By 55blacktie - 2 Years Ago
|
How often is it necessary to mill rocker stands to accommodate high-lift cams? My net valve lift will be .485.
|
By charliemccraney - 2 Years Ago
|
It is not patently necessary. Milling (or shimming) is used to correct geometry, which has many benefits but it is not a necessity for most cases. There may be extremes where it becomes necessary. I'll let others who may know expand on that.
Assuming that geometry starts in an ideal configuration, any subsequent change to the valvetrain will require an adjustment be made, whether that is milling stands or shimming stands in order to return it to an ideal configuration. Items that affect geometry are pushrod length, rocker ratio, rocker tip style, cam lift, valve stem length, depth of valve at the seat, lash caps (not common), probably others I'm forgetting.
If using roller rockers, I think you will most likely need to shim the stands. It may be possible that with factory style rockers milling is required. You do need to check before you do either. Exactly how much adjustment is required is something that has to be determined on a case-by-case basis.
The bottom line is if you want the geometry to be correct, shimming or milling will be required.
|
By Joe-JDC - 2 Years Ago
|
Several things needed to be addressed before moving the rocker stands. Was the block decked? How much? Were the heads milled? How much? New camshaft? New lifters? New pushrods? New rocker arms, or different rocker arm ratio? Valves replaced? Stock or longer valves? Valve job completed after all machine work on block and heads? Typically milling the heads, decking the block and new longer stem valves will require adding shims, not milling the stands. I had to add a 3/16" steel shim on my iron heads after all the above work was accomplished to get the rocker arm centered on the valve stem tip at mid lift. Joe-JDC
|
By 55blacktie - 2 Years Ago
|
Thanks, Joe. In my case, it's theoretical until the engine is assembled with rocker assemblies installed. After reading Ted's article, I thought that more valve lift would require milling the stands, not adding shims. Are the shims readily available? I will hold off on pressurizing the rocker arms until I know for certain.
|
By charliemccraney - 2 Years Ago
|
A lot of factors affect geometry, with lift being one of them.
For mine, I needed a shim just under 1/4" thick. I'm not aware of any readily available shims. I did use arbor shims to help determine the thickness needed but made shims out of a piece of 1/4" thick aluminum strip, 3/4" wide.
|
By DANIEL TINDER - 2 Years Ago
|
The early OEM Y-Block stand oil trays I have are around .043”, if that’s any help. If your target measurement is in the ballpark, finding a used set would likely simplify things (?).
|
By 55blacktie - 2 Years Ago
|
I have the oil tray baffles from my 55 heads. I will determine rocker arm geometry on 57 G heads with & without baffles to see which is better. Thanks, Daniel.
|
By 2721955meteor - 2 Years Ago
|
if you are using new style head gaskets(like I did) I did not use the metal spacers that wher suppose to direct oil.when I measured new style head gaskets the increased thickness and the thickness of the plates ,returned the rocker geometry back to stock I would recommend 302 valve seales,but trim them so they are a bit shorter ,not as short as corect seals for y blocks I have found supper lube going to all valve train as well as plenty of drainage back to pan both ends. my own truck with 292 y never had to change rockers to valve stem adjustment as whole valve train gets proper lubrecation
have only rebuilt 4ys the last4 years but no complaints from any one
|
By charliemccraney - 2 Years Ago
|
Joe-JDC (11/18/2023)
Typically milling the heads, decking the block ... will require adding shims, not milling the stands.
I would expect those changes to require pushrod length be altered but not require any significant change to stand positioning. Since the Y uses shaft mounted rockers, the relation of the rocker to the valve stays the same no matter how much is removed from deck surfaces.
|
By 2721955meteor - 2 Years Ago
|
have you measured the latest head gaskets,in my case the thicker gaskets wher the same thickness as the trays.so with trays removed should be a time to check other changes (re surfacing heads and block). also be careful with the head cap screws. the picture of ones being used(in 1 picture spells trouble
|
By Ted - 2 Years Ago
|
To reiterate what Charlie mentions, changes to the head gasket thickness and any milling of the decks and/or heads will not have a bearing on the valve train rocker arm geometry on engines that use shaft mounted rockers. You can install 1” thick head gaskets and the valve train geometry will basically go unchanged. Granted the pushrod length will be affected but the actual geometry will not. Valve lift and the valve stem lengths, if changed, will affect the geometry though as the rocker arm pivot point in relation to the valve stem tip and rocker sweep is then being altered. I have found that biassing the rocker arm geometry to the high side is advantageous to low lift air flow but that will be at some expense to valve guide wear and/or longevity.
