By B-rad - Last Year
|
I understand that an engine should be pre lubed before the first start after a rebuild but if the mechanic that rebuilt the engine used whatever they use, some kind of grease on all the parts, wouldn't that be good enough? A friend of mine said that he has rebuilt a number of engines with the grease stuff and started them as is and never had an issue. It seems like a pain to do the pre lube if it's still greased up. But I don't want to waste 5k on a rebuild. Would pouring oil over the rockers and letting it drain down help some?
|
By charliemccraney - Last Year
|
There are multiple reasons to prelube. One is to ensure that the oil pump works and that the system can achieve adequate pressure. Another is to ensure that the filter and passages are full of oil so there is minimal delay in the supply of oil through the system. Yet another is to ensure that oil makes it all the way through the system, which is a reassurance that it is assembled correctly.
|
By Ted - Last Year
|
The length of time that an engine sits after being rebuilt before being started for the first time is also a player. Time is your enemy on a freshly built engine and any initial lube applied to the bearings and engine components can slowly disappear. As Charlie brings up, prelubing restores the initial lube as well as putting lube in places it was not originally applied. While engine oil or a very viscous lube is recommended for engine assembly purposes, the use of ‘white’ or lithium grease is typically considered detrimental for engine assembly purposes. Some reasons for not using ‘grease’ for the engine assembly components includes potential hydro locking or deformation of the bearings when they are torqued down, the inability of oil to flow past that grease during the initial startup, cold grease stopping up the oil filter until the engine warms up, and the grease actually drying out and getting crusty if it sits for too long before the engine is cranked up. Here are some pictures of commercially available engine bearing assembly lubes. Keep in mind that the lube used for flat tappet camshafts differs significantly from the lube used on engine bearings.
|
By B-rad - Last Year
|
Is like to hook up an oil pressure gauge while I'm spinning the oil pump to ensure I'm getting proper pressure. Where do I attach the gauge? The engine is out of the car.
|
By paul2748 - Last Year
|
Any of the plugs that are on the side oil line. You don't have to spin the whole engine over. Spinning the oil pump by the pump drive located in the hole for the distributor will do very nicely.. I even do it by hand but this won't give you an indication of pressure, just that you are getting oil all the way up. Use a drill to rotate the drive for that. Make sure you spin counter-clock wise
B-rad (10/6/2024)
Is like to hook up an oil pressure gauge while I'm spinning the oil pump to ensure I'm getting proper pressure. Where do I attach the gauge? The engine is out of the car.
|
By B-rad - Last Year
|
I'm not sure if understand . The side oil line. Plugs? Do you mean spark plugs? I tried to spin the oil pump shaft from under the dizzy but wasn't sure i was engaging the shaft with the socket on the extension. I spun it ccw with a drill for a couple of minutes but didn't see any oil coming up to the heads. I used a cheap cordless drill, maybe it didn't have enough power to spin fast enough.
|
By Ted - Last Year
|
B-rad (10/6/2024) I'm not sure if I understand . The side oil line. Plugs? Do you mean spark plugs? I tried to spin the oil pump shaft from under the dizzy but wasn't sure i was engaging the shaft with the socket on the extension. I spun it ccw with a drill for a couple of minutes but didn't see any oil coming up to the heads. I used a cheap cordless drill, maybe it didn't have enough power to spin fast enough. Any of the ¼” NPT oil galley plugs on the filter side of the engine will work for an oil pressure gauge hookup. There is a ¼” NPT hole on each side of the block for a coolant drain but it will be in a different ‘line’ than the oil galley plugs. I prelube the engines using a speed handle and starting with an empty filter it takes ~20 seconds to get pressure at the oil galleys. It then takes roughly another 20-30 seconds to get a flow up to both rocker arm assemblies. This is with a speed handle which is lucky if I’m getting 300 rpm at the pump. If the oil pump was not prelubed during the engine assembly, then the oil pump may have a hard time getting the oil flow started. A leaking rubber seal at the oil pump inlet can also prevent a speedy pickup of the oil.
|
By B-rad - Last Year
|
I see that the oil pump shaft is not centered in the hole in the block. That's why I'm not sure the socket is turning the shaft, it might be spinning on top of the shaft. Is there a trick to keep the shaft centered while putting the socket in the hole? Plus it'll help putting the dizzy back in.
|
By KULTULZ - Last Year
|
Ted wrote -
I prelube the engines using a speed handle and starting with an empty filter it takes ~20 seconds to get pressure at the oil galleys. It then takes roughly another 20-30 seconds to get a flow up to both rocker arm assemblies.
