my good 3/8" sockets THAT I STILL CANNOT FIND... I guess it is some box of parts or somewhere in the garage. I laugh about it each time I talk to him.
Yep - the old vice grips. Surprisingly they stayed in such good shape. I guess the car really never was driven in wet weather making the difference.
@Meandean - lol - my dad was same way!
|
By Daniel Jessup - 11 Years Ago
|
pegleg (8/25/2014) Probably the base Caled "Great Lakes" which is actually in North Chicago or Waukegan, Il. It's the basic training site for most of the Navy. I was there a few short years ago (50! )
Frank - shows how ignorant I am, until Brian phoned me from there to let me know he was stationed there I had NO IDEA we had a naval base outside of Chicago! Brian is a good kid and has turned a major corner in his life. He went from suicidal to being quite confident in himself as an individual. A lot of time, PRAYER, and sweat went into that boy and we are proud of him. He is supposed to see me at Christmas time when he gets extended leave.
Crazy thing is... he told me wanted to go on SUB duty and was trying to find some way to be an engineer on one of the nuclear subs we've got! 
|
By Daniel Jessup - 11 Years Ago
|
Alrighty back to work on the old Fairlane (after our first whirlwind week at school). I cleaned up the interior a bit and removed the dash and quite a bit of hardware. I already have a painted dash and painted trim pieces ready to install, just wanted to get all of this removed to make the firewall work easier. I also have plans to put in the clutch/brake pedal assembly that I have ready to go. On the list are quite a few grommets, a new wiring harness, and various pieces of anti-rattle/anti-squeak pieces. I am also going to replace the carpet.
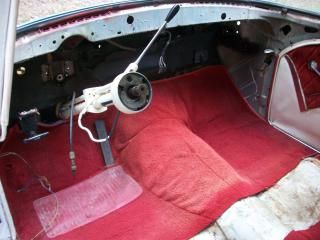
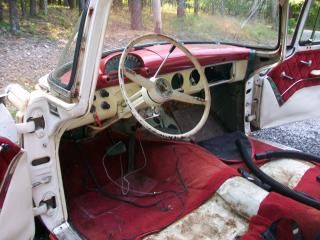
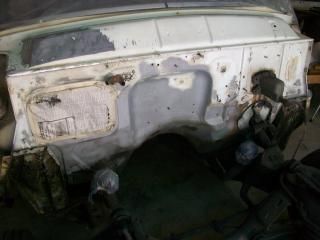
I also pressure washed the firewall and front end trying to degrease it... wasn't too successful there. I need a steam cleaner - anyone got one to loan out? After it dried I broke out the sandblaster but it did not work too well. The sandblaster is a decent one I got from Tractor Supply a few years back. Of course I was blasting in 90 degree weather and high humidity so that did not help, but my air getting to the tank was dry. I think the tank itself had some condensation in it working against me. I turned it over and put my flashlight through the hole to see the valve. On the interior of the tank at the bottom there were some "runs" of water leading to the valve. If you guys got any tips on sandblasting in hot weather I am all ears! I only got a little bit done on the firewall and had hoped to do a lot more today before being pulled off on another wifey project to make an antique headboard for my oldest daughter's bedroom. Maybe I will put up some photos of that project too. It is being made from a turn of the century door and vintage trim that is about 6" wide. She wants me to make "homemade" crown molding - haha, we will see how that turns out. I did order the Ford Wimbledon White for 66-69 Mustangs from Eastwood yesterday. Hopefully I can get this firewall painted (and maybe the hood hinges) before weather sets in.
|
By Y block Billy - 10 Years Ago
|
A good buffer and rubbing compound and you can buff those clear again. I had a roll of mylar and would just tape a new one on but its always a pain in the ass keeping them clean. I learned a long time ago to never let the richochet head towards the window and it last much much longer. The other problem is people keep blasting through the left index finger of my gloves because they blast right into it while holding small parts. I can make stuff last because I know how to use the thing without damaging the window or gloves. Its when you let other people use it that its common nature to keep getting the part closer to the glass, getting more richocheting material at it and before you know it you cant see. I hate that every time I repair it so things are clear as a bell, somebody else has messed it up and I have to gop through it again to get my own work done.
|
By miker - 9 Years Ago
|
Daniel
I know it's a lot of work. This may help you stay motivated on the wheel.
http://limeworksspeedshop.theshoppad.com/#/product/crestliner-steering-wheel-16-diameter-ivory-white-for-1951-ford
Yikes!
