By B-rad - 2 Years Ago
|
I finally got my 317 back from the shop. It's got new pistons, bored out .030 over, new cam bearings, rod bearings and mains. He was so reasonably priced that I had him put new exhaust valve seats, pushrods and hydraulic lifters. Oil pump put on along with pan, pick up and oil tubes. He cleaned up rockers and checked everything out, replacing whatever was needed, and which wasn't much. A seal here or there. He put the heads back on and adjusted everything. Only charged me a little over 2 grand, labor only. Now the reason for this post. My wife bought me a new 1.5 ton engine stand with a front bar about 18" long with casters on the ends. My hoist has the two angled legs. Unfortunately the stand won't fit between the hoist legs. Just thinking about it now, I'll try putting the stand on the side of the legs maybe it'll reach. The other problem is the bolt pattern on the engine doesn't allow the stand to line up with them. There are two on top, two on the sides and two way down on the corners. The bottom ones are too far out for the stand bracket to reach and the two top ones are too close to use along with the two side ones. Just can't figure this out. Never used a stand before but have watched a few videos. I'm sure I'm not the only one experiencing these issues.
|
By Tealy64 - 2 Years Ago
|
Does your stand not have adjustable arms that will mount on the rear of the engine (where the bell-housing bolts on)? It took a little fiddling (and a bolt kit from Summit Racing (https://www.summitracing.com/parts/SUM-G1012 ) but we managed to get it on the stand. We've just got one of the stands from Harbor freight and it hold the 292 no problem.
Good luck and be careful. The last thing you want to do is drop that shiny new engine!
|
By B-rad - 2 Years Ago
|
It does have the adjustable arms but the way the holes are spaced I can't seem to be able to get 4 bolts lined up. I'll get a vid or some pics tomorrow. Maybe after some sleep I'll be able to figure it out. Still trying to figure out how to get the stand close enough to the engine since the hoist legs are in the way.
|
By miker - 2 Years Ago
|
Couple pictures would help. I’ve had similar problems, especially with the engine stands. Sometimes, if the arms are different lengths you can swap them around until you find a combination that fits. Be careful, those are big heavy engines, and I’ve had trouble getting them close to balancing making it dangerous to turn them over. Or a 3 man job to be safe.
I was lucky, most of the time I had a sliding overhead hoist, I beams on structure, all chain, good for 10 times what an engine would weigh. But it still scared me and made me very careful.
|
By Florida_Phil - 2 Years Ago
|
Don't try to mount the engine on the stand with the rotating mounting fixture and the stand as a unit. The Y-Block has a wide bolt bell housing pattern. Remove the fixture from the stand. Loosen the adjustable arms and mount the fixture on the rear of the block. Lift the engine and put the fixture in the hole in the stand. Here's a couple of photos from my shop. Be careful putting that engine in the car. The young guy in these photos is my friend Joe. Old guys like me shouldn't do this by themselves.
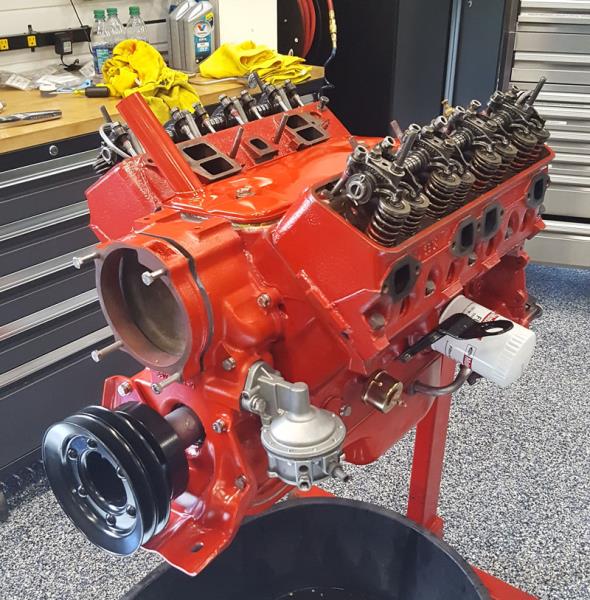
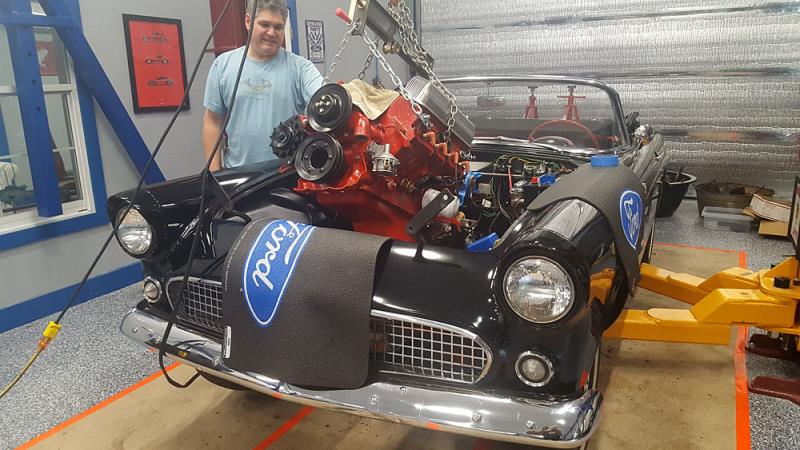
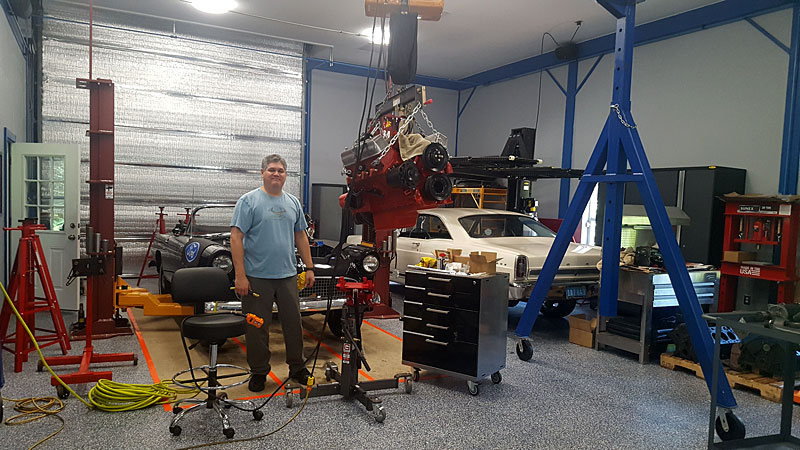
