By bird55 - 16 Years Ago
|
I've tried do do a blog to inform others of install questions about this project of mine.
There will also be random tbird and yblock photos posted there for other reference as I get around to it.
I'm still working on the bird AND the blog so they're both still in the works. 
http://birddropnz.blogspot.com
|
By Barry L - 16 Years Ago
|
Thanks for the blog link,maybe the pics of progress will inspire me to get off the computer and back out to the shop to work on my long neglected 57 'bird Barry
|
By pcmenten - 16 Years Ago
|
The torque curve of your engine caught my eye. That Isky 300 cam looks like a good one.
|
By LordMrFord - 16 Years Ago
|
I had problems with Bendsen's starter. One starter bearing broked after half year and a flywheel was not tapered for starter gear. So a gear just always not go far enough.
|
By bird55 - 16 Years Ago
|
LordMrFord, thanks for the heads up on the starter flywheel. I'll keep my eye out for issues with it. I think the flywheel I have IS tapered though.
|
By bird55 - 16 Years Ago
|
Barry L (1/3/2009) Thanks for the blog link,maybe the pics of progress will inspire me to get off the computer and back out to the shop to work on my long neglected 57 'bird Barry
Barry, I thought you had an AOD in your 57?
|
By Barry L - 16 Years Ago
|
No,might have been a different Barry. Nothing in my '57 right now.Still have the 312 & std 3spd w/od, sitting ,waiting for body repair.Years ago I swapped in a 428cj and C6 and a 4:30 gear set....way too impractical for a driver,but it sure did go! It all seemed like a great idea back then,but I'd like to get back to Y power and have something i can drive. Never did put more than 50 miles on the thing before parking it and tearing it all apart. Barry in Manitoba
|
By Don Woodruff - 16 Years Ago
|
Alan I am wondering how the steady mount stabilizers on the headers is holding up? At least that is what I assume they are from the pictures at the FPA website. Seems as if they may be a bit on the light side to keep a high torque engine in place. Don Woodruff
|
By bird55 - 16 Years Ago
|
Thanks for asking Don, I have had the same fears and had conversations with Stan (the designer/builder of FPT) from the beginning as I was very skeptical. He was very confident in his product and explained it in principle.
You have to consider that the steady rest must be tight so the engine doesn't rock or in any way be loose. Just like the original style. Then realize that one is "pulling" and the other is "pushing" against each other. They are 5/16" steel rod. And remember the engine actually is "sitting" on front and rear motor mounts as well.
I have had no issues yet, knock on wood. However, I run an automatic with a shift kit so I'm guessing that's less stress with shifting. I still wouldn't mind installing a safety chain or turnbuckle, link for some kind for insurance.
|
By PWH42 - 16 Years Ago
|
The safety chain is an idea borrowed from a major manufacturer.A few years back I took a Brand X car in trade for a Harley( stupid,Huh).A while after I got this car I got a recall letter from GM concerning bad motor mounts in that model with 327 engines.I took the car to the dealer and,you guessed it.Their repair was a chain wrapped around the left exhaust manifold and the frame.
|
By GREENBIRD56 - 16 Years Ago
|
Ok - I'm at work and the tables are right here - at a (conservative) 33,000 psi "proof load" for the 5/16 coarse threaded rod, its good for (.0524 x 33000 x .75) = about 1300 pounds axial pull. That using 75% of proof strength for safety sake. No worries with this unless you leave it loose and pound on it like a slide hammer. SAE grade 5 material jumps this to (.0524 x 85000 x .75 = 3,340 lbs allowable and SAE Grade 8 to (.0524 x120000 x .75) = 4,700 lbs. The weakest link looks like the male thread of the rod-end being placed in a bending situation - not good. Better design would be SAE Grade 8 threaded "stud" (all-thread / cut off bolt / whatever) tightened into the internally threaded bar (for 5/8 inch depth - two times the nominal diameter) and using a female threaded rod end. Fit thick washer between the rod end and the bar - and grind it (thinner) until the rod end tightens securely and stops turning - exactly where it needs to be pointed. If this doesn't work - get a chain........