Interesting. Why a dry filter and not an electric drill (will be my newly learned FACTOID of THE DAY).
Regarding the oil pressure gauge, use the oil pressure sender port. This is a LYB.
|
By paul2748 - Last Year
|
I use a 1/4 drive deep socket on an extension with speed wrench (3/8 with an 1/4-3/8 drive adapter) to make sure the socket connects with the oil pump shaft/drive. An ordinary length socket may not reach the oil pump drive.. Usually, the socket will just go over the drive - never had a problem with centering (except when putting in the distributor).
B-rad (10/7/2024)
I see that the oil pump shaft is not centered in the hole in the block. That's why I'm not sure the socket is turning the shaft, it might be spinning on top of the shaft. Is there a trick to keep the shaft centered while putting the socket in the hole? Plus it'll help putting the dizzy back in.
|
By Ted - Last Year
|
KULTULZ (10/7/2024) ...Interesting. Why a dry filter and not an electric drill (will be my newly learned FACTOID of THE DAY). There’s no mess or spillage when installing the filter when it’s empty. I do prefer priming by hand with a speed handle rather than a drill as if there is problem with the oil pump meshing smoothly, you will feel it with the speed handle but not if you have a drill motor turning the pump. A case in point is a BBC engine that was being primed by hand prior to being installed on the dyno and it had an obvious tight spot when rotating the pump. Upon removing the oil pump, its housing had been heat warped when the customer brazed his oil pickup to the pump. That would not have been found if using a drill motor to turn the pump.
B-rad (10/7/2024) I see that the oil pump shaft is not centered in the hole in the block. That's why I'm not sure the socket is turning the shaft, it might be spinning on top of the shaft. Is there a trick to keep the shaft centered while putting the socket in the hole? Plus, it'll help putting the dizzy back in. Without a distributor lower shaft in the distributor pilot hole, it’s normal for the oil drive shaft to be lying to one side of the hole. Between the point or chamfer on the top of the oil pump drive shaft and the corresponding counter bore in the bottom of the distributor shaft, the two parts manage to align once the six sides of both the shaft and the distributor hole are aligned. For priming the oil system before an engines’ first start, I’ll use an old distributor that has the lower gear removed and a bolt welded to the top. With this, I can use a speed handle with the appropriate socket to turn the oil pump CCW for prelubing purposes. As mentioned earlier, it takes approximately 20 seconds to fill an empty oil filter and get a pressure reading on a gauge. Another 20-30 seconds will typically have oil at the rocker arms. Here's a picture of a distributor modified for oil priming purposes.
|
By KULTULZ - Last Year
|
"There’s no mess or spillage when installing the filter when it’s empty. I do prefer priming by hand with a speed handle rather than a drill as if there is problem with the oil pump meshing smoothly, you will feel it with the speed handle but not if you have a drill motor turning the pump."
... hmmpf ...
I never though of the pump binding.
APPRECIATED!, and this my LEARNED FACTOID of THE DAY.
Always something to learn here.
|
By B-rad - Last Year
|
I must've had a brain fart.
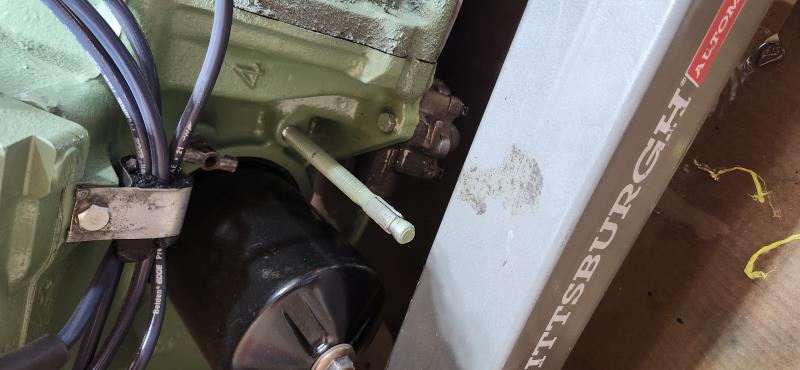 Found out that I had somehow put a bigger size socket on the extension so I was just spinning on top of the oil shaft. Put the correct size socket on and started spinning the oil pump. Soon after, I saw oil coming from a hole next to the oil filter. I'm sharing a picture of a long threaded rod i put in to stop the leak. The manual doesn't show what piece belongs there. Help please.