|
By DANIEL TINDER - 2 Years Ago
|
“The High Side” (?). Does that that mean longer valve stems, or longer pushrods? (sorry if I’m a bit slow on the uptake).
|
By 55blacktie - 2 Years Ago
|
Shimming stands?
|
By charliemccraney - 2 Years Ago
|
DANIEL TINDER (11/20/2023)
“The High Side” (?). Does that that mean longer valve stems, or longer pushrods? (sorry if I’m a bit slow on the uptake).
That means to err on the side of having the stand positioned slightly higher than ideal.
|
By charliemccraney - 2 Years Ago
|
If the stands need to be higher, you need to shim them. Here is an example of shins i have made.
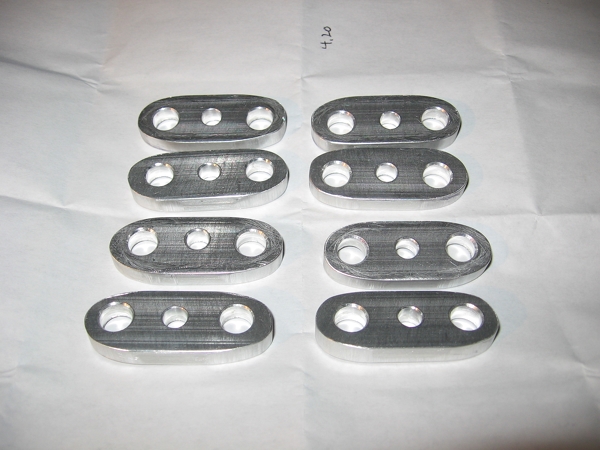
|
By KULTULZ - 2 Years Ago
|
... i wish i would learn to keep my big mouth shut ...
Either TED or JOHN should have a TECH ARTICLE written on PROPER VALVE-TRAIN GEOMETRY and how to get there.
You would start (IMO) with adj. checking push-rod(s) to find proper rocker arm/valve stem contact/sweep and go from there wouldn't you?
I have always wondered why FYB push-rod length(s) differences (between model years) was never really discussed, especially between differing rocker arm ratios.
|
By paul2748 - 2 Years Ago
|
Ted did an article on this subject some time ago. I do not have a reference to it.
|
By 55blacktie - 2 Years Ago
|
Nice job on the shims, Charlie, but they look a bit thick. Have you made others?
|
By charliemccraney - 2 Years Ago
|
Here's a link to Ted's article
https://www.eatonbalancing.com/2007/12/10/rocker-arm-geometry/
When I did mine, I also came across a technique that I think is called mid-lift. I can't find the article now. That method states that at mid lift, if you drew an imaginary line from the valve tip (or roller axis for roller tipped rocker arms) to the center of the shaft, that line should form a 90° angle with the valve centerline. It makes sense as that would ensure that rocker tip travel across the valve tip is minimal. As such, I set the valve at mid lift (cam lift x rocker ratio - lash) / 2 and was able to make a rough measurement of how much the stand height would have to change in order to achieve that 90° angle. If you took very careful measurements, you can probably calculate it exactly. That gave me a god starting point.
A checking pushrod is advised for this simply because the required pushrod length will change with a change in stand height and the rocker ratio changes as the depth of the lash adjusting screw is changed. The checking pushrod allows you to keep the adjuster screw locked down so that the variables can be kept to a minimum. It also helps you figure out the length of pushrod you need to order once the geometry is where you want it.
|
By charliemccraney - 2 Years Ago
|
55blacktie (11/20/2023)
Nice job on the shims, Charlie, but they look a bit thick. Have you made others?