|
By Don Woodruff - 16 Years Ago
|
I am most concerned about the bending moment of the outrigger welded to the header flange. Looks like all of the torque load is transmitted through about a 5/8 or so stand off about 6 or so inches long. It sure looks as this stand off will bend and or distort the headder flange with any serious torque load. 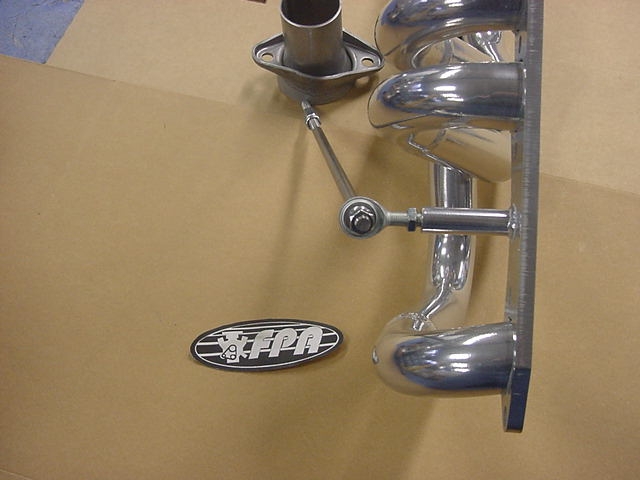
|
By bird55 - 16 Years Ago
|

I am not saying this ain't gonna break some day-maybe soon. But here is some more info on what it is.
The standoff you write of, Don is about 3" long, not 6". I was able to shorten mine some to get the rod to lean over more away from some other stuff below.
For my money it seems like an additional safety chain or turnbuckle link would solve the question. And I might add, I am no engineer, but this setup has been working pretty well-time will tell, I've got my fingers crossed.
If it's a stick car or of course a race car, there is gonna be more load - on everything. So on the headers you could always modify this part or start over and build your own.
Like I said somewhere else, I was skeptical, and discussed it with the manufacturer. I am not a salesman for the FPT.
You also have to keep assume that the rods and nuts are taunt. No rock and roll. This is a bad thing even on a stock tbird if not looked after and disaster can happen. With no slack in them there is less inertia.
|
By GREENBIRD56 - 16 Years Ago
|
I usually have my guys design little round bars welded on like that as if the fillet weld on the end is a tube.......so it would be a tube .75 diameter OD and .625 ID - .060 wall. Section modulus is .135 (a measure of bending stiffness) Moment arm (leverage) is 6 inches - load is 400 pounds maybe? How far from the rod eye to the crank centerline? Assume one side is loose? Many unknowns here. Stress in the weld (6 x 400) ÷ .135 =17,800 psi 17.8 ksi is less than the yielding strength of a MIG weld - this is a higher stress than I allow on the mining machines - but they run 24/7 all of the time. Usually on a weld of this type I insist on max stress of 7500 psi. Its beer thirty isn't it?
|
By Don Woodruff - 16 Years Ago
|
The design is probably OK but it seems a bit questionable. The constant loading under part or full throttle is probably ok but the impact loading during shifting is really questionable. As you have had no problems I'll shelve my concerns.
|
By GREENBIRD56 - 16 Years Ago
|
I think the offset, rod end style restraint is an excellent "out of the box" solution to the header clearance issues in the T-bird. After I saw this I immediately started daydreaming about using an "angle-milled" plate under a pair of "rams horns" (to turn them in toward the block a bit) with this sort of set-up welded onto the spacers. Anyway........ I don't agree with the size of the restraint bar - and the use of the male threaded rod end. Impact can increase any of the stresses we figure by a factor of three (or more) at any time. If the bar were increased to 3/4 diameter, fillet weld increased to 1/8 of throat, and the rod end mounted in a different manner, you could pound on it with a little less mercy.....which is usually what racers do! There is another way of mounting, with a female rod end - to clamp it to the welded stub with a Grade 8 capscrew through the ball (using a taper on the end of the stub for angular clearance). That way the rod end is axially loaded (as they are intended to be) down towards the frame mount. At the frame eyelet a set of the polyurethane biscuits used on a sway bar link would be just right......