|
By Ted - 2 Years Ago
|
Depending upon the brand or style of engine stand, I find it necessary to drill some extra holes in the attachment arms to get the engine stand heads to bolt up to the blocks. I like the camshaft hole to be close to the pivot point thus making the engine easier to rotate and/or not have a heavy side when rotating the engine with the cylinder heads on. Here are some pics.
|
By DANIEL TINDER - 2 Years Ago
|
Ted (1/18/2023)I like the camshaft hole to be close to the pivot point thus making the engine easier to rotate and/or not have a heavy side when rotating the engine with the cylinder heads on. Here are some pics.
Wish I had thought of that. Working on the motor in my basement, I had to drill the steel ceiling I-beam and attach a chain hoist in order the rotate the engine on the stand after I had installed the iron heads.
|
By B-rad - 2 Years Ago
|
Thanks for the info. I'll be drilling some holes in the arms. Now can someone advise me on the problem I'm having regarding the hoist legs getting in the way of the stand front support?
|
By Joe-JDC - 2 Years Ago
|
Take the front castors off the engine stand, move the hoist over the front and lift the engine off the engine stand. May have to go in at an angle and straighten out the lift. Does your lift have an extension that moves it out further? My engine stand has three positions on the lift arm to extend the reach. Joe-JDC
|
By B-rad - 2 Years Ago
|
It does extend our, 3 settings. It's out as far as it can go. I suppose it might work, taking the casters off the end of the hoist legs and put the front support of the stand up on top of the hoist legs. Then slide the stand back off the hoist legs. Then it'll be fun putting the engine back on the hoist to install it back into the car
|
By Joe-JDC - 2 Years Ago
|
I guess you could always install a castor in the center of the engine stand leg, and cut off the extensions making it a tripod stand, or move the castors in a few inches and cut off the ends to make it narrower. Joe-JDC
|
By paul2748 - 2 Years Ago
|
Can you attach a chain to something on the ceiling that will hold the weight while you make the transfer
|
By B-rad - 2 Years Ago
|
Nah. It's in a pretty cheap one car garage. Not heavy duty built. I'll figure out some kind of ramp or some way to get one over the other and remaining safe. Still open to ideas. I did get the holes drilled in the adjustable arms allowing me to get it lined up. I'm wondering if I can somehow use a floor jack to hold the engine and move the hoist out of the way then bring in the stand.
|
By MoonShadow - 2 Years Ago
|
Jack up the front of the car and put it on stands. I do that for my 56 Victoria and it helps. With pulling or setting the engine in place and maneuvering the engine hoist. I lower the engine near the floor to pull the transmission and lift it to the stand. That adjustable engine lift is really a must have. At my age it makes it easier when its a one man job. The legs on the engine hoist need to be out as far as possible to support the engine weight without tipping. The longer the better. Oh and never ever work under the engine while its up on the hoist that engine is heavy! When I've done odd engines I put the stand head onto the engine and then into the stand. You can even lift the stand up to get it to slide onto the head assembly.