The link opens real slow.
|
By miker - 9 Years Ago
|
FWIW, I've had good luck hiding relays in a hollow voltage regulator. Looks more like stock, even if you have two of them. On a 'bird it's even up by the headlights.
|
By 43mike - 10 Years Ago
|
You're doing a great job on this, what with the comments, pictures, and advice. I'm getting ready to do the same with my '55 Townsedan, so I'm watching this with great interest. What your doing is almost exactly what I have planned for mine, to the letter so far. Keep up the good work. Mike, Lanett, Alabama
|
By texasmark1 - 11 Years Ago
|
go Daddy go!
|
By texasmark1 - 11 Years Ago
|
reminds me of how my Daniel began helping me on my 57... he was only 5 or so, but he dug right in!
now he's driving his restored 63 Mercury back to his sophomore year of college...
best times we've had together... wrenching and getting greasy.
don't miss a minute of it... EJ may surprise you and really pick up the torch!
Mark
|
By Rono - 10 Years Ago
|
Nice job Daniel....what type of spray gun did you use?
Rono
|
By Rono - 10 Years Ago
|
I feel for you Daniel. I know just what you are going through. How does U Haul put it?... "An Adventure In Moving"! These major "life events" always set you back on the projects you have started no matter how well you try to plan. One storage/ organizing solution that has worked for me in the past when I have moved is to use the mobile metal storage shelving you can buy at COSTCO. They are VERY strong and you can set the shelve height on the legs wherever you want. I have several of the 6' tall units with 5 or 6 shelves on each that I store project parts on. Since they roll around, you can move them fully loaded. I have 2 sets for the coupe, 1 for the Ranch Wagon and a couple of the lower ones for my Customline and the Harleys. I hope your transition goes as smoothly as possible. Rono
|
By Rono - 10 Years Ago
|
Hey Daniel; A move like the one you (and I) made definitely takes the wind out of your sails when you are on a roll and getting things done on a project. I'm confident you will be back on track soon. It's hard to kill the passion we have. Rono
|
By Rono - 8 Years Ago
|
Daniel;
Glad to see you are back at your project. It's a good feeling to get up and get going on a project you love. I have heard about the Vintage Air Alt/AC brackets, but this is the first time I have actually seen the kit. Looks good! We plan on putting Vintage Air in the Ranch Wagon and will be using that bracket kit.
We also mounted a radiator overflow tank in the Ranch Wagon and I didn't use the pop rivets they included either. I took a little bit different route for mounting and made 1 long bracket that attached to the two radiator mounting holes. Then I mounted the two tabs on the tank directly to the bracket.
Your 55 is looking great! Keep it up.
Rono
|
By slumlord444 - 9 Years Ago
|
I've been running off the shelf halogen sealed beams in my T Bird for many years. Also ran them in a '56 Ford pick up many years back. No relay and no problems with the stock headlight switch. Large improvement.