|
By pegleg - 16 Years Ago
|
Also transmits all the vibration directly through the link to the frame. Makes the rubber in the motor mounts useless. The rod end would be better utilized turned 90 degrees. They are not designed for any stress's in this direction. Steve, Notice he said it's embedded into the header flange. If the joint in the flange is tight, then it's all a bending force at the face of the flange and really is a solid bar. The weld is not really structural. It's five o'clock somewhere!
|
By Don Woodruff - 16 Years Ago
|
I agree the rod end is being used incorrectly. I intended to machine up a Y for the vertical rod, but I still have a serious concern about the bending moment on the header flange. This could be adressed to some extent by using a larger outrigger footprint. As the welding demonstration artist asked after welding cast Iron, "Alright folks what do you want to see welded"? My cousin with out missing a beat said Aluminum to Oak.
|
By bird55 - 16 Years Ago
|
The stock steady rests mount to the side of the block(by the water petcocks) and then the same setup of a rod/but shorter attaches to the frame sides with rubber bushings on to a bracket. The header design of tubes/for the best flow, prevents the use of the stock location steadies, so they were built into the header design. clear as mud?
Hang on I think I have a picture somewhere-here it is.

|
By GREENBIRD56 - 16 Years Ago
|
Charlie - Solid clamping the ball of the rod end is an accepted mounting practice - and some rod end manufacturers even produce the little tapered clamping rings for use like this with a torqued capscrew. 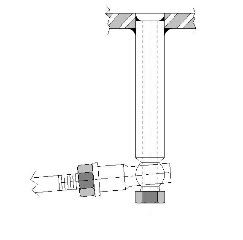
The output driveshaft torque is applied to these supports as if everything is rotating around an axis going through the front and rear rubber mounts of the engine and tranny (t-bird arrangement) and then resisted by these sidemount "steady rests". So they have to be as strong as the u-joints - and spaced as far apart as they are, the loads are really reduced.
|
By bird55 - 16 Years Ago
|
Steve, After further examining this, I have some of the female heim joints and looked over how they might be adapted. The ones I have are too big. But, anyway it got me to thinking, I am going to make that change. But… shouldn't a street car have some give there as in the rubber bushings? Afterall if it were rock solid or with urethane bushings somehow to the frame there would be no absorbsion of vibration? Again I am talking 300 odd horsepower in a primarily street driven car.
If it were a race setup you could lock it up. right? You wouldn't being going for a setup that was a compromise, quiet and comfy with 300hp.
An example I can think of is say…Ted's roadster, the engine is basically bolted to the frame (I think?)and the flexing of the frame absorbs the torque, but of course Teds not looking for less vibration and is why the front wheels leave the ground alot.
I do think I can get some new heims and rotate them. But it still seems like as you said the driveshaft/u-joint etc. could be just as weak, or become the weakest link, so the chase begins.
I have seen several birds with the steadies cracked, so I know this is a point of pressure, but I think I said earlier, You have to make sure they are kept adjusted. And a backup safety (chain) of some kind if you plan on racing regularly.
I know that when you completely remove the steadies, the engine can rock from side to side at least an inch either way. So the pivot is the front and back mounts. I also realize at this point that I may change my stock Mustang trans mount for a racing version to counteract some of this "roll".
I see how one might relocate the stock steady location to the top of the frame and weld on the mounts there. This would allow one to use shorter steady rods too.
If nothing gives, Then something may eventually break. Assuming the tires aren't spinning.