|
By Ted - Last Year
|
On the Ford Y, you will find the sending unit for the oil pressure light typically in that particular hole from the factory. I suspect the same was for the Lincoln Y or LYB engines. If you are getting your oil pressure reading from a different oil galley hole in the block, then a simple ¼” NPT plug in that particular hole will fix you up. Otherwise, hook up your oil light sending unit or an oil pressure gauge in that hole.
|
By B-rad - Last Year
|
Is this the sending unit? Is there an easy way to test it while it's outta the car?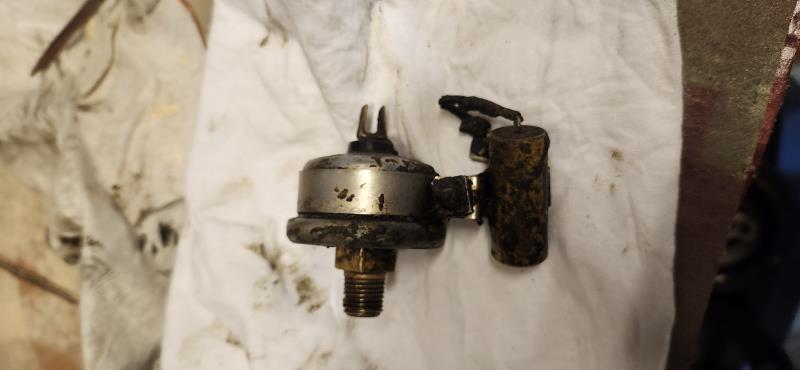
|
By Ted - Last Year
|
If it’s for a light, just check it with an ohm meter for continuity. If it’s for an oil pressure gauge, just check that there is some kind of ohm reading. Beyond that, just install it, hook up the wire, crank the engine, and see if you get a reading assuming it’s for a gauge.
|
By B-rad - Last Year
|
Is this the oil pressure sending unit? It seems to be just a tad too big to fit in the hole. And that's that thing attached to it for?
|
By alanfreeman - Last Year
|
Yes, that is the sending unit for the oil pressure gauge in the dash. The device attached to the sender is a condenser.
|
By B-rad - Last Year
|
What's the condenser first? What foes it hook up to?
|
By Ted - Last Year
|
B-rad (10/10/2024) What's the condenser for? What does it hook up to? My thought is to hook up the gauge wire to the sending unit first without the condenser. If the gauge reading is inconsistent or fluctuates, then hook up the condenser. There are two terminals on the sending unit and I suspect one of them was for the condenser.
|
By B-rad - Last Year
|
Ok. So the threads were screwed up on the sending unit. I tried to fix and rethread but only made it worse. Anyone know if there are other units that will work on this 317 lyb? It has a 1/2" npt thread. Or can I use an adapter for a unit with a 1/8" thread to get it to fit into the half inch hole?
|
By Ted - Last Year
|
½” NPT sounds too big for an oil sending unit hole in the block. I do not have a LYB block sitting here to look at, but I would think the threaded oil pressure hole on the LYB would be ¼” NPT like those on the Ford Y. As a FYI, a NPT hole is not measured across the top of the threaded hole but rather on the size of the hole within the pipe that goes into that threaded hole. A ¼” NPT hole will be approximately ½” as measured across the top of the hole.
|
By B-rad - Last Year
|
I've seen a lot of sending units with 1/8" threads, unless that's the electrical connection size. I assume all units are basically the same and as long as it screws into the block it should work. Am I correct? If so, I have options without having to find an elusive lyb part. And is an adapter a viable solution if the sizes are different?