|
By Bobwanna - 9 Years Ago
|
Daniel, Thanks for keeping up on this project and sharing with us the products and tools used especially stuff from HF. I have learned much about painting here since I am more of wrencher on cars - Bob
|
By Bobwanna - 8 Years Ago
|
Hello Rev, Sorry to hear you were under the weather a bit, however I am very happy to see your progress on the 55. I will be following your progress on the AC install for whenever I do that on my 56 Fairlane Club. I tend to keep my older cars as original as possible but adding the coolant recovery tank make sense. I hate the thought of puking coolant on the ground. I am pretty poor at body work and understand using some sort of pin on trunk or hood removal. There is a system using "Cleco" pins to keep parts in alignment. I believe they go down to 1/8". ( They are definitely more expensive than the tractor pins) I know you also post at Ford Barn and am starting to follow discussions and maybe contribute my limited knowledge there. Cheers - Bob
|
By Lord Gaga - 8 Years Ago
|
"Why I get involved in little projects like this, I don't know. Maybe it is the satisfaction of fabricating something small that will be entirely functional and serve a purpose, maybe it's the OCD part of me that just can't let things rest, who knows? :confused:"
It's called Anal Retentive Disorder. ( Describes a person who pays such attention to detail that it becomes an obsession and may be an annoyance to others, potentially to the detriment of the anal-retentive person.) Good luck with that!
|
By brokengate - 11 Years Ago
|
Daniel the washers are a substition for the alignment shims, on my 56 they are u shaped or slotted squares. Pay attention to how many or the measurement of them for your returning fender alignment on rebuild, the slotted make it easy to add or remove, think I've seen repops on ebay. Thanks for the pics you know we love the photo journals.
|
By lyonroad - 11 Years Ago
|
Daniel Jessup (8/2/2014)[hr Now I have delved into the realm where only the talented and dedicated dwell - an all out assault on your vehicle, by yourself, to do the mechanical, the body work, the paint, etc.
Daniel, I have done a couple of vehicles, well one done and one underway, and I am living proof that in no way am I in the realm of the talented. Given your current experience I expect that your level of expertise will surpass mine in, if it already hasn't, in short order.
I am still trying to wrap my head around your hood removal system. My wife won't help me anymore.
Good luck with your project.
|
By lyonroad - 11 Years Ago
|
Daniel Jessup (8/7/2014)
One last item - you see the stack of washers there on the firewall mount for the fender at the rear. What is all of that about? Is that something Ford did? I will have to check the manual - it seemed like a Mickey Mouse setup.
Daniel, My '55 Club Sedan had a stack (two) of washers there too. I replaced them temporarily with a thick stainless washer. I suspect they are part of the process of aligning the top of the fender with the cowl and leading edge of the door.
|
By lyonroad - 11 Years Ago
|
Daniel Jessup (8/24/2014)
The photos of the tail pipes are a for a member who asked for them sometime ago but I could not find his post. If you know the member or remember the post... can you direct him here?
thanks
Found it myself Daniel. Thanks. Good call on the vice grips - "it was a teenager". I'm still looking for a 9/16" wrench that was used somewhere but there hasn't been a teenager around here for almost 15 years!
|
By lyonroad - 11 Years Ago
|
Daniel Jessup (10/8/2014)
Does anyone know why Ford had to put these shims in the FRONT of the Lower A Arm pivot point? I am wondering if they have anything to do with alignment (like the shims used on the Upper A Arm) or is this just something that Ford used because the crossmembers were never square? I don't think they have anything to do with alignment but I could be wrong on that.... I plan to put them back in because they were there when I disassembled the arm. 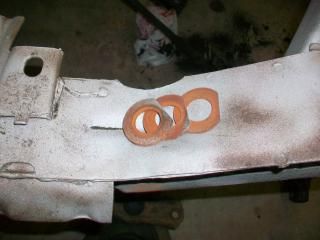 Daniel, I am pretty sure they have something to do with the alignment. A few months ago markmontereybay (I think) posted that he was able to increase the caster on his Tbird by moving the shims around. I replaced mine with the horseshoe shaped shims so I can pull them out, put them back or move them around later. Nice looking family. Oops somehow I lost your quote.
|
By lyonroad - 11 Years Ago
|
Daniel, I took a small diameter drill bit (can't remember the exact size) and drilled as many holes as I could through the rubber. Eventually I could push enough rubber out that the outer part of the bushing came of. Then you can work on the inner sleeve. I think I used a die grinder ans a small cut off wheel to cut a groove in the inner piece and force it off. Here is how I put the new bushings on. I made a bunch of thick aluminum washers from scrap and disassembled a large three jaw puller.