I appreciate the discussion. and thanks for all the help. I would like to incorporate some this and maybe we can all learn something, or at least me.
|
By pegleg - 16 Years Ago
|
Hoosier Hurricane (1/9/2009)
Don: That's a good one. Back in the earliest days of Hot Rod Magazine, one of the writers, trying to brag about a welder's skill, said he could "weld a glass rod to a toilet seat". Another story. When I was working in auto repair about 40 years ago, someone brought an exhaust manifold in with a twisted off stud. I drilled a pilot hole through the stud, then took my cutting torch and burned out the steel stud, leaving the cast iron intact. An old guy walked over and looked at the manifold, then said, "I'll be damned. First time I ever saw anyone cut threads with a torch". I never told him any differently. John I hear if you get real good at it, you can cut fine threads!
|
By GREENBIRD56 - 16 Years Ago
|
Charlie - I have an old orthographic style CAD system that I keep resident on my computer(s) - called "Cadkey". It's quick and doesn't smudge like my hand sketches do. When I have created a "picture" (lines in a white space) - I put that into "Paint" to add words, tint, whatever. Paint will let you save the drawing as a bit map until its done - then I save it as a JPEG (smudges the lines a bit) and transfer over into "Paintbucket" to use on the website. The ball of the rod end is (I believe) rated to carry a greater load than the pin bore (has much greater bearing area too). I would have to look it up in the Timken/Torrington literature. These "ball bushings" are used in machinery for a lot more than rod ends. The clevis adds several extra parts so we often just clamp the ball.....But pulling on the ball sideways is always verboten.
|
By glrbird - 16 Years Ago
|
Do you think you had to notch the frame because the trans adapter put the trans further back in the chassis. The adapter is about 1 1/2 thick right? I was thinking of a thinner steel adapter that would keep the trans closer to the front of the car and away from the X-member. I would have to make it of course, but it would eliminate the cutting of the frame which is harder to do with the body on.
|
By bird55 - 16 Years Ago
|
Gary, If you are up to the task of making the adapter, then dive in. But you will still need an appropriate flywheel, Hub Adapter and starter that engages properly. I have no issues with the Bendstens adapter as yet.
In answer to pushing the trans back, yes it does, about 1 1/2" like you said but trimming the x member is not difficult with the body on. I was dreading it but it actually turned out to be pretty simple. + you'll have need room around the rear of the trans for other linkage etc.
If you are nervous about sawing up your frame I was too. But the hurt goes away after you drive your bird with a 4 speed automatic, doing 75 mph at 1900 rpm. And besides if you do it right only an expert could see where it was altered.
|
By glrbird - 16 Years Ago
|
I was a Machinist in a previous life. After making the adapter,With the 59 flexplate and an a new gear drive starter to fit the 312, all I need to do is make a pilot bushing for the AOD converter and space the converter to make sure it is engaged in the transmission pump. I will probably have to some fitting for the starter in the trans bellhousing area. I could trim the Left side of the frame for the linkage if needed. Thanks for the photo journal, it is very helpfull. Thanks
|
By bird55 - 16 Years Ago
|
Sure, You sound like you know what you are doing, and should have no problems. Use a block and trans to mock up with and a front mount. You'll knoe exactly where everything falls for the rear trans mount. etc. One more thing to add I recomend a new Throttle pedal and linkage. See my blog for more. Gets rid of lots of linkage issues BUT certainly not stock looking.
Can we see your car? is it a 57?
|
By glrbird - 16 Years Ago
|
I have bought Lokar cable for the AOD and had planed to change the carb linkage, retighting the firewall screws gets old. I was trying to decide on whether to go with a later model cable style gas peddle or something else. I have been gathering parts for updated brakes, brake lines fuel lines suspension parts and freshen up the motor while the car is apart. I have got some heads I would like to try with a newer cam. The one that is in it now is 35 yr old Engle. I am going to try to get it all together and back on the road this year, but who knows. I will check out the Blog more this week. There is an old picture of the 57 in Texas profiles when the web site first started. Thanks
|
By MoonShadow - 16 Years Ago
|
I gave up and replaced the gas pedal with a Lokar unit. Works great and has tons of adjustments. Cable is clean and simple and the AOD TV cab;e was easy to adjust. Chuck in NH
|
By bird55 - 16 Years Ago
|
ok, Steve, It's pretty dang cold here and we were iced in all day so here is what I did. you get the credit.