|
By B-rad - 2 Years Ago
|
Yeah moon shadow, the engine is out of the car on the hoist. The issue, as stated before, is the width of the hoist legs and the width of the engine stand front support. With the extendable arm on the hoist all the way out, the stand still can't go between the hoist legs. It's about 6-12" away
|
By Ted - 2 Years Ago
|
B-rad (1/18/2023) .....Now can someone advise me on the problem I'm having regarding the hoist legs getting in the way of the stand front support? Without a picture of your hoist, I’m thinking that the engine stand needs to go into the hoist opening by starting one front leg or wheel of the stand going in sideways to the hoist. Then move the stand into the hoist opening while also turning the front of the stand simultaneously so that the other front wheel of the engine stand goes in between the hoist legs. When done, this should have the engine stand sitting square within the hoist legs if I picture this correctly. I hope that made sense.
|
By B-rad - 2 Years Ago
|
Actually Ted, the hoist legs are in a big vee shape open at the end where the stand needs to roll in. But the width at the end is about the same width as the front support of the stand so the stand can't go in much before it hits the hoist legs. I'll be posting some pics in a little while. I did get the stand head to bolt up to the engine by drilling holes in the adjustable arms to shorten them.
|
By B-rad - 2 Years Ago
|
Here are some pics of the issue. I did turn it in on an angle but still have a 3-4" gap between the stand and head
|
By paul2748 - 2 Years Ago
|
Put the long leg of the stand on top of one of the legs of the hoist to get it nearer. Then slide the stand off the leg of the hoist ??. Or put the front piece of the stand on top of the leg of the hoist, use wood to keep the other end of the front piece to keep the stand even.
|
By Joe-JDC - 2 Years Ago
|
Like I mentioned above, move those two front castors inboard and cut that front shorter. The stand will still be stable with those front castors half the distance they are now. Joe-JDC
|
By Richard - 2 Years Ago
|
I’ve had this problem. The bracket on the engine looks good, just make sure the round mounting tube ends up so the engine angled up, not down. Jack up host and mount engine stand so the whole is airborne. Put the locating pin in. Since it’s all in the air you can slowly lower it maneuvering it to a safe landing. It’s good to have another person to maneuver the engine and one lowering the host. Good luck
|
By B-rad - 2 Years Ago
|
Great idea Richard. I'll be trying that later
|
By MoonShadow - 2 Years Ago
|
The stand you are using is more stable but the long front legs are the problem (duh, thanks for the pictures). Maybe you can set the engine down on something and come in from the side with the hoist?
|
By FORD DEARBORN - 2 Years Ago
|
Seeing that your engine is mostly assembled already, why bother with the stand. I'll TRY to send a pic of my 312 mounted between the legs of my portable shop hoist in preparation for the initial run-in which worked out excellent. I have also done this procedure with a 302 engine. Here I am hooking up the electrics for the run-in.
|
By 57RancheroJim - 2 Years Ago
|
I feel your pain, I have the same issue and I built the hoist and stand myself. It worked fine for the 223 six I was pulling from my truck at that time but then when I used it for the Y block in my 57 the legs on the hoist are about 10" to long. I have put the cross leg of the engine stand on top of the legs of the hoist.