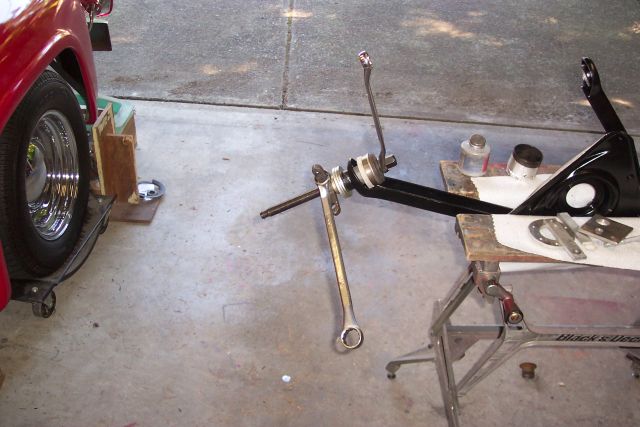
|
By lyonroad - 11 Years Ago
|
Daniel Jessup (11/29/2014)
For all of the success I have had, I did experience a "DUH!" moment last night when I was installing the bushings in the lower control arms. Note the photos... Maybe it was because it was thanksgiving week and I was distracted with deer hunting, smoking a turkey, having folks in, baking all kinds of food with the wife, Christmas decorations, blah, blah, blah. I don't know. The 55 Ford shop manual is a tick misleading when you look a the diagram. It shows the lower control arm bushing coming in from the front side, but if you look at it closely in the manual you can see a faint, dashed line, showing insertion from the BACK! Yep, I didn't catch all of this until I had fully seated the first bushing!!! When you do these, remember that both bushings, front and rear, are installed from the INSIDE of the arm facing out.... the large cupped washer should compress up against the rubber that is on the lip side of the bushing. Daniel, I came across this issue as well when I was redoing my front end on my '55 Club Sedan. When I disassembled the front suspension the bushings were installed as you have yours now. However the shop manual p.274 says "On the Thunderbird, the front bushing is pressed in from the inside of the lower front leg. On all other cars, the front bushing is pressed in from the outside of the leg." I raised this discrepancy on the forum, wondering if there was a typo in the shop manual. Some of the boys from Australia said that they had always seen the bushings pressed in from the inside in all cases. Another member of this forum advised that the '56 Shop manual does not have this note. Then came the revelation: Jimz Bird posted the following notification from Product Service Letter P-235: "A COMPILATION of PRODUCT SERVICE LETTERS" which is a publication from CTCI. This may clarify the bushing install.Product Service Letter P-235 Items 1002-1014 February 21, 1955 Item 1005 FRONT SUSPENSION (1955 Car and Thunderbird) A double-shoulder front suspension lower arm mounting bolt bushing (B4A-3069-D) was released for the 1955 car and Thunderbird. However, this bushing was not used in production. The bushing (B4A-3069-C) now being used in production has a single shoulder and was used in late 1954 production. The removal and installation procedures in the 1955 Ford Car Shop Manual are for the double-shoulder bushing. Please make the following correction Page 274 of the shop manual to cover the single shoulder bushing. On fig. 8, change Detail #5 to Detail #13. Cross out the note concerning Detail #6. Rewrite the second paragraph fig. 9 to read as follows: “On the Thunderbird and all car models, the front bushing is pressed in from the inside of the lower arm front leg.” In fig. 9, cross out the note concerning Detail #6.
I have taped a copy of this correction in my shop manual.