Don Woodruff, you might take notice. thanks guys.
http://birddropnz.blogspot.com/
|
By Don Woodruff - 16 Years Ago
|
Alan: You do a heck of a job detailing your projects. Thanks so much.
|
By pcmenten - 16 Years Ago
|
Alan, you mention putting oversize valves in ECZ-C heads on the T-bird 312? What size valves did you install?
|
By bird55 - 16 Years Ago
|
Paul, That was eons ago, and I don't remember! But I still have 'em so I will try to go out and measure.
a few minutes go by…
Exhaust 1.509
Intake 1.780
The heads are ECZ-B, so not ideal, I think i might have said they were "C"? but it was what I had at the time chambers are deeper. But all the runners are smoothed up and port matched for the day.
|
By bird55 - 16 Years Ago
|
I just rechecked specs on those heads and 1.780 was stock for intakes?
These are 1956 312 heads 215 hp I believe. I don't know what the exhaust should be. These might actually be good to have reworked? With Lower compression? might make a decent blower head?
|
By pcmenten - 16 Years Ago
|
Alan, yes, that sounds like the stock valve sizes. I have ECZ-B heads that came off of a 56 292 Thunderbird Special in a Fairlane. Large chambers. They'll be good on a stroker motor because they do have a quench area.
I was asking about the -C heads because I'm about to do some work on a pair of -C heads for another 292. I'm thinking of using 1.84" valves.
Thanks.
|
By Hoosier Hurricane - 16 Years Ago
|
Don: That's a good one. Back in the earliest days of Hot Rod Magazine, one of the writers, trying to brag about a welder's skill, said he could "weld a glass rod to a toilet seat". Another story. When I was working in auto repair about 40 years ago, someone brought an exhaust manifold in with a twisted off stud. I drilled a pilot hole through the stud, then took my cutting torch and burned out the steel stud, leaving the cast iron intact. An old guy walked over and looked at the manifold, then said, "I'll be damned. First time I ever saw anyone cut threads with a torch". I never told him any differently. John
|
By charliemccraney - 16 Years Ago
|
Where does the stock steady rest mount?
|
By charliemccraney - 16 Years Ago
|
Clear as mud!
So the engine will be forced to pivot along the center-line of the front and rear mounts. The center-line of the crankshaft will be the approximate source of the force. The header mounted steady rest will be positioned farther from the fulcrum than the stock steady rest. Am I right in thinking that the header mounted rest will not have as much force acting on it?
Now let me really throw myself out there.
What is the installed orientation of the header steady rest? I'm figuring that the relation of the rods to the stand-off will be approximately 90 degrees. Given the length of the rods, the arc in which they travel will be more or less in a horizontal plane, which means that the spherical rod ends will be loaded mostly as designed. It seems like most of the force will be acting horizontally rather than vertically.
I think the best war to improve upon the design is to rotate the rod end 90 degrees and use a clevis so that all of the force will be transmitted as intended.
|
By charliemccraney - 16 Years Ago
|
Do you do these drawings on the fly, Steve? You have a drawing for everything! I'm suggesting the design on the left rather than the one on the right: 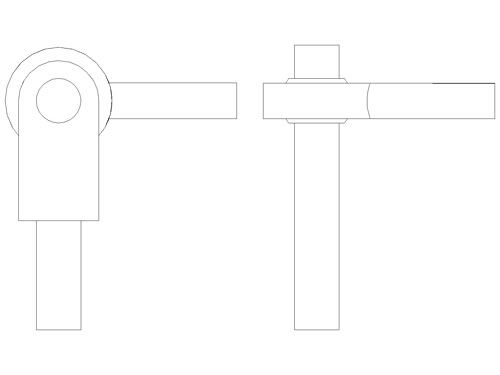
This way the rod end will be used just as designed. This, along with your improvement for the bending situation should maximize the strength of the steady rest.
|