They are as thick as necessary. Required thickness will vary from one build to another. I have made others. Here's the easiest way I've found to make them without a machine shop. 3/4" wide strip and a lot of care a patience with a belt sander although if the required dimension is significantly different than standard metal thicknesses, i suggest a machine shop.
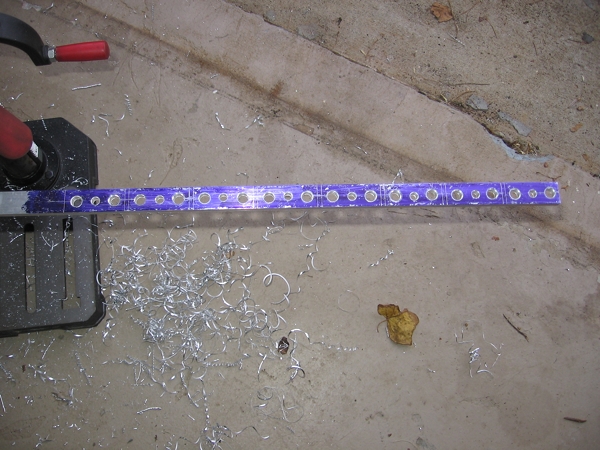
|
By Joe-JDC - 2 Years Ago
|
Here is how Ted and I solved the problem on the 2018 303Y for EMC. Iron head rule, 1.6 Harland Sharp roller rocker arms, Smith Brothers push rods, etc. Joe-JDC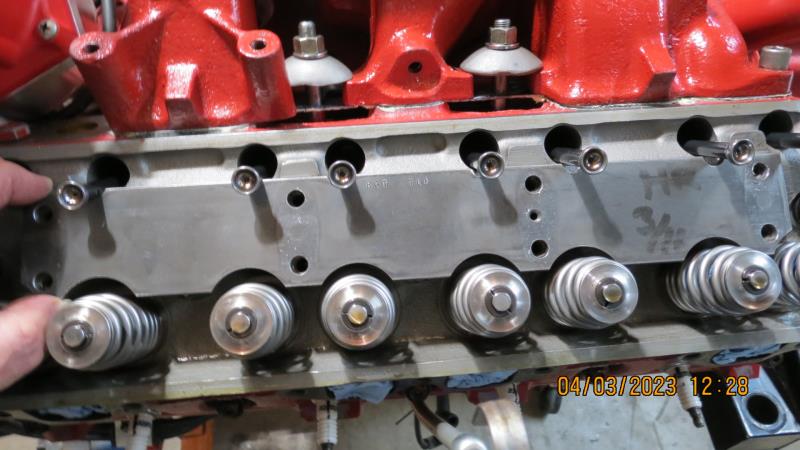
|
By KULTULZ - 2 Years Ago
|
charliemccraney (11/20/2023)
Here's a link to Ted's article ... There 'ya go. Just like PREGO, it's in there.
|
By DANIEL TINDER - 2 Years Ago
|
charliemccraney (11/20/2023)
DANIEL TINDER (11/20/2023)
“The High Side” (?). Does that that mean longer valve stems, or longer pushrods? (sorry if I’m a bit slow on the uptake). That means to err on the side of having the stand positioned slightly higher than ideal.
Right. I was confusing ‘rocker’ geometry with ‘adjuster-ball/PR-cup’ geometry. Mostly a wear, rather than performance issue (?).
|
By charliemccraney - 2 Years Ago
|
Rocker geometry is both a wear issue and performance issue. Poor geometry increases wear and decreases lift.
|
By DANIEL TINDER - 2 Years Ago
|
Funny how the mind plays tricks. My comment was based on a memory re: a (supposed) tech article from years back that dealt with increased adj. ball/cup wear due to setting the adjuster/PR length for max. rocker ratio, but a thorough search of all my accumulated literature proved fruitless. So, must be a figment of my imagination. Search did point out though how complicated are the complex myriad of factors involved re: the compromises between perfect geometry/min. wear, and power range (as Ted’s single comment re: sacrificing guide wear demonstrates). BTW: Re: the OP’s original question: I noticed a tech comment (while searching) that stated increasing cam lift typically requires milling (not shimming) the stands (likely in relation to otherwise OEM setup).
|