|
By 57RancheroJim - 2 Years Ago
|
FORD DEARBORN (1/20/2023)
Seeing that your engine is mostly assembled already, why bother with the stand. I'll TRY to send a pic of my 312 mounted between the legs of my portable shop hoist in preparation for the initial run-in which worked out excellent. I have also done this procedure with a 302 engine. Here I am hooking up the electrics for the run-in. 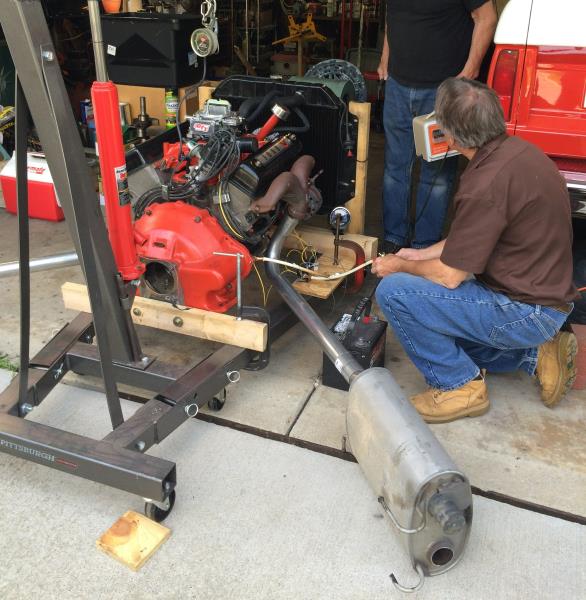 I like your run in stand. I made one out of mostly scrap. It has a fuel tank added now.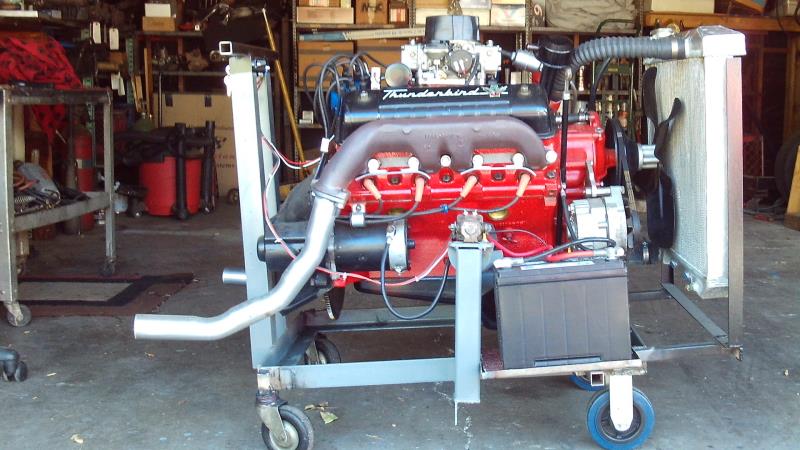
|
By paul2748 - 2 Years Ago
|
Another possibility - drop the engine to the ground, disconnect from hoist. Raise hoist on something so the stand legs go under the hoist legs. Raise engine by hoist, slide stand under legs, attach stand to engine.
|
By 55blacktie - 2 Years Ago
|
I would use extreme caution if you attempt to "Raise hoist on something." I tried doing that with a floor jack; it didn't stay put, but no damage was done.
|
By B-rad - 2 Years Ago
|
Got it on the stand. Thanks for all the advice. Now to paint and assembly.
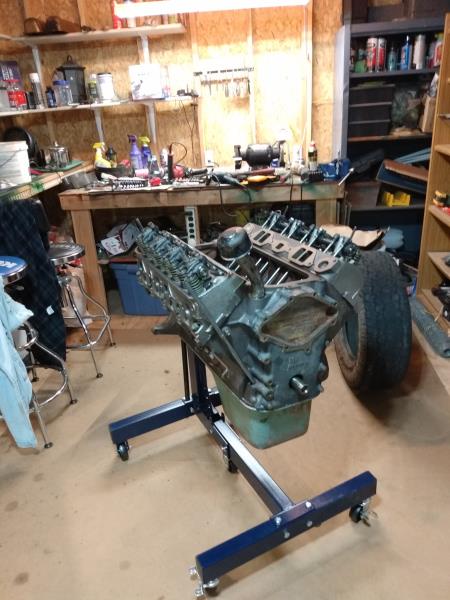
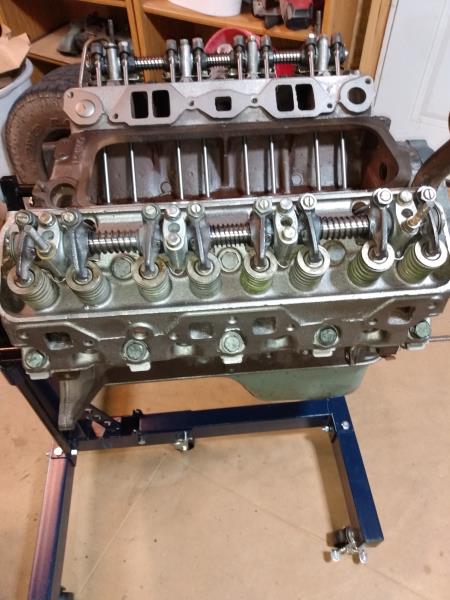
|
By DryLakesRacer - 2 Years Ago
|
Off the subject..Always baffles me why Ford, with the introduction of the overhead valve 239/254, the engineers didn’t use the port design they already had with the Lincoln. It had to be $$$$ or wanting better for the more prestigious car.
|
By FORD DEARBORN - 2 Years Ago
|
B-rad, are the 2 freeze/welch plugs oriented correctly in the rear coolant passages of the cylinder heads? It's hard to tell from the photograph posted but it looks like the convex surface is on the atmospheric side rather than on the pressurized side. I'm not familiar with the assembly details of the Lincoln Y - hope this helps.
|
By B-rad - 2 Years Ago
|
No idea. Gonna take a look in the manual when I get back out there. Not even sure what I'm looking at
|