|
By KULTULZ - Last Year
|
This seems to be what is in it now - 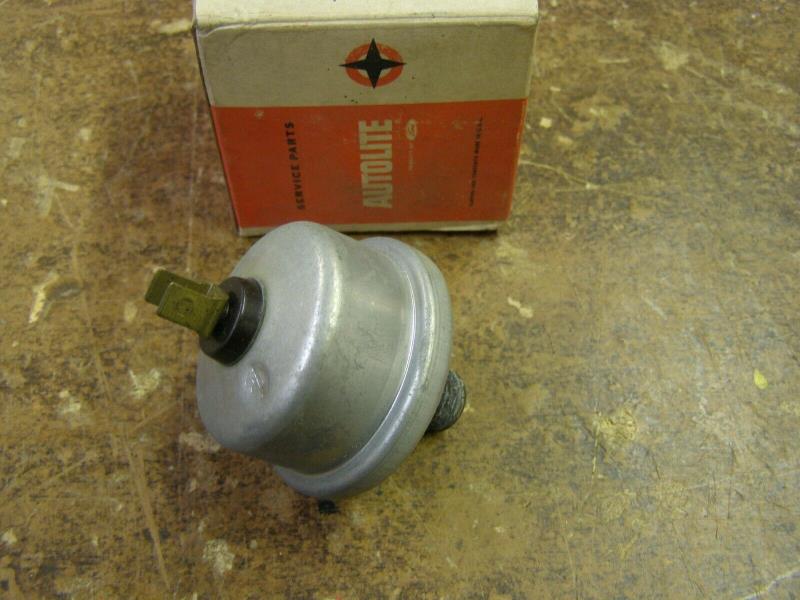 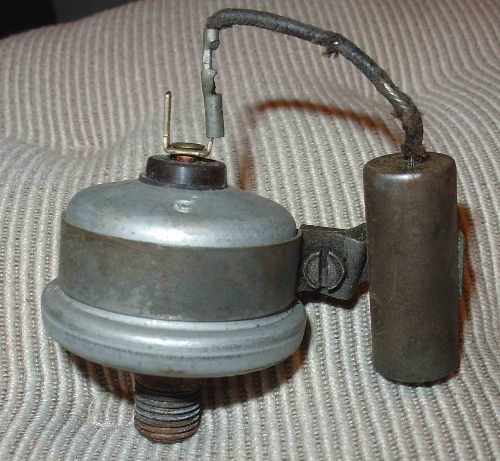 Where the terminal is attached to the sender body, is there a retaining screw or a rivet? The purpose of the condenser should be explained in the WSM.
|
By B-rad - Last Year
|
Just like it but mine has a rivet. Does that make a difference?
|
By B-rad - Last Year
|
Is that one for sale?
|
By B-rad - Last Year
|
I'm seeing a lot of sendors online that say thread 1/8 npt. Anyone know what that is referring to? It can't be 1/8". Pictures show what looks to be a similar size to the lincoln one. Just trying to find a suitable replacement
|
By miker - Last Year
|
The sensor you have is almost certainly 1/8” NPT. Most oil pretty switches are. If it’s a light, it’s a switch. If it’s a gauge, it’s more sensitive. Most old cars would have either a mechanical oil pressure or just a light. I’m guessing yours is a light. Those operate at 5-10lbs pressure in my experience.
So if you measure the outside diameter, and it .4, just under 1/2”, it’s 1/8” NPT.
Picked up from the internet.
“The dimensions for a 1/8 inch National Pipe Thread (NPT) are: Outside diameter: 0.405 in Handtight engagement: 0.1615 in NPT threads are tapered, so the nominal diameter is the diameter in the middle of the threaded portion. The outside diameter of an NPT fitting is usually about 1/4 in larger than the fitting's name. “
|
By B-rad - Last Year
|
So would another sensor work on my car, if it's designed for a gauge, since that's what's in my car? If the threads are the tight size? Oh, BTW, Hi Mike And will a regular tap and die work on npt? That's what I used to try to fix the threads.
|
By miker - Last Year
|
Trying to retap a nipple that short can be a challenge, and I don’t know if they make a thread “chaser” for those.
Yes, if it’s a gauge, likely it’s pretty special. If you can’t find one, try the instrument repair guys. Also, I don’t know what Lincoln used, but Ford used the King Seeley gauges. I’ve had some luck looking on the Jeep Willy’s sites for info on those. Maybe one of the Lincoln guys will chime in.