Hope this clears things up for you and others who follow.
|
By DryLakesRacer - 11 Years Ago
|
I use Summit Urethane restoration shop paint for our race cars. It works great; I always add fish eye to it.. California is getting to be a pain to buy paint unless you want to put clear over it which I don't like to do so mail order has become my life line....Good Luck
|
By MplsMike - 7 Years Ago
|
Nice job! Your car is looking awesome.
|
By 56_Fairlane - 11 Years Ago
|
I doubt it came from the factory with a stack of washers like that since it looks like there's some of that white respray on them.
|
By 56_Fairlane - 11 Years Ago
|
Does your compressor have a water trap or water separator? Your compressor can be the source of moisture especially in high humidity.
|
By crownvic55 - 10 Years Ago
|
Daniel, If, as the saying goes, cleanliness is next to Godliness then you are in very good shape. Your work is immaculate. Ben
|
By ian57tbird - 10 Years Ago
|
Looking good. It will be better than when it left the factory. Always nice to see.
|
By ian57tbird - 9 Years Ago
|
Be careful. The heat from the disk sanding can buckle panels and you will find yourself filling areas that may have been straight before. I prefer a composite disk that is an open plastic structure with an abrasive in it. The disk I am talking about removes the paint but does not score the steel surface easily, preserving the factory metal. Which ever disk is used you should take care not to heat it or it will distort.
|
By ian57tbird - 9 Years Ago
|
Be aware, bondo dust is carcinogenic.
|
By ian57tbird - 9 Years Ago
|
You still need to take care even with those discs as they still create some heat and it doesn't take much to get warping.
|
By ian57tbird - 8 Years Ago
|
That sounds amazing! Things have changed so much over the years. I need to learn more about the chemistry behind the paints.
|
By Cliff - 7 Years Ago
|
NICE
|
By jsprengeler - 7 Years Ago
|
Awesome Dan!!
|
By Meandean - 11 Years Ago
|
The vice grip photo reminded me of growing up just a little bit on the rural (not redneck, just rural) side.
My father was not big on fixing things around the house and all projects he started seemed to fizzle out before they were finished.
Our kitchen sink had plastic/bakelite type handles over the ribbed valves. At some point the one for the cold water broke or stripped so for years we could only get hot water out of the kitchen sink. Eventually he stuck a pair of vice grips onto the valve and viola', we could turn the cold water on again! Only 1/2 a revolution before the vice grips hit the wall so not a lot of flow, but definitely an improvement!
|
By steinauge - 10 Years Ago
|
I cant speak for anyone else but I am thoroughly enjoying this thread! Thank you for going to the trouble of putting it up.
|
By Sirstud1 - 10 Years Ago
|
Love the build! I also have a 55 I'm working on... mine will be ratted out tho.. check it out... hope I can turn to u for some advise if things get complicated... lol. https://flic.kr/p/uaF8bN
|
By beachbumrod - 9 Years Ago
|
Nice plan, I am not that involved in mine yet but do have it on the road.
|
By charliemccraney - 9 Years Ago
|
Haven't done anything to upgrade the headlights yet. There are LED headlights now, and tried and true H4 halogen. For sealed beams, there are usually a couple options for brightness and that should allow for the easiest installation. I use Sylvania Silver Star sealed beams on my Firebird. They are quite a bit brighter than the standard version. They do draw more power, close to H4, so relays would be a good idea to go along with a higher powered sealed beam.
|
By charliemccraney - 9 Years Ago
|
Sylvania off at least two types of sealed beams. One is standard. The other is a brighter Silver Star. The silver star draws more power, closer to that of a standard H4 bulb. They're in most parts stores.
|
By charliemccraney - 8 Years Ago
|
Those alternators can be clocked. Loosen the four screws, separate the case just enough that it turns, and spin it to the desired location, tighten the four screws. If you separate the case too much, the brushes fall off, then you have to pull it all the way apart to reinstall those.
|
By charliemccraney - 8 Years Ago
|
NIce work. I would find a way to attach that shield using at least 2 mounting points. The hoses will lay on it in a way that the vibration and very slight force applied could loosen the bolt.
|
By Ted - 11 Years Ago
|
Daniel Jessup (10/21/2014) You can see the photos (looking from the firewall) I only need a few plates welded in and we are good to go. Could I get another crossmember from a repro shop? Replacement ‘54-56 crossmembers are available from Goodell Fabrications. 11986 S. 267th E. Avenue Coweta, OK 74429 Ph: 918-636-7071 Pricing is $299.95 postpaid.
|
|