I see you guys are at least in the low 90’s, when Tucson cools off I’ll come back.
|
By KULTULZ - Last Year
|
You have a 1954 LINC - 317CI.
Does it have an oil pressure gauge or lamp?
|
By B-rad - Last Year
|
Gauge
|
By B-rad - Last Year
|
I looked at the threads and they just needed a little filing. It went right into the block. Golden. It's gonna be a pain trying to get a wrench on it with the filter and oil pump right there.
|
By miker - Last Year
|
If the filing was just to get it started, the threads that seal it are probably fine. Tapered pipe threads, tight, but don’t over do it. Better to tighten it a bit later than Armstrong it and strip something.
I’m glad you’re getting close.
For the rest of the site, my wife and I had the pleasure of having lunch with Brad and his wife, and being invited to see the Lincoln. There’s some work to be done, but it’s all pretty much complete and a heavily optioned car. It’ll be a jewel when it’s done.
|
By B-rad - Last Year
|
Thanks Mike, it was nice meeting you two too. And now I can turn the oil pump and hopefully see oil up in the rockers. Without any more leaks. That'll be a big relief knowing that part of the rebuild was done right. Then in the bay it'll go. It'll be a long journey from there, paint, interior, all the accessories. Rewiring, converting to 12v, power windows, seats. Changing out the treacle brakes for a two line p brake mc. Basically the front suspension and 4 wheels brakes rebuilt, tank and fuel line redone, are all I've gotten done besides getting the engine and tranny rebuilt. The pic is for those that haven't seen it yet.
|
By KULTULZ - Last Year
|
B-rad (10/12/2024)
Just like it but mine has a rivet. Does that make a difference? 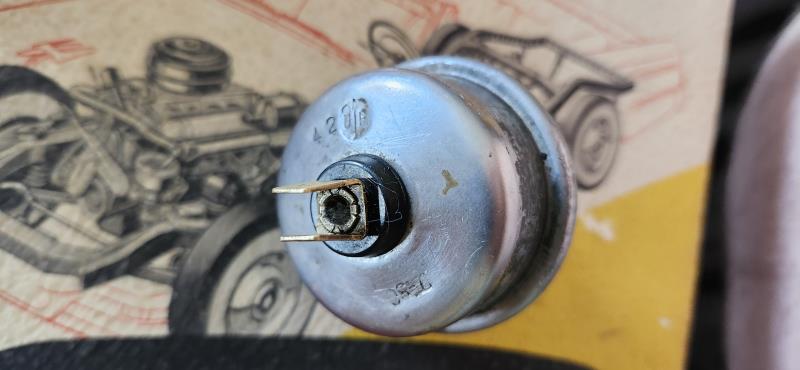 Herein lies the problem - The sender you removed, if OEM and not aftermarket, appears as a 1956/ sender which is for a 12V SYSTEM. The prior 6V sender appeared as - There was available a 2PIN TAB to attach to the 6V sender to convert it for this particular application.
It may have been installed years ago when the supposedly correct sending switch was not available.
As for the condenser, is there any stamped identification on the bottom of the cylinder?
|
By KULTULZ - Last Year
|
I looked at the threads and they just needed a little filing. It went right into the block. Golden. It's gonna be a pain trying to get a wrench on it with the filter and oil pump right there.
Remove the filter so you can get to it easily.
Most likely, FORD offered a SPECIAL SERVICE TOOL (bent crows-foot) to get at it while in the chassis. If there was one, it will be shown in the WSM.
|
By B-rad - Last Year
|
|
By B-rad - Last Year
|
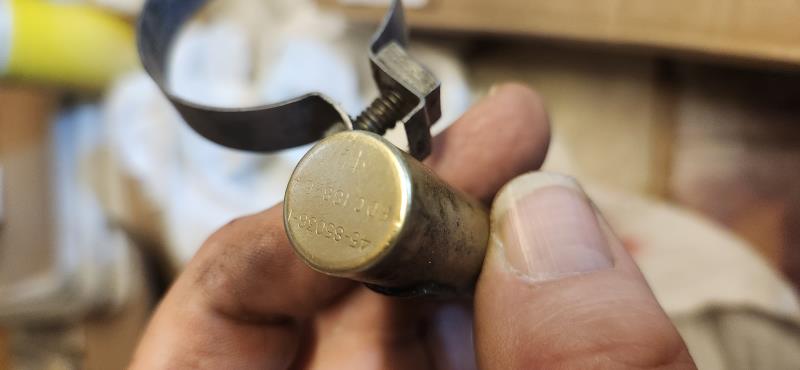 I think it says 45-85036-1 FDC 108701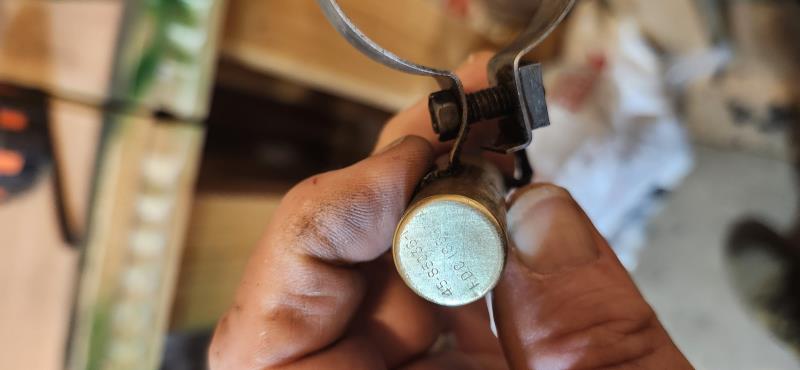
|
By KULTULZ - Last Year
|
THANX! for posting the nos.
I cannot cross it over. It is an ENGINEERING PN. Need a FORD PN INTERCHANGE MANUAL and I do not have one.
Sill wondering why a suppressor on the circuit.
|
By alanfreeman - Last Year
|
Maybe the condenser was to avoid radio interference???
|
By KULTULZ - Last Year
|
alanfreeman (10/14/2024)
Maybe the condenser was to avoid radio interference??? Correct, but it will usually be in either the ignition and/or charging system.
|
By FORD DEARBORN - Last Year
|
That particular oil pressure sender has a contact on a bimetal strip with a fine wire wound around it. That design was used through '55 and possibly '56. As oil pressure increased, a diaphragm increased force on the contact which caused an increase in current thus further heating the bimetal strip enough to cause the contact to open/close again. The same current flowed through the bimetal device in the gauge which moved the pointer accordantly. As stated above, condensers were used as noise filters on ignition and charging systems that had operating contacts also. AM radios picked up a lot of electrical noise in those days. I'm not sure at this time, but those noise suppressor caps had a similar value as an ignition cap. I'll see if I can find that information.
|
By miker - Last Year
|
Ford Dearborn, if I’m reading that correctly, Lincoln also used the King Seeley gauges?
|
By FORD DEARBORN - Last Year
|
IF King Seeley is the contact/heater device in the sender then I would say yes. I know the big change was in 1957 but even the 56 Lincoln car used the contact/heater method in the fuel sender. I would think that when 12 volts came about in 56 the senders were probably calibrated differently. This method was also used in the trucks, at least according to my 54/55 truck WSM so it must have been a Ford instrumentation design across the board until 1957. In '57, a voltage regulator for the instruments was incorporated putting stability into the system and simplifying components. This is just my understanding of the subject so hopefully others may have additional information to add.
|
By miker - Last Year
|
This link is to a very old post about the King Seeley’s. Some of the drawings seem to have been lost to time, and there was a more extensive post on adjustments I’ve never been able to track down. Appreciate Ford “bought out” these gauges, and when I was looking for them the most active sites where Jeep/Willy’s for info and rebuilders
http://forums.y-blocksforever.com/Topic22135-1.aspx
|
By retromod56 - Last Year
|
I faced the same issue, and wanted to pre oil my new stroker EVERY time it was started (once monthly about) so I bought a pre-oiling system from a company called Masterlube. Basically, its tank, with Schrader valve. Add oil, pressurize (depends on application) mine is at 60lbs. (has guage to check fill and pressure drop. solenoid controlled by toggle switch on dash sends about 40lbs oil pressure to engine before startup. BEST thing I ever bought for this long term project. Permanently attached to radiator support. Its a little bulky/unsightly for some, but my expensive build has never had a dry start.
|
By 55blacktie - Last Year
|
I would like to see it. Price?
|